Устройство адсорберов и схемы адсорбционных установок
Процессы адсорбции могут проводиться периодически (в аппаратах с неподвижным слоем адсорбента) и непрерывно — в аппаратах с движущимся или кипящим слоем адсорбента, а также в аппаратах с неподвижным слоем — в установке из двух или большего числа адсорберов, в которых отдельные стадии процесса протекают не одновременно.
|
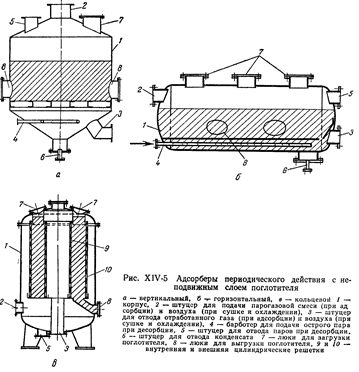
Адсорберы с неподвижным слоем поглотителя. Наиболее часто применяются цилиндрические адсорберы вертикального (рис. XVII-1,а) и горизонтального (рис. XVII-1,б) типов. Адсорберы со слоем поглотителя кольцевого сечения (рис. XVII-1, б) используются сравнительно редко.
Периодические процессы адсорбции часто проводятся четырехфазным способом, при котором процесс проходит в четыре стадии.
Первая стадия — собственно адсорбция, т.е. насыщение поглотителя адсорбируемым компонентом. Парогазовая смесь подается в корпус 7 аппарата (рис. XVII-1) через штуцер 2, проходит через слой поглотителя (на рисунке заштрихован) и выходит через штуцер 3.
Вторая стадия — десорбция поглощенного компонента из поглотителя. Подача парогазовой смеси прекращается, и в аппарат подается водяной пар через барботер 4 (рис. XVII-1,а, б) или через штуцер 3 (рис. XVII-1,б). Смесь паров десорбированного компонента и воды удаляется через штуцер 5. Конденсат пара отводится из аппарата после десорбции через штуцер 6 (рис. XVII-1,а, б) или 5 (рис. XVII-1,в),
Третья стадия — сушка поглотителя. Перекрывается вход и выход водяного пара, после чего влажный поглотитель сушится горячим воздухом, поступающим в аппарат через штуцер 2 и выходящим из аппарата через штуцер 3.
Четвертая стадия — охлаждение поглотителя. Прекращается подача горячего воздуха, после чего поглотитель охлаждается холодным воздухом, поступающим в аппарат также через штуцер 2; отработанный воздух удаляется через штуцер 3.
По окончании четвертой стадии цикл работы аппарата начинается снова. Загрузку и выгрузку поглотителя производят периодически через люки 7 и 8.
В случае отсутствия одной из последних двух стадий (охлаждение угля или его осушка) метод проведения процесса будет называться трехфазным.
Существует также двухфазный метод, при котором в прошедший регенерацию водяным паром горячий и влажный уголь подаются последовательно горячая и холодная паро-воздушная смесь (первая стадия). При этом процессы сушки и охлаждения угля идут одновременно с процессом поглощения. По окончании первой стадии осуществляется десорбция поглощенных веществ водяным паром (вторая стадия).
Выбор метода работы производится на основании технико-экономических показателей.
|
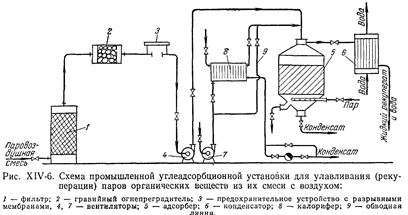
Для уменьшения потерь тепла в окружающую среду (при десорбции и сушке поглотителя) адсорберы покрывают тепловой изоляцией.
Установки для периодической адсорбции, помимо основного аппарата-адсорбера, включают вспомогательное оборудование. На рис. XVII-2 приведена схема установки для улавливания паров органических веществ из их смеси с воздухом; Перед поступлением в адсорбер паро-воздушная смесь проходит через фильтр 1, где очищается от пыли. Это предотвращает засорение трубопроводов и быстрое снижение активности поглотителя. Смеси паров органических веществ с воздухом часто взрывоопасны (при определенных соотношениях паров и воздуха). Поэтому после фильтра смесь проходит огнепреградитель 2 — емкость, заполненную материалом с высокой теплоемкостью (обычно гравием). В случае загорания смеси в этом аппарате поток охлаждается до температуры, значительно меньшей температуры ее воспламенения, и этим предотвращается распространение пламени внутри установки. Далее смесь проходит через предохранительное устройство 3, основной частью которого является обычно мембрана, разрывающаяся при увеличении давления в трубопроводе сверх допустимого.
Выходящая из предохранительного устройства паро-воздушная смесь при адсорбции (первая стадия) вентилятором или газодувкой 4 подается в адсорбер 5. При десорбции (вторая стадия) выходящие из адсорбера пары конденсируются в конденсаторе 6. Получаемый конденсат (называемый рекуператом) разделяется ректификацией или путем расслаивания в сепараторе, если десорбируемый компонент не смешивается с водой. При сушке адсорбента (третья стадия) в адсорбер вентилятором 7 подается воздух, предварительно нагретый в калорифере 8. При охлаждении адсорбента (четвертая стадия) подаваемый в адсорбер вентилятором 7 воздух проходит по обводной линии 9, минуя калорифер.
Несмотря на то, что адсорбер в описанной установке работает периодически, вся установка в целом может работать непрерывно при наличии нескольких (минимально — двух) адсорберов, включаемых поочередно и работающих со сдвигом стадий (например, при адсорбции в одном аппарате в другом может происходить десорбция),
Адсорберы с движущимся слоем поглотителя. Принцип работы адсорберов этого типа был указан ранее. Исходная газовая смесь поступает в колонну под распределительную тарелку 1 (рис. XVII-3), представляющую собой трубную решетку с направленными вниз патрубками. Через патрубки газовая смесь поднимается в адсорбционную зону I, где взаимодействует с движущимся слоем активного угля, охлажденного в трубах холодильника 2. В зоне I поглощаемые компоненты извлекаются углем, а не поглощенная часть смеси (легкая фракция) отводится через штуцер, расположенный под распределительной тарелкой 3.
Из зоны I уголь проходит в нижерасположенную ректификационную зону II, ограниченную распределительными тарелками 1 и 4. В зоне II поднимающиеся из нижней части колонны пары вытесняют из угля менее сорбируемые компоненты, образуя при этом смеси различных составов (промежуточные фракции). На схеме показан отбор одной промежуточной фракции из-под третьей (сверху) тарелки (4а). Состав промежуточной фракции зависит от места ее отбора (по высоте ректификационной зоны). В некоторых случаях по высоте зоны II отбирают несколько промежуточных фракций.
Из зоны II уголь поступает через распределительную тарелку 4 в десорбционную (или отпарную) зону III, где он проходит по трубам,, обогреваемым снаружи чаще всего парами высокотемпературных теплоносителей. Одновременно уголь в трубах продувают острым перегретым водяным паром. Острый пар, не конденсируясь, выдувает из угля десорбируемые вещества. Эти вещества в смеси с водяным паром (тяжелая фракция) отводится под распределительной тарелкой 4. Часть тяжелой фракции направляется в зону II для выделения из угля менее сорбируемых компонентов и образования промежуточных фракций.
Распределительные тарелки обеспечивают более равномерное распределение газа и угля по сечению колонны и уменьшение уноса частиц угля выходящими газами.
Нагретый уголь выводится из аппарата через разгрузочное устройство 5. Далее уголь проходит гидрозатвор 6, который предотвращает выход пара из аппарата и попадание его с углем в газовый подъемник 7. В последний уголь поступает через регулирующий клапан 8 и промежуточный сборник 9. В токе воздуха (или другого газа), нагнетаемого вентилятором (или газодувкой) 10, уголь подается в бункер 11, из которого ссыпается в водяной холодильник 2 и затем в зону I адсорбционной колонны. Описанный цикл работы адсорбера повторяется снова. Для компенсации потерь угля вследствие его истирания, а также для поддержания постоянного уровня загрузки в бункере 11 в него добавляют свежий уголь.
Разделяемый газ может содержать труднодесорбируемые вещества, не выделяющиеся в десорбционной зоне из угля и, следовательно, снижающие его активность. В этих случаях часть угля из бункера направляют в реактиватор 12 — аппарат, нагреваемый до температуры более высокой, чем десорбер колонны. В реактиваторе, так же как и в десорбционной зоне колонны, обрабатывают уголь острым водяным паром. Продукты реактивации и водяной пар отводят из верхней части реактиватора. При дополнительной обработке в реактиваторе активность угля не снижается даже при длительной работе установки.
Адсорберы с кипящим слоем поглотителя. В кипящем слое размеры частиц адсорбента меньше, чем размеры его частиц в неподвижном слое, что способствует уменьшению внутридиффузионного сопротивления твердой фазы и приводит к существенному увеличению поверхности контакта фаз. В кипящем слое при прочих равных условиях интенсивность внешнего массопереноса также выше, чем в неподвижном слое, вследствие больших скоростей газа, движущегося через слой.
Вместе с тем проведение процессов адсорбции в кипящем слое связано с трудностями выбора механически прочного адсорбента, способного выдержать достаточное число циклов работы в условиях повышенной истираемости при интенсивном механическом перемешивании частиц в самом аппарате и пневмотранспортных трубах.
В промышленности обычно применяются непрерывно действующие многокамерные адсорберы с кипящим слоем.
На рис. XVII-4 показан однокамерный адсорбер с кипящим слоем, в котором газ непрерывно движется через корпус 1 снизу вверх, поддерживая находящийся на газораспределительной решетке слой адсорбента в псевдоожиженном состоянии. Газ удаляется из аппарата через циклонное устройство 2, служащее для выделения из газа захваченных им мелких частиц адсорбента.
В однокамерных аппаратах такого типа интенсивное перемешивание твердых частиц приводит к значительной неравномерности времени пребывания в слое и соответственно различию степени их насыщения поглощаемым компонентом. В этих аппаратах, работающих по принципу прямотока фаз, не удается достичь концентрации адсорбтива в газовой фазе меньшей, чем равновесная, которая соответствует средней концентрации адсорбента в слое.
|
|
|
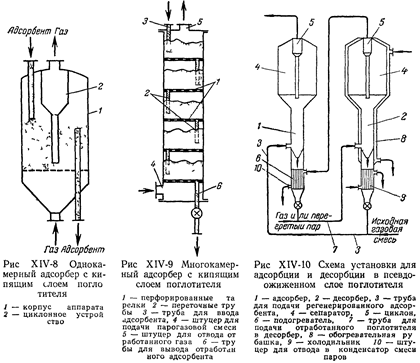
Указанные недостатки, присущие и другим одноступенчатым (односекционным) массообменным аппаратам, можно в значительной мере преодолеть при использовании многосекционных аппаратов, в которых взаимодействие фаз приближается к противоточному.
В многокамерном адсорбере с кипящим слоем (рис. XVII-5) газ последовательно проходит через перфорированные тарелки (газораспределительные решетки) 1, имеющие переточные трубы 2, по которым твердые частицы адсорбента «стекают» со ступени на ступень, противотоком к потоку газа. При псевдоожиженном адсорбенте на каждой ступени взаимодействие фаз приближается к режиму идеального смещения, в то время как для аппарата в целом это взаимодействие близко к режиму идеального вытеснения. В таких условиях газ более равномерно распределяется по площади поперечного сечения аппарата, сводится к минимуму «проскок» газа без взаимодействия с адсорбентом и увеличивается время взаимодействия фаз. В результате достигается более равномерная и полная «отработка» зерен адсорбента.
На рис. XVII-6 приведена схема установки, в которой и адсорбция и десорбция осуществляются в псевдоожиженном слое поглотителя. Адсорбер 1 и десорбер 2 имеют цилиндрический корпус с коническим днищем. Выходящий из десорбера регенерированный поглотитель увлекается потоком исходной парогазовой смеси и подается в адсорбер по трубе 3. Скорость газа в адсорбере должна быть такой, чтобы зернистый поглотитель находился в нем в псевдоожиженном состоянии.
Непоглощенная часть газовой смеси через сепаратор 4 и циклон 5 удаляется из аппарата. Отработанный поглотитель отводится из нижней части адсорбера, нагревается в теплообменнике 6 и поступает в трубу 7, где увлекается десорбирующим агентом (например, перегретым водяным паром), и подается в десорбер, снабженный обогревательной рубашкой 8. В десорбере скорость десорбирующего агента должна быть такой, чтобы поглотитель находился в псевдоожиженном состоянии. Регенерированный поглотитель отводится из нижней части десорбера, охлаждается в теплообменнике 9, поступает в трубу 3, и цикл начинается снова. Смесь паров воды и десорбированных веществ выходит из десорбера через сепаратор 4 и циклон 5, поступает в качестве нагревающего агента в теплообменник 6, а затем выходит через штуцер 10 в конденсатор.
Дата добавления: 2016-10-18; просмотров: 12553;