Методы расчета площади контакта металла с валками
Контакт полосы с каждым из валков происходит по некоторой криволинейной поверхности, площадь которой зависит от кривизны цилиндрической поверхности бочки, искаженной упругим сплющиванием, длины очага деформации, а также от формы калибра (если прокатывают сортовой или фасонный профиль).
Точно определить площадь контакта в функции всех этих факторов очень сложно, поэтому величину Fконтi, входящую в формулу силы прокатки (8.2), рассчитывают, используя некоторые упрощающие допущения, исходя из той цели, чтобы погрешность расчета силы прокатки (разность между рассчитанной и измеренной величинами Fi) была по возможности минимальной.
Одно из допущений состоит в том, что в качестве величины Fконтi принимают площадь не фактической поверхности контакта полосы и валка, а ее горизонтальной проекции на плоскость, проходящую через ось прокатки.
На основе этого допущения при прокатке полосы прямоугольного поперечного сечения величину Fконтi определяют по формуле:
, (8.17)
где li – длина очага деформации в i-й рабочей клети;
bсрi – средняя ширина полосы в очаге деформации.
Если прокатка происходит с уширением, то кривая, по которой в очаге деформации движется боковая кромка полосы, близка по форме к экспоненте, поэтому среднюю ширину полосы вычисляют по формуле:
, (8.18)
где bi-1 – ширина полосы на входе в i-ю клеть;
- абсолютное уширение;
bi – ширина полосы на выходе из i-й клети.
При двумерной информации, когда уширение практически отсутствует (прокатка тонких широких полос):
,
где b – постоянная во всех клетях ширина полосы.
Длину очага деформации li для расчета Fконтi по формуле (8.17) определяют следующим образом:
а) при горячей прокатке полос толщиной hi ≥ 8…10 мм, когда упругое сплющивание валков и полосы незначительно и им можно пренебречь, используют приближенную формулу, вывод которой дан в главе 3:
, (8.19)
где Ri - радиус бочки валка в i-й клети;
Δhi – абсолютное обжатие полосы в очаге деформации i-й клети.
б) при горячей и холодной прокатке полос толщиной hi < 8 мм пренебрегать совместным упругим сплющиванием валков и полосы в очаге деформации не следует, т.к. это значительно увеличивает погрешность расчета площади контакта, а значит и силы прокатки. Доля длины упругих участков от общей длины очага деформации может достигать:
- при горячей прокатке полос толщиной hi ≤ 1,5 мм – 17 - 21%;
- при холодной прокатке полос толщиной hi ≤ 0,5 мм – 60% и более (чем тоньше полоса, тем больше эта доля).
Поэтому для полос указанного сортамента длину очага деформации рассчитывают с учетом упругого сплющивания полосы и валков. В отличие от длины li, определяемой формулой (8.19), ее обозначают lсi, добавляя индекс ''с'', свидетельствующий об учете упругого сплющивания. Формулы для расчета общей длины очага деформации lсi и длин ее составных частей (упругих и пластических участков) приведены в главе 6, при изложении методики расчета переменных контактных напряжений. Однако, подробного вывода этих формул дано не было, он излагается в данной главе, поскольку этот вывод имеет существенное значение для понимания методики расчета силы прокатки. Впервые этот вывод изложен в работах А.И. Целикова и его учеников [1;15]. Расчетная схема, на основе которой сделан вывод формулы lсi, представлена на рис. 8.3,а.
б) |
а) |
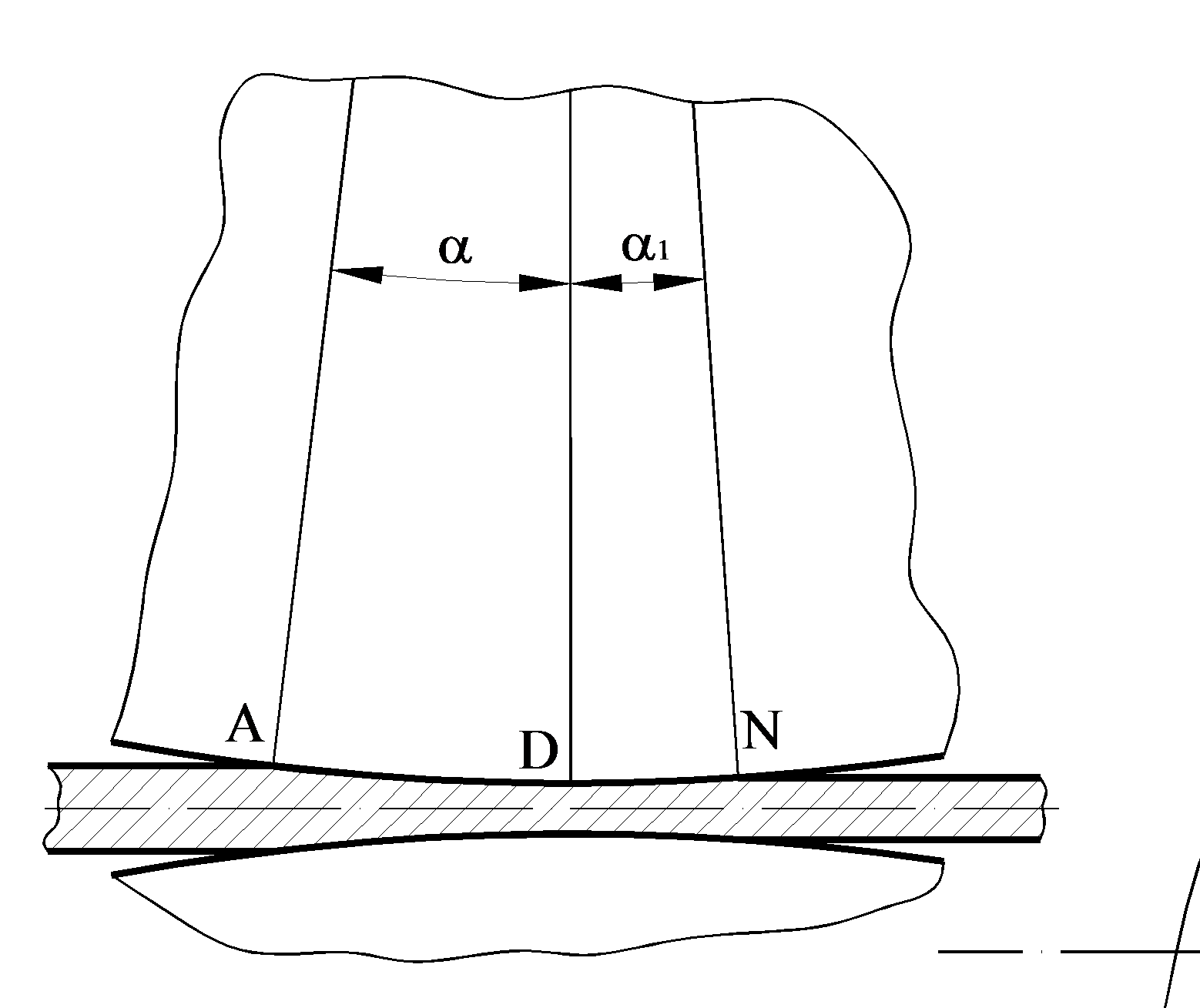
Рис. 8.3 Расчетная схема для вывода формулы длины очага деформации с учетом упругого сплющивания валков и полосы (а) и форма дуги контакта при реальных углах захвата в процессе прокатки тонких полос (б)
На схеме показаны:
hi-1 – толщина полосы на входе в валки;
AB – дуга захвата, если не учитывать упругое сплющивание валка;
- толщина, которую имела бы полоса на выходе из очага деформации, если бы ее контакт с валками происходил только по дуге АВ;
ADC – дуга захвата, если учитывать радиальное упругое сплющивание валка
Wв, но не учитывать упругую деформацию полосы, происходящую на выходе ее из очага деформации.
- толщина, которую имела бы полоса на выходе из очага деформации, если учитывать только упругое сплющивание валков.
Необходимо иметь в виду, что в начале очага деформации, правее точки А, полоса не сразу подвергается пластической деформации, а сначала сжимается упруго. И лишь только после того, как сопротивление упругому сжатию достигнет предельного для материала значения (на входе в i-ю клеть оно равно σфi-1), начинается процесс пластической деформации полосы.
Он заканчивается после прохождения полосой точки D, лежащей на вертикальной осевой плоскости валка EOB.
Правее точки D поверхность бочки начинает удаляться от оси прокатки и межвалковый зазор увеличивается. Однако, толщина полосы не остается после этого постоянной, равной , т.к. металл имеет свойство после пластической деформации упруго восстанавливать часть первоначальной толщины. Таким образом, на участке очага деформации длиной x1 имеет место упруго-пластическая деформация обжатия полосы, а на участке длиной x2упр – только упругая деформация, состоящая в возврате части толщины полосы, равной 2WП (см. схему «а» рисунка 8.3, где WП – упругое увеличение толщины полосы со стороны одного валка).
В результате общая длина очага деформации будет равна:
, (8.20)
где x1 соответствует отрезку дуги AD, а x2 соответствует отрезку дуги DN, причем точка N возникает в том месте, где полностью заканчивается упругое восстановление части толщины полосы. Точка N определяет длину отрезка x2упр, окончательную толщину полосы на выходе из i-й клети hi и ее абсолютное обжатие:
, (8.21)
Таким образом, чтобы получить расчетную формулу lсi, необходимо определить длины x1 и x2упр.
А.И. Целиков решил эту задачу, начиная с определения длины x2упр, соответствующей отрезку DN дуги захвата [1]. Поскольку на участке DN в контакте валка и полосы имеют место только упругие деформации, он предложил использовать для расчета x2 классическую формулу теории упругости – формулу Герца (случай упругого контакта цилиндра и плоскости):
, (8.22)
где pсрi – среднее удельное давление;
Ri – радиус бочки валка;
νB, νП – коэффициенты Пуассона материалов валков и полосы;
ЕВ, ЕП – модули упругости материала валков и полосы.
Величину x1 можно найти из соотношения сторон двух пар подобных прямоугольных треугольников: ABE и ABF, BNE и BNG (рис. 8.3,а):
. (8.23)
Подставив в равенства (8.23) значения отрезков:
после простых алгебраических преобразований получим:
, (8.24)
(изучающим теорию прокатки рекомендуем преобразования равенств (8.23) к виду (8.24) выполнить самостоятельно).
Заметим, что на схеме рис. 8.3,а углы α (угол захвата) и α1 изображены значительно бóльшими, чем в реальности. Это сделано для того, чтобы четко показать все отрезки (WВ, WП, ) и объяснить вывод формулы (8.24).
Фактически при прокатке тонких полос углы захвата не превышают 10° (αmax=10°), а угол α1, образующийся на участке упругого восстановления части толщины полосы, не превышает 6° (αmax=6°). В связи с этим форма дуги AND, образующей очаг деформации, имеет при реальных углах α и α1 вид, показанный на схеме рис. 8.3,б. Как видно, отрезки этой дуги AD и DN очень близки по форме к отрезкам прямых, поэтому их линейная аппроксимация в энергосиловых расчетах вполне обоснована.
Кроме того,
, поэтому с погрешностью, не превышающей 0,5%, можно принять в формуле (8.24)
, и окончательно эта формула будет иметь вид [8.1]:
. (8.25)
Таким образом, алгоритм вычисления длины очага деформации с учетом упругого сплющивания валков и полосы заключается в следующем:
1. Рассчитывают длину x2упр по формуле (8.22).
2. Рассчитывают длину x1 по формуле (8.25).
3. Рассчитывают длину lсi по формуле (8.20).
Уточненный расчет длины второго упругого участка x2упр при холодной прокатке.
Опыт энергосиловых расчетов широкополосных станов показал, что изложенная методика определения длины очага деформации с учетом упругого сплющивания валков и полосы позволяет рассчитать силу прокатки с погрешностью, не превышающей 5-10%, при горячей прокатке, т.к. длина второго упругого участка очага деформации в этом случае не превышает 15-21% общей длины очага деформации. И если длина x2упр по формуле Герца (8.22) рассчитана неточно, например, с погрешностью 30%, то общая погрешность вычисления длины lсi не превысит 30%·0,17=5,1%.
На станах холодной прокатки, особенно при производстве наиболее тонких полос (толщиной менее 0,5 мм), длина упругих участков достигает 50% и более, поэтому требования к точности вычисления x2упр на этих станах более жесткие.
Анализ этого вопроса, изложенный в главе 6, показал, что формула Герца (8.22) для расчета длины x2упр не учитывает некоторых существенных особенностей контакта валков и полосы на втором упругом участке очага деформации. В теории упругости эта формула получена для случая прижатия неподвижного цилиндра к упругому полупространству, ограниченному плоской поверхностью.
При прокатке валки вращаются, а полоса, в отличие от полупространства, движется, имеет конечную толщину и переменную жесткость, возрастающую по мере обжатия, причем между ней и валками действуют напряжения трения. Следовательно, формула (8.22) не учитывает факторы, которые могут влиять на длину упругого участка x2: трение между полосой и валками, изменение ее толщины и жесткости по мере обжатия.
Для учета этих факторов в главе 6 приведена уточненная формула (6.40), которая отличается от формулы Герца (8.22) введением в нее поправочного коэффициента Кпопрi. Для удобства изучения студентами материала главы 8 ниже повторно приведены из главы 6 уточненная формула (6.40) для расчета x2упр и формула (6.41) для расчета поправочного коэффициента Кпопрi (этим формулам присвоены новые номера, соответствующие порядку нумерации формул главы 8).
. (8.26)
Величина Кпопрi зависит от значения комплекса:
, (8.27)
где - приращение условного предела текучести полосы от исходного значения (наклеп полосы на выходе из i-ой клети):
; (8.28)
hi, μi – толщина полосы на выходе из i-й клети и среднее значение коэффициента трения в ее очаге деформации.
Если > 5200 МПа·мм, то Кпопрi=1.
Если ≤ 5200 МПа·мм, то Кпопрi вычисляют по регрессионному уравнению:
; (8.29)
(размерности : : МПа, hi: мм).
Регрессионное уравнение (8.29) получено в результате статистической обработки более 7000 режимов прокатки, их технологических и энергосиловых параметров, содержащихся в базах данных АСУТП действующих станов. Обработанные режимы охватывают широкий спектр параметров: толщины hi = 0,27…1 мм, коэффициенты трения μi = 0,034…0,072; приращение предела текучести: = 336…519 МПа. Множественный коэффициент детерминации для уравнения (8.29) оказался равным: R2 = 0,974, что свидетельствует о статистической достоверности этого уравнения.
Из выражений (8.27) и (8.29) видно, что из факторов, не учитываемых формулой Герца (8.22), на длину упругого участка деформации наибольшее влияние оказывают толщина полосы и коэффициент трения: чем тоньше полоса и чем больше коэффициент трения, тем меньше длина x2упр, по сравнению со значением, полученным по формуле (8.22).
Так, например, в 5й клети 5тиклетевого стана «1700», при прокатке полосы из стали 08пс толщиной h5=0,3 мм с коэффициентом трения μ5=0,036 Кпопр5=0,8. Увеличение коэффициента трения до значения μ5=0,049 вызывает снижение поправочного коэффициента до величины Кпопр5=0,6. Таким образом, для указанных условий холодной прокатки наиболее тонких полос в 5й клети формула Герца дает существенно завышенное значение x2упр (а, следовательно и всей длины очага деформации): при μ5=0,036 это завышение составляет 20%, а при μ5=0,049 оно возрастает до 40%.
Расчет площади контакта металла с валками при прокатке в калибрах [15].
Поверхность контакта при прокатке в калибрах имеет сложную форму, зависящую от профиля сортового или фасонного металла. Точно вычислить ее площадь аналитическим методом крайне сложно, поэтому данную задачу решают приближенными инженерными методами: графическим (с помощью приемов начертательной геометрии), графоаналитическим или аналитическим. Сущность этих методов изложена в книге [15].
В современных условиях, когда инженерные расчеты технологии и оборудования прокатного производства выполняют с использованием компьютерных средств, применение графических методов нецелесообразно. Лучше воспользоваться проверенными на практике эмпирическими или полуэмпирическими формулами.
К их числу относятся формулы В.Г. Дрозда для расчета контактной площади при прокатке сортовых профилей, исходя из наиболее распространенных схем калибровки квадрата, овала и ромба. Эти формулы приведены в таблице 8.5. Для расчета площади контакта при прокатке профилей сложной формы (уголков, балок, швеллеров и т.д.) можно, используя метод приведенной полосы, рассчитать по формуле (8.14) обжатие Δhi, по формуле (8.16) катающий радиус Rкi, по формуле (8.15) длину очага деформации li, а затем определить среднее значение ширины профиля в очаге деформации Всрi, и, наконец, вычислить площадь контакта:
Таблица 8.5
Контактные площади при прокатке сортовых профилей
(формулы В.Г. Дрозда)
№ | Схема калибровки | Формула контактной площади | Примечания |
Прокатка квадрата из овала
![]() | ![]() | RКi – радиус валка в середине калибра. Остальные размеры – на схемах. | |
Прокатка овала из квадрата
![]() | ![]() | ||
Прокатка ромба или квадрата из ромба
![]() | ![]() |
О других методах расчета величины Fконтi при прокатке в калибрах можно прочитать в книгах [11.5; 11.10].
Дата добавления: 2019-02-08; просмотров: 2463;