Общие сведения о металлах и сплавах 4 глава
Описание диаграммы. По линии ликвидуса АС начинается кристаллизация аустенита. На первом участке линии солидуса АЕ заканчивается кристаллизация сплавов содержащих до 2% углерода, а по линии ЕС – от 2 до 4,3% углерода. В последнем случае окончательное затвердевание расплава происходит при 1147 ºС. Одновременно из нее выпадают кристаллы аустенита, содержащего 2% углерода (точка Е) и цементита, содержащего 6,67% углерода (точка F). Кристаллы первично выпавшего аустенита и цементита образуют ледебурит (точка С). Т.е. ниже линии ЕС затвердевший сплав состоит из аустенита, цементита и ледебурита.
Эвтектика (точка С) содержит 4,3% углерода и кристаллизуется при 1147ºС в виде ледебурита.
Кристаллизация сплавов содержащих 4,3…6,67% углерода начинается по линии CD с выделением из расплава первичного цементита, в результате чего расплав обедняется углеродом. При достижении линии ECF расплав приобретает эвтектический состав (4,3 % углерода) и кристаллизуется при 1147 ºС, т.е. ниже линии CF сплав состоит из первичного цементита и ледебурита.
Структура сталей в равновесном состоянии. При 910ºС γ-железо должно переходить в α-железо, однако наличие углерода в кристаллической решетке γ-железа расширяет область его устойчивости и аустенит сохраняется при температурах ниже 910 ºС. Минимальная температура, при которой в условиях медленного охлаждения еще сохраняется аустенит, равна 727ºС, при этом в нем содержится 0,83% углерода. При дальнейшем охлаждении происходит распад твердого раствора с образованием Ф+Ц2. Продукт распада аустенита с 0,8% углерода – перлит – равномерная дисперсная смесь Ц2+ Ф (эвтектоид). По своей структуре перлит напоминает эвтектику, но в отличие от эвтектики, образующейся из расплава, перлит получается при распаде твердого раствора.
При охлаждении сталей с углеродом меньше 0,83% распад аустенита начинается с частичной перекристаллизации γ-железа в α-железо с образованием Ф, т.е. образующееся α-железо сохраняет в своей кристаллической решетке не более 0,1% углерода. Линия GS – геометрическое место критических точек начала образования феррита вследствие перекристаллизации γ-железа в α-железо. Чем больше углерода содержит аустенит, тем при более низкой температуре начинаются эти превращения при охлаждении доэвтектоидных сталей. За счет образования феррита оставшийся аустенит обогащается углеродом, и его состав по мере понижения температуры изменяется по линии GS. При температуре равной 727 ºС аустенит содержит 0,83% углерода и при охлаждении дает перлит.
Линия QPG – изменение растворимости углерода в α-железе с понижением температуры, вследствие чего из феррита выделяется углерод, взаимодействующий с железом с образованием Fe3C. Этот цементит называется третичным.
Линия РК – геометрическое место точек распада аустенита с образованием перлита – линия перлитовых превращений. При охлаждении заэвтектоидных сталей по линии SE из твердого раствора (аустенита) выделяется цементит из-за уменьшения растворимости углерода в γ-железе с понижением температуры. Чтобы отличить цементит, образующийся из жидкого раствора при затвердевании сплавов с содержанием углерода более 4,3%, от цементита, образующегося при распаде аустенита с содержанием углерода более 0,8%, последний называют вторичным цементитом. С его выделением содержание углерода в аустените падает до 0,83%, а на линии PSK – он переходит в перлит.
Сплавы с 2…4,3% углерода выше линии PSK, но ниже ЕС состоят из аустенита, вторичного цементита и ледебурита. Ниже линии PSK в этих сплавах происходит превращение аустенита в перлит. Сплавы, соответствующие эвтектике – содержат 4,3% углерода, ниже линии PSK имеют структуру одного ледебурита.
Структура белых чугунов. Доэвтектический чугун на линии содидуса ЕС состоит из аустенита и ледебурита. При дальнейшем понижении температуры вследствие уменьшения растворимости углерода в γ-железе из аустенита выделяется вторичный цементит. На линии перлитных превращений PSK при 727 ºС аустенит, содержащий 0,83% углерода, переходит в перлит. Следовательно, при температурах ниже 727 ºС белый доэвтектический чугун состоит из перлита, вторичного цементита и ледебурита.
На линии РК в ледебурите происходит вторичное превращение, связанное с переходом входящего в его состав аустенита в перлит, однако при этом сохраняется внешняя форма строения эвтектики и не утрачивается общий характер структуры ледебурита.
Эвтектический чугун состоит только из ледебурита, а заэвтектический – из ледебурита и первичного цементита в виде крупных иголок. Ледебурит является характерной структурной составляющей белых чугунов.
Железоуглеродистые сплавы в зависимости от содержания углерода имеют следующие наименования:
1) доэвтектоидная сталь (углерода меньше 0,83%) – состоит из зерен перлита и феррита;
2) эвтектоидная сталь (С=0,83%) – состоит из одного перлита;
3) заэвтектоидная сталь (С=0,83…2,0%) – состоит из зерен перлита и вторичного цементита, располагающегося в виде игл и зерен в перлитной основе;
4) доэвтектический чугун (С=2,0…4,3%) – состоит при комнатной температуре из перлита, включений цементита и ледебурита. Ледебурит при температуре меньше 727ºС состоит из перлита и цементита;
5) эвтектический чугун (С=4,3%) – структурными составляющими является ледебурит, состоящий из цементита и перлита;
6) заэвтектический чугун (С=4,3…6,67%) – состоит из цементита и ледебурита.
Нанесенные на диаграмме состояний линии, соответствующие структурным изменениям в сплаве, отмечают положение критических точек (открыты Д.К.Черновым). Линия GS называется линией верхних критических точек (АС3), линия PSK – линия нижних критических точек (АС1) или линией перлитных превращений. Линии АС1 и АС3 определяют режимы термической и горячей механической обработки для доэвтектоидных сталей. Для заэвтектоидных сталей особенно важна линия ES – линия выделения цементита.
3.7. Основы термической обработки стали
Под термической обработкой понимают нагрев или охлаждение (до температур ниже температуры плавления), проведенные по определенному режиму для изменения структуры, механических и физических свойств стали.
Открытием в 1868 году критических точек великий русский металлург Д.К.Чернов практически решил вопрос о термической обработке стали.
При медленном охлаждении сталь получается в равновесном состоянии, характеризующемся наличием в ее структуре перлита, что указывает на полное превращение (распад) аустенита. Однако, при быстром охлаждении могут быть получены различные неравновесные структуры стали.
Чтобы понять, как влияет скорость охлаждения на структуру стали, рассмотрим диаграмму изотермического распада аустенита. Для ее построения образцы стали нагревают выше АС3 (т.е. выше линии GS по диаграмме состояния), а затем быстро переносят в печь с определенной температурой для выдержки до полного распада аустенита. Превращение аустенита при постоянной температуре начинается после некоторой выдержки - инкубационного периода.
Сталь при 700 ºС сохраняет аустенитовую структуру в течение инкубационного периода, затем в точке ан начинается распад аустенита, который заканчивается в точке ак. При 600ºС – начало превращений bн, конец bк; при 400ºС – сн, ск. Соединив все точки начала и конца распада аустенита получают кривые 1 и 2. Выше линии A1 аустенит устойчив.
|
|
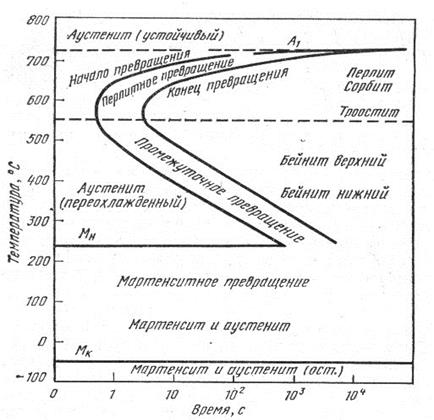
Рис.20. Изотермические превращения аустенита
В области левее кривой 1 находится переохлажденный аустенит, в области правее кривой 2 – находятся продукты распада аустенита, в области между кривыми 1-2 – происходит распад аустенита.
При изотермическом распаде аустенита, переохлажденного не ниже 700 ºС продуктом распада является равновесная структура перлит (механическая смесь феррита и цементита Fe3C), причем размеры зерен цементита более 1·10-4 см (НВ=160).
Изотермический распад эвтектоидной стали при 600…650 ºС дает структуру, которая называется сорбит. Размеры частиц цементита в этой структуре около 1·10-5 см (НВ=250…300).
Изотермический распад при температуре 450…600 ºС дает структуру – тростит (троостит), в которой частицы цементита имеют размеры около1·10-7 см (НВ=400…450). Изотермический распад при температуре 300 ºС дает так называемый игольчатый треостит (или бейнит), в котором частицы цементита еще мельче, а твердость стали еще выше, чем у сталей ранее указанных структур, но пластичность и вязкость ниже.
Табл.1. Структура железоуглеродистых сплавов
Название | Структуры | Название металлов | твердость НВ |
Аустенит | Твердый раствор углерода и других элементов в γ-железе. | Высоколегированные стали, обыкновенные стали при температурах выше 727ºС | 200…250 |
Феррит | Твердый раствор углерода (в очень малых количествах) и других элементов в α-железе. | а)чистое железо; б)доэвтектоидная сталь; в)серый и ковкий чугун; г) перлит. | |
Цементит | Химическое соединение Fe3C | а)перлит; б)заэвтектоидная сталь; в)белый чугун. | |
Перлит | Эвтектоидная смесь феррита и цементита. | а)незакаленные стали; б)чугуны. | |
Ледебурит | Эвтектическая смесь аустенита и цементита | Белый чугун | |
Графит | По составу близок к природному графиту | а)серый чугун; б)ковкий чугун. | - |
Мартенсит | Пересыщенный твердый раствор углерода в α-железе. | Стали, закаленные в среде, имеющей температуру ниже Мн. | 650…700 |
Игольчатый треостит (бейнит) | Высокодисперсная смесь частиц Fe3C с α-железом. | Стали, закаленные в среде с температурой немного выше Мн | 450…500 |
Троостит | Тонкодисперсная смесь частиц Fe3C с α-железом. | а)стали, закаленные в среде с температурой около 450ºС; б)закаленные стали с последующим низким или средним отпуском. | 400…450 |
Сорбит | Грубодисперсная смесь частиц Fe3C с α-железом. | а)стали, закаленные в среде с температурой около 600ºС; б)закаленные стали с последующим высоким отпуском. | 250…300 |
На диаграмме изотермического превращения аустенита при температуре 230ºС кривые начала и конца превращения аустенита обрываются линией Мн. Часть аустенита, переохлажденного ниже 230ºС, мгновенно превращается в мартенсит, другая часть сохраняет структуру аустенита. Чем ниже температура переохлаждения, тем больше образуется мартенсита. Ниже температуры линии Мк весь аустенит переходит в мартенсит - пересыщенный раствор углерода в α-железе с искаженной кристаллической решеткой. Чем ниже температура переохлаждения, тем больше образуется мартенсита.
Рис. 21. Влияние содержания углерода на температуру начала и конца мартенситного превращения
Положение линий Мн и Мк зависит от содержания углерода (рис.21). При повышении его содержания линии изотермического распада сдвигаются вправо и структуры мартенсита, сорбита и перлита могут быть получены при меньшей скорости охлаждения.
Для малоуглеродистых сталей значение Мн и Мк находятся в области столь высоких температур, что образовавшийся на короткий срок мартенсит немедленно распадается на более устойчивые структуры. Практически при содержании углерода меньше 0,2% в сталях нельзя получить мартенситовую структуру (они не принимают закалку).
С понижением температуры переохлаждения (ниже 240ºС – линия Мн) диффузионные процессы в стали резко замедляются, а при температурах менее минус 50ºС полностью прекращаются – линия Мк. Это приводит к тому, что из аустенита перестает выделяться углерод в виде цементита (он сохраняется в твердом растворе). Кристаллическая решетка перестраивается из гранецентрированного γ-железа в объемно-центрированное α-железо. Образовавшаяся игольчатая структура представляет собой пересыщенный твердый раствор углерода в α-железе и называется мартенситом. Это наиболее твердый продукт распада аустенита (НВ=600…650) и наименее пластичный.
В закаленной стали наряду с мартенситом имеется небольшое количество остаточного аустенита, которое зависит от содержания углерода в аустените и скорости охлаждения ниже температуры начала мартенситовых превращений (линия Мн). Т.е. диаграмма изотермического распада аустенита позволяет установить скорость охлаждения данной стали для получения требуемого строения и свойств.
Увеличение скорости охлаждения стали, что будет соответствовать увеличению степени переохлаждения аустенита относительно линии PSK (на диаграмме состояний), приводит к образованию все более мелкодисперсной структуры. Можно выбрать такую скорость охлаждения стали, при которой аустенит будет переходить непосредственно в мартенсит (критическая скорость закалки). Мартенситовое превращение ниже линии Мн не зависит от скорости охлаждения; необходимо только, чтобы аустенит был переохлажден до температуры ниже линии Мн без распада.
3.8. Виды термической обработки стали
1) Закалка – быстрое охлаждение стали, нагретой до температуры выше критических точек, дающее возможность получить структуры, обладающие высокой твердостью (мартенсит, бейнит, тростит).
При закалке доэвтектоидных сталей температура нагрева: t = AC3 + (30÷50º), при этом исходная структура целиком переходит в аустенит. При закалке заэвтектоидных сталей температура нагрева: t = AC1 + (30÷50º), т.е. исходная структура переходит в аустенит и цементит. В процессе закалки цементит не изменяется, оставаясь в закаленной стали и повышая ее твердость, а аустенит переходит в мартенсит.
Полной закалкой стали считается такая, при которой образуется мартенситовая структура и сталь приобретает максимальную твердость.
Углеродистые стали воспринимают закалку с образованием мартенсита только при содержании углерода более 0,2%. При меньшем содержании углерода в стали после закалки происходит измельчение зерен и даже повышение ее вязкости.
2) Отпуск – нагрев предварительно нагретого изделия до температур ниже АС1, для перевода неустойчивых структур (мартенсита) в более устойчивые, менее хрупкие и более вязкие.
Различают следующие виды отпуска:
а) низкий отпуск – нагрев до температур ниже 300ºС снимает внутренние напряжения в стали, сохраняя ее высокую твердость и износоустойчивость. Применяется для высокоуглеродистых сталей с высокой твердостью (режущий инструмент);
б) средний отпуск нагрев до температур в диапазоне 300…500ºС для повышения вязкости стали при сохранении высокого предела упругости и прочности. Он дает тростито-сорбитовую структуру, применяется для среднеуглеродистых сталей (при изготовлении пружин, рессор, штампов, ударного инструмента);
в) высокий отпуск – нагрев до температур 500…550ºС для получения максимальной вязкости при достаточно высоком пределе упругости и прочности. Применяется для среднеуглеродистых и низколегированных сталей. Получается сорбитовая структура (НВ=250…300), хорошо работающая при высоких напряжениях и особенно под ударной нагрузкой.
Закалку вместе с высоким отпуском называют улучшением.
3) Отжиг – нагрев стали выше критических температур, а затем медленное охлаждение для получения равновесных структур стали, соответствующих диаграмме состояния. Полный отжиг доэвтектоидных сталей заключается в нагреве до t = AC3 + (30÷50º) с выдержкой, необходимой для полной перекристаллизации по всему объему. В процессе медленного охлаждения стали в горячем песке или золе аустенит полностью распадается и образуется нормальная феррито-перлитовая структура.
Стали, подвергшиеся холодной деформации и получившие вследствие этого (наклеп) упрочнение – после холодной прокатки, волочения или холодной штамповки, отжигают при температурах AC1. При таком отжиге в наклепанной стали происходит рекристаллизация, которая заключается в переходе маловязкой холоднодеформированной структуры, состоящей из вытянутых зерен, в нормальную мелкозернистую мягкую и вязкую. Для малоуглеродистой стали такой рекристаллизационный отжиг производят при температуре около 600 ºС.
Отжиг снижает твердость стали, повышает ее пластичность и вязкость, устраняет внутренние напряжения и улучшает обрабатываемость при резании.
4) Нормализация – нагрев стали до t = AC3 + (30÷50º) с последующим охлаждением на воздухе. Сталь полностью перекристаллизовывается и приобретает более мелкозеристую и однородную структуру с большей твердостью и прочностью, но с меньшей пластичностью, чем после отжига. Нормализация как более дешевая операция часто для малоуглеродистых сталей (содержание углерода 0,2…0,3%) заменяет отжиг, для среднеуглеродистых (содержание углерода 0,3…0,5%), она иногда заменяет улучшение (закалка+высокий отпуск).
Рис. 22. Область температур нагрева для различных видов отжига и нормализации I – полный отжиг; II – неполный отжиг; III – гомогенизация (диффузионный отжиг); IV – низкий отжиг; V – нормализация
Для повышения физико-механических свойств поверхности стального изделия применяют поверхностную закалку.
Закалка в индукционном токе. Индукционный нагрев происходит вследствие теплового воздействия тока, индуктируемого в изделие, которое помещают для этого в переменное магнитное поле.
Для нагрева деталь устанавливают в соленоид, переменный ток, протекая через него, создает переменное магнитное поле. Индуктированное в изделие переменное магнитное поле приводит к появлению вихревых токов и выделению тепла в обрабатываемом изделии. Ток при этом проходит в основном по поверхности изделия - поверхностный эффект. Около 90% тепла выделяется в слое толщиной y.
- толщина слоя, мм;
- электрическое сопротивление металла;
- магнитная проницаемость;
- частота тока
Чем больше частота тока, тем меньше толщина закаленного слоя. Например:y=1 мм, f=50…60 тыс. Гц, y=4 мм, f=4 тыс. Гц при высоких скоростях нагрева (десятки и даже сотни градусов в секунду, а в печах 1,5…3 градусов в секунду). Превращения перлита в аустенит сдвигаются в область более высоких температур, поэтому, чем больше скорость нагрева в районе фазовых превращений, тем выше должна быть температура для получения оптимальной структуры и максимальной твердости.
Использование индукционного нагрева позволяет сократить длительность термообработки, получать изделие без окалины, позволяет автоматизировать процесс.
Закалка с газопламенным нагревом применяется для крупных деталей. Поверхность нагревают газовым пламенем, имеющим температуру 2400…3150 ºС. Вследствие подвода большого количества тепла поверхность изделий быстро разогревается до температуры закалки, а сердцевина не успевает нагреваться. Последующее быстрое охлаждение обеспечивает закалку поверхностного слоя. Горючее – ацетилен, природный газ, керосин. Толщина закаленного слоя 2…4 мм. Пламенная закалка вызывает меньшие деформации, чем объемная, и сохраняет чистую поверхность.
Химико-термическая обработка стали – поверхностное насыщение стали определенным элементом (углерод, азот, алюминий, хром и другие) путем его диффузии в атомарном состоянии из внешней среды в металл при высокой температуре. Химико-термическая обработка стали заключается в нагреве изделия до заданной температуры в твердой, газовой или жидкой среде, легко выделяющей диффундирующий элемент, выдержке при этой температуре с последующим охлаждением. Эта обработка меняет не только структуру, но и химический состав поверхностных слоев, что позволяет в более широких пределах изменять их физико-механические свойства.
Химико-термическая обработка состоит из трех процессов:
1) во внешней среде – выделение диффундирующего элемента в атомарном состоянии;
2) проникновения (растворения) его в решетку железа (адсобция);
3) продвижения насыщающего элемента в глубь металла – диффузия.
Глубина проникновения элемента зависит от температуры и продолжительности насыщения, а также от концентрации диффундирующего элемента на поверхности.
Цементация стали – процесс насыщения поверхностного слоя стали углеродом. В результате повышается твердость и износостойкость поверхности за счет обогащения углеродом (до 0,8…1 %) и последующей закалки. Для цементации используют низкоуглеродистые стали с содержанием углерода 0,1…0,18 %, при этом сердцевина изделий, не насыщенная углеродом, сохраняет высокую вязкость после закалки.
Температура закалки выше AC3 (930…950 ºС). Углерод диффундирует в решетку γ-железа, при достижении предела насыщения аустенита углеродом на поверхности может образоваться сплошной слой цементита. Цементированный слой имеет переменную концентрацию углерода толщиной 0,5…2 мм. Большинство легирующих элементов уменьшают диффузию углерода или концентрацию его в поверхностном слое (кроме марганца).
Цементация осуществляется:
1) твердым карбюризатором – древесный уголь, каменноугольный полукокс. Для ускорения к ним добавляют BaCO3, Na2CO3 в количестве 10…40 % от массы угля. Насыпают и утрамбовывают карбюризатор толщиной 20…30 мм на дно металлического ящика, затем укладывают слой изделий, затем слой карбюризатора 10…15 мм и новый слой изделий и т.д. Ящик накрывают крышкой, обмазывают ее глиной и помещают в печь. В ящике кислород воздуха с углеродом карбюризатора дает:
2С + О2 → 2СО,
в присутствии железа: 2СО → СО2 + Сатом.
2) газовая цементация – в среде газов, содержащих углерод:
СН4 → 2Н2 + Сатом.
Азотирование стали – диффузионное насыщение поверхностного слоя стали азотом при нагреве t=500…520 ºС в аммиаке: 2NH3 → 2N + 6H. При этом за счет диффузии азота образуются нитриды железа Fe4N, Fe3N, Fe2N, имеющие высокую твердость и нитриды легирующих элементов Cr2N, Mo2N и др.
Цианирование и нитроцементация – совместное насыщение поверхности стали углеродом и азотом, для повышения твердости и износостойкости стали с содержанием углерода 0,2…0,4%.
Диффузионная цементация – поверхностное насыщение стали алюминием, хромом, бором и другими элементами, что приводит к повышению жаростойкости, коррозионной стойкости, твердости поверхностного слоя. Поверхностное насыщение металлами производится: 1) при t=900…1050 ºС упаковкой изделий в ферросплавы-порошки, 2) погружением в расплавленный металл, если температура плавления его невысока, 3) насыщением из газовой среды.
3.9. Наклеп и старение стали
Упругая деформация в металле развивается в отдельных кристаллах за счет обратимых изменений в кристаллической решетке, в которой при этом происходит накопление внутренней потенциальной энергии. После прекращения действия сил, вызвавших упругую деформацию, внутренняя энергия производит работу обратного восстановления деформированной кристаллической решетки и тело приобретает первоначальные размеры и форму. Следовательно, в определенных пределах возрастания нагрузки кристалл будет испытывать упругие деформации, причем между напряжением σ и относительными деформациями ε будет зависимость очень близкая к линейной.
При увеличении нагрузки выше определенного предела (предел упругости) в кристалле металла возникают необратимые остаточные (пластические) деформации, которые являются следствием сдвига одних частей кристалла относительно других.
С развитием остаточной деформации в кристалле возникают явления физического упрочнения, которые затрудняют дальнейшие сдвиги. Появление такого упрочнения объясняется искажением поверхности сдвига в процессе деформирования, а также выпадением мелких обломков кристаллов в плоскостях сдвига. Это препятствует дальнейшему скольжению кристаллов и повышает тем самым сопротивление металла сдвигу.
Исследования микроструктуры металла показали, что при пластической деформации в кристаллитах (зернах) возникают необратимые сдвиги, выражающиеся в смещении слоев атомов относительно друг друга по плоскостям, наиболее плотно заполненным атомами.
При дальнейшем течении пластической деформации происходят перемещения, повороты одних зерен относительно других и разламывание их на отдельные блоки с возникновением так называемой мозаичной структуры. Это затрудняет образование сплошных плоскостей скольжения, что приводит к упрочнению металла. Упрочнение мягкой стали вызывается также выделением из феррита по плоскостям скольжения высокодисперсных частиц – оксидов, нитридов и карбидов железа, препятствующих дальнейшим сдвигам и тем самым повышающих сопротивление пластической деформации.
Упрочнение, полученное металлом в результате пластической деформации, выражающееся в повышении твердости, предела текучести σт и временного сопротивления σв и сопровождающееся снижением пластичности и вязкости, носит название наклепа. Он появляется при холодной обработке металла давлением. В строительстве наклеп используют для повышения σт арматуры железобетонных изделий. Для этого арматуру подвергают рифлению или холодной вытяжке.
С повышением степени деформации сопротивление металла деформированию возрастает, но способность к пластическому деформированию утрачивается и при достижении известного предела металл разрушается. Если металл обладает повышенным сопротивлением сдвигу, то разрушение происходит без пластической деформации (хрупкое разрушение) и с меньшей затратой работы. Хрупкое разрушение может наблюдаться и для пластичного металла при резких изменениях формы детали, пониженных температурах, ударных нагрузках. При длительном воздействии повторно-переменных нагрузок возникает усталостное разрушение.
Поверхностный наклеп создается обработкой поверхности металла струей чугунной дроби или обкаткой роликами.
Наклепанный металл вследствие искаженной кристаллической решетки испытывает внутренние напряжения, которые можно ликвидировать низкотемпературным нагревом. Снятие внутренних напряжений в процессе нагрева наклепанного металла, при котором в его микроструктуре происходят изменения, называется возвратом. Дальнейший нагрев наклепанного металла приводит к изменению микроструктуры с понижением твердости, прочности и повышением пластичности и вязкости. Такое изменение микроструктуры наклепанного металла называется рекристаллизацией. Для низкоуглеродистой стали температура рекристаллизации около 600 ºС. После такого отжига сталь приобретает свойства, соответствующие ее равновесному состоянию.
Повышение прочности и понижение пластичности может продолжаться и после снятия нагрузки, вызвавшей пластическую деформацию; это явление называется механическим старением.
Старение сталей при комнатной температуре – естественное старение, ускоряется с повышением температуры. Старение в нагретом состоянии – искусственное старение. При нагреве до температур 200…400 ºС наклепанная мягкая сталь утрачивает пластичность и делается хрупкой вследствие мгновенного протекания процесса старения. Это явление называется синеломкость, ему особенно подвержены кипящие стали. Конверторные стали показывают большую склонность к старению, чем даже кипящая мартеновская сталь. Хорошо раскисленная мартеновская сталь практически не стареет. Старению подвержены не только наклепанные, но и быстроохлажденные стали.
Дата добавления: 2020-02-05; просмотров: 553;