Выбор электродвигателя. Кинематический расчет привода
Привод состоит из электродвигателя (1), муфты (2) и редуктора (3). В зависимости от задания редуктор может быть одноступенчатым (рис.1а), или двухступенчатым (рис.1б).
![]() |
Рис. 1.1а
![]() |
Рис. 1.1б
Электродвигатель является одним из основных элементов привода. В проектируемом приводе рекомендуется использовать трехфазные асинхронные короткозамкнутые двигатели серии 4А.
Мощность электродвигателя зависит от требуемой мощности исполнительного механизма (мощности на ведомом валу редуктора), а частота вращения – от частоты вращения приводного вала исполнительного механизма.
Требуемая мощность электродвигателя Pдв, кВт:
(1.1)
где Pn – мощность на ведомом валу;
h0 - общий коэффициент полезного действия привода (КПД)
, (1.2)
где hзп – КПД зубчатой передачи; hпк – КПД пары подшипников качения; hм – КПД муфты; i =1, k =2 – для одноступенчатого редуктора, i =2, k =3 – для двухступенчатого редуктора (табл. 1.1).
Таблица 1.1
Значения КПД элементов механических передач
Элемент передачи | КПД |
Пара цилиндрических зубчатых колес | 0,96…0,97 |
Пара подшипников качения | 0,99…0,995 |
Муфта | 0,98 |
Электродвигатель выбирается по требуемой мощности из табл. 1.2 по величине, большей (иногда несколько меньшей), но ближайшей к требуемой мощности Pдв:
. (1.3)
Каждому значению номинальной мощности Рном соответствует несколько типов двигателей с различными синхронными частотами вращения 3000, 1500, 1000, 750 об/мин. Необходимо отметить, что электродвигатели с большой синхронной частотой вращения (3000 об/мин) имеют низкий рабочий ресурс, а двигатели с низкими частотами (750 об/мин) весьма металлоемки, поэтому их использование в приводах общего назначения малой мощности не рекомендуется. Окончательный выбор оптимального типа двигателя зависит от исходных данных и производится из табл. 1.2 после определения передаточного числа редуктора.
Таблица 1.2
Двигатели асинхронные короткозамкнутые трехфазные серии 4А.
Технические данные
Рном, кВт | Синхронная частота вращения, об/мин | |||||||
Тип двигателя | nном, об/мин | Тип двигателя | nном, об/мин | Тип двигателя | nном, об/мин | Тип двигателя | nном, об/мин | |
0,25 | 4ААМ56В2У3 | 4ААМ63А4У3 | 4ААМ63В6У3 | 4АМ71В8УЗ | ||||
0,37 | 4ААМ63А2У3 | 4ААМ63В4У3 | 4АМ71А6У3 | 4АМ80А8У3 | ||||
0,55 | 4ААМ63В2У3 | 4АМ71А4УЗ | 4АМ71В6У3 | 4АМ80В8У3 | ||||
0,75 | 4АМ71А2У3 | 4АМ71В4У3 | 4АМ80А6У3 | 4АМ90LА8У3 | ||||
1,1 | 4АМ71В2У3 | 4АМ80А4У3 | 4АМ80В6У3 | 4АМ90LВ8У3 | ||||
1,5 | 4АМ80А2У3 | 4АМ80В4У3 | 4АМ90L6У3 | 4АМ100L8У3 | ||||
2,2 | 4АМ80В2У3 | 4АМ90L4У3 | 4АМ100L6У3 | 4АМ112МА8У3 | ||||
3,0 | 4АМ90L2У3 | 4АМ100S4У3 | 4АМ112МА6У3 | 4АМ112МВ8У3 | ||||
4,0 | 4АМ100S2У3 | 4АМ100L4У3 | 4АМ112МВ6У3 | 4АМ132S8У3 | ||||
5,5 | 4АМ100L2УЗ | 4АМ112М4У3 | 4АМ132S6У3 | 4АМ132М8У3 | ||||
7,5 | 4АМ112М2У3 | 4АМ132S4УЗ | 4АМ132М6У3 | 4АМ160S8У3 | ||||
4АМ132M2У3 | 4AM132M4У3 | 4A160S6У3 | 4А160М8У3 | |||||
4А160S2У3 | 4А160S4У3 | 4А160М6У3 | 4А180М8У3 | |||||
18,5 | 4А160М2У3 | 4А160М4У3 | 4А180М6У3 | - | - | |||
4А180S2У3 | 4А180М4У3 | - | - | - | - |
Размеры электродвигателей (для графической части проекта) приведены на рис. 1.2 и в табл. 1.3.
1.2. Передаточное число редуктора определяется отношением номинальной частоты вращения электродвигателя n1 к частоте вращения ведомого вала при номинальной нагрузке:
. (1.4)
Рис. 1.2. Электродвигатели серии 4А
Таблица 1.3
Электродвигатели серии 4А. Основные размеры, мм
Тип двигателя | Число полюсов | d30 | l1 | l30 | d1 | b1 | h1 |
71A,B | 2, 4, 6, 8 | ||||||
80A | |||||||
80B | |||||||
90L | |||||||
100S | |||||||
100L | |||||||
112M | |||||||
132S 132M | 4, 6, 8 | ||||||
2, 4, 6, 8 | |||||||
160S | |||||||
4, 6, 8 | |||||||
160M | |||||||
4, 6, 8 | |||||||
180S | |||||||
180M | |||||||
4, 6, 8 |
Для двухступенчатого редуктора общее передаточное число
, (1.5)
, (1.6)
где и1 – передаточное число первой (быстроходной) ступени, и2 - второй (тихоходной).
Передаточные числа одноступенчатых редукторов рекомендуется принимать согласно ГОСТ 21426 – 75 (табл. 1.4)
Таблица 1.4
Передаточные числа цилиндрических зубчатых редукторов и их ступеней
Редукторы | |
Одноступенчатые, uР | Двухступенчатые трёхосные, ![]() |
1,25 | 8=2´4 |
1,4 | 9»2,24´4 |
1,6 | 10=2,5´4 |
1,8 | 11,2=2,8´4 |
2,0 | 12,5»3,15´4 |
2,24 | 16»3,55´4,5 |
2,5 | 18=4´4,5 |
2,8 | 20»4,5´4,5 |
3,15 | 22,4»4,5´5 |
3,55 | 25=5´5 |
4,0 | 28=5,6´5 |
4,5 | 31,5=6,3´5 |
5,0 | 35,5»6,3´5,6 |
5,6 | 40»7,1´5,6 |
6,3 | 45»8´5,6 |
7,1 | 50»9´5,6 |
8,0 |
Примечание: фактическое передаточное число может иметь отклонение от номинальной величины до 4%.
Принято считать оптимальным для одноступенчатых редукторов uР £ 5; двухступенчатых uР £ 30.
Частота вращения валов (фактическая), мин-1:
- ведомого вала одноступенчатого редуктора ;
- промежуточного вала двухступенчатого редуктора ;
- ведомого вала двухступенчатого редуктора .
1.4. Угловая скорость каждого из валов редуктора, с-1:
. (1.9)
1. Расчет зубчатых передач
2.1. Выбор материалов зубчатых колес и термической обработки
Основным материалом для изготовления зубчатых колес в настоящее время является качественная углеродистая или низколегированная сталь марок 35, 40, 45, 40Х, 40ХН, 35ХМ. В мало- и средненагруженных передачах рекомендуется применять зубчатые колеса с твердостью материала £350 НВ. При этом обеспечивается высокая точность и низкая стоимость изготовления и хорошая прирабатываемость зубьев.
Для равномерного изнашивания зубьев и лучшей их прирабатываемости твердость шестерни назначается на (30¸50) НВ больше твердости колеса.
2.2. Допускаемые напряжения
2.2.1. Допускаемые контактные напряжения.
Расчет на контактную прочность ведется по зубьям колеса, как менее прочным (твёрдым).
, (МПа), (2.1)
где sН0 – предел контактной выносливости при пульсирующем (отнулевом) цикле напряжений, МПа; KHL – коэффициент долговечности; SH – коэффициент безопасности.
Таблица 2.1
Механические характеристики сталей
Марка стали | Термо-обработка | Твердость, НВ | sв, МПа | sт Н/мм2 | s-1 Н/мм2 |
Н | 163…192 | ||||
у | 192…228 | ||||
Н | 179…207 | ||||
у | 235…262 | ||||
40Х | у | 235…262 | |||
40ХН | у | 235…262 | |||
35ХМ | У | 235…262 |
В графе «Термообработка» приняты следующие обозначения: Н – нормализация, У – улучшение.
Для нормализованных, улучшенных и объемнозакаленных материалов передачи принимают
, (2.2)
где НВ – твердость колеса в единицах Бринелля, SH = 1,1 – коэффициент безопасности;
Коэффициент долговечности
, (2.3)
где NH0 =107 – базовое число циклов перемены напряжений, соответствующее пределу выносливости; N – число циклов перемены напряжений за весь срок службы.
, (2.4)
где Lh – срок работы передачи (ресурс), ч, при N> NH0 принимают KHL = 1.
2.2.2. Допускаемые напряжения изгиба.
Допускаемые напряжения изгиба определяются для шестерни и для колеса:
, (МПа), (2.5)
где sF0i – предел выносливости материала при пульсирующем (отнулевом) цикле напряжений при изгибе, МПа;
, (2.6)
KFL – коэффициент долговечности; KFC – коэффициент реверсивности, учитывающий характер изменения напряжений, для нереверсируемых передач KFC =1, для реверсируемых передач KFC = 0,75; SF = 1,75 – коэффициент безопасности.
, (2.7)
где NF0= 5×106 – базовое число циклов перемены напряжений, соответствующее пределу выносливости.
2.3. Проектный расчёт на контактную прочность
2.3.1. Определение межосевого расстояния
Межосевое расстояние определяют из условия контактной прочности, мм
, (2.8)
где (Н×мм) - крутящий момент на ведомом валу одноступенчатого редуктора или рассчитываемой ступени двухступенчатого, n=2 для одноступенчатого и первой ступени двухступенчатого редуктора, n=3 для второй ступени двухступенчатого редуктора;
- мощность на ведомом валу, кВт; KH – коэффициент расчетной нагрузки, предварительно принимают KH =1,2…1,6; Yа – коэффициент ширины колеса по межосевому расстоянию, значения Yа принимают из ряда стандартных: 0,1; 0,15; 0,2; 0,25; 0,315; 0,4; 0,5; 0,63, при симметричном расположении колес рекомендуется принимать Yа=0,4…0,5, при несимметричном - Yа=0,25…0,4.
Определяем аw для одноступенчатого редуктора; для двухступенчатого редуктора определяем сначала аw2, а затем аw1, при этом в формулу (2.8) подставляют для одноступенчатого редуктора uР и yа, для двухступенчатого u1 и yа1, или u2 и yа2.
Вычисленное межосевое расстояние округляют в большую сторону до стандартного значения из ряда значений: 50; 63; 71; 80; 90; 100; 112;125;140; 160; 180; 200; 224; 250; 260; 280; 300; 320; 340; 360; 380; 400.
2.3.2. Модуль зацепления:
m = (0,01…0,02) , (2.9)
Для силовых передач назначают m ³ 1,5 мм.
Полученное значение модуля m округляют до стандартной величины (табл. 2.2), отдавая предпочтение значениям первого ряда перед вторым. При этом, для быстроходной (первой) ступени следует назначать модуль зацепления ближе к меньшему значению диапазона, полученного по формуле (2.9), для тихоходной – к большему.
Таблица 2.2.
Значение модулей
m, мм | 1-й ряд | 1,5; | 2; | 2,5; | 3; | 4; | 5; | 6; | 8; | 10; |
2-й ряд | 1,75; | 2,25; | 2,75; | 3,5; | 4,5; | 5,5; | 7; | 9; |
2.3.3. Числа зубьев
Суммарное число зубьев пары шестерня – колесо:
. (2.10)
Полученное значение zS округлить в меньшую сторону до целого числа.
Шестерни:
. (2.11)
Значение z1 округлить до ближайшего целого числа. Из условия отсутствия подрезания зубьев рекомендуется z1 ³ 17.
Колеса:
. (2.12)
Для двухступенчатого редуктора соответственно определяются для быстроходной ступени ZS, Z1, Z2 и для тихоходной ступени ZS, Z3, Z4.
2.3.4. Фактическое передаточное число
. (2.13)
Отклонение фактического передаточного числа от номинальной величины
. (2.14)
2.3.5. Геометрические параметры зацепления, мм
Диаметры делительных (начальных) окружностей | ![]() |
Диаметры окружностей выступов | ![]() |
Диаметры окружностей впадин | ![]() |
Ширина колеса, целое число | ![]() ![]() |
ширина шестерни | ![]() ![]() |
Фактическое межосевое расстояние | |
одноступенчатого редуктора | ![]() |
двухступенчатого редуктора | ![]() ![]() |
2.4. Проверочный расчет
2.4.1.Окружная скорость, м/c:
. (2.15)
Окружная скорость второй ступени двухступенчатого редуктора:
.
По окружной скорости назначают степень точности передачи по табл. 2.3.
Таблица 2.3
Степени точности прямозубых цилиндрических передач
Степень точности | Окружная скорость, м/с |
До 18 | |
» 12 | |
» 6 | |
» 2 |
По степени точности и окружной скорости определяют коэффициенты динамической нагрузки при расчете по контактным напряжениям KHv и напряжениям изгиба KFv.
Таблица 2.4
Значения коэффициентов KHv, KFv при НВ2 £350
Степень точности | Коэффициент | Окружная скорость, м/с | |||||
KHv | 1,03 | 1,06 | 1,12 | 1,17 | 1,23 | 1,28 | |
KFv | 1,06 | 1,13 | 1,26 | 1,40 | 1,58 | 1,67 | |
KHv | 1,04 | 1,07 | 1,14 | 1,21 | 1,29 | 1,36 | |
KFv | 1,08 | 1,16 | 1,33 | 1,50 | 1,67 | 1,80 | |
KHv | 1,04 | 1,08 | 1,16 | 1,24 | - | - | |
KFv | 1,10 | 1,20 | 1,38 | 1,58 | - | - | |
KHv | 1,05 | 1,1 | - | - | - | - | |
KFv | 1,13 | 1,28 | - | - | - | - |
2.4.2. Проверку прочности зубьев по контактным напряжениям осуществляют по формуле:
, (2.16)
где - коэффициент расчетной нагрузки; KHb - коэффициент концентрации нагрузки, для прирабатывающихся зубьев KHb =1.
Если величина не превышает принятую ранее (в проектном расчёте), проверка зубьев на контактную прочность не требуется.
2.4.3. Силы, действующие в зацеплении, Н.
Окружная сила , где
- крутящий момент на ведущем валу, Н/мм.
Вторая ступень двухступенчатого редуктора .
Радиальная сила , где a = 20о - угол зацепления.
Нормальная (полная) сила .
2.4.4. Проверка прочности зубьев по напряжениям изгиба:
, (2.17)
где - коэффициент расчетной нагрузки, KFb=1- коэффициент концентрации нагрузки при расчете по напряжениям изгиба; YFi – коэффициент формы зуба, определяется по табл. 2.5 в зависимости от числа зубьев при коэффициенте смещения Х=0.
Проверку производят по зубьям того из колёс, у которого меньше значение . При расчёте двухступенчатого редуктора для второй ступени выполняют расчёт по п.п. 2.5-2.6 аналогично п.п. 2.3-2.4.
Таблица 2.5
Коэффициент формы зуба YF
z | YF | z | YF | z | YF | z | YF | z | YF | z | YF |
4,28 | 3,92 | 3,80 | 3,66 | 3,61 | 3,62 | ||||||
4,27 | 3,90 | 3,78 | 3,65 | 3,61 | ¥ | 3,63 | |||||
4,07 | 3,88 | 3,75 | 3,62 | 3,60 | |||||||
3,98 | 3,81 | 3,70 | 3,62 | 3,60 |
3 Проектный расчет валов на прочность
3.1. Выбор материала валов
В проектируемых редукторах рекомендуется применять валы из термически обработанных среднеуглеродистых или низколегированных качественных сталей 35, 40, 45 или низколегированных сталей 40Х, 40ХН, 45Х.
Механические характеристики сталей, применяемых для изготовления валов, представлены в табл. 2.1.
3.2. Выбор допускаемых напряжений
В рассматриваемой здесь методике проектный расчет валов выполняется только по напряжениям кручения. Напряжения изгиба, концентрация напряжений и переменность напряжений во времени при этом не учитываются. Поэтому, в целях компенсации приближенности проектного расчета, допускаемые напряжения на кручение применяют пониженными [tк]=20…25 МПа.
3.3. Определение геометрических параметров ступеней валов
Расчетный диаметр соответствующего участка вала в мм определяют по формуле
, (3.1)
где Т – крутящий момент на рассматриваемом валу, Н×мм.
3.3.1. Ведущий вал
Диаметр выходного конца вала d1 (под полумуфту) находят по формуле (3.1), где ;[tк]= 25 МПа.
Полученный диаметр округляют до ближайшего большего стандартного значения из ряда Ra 40 ГОСТ 6636-69.
Длину первой ступени l1 под полумуфту принимают по длине полумуфты (табл.11.2). Длины остальных ступеней и всего вала получают из эскизной компоновки.
Диаметр под уплотнение крышки с отверстием:
d1’= d1+(1...3), (мм),
в проектируемом редукторе применяются манжетные (резиновые) или войлочные уплотнения, поэтому полученное значение диаметра d1’ необходимо округлить до ближайшего стандартного значения внутреннего диаметра манжеты или войлочного кольца (см. табл.П.1, П.2).
Диаметр под подшипник:
d1’’= d1’+ (1...3), (мм),
полученное значение необходимо округлить до ближайшего стандартного значения диаметра внутреннего кольца подшипника d (см. табл.П.3).
Диаметр под шестерню:
d1’’’= d1’’+ (3...5), (мм).
Диаметр буртика d1б= d1’’’+ (3...5) (мм), ширина буртика lб=10...15,(мм).
|
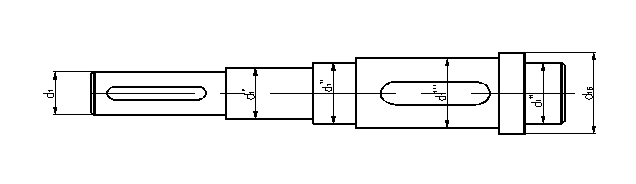
3.3.2. Промежуточный вал
Диаметр наиболее напряжённого участка вала d2’’’ под колесо первой ступени и шестерню второй ступени находят по формуле (3.1) при Т=Т2 и допускаемых напряжениях [tк]=20МПа. Диаметры под подшипники d2’’ задают по конструктивным соображениям, согласуя его с возможным диаметром внутреннего кольца подшипника (см. табл. П.3).
Рис. 3.2. Промежуточный вал
3.3.3. Ведомый вал
Определение размеров и разработка конструкции ведомого (тихоходного) вала осуществляется по аналогии с ведущим валом при Т=Т3 и допускаемых напряжениях [tк]=25 МПа. Длину выходного конца l3 принимают по длине полумуфты (табл. 11.2.).
4. Конструирование зубчатых колес
Конструкция зубчатого колеса зависит от проектных размеров, материала, способа получения заготовки и масштаба производства.
Основные конструктивные элементы колеса – обод, ступица и диск.
Обод воспринимает нагрузку от зубьев и должен быть достаточно прочным и в то же время податливым, чтобы способствовать равномерному распределению нагрузки по длине зуба.
Ступица служит для соединения колеса с валом.
Диск соединяет обод и ступицу. Иногда в диске колеса выполняют отверстия, которые используются при транспортировке и обработке колес, а при больших габаритах уменьшают массу колеса.
В проектируемых редукторах зубчатые колеса получаются, как правило, относительно небольших диаметров, поэтому их целесообразно изготавливать из круглого проката, поковок или горячештампованных заготовок. Ступицу зубчатых колес цилиндрических редукторов обычно располагают симметрично относительно обода.
Размеры колёс, полученные ранее:
dai = … (мм); | bi = … (мм); | di = di’’’= … (мм) | m = … (мм) | |
Толщина обода, мм | ![]() | |||
Внутренний диаметр ступицы, мм | dвi=di’’’. | |||
Наружный диаметр ступицы, мм | dстi=1,6di. | |||
Длина ступицы, мм | lстi=(1,0…1,5)dвi; Lст³ bi. | |||
Толщина диска, мм | С=(0,25…0,3) bi. | |||
Радиусы закруглений (мм) и уклон | R ³ 6; g ³ 7o. | |||
Размеры фасок принимают по табл. 4.1.
Для двухступенчатого редуктора определяют размеры зубчатых колёс каждой ступени.
![]() |
Рис. 4.1. Конструкция цилиндрического колеса
Таблица 4.1
Стандартные размеры фасок
Диаметр ступицы или обода, мм | св. 20 до 30 | св. 30 до 40 | св. 40 до 50 | св. 50 до 80 | св. 80 до 120 | св. 120 до 150 | св. 150 до 250 | св. 250 до 500 |
n,мм | 1,0 | 1,2 | 1,6 | 2,0 | 2,5 | 3,0 | 4,0 | 5,0 |
5. Определение геометрических размеров основных элементов корпуса и крышки редуктора
Корпус и крышка редуктора служат для размещения и координации деталей передачи, защиты их от загрязнения, организации системы смазки, а также восприятия сил, возникающих в зацеплении.
Корпус и крышку редуктора обычно изготавливают способом литья из серого чугуна марок не ниже СЧ 15 или, реже, из алюминиевого сплава АЛ 9.
Форма корпуса и крышки определяется технологическими, эксплуатационными и эстетическими условиями с учетом прочности и жесткости.
Габаритные размеры корпусных деталей (корпуса и крышки) определяются размерами находящейся в корпусе редукторной пары и кинематической схемой редуктора. Вертикальные стенки корпуса редуктора перпендикулярны, а верхняя плоскость разъема параллельна основанию. Для повышения жесткости при одновременном снижении массы корпус снабжается рёбрами жесткости. Расположение рёбер согласовывают с направлением усилий, деформирующих корпус.
Размеры основных элементов чугунного литого корпуса и крышки цилиндрического редуктора (рис.5.1).
Толщина стенки корпуса, мм | ![]() |
Толщина стенки крышки, мм | ![]() |
Толщина верхнего фланца корпуса и нижнего фланца крышки, мм | ![]() ![]() |
Толщина нижнего фланца корпуса, мм | ![]() |
Толщина ребер жесткости, мм | ![]() |
Диаметр фундаментных болтов, мм | ![]() |
Ширина опорной поверхности, мм | ![]() |
Высота h, мм | ![]() |
Диаметр болтов, крепящих крышку к корпусу, мм | ![]() |
Расстояние от края расточки до оси болта, крепящего крышку к корпусу, мм | ![]() |
Диаметр болтов, крепящих смотровую крышку, мм | ![]() |
Диаметр бобышки, мм | ![]() |
Диаметр штифтов, мм | ![]() |
Длина штифтов, мм | ![]() |
Полученные в расчете диаметры болтов округляют до ближайшего большего стандартного значения по ГОСТ 7798 – 70 (табл. П.4). Диаметр и длину штифтов назначают по ГОСТ 3129 – 70 (табл.П.9).
Ширину корпуса Е принимают одинаковой для всех бобышек.
Размер е проверяют графически на отсутствие пересечений с отверстиями винтов d4 торцевой крышки.
Размеры конструктивных элементов фланцев – ширина К1, К2 и координаты оси отверстия под болт С1, С2 выбирают в зависимости от диаметра болта из табл. 5.1.
Таблица 5.1
Конструктивные элементы фланцев, мм
Элемент фланца | Диаметр болта | ||||||
М6 | М8 | М10 | М12 | М14 | М16 | М20 | |
К | |||||||
С |
Рис. 5.1. Размеры основных элементов корпуса и крышки
Дата добавления: 2020-06-09; просмотров: 1041;