Устройство экстракционных аппаратов
К конструкции аппаратов, в которых проводят процессы экстракции и растворения, предъявляются следующие основные требования:
1) высокая удельная производительность, характеризуемая выходом раствора с единицы рабочего объема аппарата;
2) возможно более высокая концентрация получаемого раствора;
3) низкий расход энергии на единицу объема конечного раствора.
Аппараты для экстракции и растворения делятся на периодически и непрерывно действующие. В зависимости от взаимного направления движения фаз различают аппараты прямоточные и противоточные, а также аппараты, работающие по принципу смешанного тока.
По способу создания скорости обтекания твердых частиц жидкостью различают аппараты: неподвижным слоем твердого материала, с механическим перемешиванием и со взвешенным, или кипящим, слоем.
Аппараты периодического действия вследствие низкой производительности применяются лишь в малотоннажных производствах и представляют собой обычно аппараты (реакторы) без перемешивающих устройств, снабженные обогревом, и аппараты с мешалками. В промышленной практике все большее распространение получают непрерывно действующие аппараты.
Аппараты с неподвижным слоем твердого материала. В этих аппаратах скорость движения жидкости при ее фильтровании сквозь слой практически совпадает по величине я направлению со скоростью обтекания. Простейшим аппаратом такого типа является открытый резервуар с ложным днищем (решеткой), подобный открытому нутч-фильтру. На решетку загружается слой твердого материала, через который сверху вниз протекает растворитель. При таком направлении движения жидкость равномерно заполняет сечение аппарата и не происходит смешения более концентрированного раствора с раствором низкой концентрации, приводящего к снижению движущей силы. Выгрузку выщелаченного твердого остатка производят периодически, чаще всего гидравлическим способом — вымывая твердый материал из аппарата водой.
|
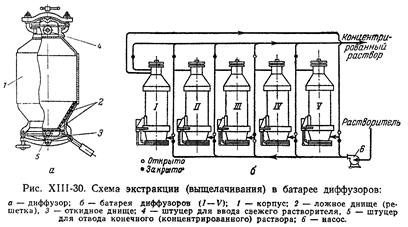
При движении жидкости сквозь слой относительно небольшой высоты не удается получить раствор достаточно высокой концентрации. Использование циркуляции жидкости для укрепления раствора нецелесообразно ввиду указанного выше вредного эффекта смешения растворов разной концентрации. Поэтому для повышения степени извлечения и увеличения производительности применяют герметически закрытые аппараты с ложным днищем, подобные закрытым нутч-фильтрам, получившие название диффузоров.
Диффузор (рис. XVI-14, а) состоит из цилиндрического корпуса 1, ложного днища, или решетки, 2 и откидного днища 3. Свежий растворитель поступает через штуцер 4, а конечный раствор удаляется через штуцер 5. Диффузоры соединяются последовательно в батареи и работают под избыточным давлением. При этом растворитель прокачивается одним насосом 6 снизу вверх последовательно через все аппараты батареи, в которых в данный момент происходит выщелачивание. Общее число диффузоров в батарее зависит от скорости процесса и может достигать 10-15 и более. В любой рассматриваемый момент один из аппаратов, в котором уже достигнута заданная степень извлечения, отключается на разгрузку выщелоченного материала и загрузку свежим материалом. В это время в остальных аппаратах (исключая один из аппаратов, находящийся обычно в резерве) осуществляется выщелачивание. Периодическая разгрузка выщелоченного материала производится самотеком под давлением через нижний люк, снабженный откидным днищем и ручным (рис. ХVI-14, а) или гидравлическим затвором.
Батарея диффузоров работает по принципу противотока, т.е. свежий растворитель взаимодействует с уже в значительной степени выщелоченным материалом, а наиболее концентрированный раствор — со свежим твердым материалом. В современных установках смена операций в условиях полунепрерывной работы диффузоров осуществляется автоматически.
Существенным недостатком аппаратов с неподвижным слоем является неравномерность обтекания твердых частиц жидкостью и образование застойных зон вблизи точек соприкосновения частиц. Увеличение скорости фильтрования ограничивается уносом мелких частиц жидкостью и значительным возрастанием гидравлического сопротивления. Поэтому такие аппараты постепенно вытесняются аппаратами непрерывного действия.
Непрерывно действующие аппараты с механическим перемешиванием. Одним из распространенных аппаратов этой группы является шнековый экстрактор (рис. XVI-15). Он представляет собой горизонтальное корыто, или желоб 1, в котором вращается горизонтальный вал 2 с укрепленными на нем спиральными лопастями 3 и крестовинами 4.
Растворяемый твердый материал непрерывно поступает через штуцер 5, а жидкость (растворитель) — через штуцер 6 и движутся прямотоком друг к другу, причем твердый материал перемещается вдоль корыта с помощью спиральных лопастей. На лопастях укреплены дополнительные лопасти-скребки 7, которые приподнимают и сбрасывают твердые частицы, осуществляя перемешивание материала на различных участках корыта в вертикальной плоскости. Для ускорения процесса жидкость в корыте нагревается острым паром, поступающим через сопла 8 (рис. XVI-15), или глухим паром через рубашку.
При движении вдоль аппарата раствор многократно направляется книзу посредством козырьков 9; это улучшает контакт между жидкой и твердой фазами. Концентрированный раствор удаляется с противоположного конца аппарата через сливной штуцер в верхней части корыта (на рисунке не изображен), а нерастворенный остаток твердого материала отводится с помощью наклонного элеватора 10. Ковши 11 элеватора имеют ситчатые стенки для отделения жидкости, сливающейся через штуцер 12.
Шнековые аппараты могут работать как по принципу прямотока, так и противотока фаз, причем чем интенсивнее перемешивание фаз в поперечном сечении аппарата, тем полнее могут быть использованы преимущества противотока.
Иногда шнековые аппараты работают комбинированным способом. Процесс проводится в двух последовательно соединенных аппаратах, из которых в один, поступает исходный твердый материал, а в другой — свежий растворитель. При этом в первом (по ходу твердой фазы) аппарате фазы движутся прямотоком, а во втором — противотоком.
Аппараты такого типа надежны в работе и обеспечивают высокие производительности. Наряду с этим они металлоемки, громоздки и требуют сравнительно больших расходов электроэнергии. Удельная производительность шнековых аппаратов (на единицу объема или веса аппарата) невелика, что объясняется относительно низкой скоростью обтекания частиц и умеренной величиной поверхности соприкосновения фаз. Контакт между фазами ухудшается вследствие «проскока» некоторой части жидкости, обусловленного заметным расслоением фаз, так как значительная часть твердого материала перемещается в виде более плотного слоя вдоль нижней части корыта.
Несколько более эффективно протекает процесс в барабанном экстракторе (рис. XVI-16). Аппарат представляет собой горизонтальный цилиндрический барабан 1, закрытый с торцов передней крышкой 2 и задней крышкой 3. Через штуцер 4 в передней крышке поступает измельченный твердый материал, который транспортируется движущейся в том же направлении жидкостью (растворителем). Барабан 1 установлен на бандажах 5, опирающихся на ролики 6; он приводится во вращение через зубчатую передачу 7 и червячный редуктор 8 электродвигателем 9.
|
В барабанных экстракторах достигаются большие удельные производительности и более высокие коэффициенты массоотдачи (вследствие большей скорости обтекания частиц), чем в шнековых аппаратах. Улучшение массоотдачи связано с систематическим обновлением поверхности контакта фаз при пересыпании твердых частиц внутри барабана.
В некоторых случаях экстракцию можно эффективно совмещать с мокрым измельчением твердого материала и осуществлять в одном аппарате, например в трубной мельнице. Проведение экстракции одновременно с размолом способствует созданию значительной и непрерывно обновляемой поверхности соприкосновения фаз.
Аппараты со взвешенным, или кипящим, слоем. В таких аппаратах практически вся поверхность твердых частиц в течение всего процесса доступна для взаимодействия с турбулентно движущимся потоком жидкости, что способствует интенсификации процесса экстракции.
Трубчатый экстрактор (рис. XVI-17) состоит из ряда последовательно соединенных труб 1, через которые с помощью насоса 2 прокачивается жидкость (растворитель) со взвешенными в ней мелкими твердыми частицами. Для проведения процесса при повышенной температуре трубы снабжаются паровыми рубашками 3. При внезапной остановке насоса 2 через штуцер 4 подается промывная вода для того, чтобы удалить твердый материал из системы и предотвратить его осаждение в трубах. Ускорение процесса экстракции достигается вследствие того, что твердые частицы взаимодействуют с растворителем, находясь во взвешенном состоянии, и аппарат работает в условиях, приближающихся к режиму идеального вытеснения.
Применению противотока в трубчатых растворителях препятствует значительный унос мелких твердых частиц жидкостью. В данном случае можно эффективно использовать работу растворителей по схеме ступенчатого противотока: несколько аппаратов, работающих при прямоточном движении фаз, объединяются в секции, соединение которых между собой осуществляется по принципу противотока.
Одна из конструкций колонных аппаратов с пеевдоожиженным (кипящим) слоем показана на рис. XVI-18. В цилиндрическую колонну 1 через нижний штуцер 2 непрерывно поступает жидкость (растворитель), которая, проходя с необходимой скоростью сквозь отверстия распределительной решетки 3, приводит слой мелкораздробленных твердых частиц в псевдоожиженное состояние.
При высоте кипящего слоя, равной нескольким метрам, удается получить на выходе из него раствор достаточно высокой концентрации, который поступает в верхнюю, расширенную часть колонны, переливается в кольцевой желоб 4 и удаляется через штуцер 5. Твердый остаток непрерывно отводится через штуцер 6, расположенный несколько выше решетки 3. Исходный твердый материал подается непосредственно в кипящий слой сверху через загрузочную трубу 7.
Аппараты такого типа отличаются простотой устройства и небольшим весом. В них достигаются значительная скорость процесса и достаточно высокая степень извлечения целевых компонентов из исходного твердого материала.
ЛЕКЦИЯ 9
XVII. АДСОРБЦИЯ
1. Общие сведения
2. Характеристики адсорбентов и их виды
3. Десорбция
4. Устройство адсорберов и схемы адсорбционных установок
5. Ионообменные процессы
Общие сведения
Под адсорбцией мы будем понимать процесс поглощения одного или нескольких компонентов из газовой смеси или раствора твердым веществом — адсорбентом. Поглощаемое вещество носит название адсорбата, или адсорбтива.
Процессы адсорбции (как и другие процессы массопередачи) избирательны и обычно обратимы. Благодаря их обратимости становится возможным выделение поглощенных веществ из адсорбента, или проведение процесса десорбции.
Механизм процесса адсорбции отличается от механизма абсорбции, вследствие того, что извлечение веществ осуществляется твердым, а не жидким поглотителем. Каждый из этих сорбционных процессов имеет свои области применения, где его использование дает больший технико-экономический эффект.
Адсорбция применяется главным образом при небольших концентрациях поглощаемого вещества в исходной смеси, когда требуется достичь практически полного извлечения адсорбтива. В тех случаях, когда концентрация поглощаемого вещества в исходной смеси велика, обычно выгоднее использовать абсорбцию.
Процессы адсорбции широко применяются в промышленности при очистке и осушке газов, очистке и осветлении растворов, разделении смесей газов или паров, в частности при извлечении летучих растворителей из их смеси с воздухом или другими газами (рекуперация летучих растворителей) и т.д. Еще сравнительно недавно адсорбция применялась в основном для осветления растворов и очистки воздуха в противогазах. В настоящее время ее используют для очистки аммиака перед контактным окислением, осушки природного газа, выделения и очистки мономеров в производствах синтетического каучука, смол и пластических масс, выделения ароматических углеводородов из коксового газа и для многих других целей. В ряде случаев после адсорбции поглощенные вещества выделяют (десорбируют) из поглотителя. Процессы адсорбции часто сопутствуют гетерогенному катализу, когда исходные реагенты адсорбируются на катализаторе, а продукты реакции десорбируются, например, при каталитическом окислении диоксида серы в триоксид на поверхности платинового катализатора и др.
Значение адсорбционных процессов сильно возросло за последнее время вследствие расширения потребности в веществах высокой чистоты.
Различают физическую и химическую адсорбцию. Физическая адсорбция обусловлена взаимным притяжением молекул адсорбата и адсорбента под действием сил Ван-дер-Ваальса и не сопровождается химическим взаимодействием адсорбированного вещества с поглотителем. При химической адсорбции, или хемосорбции, в результате химической реакции между молекулами поглощенного вещества и поверхностными молекулами поглотителя возникает химическая связь.
При поглощении паров адсорбция иногда сопровождается заполнением пор адсорбента жидкостью, образующейся в результате конденсации паров (капиллярная конденсация). Конденсация происходит вследствие понижения давления пара над вогнутым под действием сил поверхностного натяжения мениском жидкости в капиллярах.
Дата добавления: 2016-10-18; просмотров: 4577;