Аддитивная и субтрактивная технология изготовления коммутационных плат
Все большее распространение при создании электронной аппаратуры получают методы проектирования и формирования конфигурации элементов коммутационных плат на основе аддитивной технологии, включая использование маскирования проводящих дорожек из меди (SMOBC - Solder Mask Over Bare Copper), которое в большинстве случаев обеспечивает более высокую надежность формирования элементов плат, чем традиционные методы (рисунок 2.47). Плата, изготовленная приемами аддитивной технологии, представляет собой преимущественно планарную конструкцию с нанесенным в местах отсутствия маски (в окнах маскирующего слоя) припоем, осаждаемым вровень с фоторезистом [14].
а
б
в
Рисунок 2.47 - Сравнение субтрактивной и более надежной аддитивной технологий изготовления коммутационных плат: а - формирование маски припойного покрытия; б - рельеф поверхностей плат, получаемых разными способами; в - дозированное нанесение припоя на платы перед пайкой компонентов в корпусах PLCC, SOIC и SOT;
1 – газовая полость после нанесения припоя; 2 – отсутствие припоя; 3 – основание платы; 4 – медь; 5 – маскирующее покрытие; 6 -припойное покрытие; 7 – перемычка припоя; 8 – конфигурация контактной площадки с припоем после его оплавления ; 9 – часто используемая маска, предотвращающая затекание припоя за границы припойной площадки; 10 – припой
Применявшиеся до недавнего времени традиционные коммутационные платы для ТПМК были субтрактивными, при этом медные проводники выступали над поверхностью платы, и для защиты от внешних воздействий (в том числе технологических) необходимо было наносить на них через маску конформное покрытие. При этом часто наблюдались неполное маскирование или недостаточная адгезия покрытия с материалами платы. В субтрактивной технологии более вероятны пузырение защитного покрытия или отслаивание фольги. Еще одним недостатком такой технологии является повышенная возможность скопления припоя и флюсов (включая продукты разложения) в результате попадания их в пустоты (ловушки), образующиеся при некачественном маскировании. Как известно, аддитивный метод был разработан с целью металлизации сквозных отверстий для монтажа компонентов в традиционной технологии, однако он обладает также весьма специфическими достоинствами применительно к ТПМК. Во многом качество поверхностного монтажа зависит от плоскостности подложки. Используя аддитивную технологию, можно получить поверхность подложки, мало отклоняющуюся от плоской, и осуществлять более управляемое и точное нанесение адгезива и, следовательно, прецизионную установку компонентов. Формирование конфигурации элементов проводящего и диэлектрических слоев также осуществляется более точно и соответственно создается возможность формирования более узких дорожек и зазоров между ними, как правило, до величины 0,005 дюйма (0,127мм), в то время как традиционная технология, о чем уже говорилось, обеспечивает лишь размеры 0,007 - 0,008 дюйма (0,1778 - 0,2032 мм) с некоторыми ограничениями в отношении коммутационных дорожек, проходящих между контактными площадками. Затекание припоя и формирование перемычек между контактными площадками в аддитивном методе также устраняется. Защита дорожек и площадок боковыми стенками маскирующего покрытия во время процесса аддитивного нанесения, как утверждают специалисты фирмы Kollmorgen Corp., являющиеся лидерами в этой технологии, эквивалентна созданию идеально совмещенной маски. Запатентованная технология «Micro-Socket», разработанная фирмой Kollmorgen, предусматривает нанесение дополнительного покрытия, формирующего более надежные с точки зрения предупреждения возникновения перемычек стенки контактных площадок и снижающего смещение компонента во время пайки. Данная технология в равной степени совместима с пайкой в потоке припоя (подвод тепла с боковых сторон) и с расплавлением дозированного припоя при использовании припойных паст (подвод тепла сверху).
Условия, в которых изготавливаются и обычно используются микросборки с поверхностным монтажом, существенно отличаются от тех, которые характерны для традиционных изделий. В частности, в технологии поверхностного монтажа очистка изделий после пайки является более сложной и ответственной операцией из-за наличия загрязнений, скапливающихся в зазорах между корпусами компонентов и поверхностью платы, особенно если учитывать вероятность ускорения коррозионных процессов, стимулируемых химическими реакциями в местах локального перегрева. Поскольку в настоящее время расстояние между проводниками в ТПМК составляет 0,005 дюйма (0,127 мм) или меньше, на поверхности КП возникают относительно высокие градиенты напряженности электрического поля (возможно, до 150 В/мм), усиливающие ионное загрязнение платы и ускоряющие тем самым формирование путей утечки тока. Анализ факторов, затрудняющих очистку смонтированных плат в ТПМК, все более и более раскрывает решающее значение тщательного контроля состояния поверхности КП. Существует два основных метода оценки качества поверхности:
• По уровню ионного загрязнения. Этот метод основан на оценке количества растворимых в воде и спиртах примесей. Для этого плата на определенное время погружается в смесь воды и изопропилового спирта. Количество перешедших в раствор примесей оценивается путем замера его проводимости и сравнения с проводимостью исходного чистого раствора. После чего производится пересчет и определение среднего уровня загрязненности поверхности в микрограммах на квадратный сантиметр платы.
• По величине поверхностного сопротивления платы. Этот метод чаще используется в качестве дополнительного. Критерием оценки состояния поверхности в данном случае служит сопротивление участка платы между коммутационными дорожками или между контактными площадками. Обычно слоистая структура основания платы имеет величину поверхностного сопротивления до 1016 Ом на квадрат, хотя иногда эта величина может быть значительно ниже, например, 1010 Ом на квадрат. При измерении сопротивления участка платы на тестовые элементы подается, как правило, напряжение 100 - 500 В с учетом требуемой полярности. Такой метод представляет собой разновидность разрушающего испытания, поэтому недавно фирма Protonique предложила метод испытания напряжением 10,2 В. В присутствии загрязнений даже в случае низких градиентов напряженности электрического поля начинают проявляться некоторые нежелательные процессы, например, поляризация тестовой структуры при подаче отрица-тельного напряжения.
Применительно к очистке традиционных плат существуют сравнительно новые стандарты (например, MIL-P-28809 в США и DEF-STAN 00-10/3 (1988 г.) в Великобритании), однако неясно, насколько оправданными являются жесткие требования этих стандартов на практике и насколько применимы они к ТПМК. Оценка ионного загрязнения продолжает оставаться удобным методом для использования в условиях массового производства, так как позволяет гораздо быстрее получать необходимые результаты, чем при измерении поверхностного сопротивления платы.
Варианты выполнения поверхностного монтажа
Существует 3 основных варианта реализации поверхностного монтажа [14]:
• Чисто поверхностный монтаж на плате (односторонний или двухсторонний);
• Смешанно-разнесенный вариант, когда традиционные компоненты размещают на лицевой стороне платы, а простые компоненты для поверхностного монтажа – на обратной;
• Смешанный монтаж, например, на лицевой стороне платы, и поверхностный на обратной (когда традиционные компоненты и сложные компоненты для поверхностного монтажа размещают на лицевой стороне платы, а простые поверхностно монтируемые компо-ненты – на обратной стороне платы);
Чисто поверхностный монтаж (одно - или двухсторонний).
В этом случае число технологических операций минимально. На диэлектрическое основание платы наносят припойную пасту методами трафаретной печати. Количество припоя, наносимое на плату, должно обеспечивать требуемые электрофизические характеристики коммутирующих элементов (для чего необходим соответствующий контроль). После осуществления позиционирования и фиксации компонентов следует операция пайки оплавлением дозированного припоя. В случае двухстороннего поверхностного монтажа на обратной стороне платы фиксируются простые компоненты с помощью адгезива. После отверждения адгезива компо-ненты подвергаются пайке двойной волной припоя либо оплавлением дозированного припоя, затем осуществляются очистка, контроль и испытания смонтированных плат (при необходимости платы переворачиваются).
Смешанно-разнесенный монтаж. Существуют две разновидности реализации этого варианта монтажа. Чаще всего сборку начинают с установки традиционных компонентов в отверстия платы, после чего размещают компоненты на поверхности платы (рисунок 2.48). В альтернативном случае (рисунок 2.49) сначала устанавливают компоненты на поверхность платы. Первый вариант применяется тогда, когда формовка и вырубка выводов обычных компонентов осуществляется с помощью специальных приспособлений заранее, иначе компоненты, смонтированные на поверхность платы, будут затруднять обрезку выводов, проходящих через отверстия платы. Компоненты для поверхностного монтажа целесообразно монтировать первыми при повышенной плотности их размещения, что требует минимального количества переворотов платы в процессе изготовления изделия.
Установка традиционных компонентов и сложных компонентов для поверхностного монтажа на лицевой стороне платы, а также простых компонентов на поверхность обратной стороны.
Это вероятно, самая сложная разновидность монтажа из всех существующих, блок-схема ее выполнения приводится на рисунке 2.50. Первым этапом является нанесение припойной пасты через трафарет, установка на лицевой стороне платы сложных компонентов для поверхностного монтажа (SOIC, PLCC) и пайки расплавлением дозированного припоя. Затем, после установки традиционных компонентов (с соответствующей обрезкой и фиксацией выводов), плата переворачивается, на нее наносится адгезив и устанавливаются компоненты простых форм для поверхностного монтажа (чип – компоненты и компоненты в корпусе SOT). Эти простые компоненты и выводы компонентов, установленных в отверстия, одновременно пропаиваются двойной волной припоя. Возможно также использование в составе одной линии оборудования, обеспечивающего эффективную пайку компонентов (с лицевой стороны платы) расплавлением дозированного припоя и пайку (с обратной стороны платы) волной припоя.
Следует отметить, что в таком технологическом процессе возрастает количество контрольных операций из-за сложности сборки при наличии компонентов на обеих сторонах платы. Неизбежно возрастает также количество паяных соединений и трудности. Обеспечения их качества. Это усложняет работу автоматического оборудования для контроля соединений. Поскольку существующее оборудование позволяет за один прием контролировать лишь одну сторону платы, то для обеспечения контроля обеих сторон требуется дополнительная операция перевертывания платы.
Выбор варианта монтажа при проектировании изделий
Выбор варианта реализации монтажа при проектировании изделия с применением ТПМК осуществляется не только с точки зрения технологических приемов его изготовления, но и в зависимости от сочетания традиционных и монтируемых на поверхность компонентов. Специфика вариантов таких сочетаний в общих чертах описана ниже, а более подробно поясняется с помощью рисунка 2.51 и таблицы 2.20.
• Вариант I. Чисто (полностью) поверхностный монтаж: набор компонентов для ТПМК монтируется с лицевой или обеих сторон платы.
• Вариант II. Смешанный монтаж: смешанный набор компонентов монтируется с лицевой или обеих сторон платы.
• Вариант III. Смешанно-разнесенный монтаж: традиционные компоненты монтируются с лицевой стороны, а компоненты для ТПМК – с обратной.
|
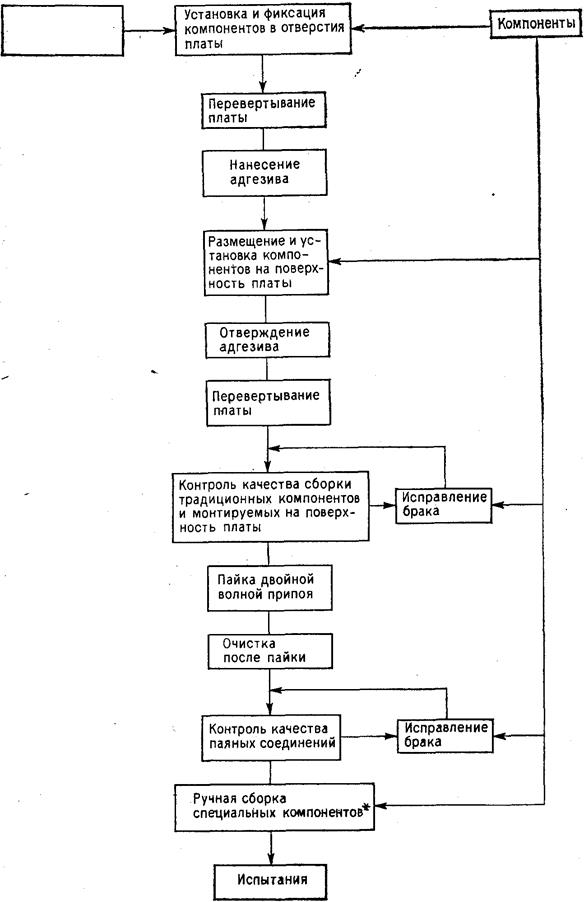
Рисунок 2.48 - Схема реализации процесса монтажа с использованием простых компонентов
для монтажа на поверхность и компонентов для монтажа в отверстия платы (вариант 1)
* Непаяемые и термочувствительные компоненты
Рисунок 2.49 - Схема реализации монтажа простых компонентов на поверхность платы и компонентов, устанавливаемых в отверстия платы (вариант 2)
* Непаяемые и термочувствительные компоненты
Рисунок 2.50- Схема реализации монтажа традиционных компонентов, а также
простых и сложных компонентов, устанавливаемых на поверхность платы.
* Непаяемые и термочувствительные компоненты
а
б
Рисунок 2.51 - Варианты монтажа с применением ТПМК:
а - вариант I. Чисто поверхностный монтаж. Все компоненты устанавливаются на поверхность платы. Компоненты могут монтироваться на одной или обеих сторонах платы. Возможна одноступенчатая (одновременная) пайка всех компонентов;
б - вариант II. Смешанный монтаж традиционных и устанавливаемых на поверхность компонентов. Возможны любые комбинации тех и других компонентов с одной или двух сторон платы, но это требует многоступенчатой пайки (расплавлением дозированного припоя, волной и, возможно, ручной);
в - вариант III. Смешанно-разнесенная технология (компоненты для поверхностного монтажа с одной стороны платы, а традиционные - с другой (с обратной));
1 - сложный компонент для монтажа на поверхность (PLCC с J-образными выводами); 2 - сложный компонент для монтажа на поверхность [кристаллоноситель с выводами в виде крыла чайки (L-образный)]; 3 - чип-конденсатор; 4 - чип-резистор; 5 - чип-резистор; 6 - сложный компонент для поверхностного монтажа (кристаллоноситель с выводами в виде крыла чайки); 7 - резистор с радиальными выводами; 8 - корпус типа DIP; 9 - конденсатор с аксиальными выводами; 10 - резистор с аксиальными выводами; 11 - резистор с радиальными выводами; 12 - корпус типа DIP; 13 - простой чип-резистор; 14 - простой чип-конденсатор
Рисунок 2.51 иллюстрирует специфику каждого из вариантов, однако важно иметь в виду, что сочетание достоинств и ограничений каждого варианта будет изменяться от пользователя к пользователю. Рекомендуемые нормы проектирования приведены в таблице 2.20.
При нанесении припойной пасты минимальное расстояние между контактными площадками должно составлять 0,020 дюйма (0,5080 мм). Фирма IPC рекомендует использовать отверстия, полученные сверлением, диаметром 0,015 дюйма (0,381 мм), в то время как другие фирмы предлагают нижний предел диаметра отверстия 0,013 дюйма (0,3302мм).
Таблица 2.20 - Рекомендуемые правила проектирования изделий в ТПМК
(для плат, изготовленных по аддитивной технологии)
Проектируемые элементы | Типовой | вариант | По специальному заказу, дюймы (мм) |
для трафаретной печати, дюймы (мм) | для фотопечати, дюймы (мм) | ||
Ширина/шаг коммутирующих дорожек | 0,0150/0,15 (0,381/3,81) | 0,008/0,008 (0,2032/0,2032) | 0,005/0,005 (0,127/0,127) |
Диаметр отверстий межслойных переходов | 0,030(0,762) | 0,025(0,635) | 0,020(0,508) |
Размер площадки межслойного перехода (диаметр) | 0,050(1,27) | 0,040(1,016) | 0,030(0,762) |
Размер площадки для вывода ИС | Рекомендуется (0,025±0,005)Х (0,070±0,001) ((0,635±0,127)Х (1,778±0,0254)) | ||
Ширина площадки для конденсатора/резистора | 0,030(0,762) | 0,020(0,508) | 0,010(0,254) |
Длина площадки для конденсатора/резистора | 0,015—0,030 | 0,010—0,020 (0,254—0,508) | 0,005—0,010 (0,127—0,254) |
(0,381—0,762) | |||
Длина проводящего участка от края контактной площадки до компонента | 0,045(1,143) | 0,030(0,762) | 0,020(0,508) |
Расстояние от проводника до контактной площадки | 0,015(0.381) | 0,010(0,254) | 0,007(0,1778) |
Расстояние между компонентами | Рекомендуется делать равным высоте большего компонента | ||
Величина зазора между краем контактной площадки и окном припойной маски | 0,015 (0,381) | 0,010 (0,254) | 0,005 (0,127) |
Шаг контактных площадок при использовании маскирования | 0,030 (0,762) | 0,020 (0,508) | 0,010 (0,254) |
Шаг контактных площадок без использования маскирования | 0,025(0,635) | 0,020(0,508) | 0,020(0,508). |
Расстояние от осевой линии проводника до края платы | 0,030 (0,762) + половина ширины проводника | 0,020(0,508) + половина ширины проводника | |
Расстояние от контактной площадки до металлизированного направляющего отверстия | ±0,010 (±0,254) | ±0,007 (±0,178) | ±0,005 (0,127) |
Расстояние от контактной площадки до неметаллизированного направляющего отверстия | ±0,012 (±0,3048) | ±0,007 (±0,178) | ±0,003 (±0,076) |
Расстояния от контактных площадок до фигур совмещения | ±0,007 (±0,178) | ±0,005 (±0,127) | ±0,003 (±0,076) |
Разброс значений толщины контактных площадок из меди | ±0,0001 (±0,0025) | ±0,0001 (±0,0025) | ±0,0001 (±0,0025) |
Разброс значений толщины контактных площадок из припойного материала | ±0,001 (±0,0254) | ±0,001 (±0,0254) | +0,00025 (±0,00635) |
Для определения минимального размера контактной площадки с межслойным переходом в коммутационной плате предложена формула:
D = d + 2Y + 2a + Δш,
где D – диаметр контактной площадки с межслойным переходом; d –диаметр переходного отверстия; Y – допуск на размеры КП; а – допустимое расстояние от края отверстия до края его площадки; Dш – допуск на изготовление эталонного шаблона.
Дата добавления: 2020-10-14; просмотров: 783;