Обзор патентов в области разработки устройств для триботехнических испытаний
Актуальность проблемы триботехнических испытаний материалов подтверждается стабильно высоким числом ежегодно патентуемых устройств [1-9,11-19] и способов испытаний триботехнических материалов, а также публикаций на эту тему [10, 20, 21].
В Тверском политехническом институте [5] разработано устройство (рис. 1.32), содержащее основание 1, держатель 2 контробразца, связанного с приводами вращения контробразца 3, связанного с приводом 4 вращения контробразца 3, силоизмеритель, состоящий из держателя 5 образца 6 и кольца 7. На кольце 7 размещены тензодатчики 9 для измерения усилий, прикладываемых к образцу. Устройство содержит также блок 10 задания и поддержания постоянной нормальной нагрузки, прикладываемой к образцу 6 и контробразцу 3. Выход блока 10 соединен со входом устройства нагружения 11, выполненного в виде силового привода 11 возвратно-поступательного перемещения, а его вход - с выходами тензодатчиков 9.
Недостатком описанного устройства также является ограниченность области применения из-за возможности реализации только одной схемы трения скольжения (диск по диску). Кроем того, такая схема не позволяет получить адекватные результаты испытаний на трение скольжения, поскольку в центре трущихся торцами дисков существует область с практически нулевой скоростью, что вызовет неравномерный износ образца.
Рис. 1.32 Машина трения Сутягина О.В. и Деменкова Э.А.
В патенте РФ № 2244290 (Томский государственный архитектурно-строительный университет, 2005г.) предложено устройство для испытаний материалов на трение (рис. 1.33). Устройство содержит основание 2, установленную на основании платформу 3 на катках 8 с расположенными на ней держателями 4, 7 с пазами, в которых размещаются образец 5 и контробразец 6. Также устройство содержит привод возвратно-поступательного перемещения 9, 10, узел нагружения образца 11, 15, 16, датчики регистрации усилий и перемещения, совмещенные с индикаторами 14, 17, 19 и соединенные с держателями, компьютер 22 с которым связаны датчики. При этом узел нагружения выполнен в виде винтового домкрата, соединенного с реверсивным двигателем 15 и динамометром 14, и установлен на тележке 12 с катками 13. Каждый датчик выполнен оптико-механическим в виде диска с прорезями, надетого на ось для стрелки соответствующего индикатора между излучателем и фотодатчиком. Технический результат – повышение точности испытаний.
Рис. 1.33. Устройство для испытаний на трение.
Недостатками данного устройства является неоправданное усложнение конструкции датчиков, что неизбежно вызовет удорожание и отсутствие ремонтопригодности устройства. Фоторезисторы, используемые в оптических датчиках весьма чувствительны к изменению температуры окружающей среды, что может привести к снижению точности оценки измеряемых параметров. При измерении силы трения между образцом и контробразцом неизбежно возникнет погрешность вследствие трения катков о платформу. Относительно большая площадь соприкосновения образца и контробразца создаст значительные сложности при испытаниях тяжелонагруженных пар трения. Отсутствие чашки не позволит провести испытания материалов в смазочном масле. Устройство ограничено испытаниями по схеме «плоскость-плоскость» при возвратно-поступательном движении.
Аналогичные недостатки имеет другой вариант конструкции машины для испытаний материалов на трение при возвратно-поступательном движении тех же авторов, описанная в патенте РФ №2289119 (2006г.). Данное устройство состоит из привода возвратно-поступательного движения (рис. 1.34), узла нагружения, держателей образцов и измерительной системы.
|
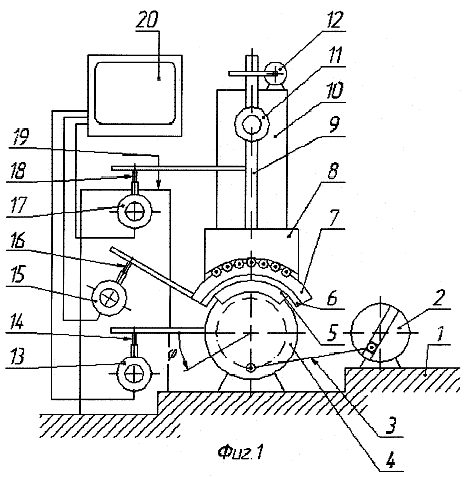
Рис. 1.34. Машина для испытаний на трение при
возвратно-поступательном движении.
В качестве держателя образца используется вал 4, соединенный с помощью кривошипно-шатунного механизма с приводом возвратно-поступательного движения, выполрненного с возможностью задания угла поворота вала и скорости его вращения при повороте на заданный угол. Сверху образца 5 установлен контробразец 6 со своим держателем 7. Узел нагружения образцов опирается катками на держатель контробразца. Измерительная система включает индикатор усилий, соединенный с держателем контробразца, индикатор перемещения образца, соединенный с его держателем, индикатор подаваемой нагрузки, соединенный с узлом нагружения образцов, оптико-механические датчики, каждый из которых выполнен в виде диска с прорезями, надетого на ось стрелки соответствующего индикатора между излучателем и фотодатчиком, и соединен через порт мыши с компьютером. Заявленный технический результат – повышение точности оценки триботехнических характеристик круглых и сферических тел при их вращении.
Основной недостаток – функциональная ограниченность стенда при достаточно сложном исполнении.
В патенте № 1711572 (АО Авиационная корпорация "Рубин", 1999г.) [8] описано устройство для испытаний материалов на трение и износ, содержащее основание и установленные на нем сферическую опору, сферическую пяту для закрепления контробразца, держатель образца с приводом его вращения, пневматический узел предварительного нагружения и датчики измерения соответственно момента трения и износа, в котором с целью повышения точности и производительности путем обеспечения испытаний пары трения в широком диапазоне скоростей скольжения, оно снабжено датчиком измерения скорости скольжения образца по контробразцу и узлом нагружения дополнительной и автоматической регулировки, выполненным в виде насоса с механизмом регулирования нагрузки, бака, силового гидроцилиндра, сообщенного с линией нагнетания насоса, и двухпозиционного гидравлического распределителя с электромагнитным управлением, гидравлический вход которого сообщен с линией нагнетания насоса, гидравлический выход - с баком, а электрический вход соединен с выходами датчиков измерения момента трения, скорости скольжения и износа, при этом поршень силового гидроцилиндра жестко связан со сферической опорой, а гидроцилиндр - с основанием.
Преимущество установки заключается в возможности проведения испытаний при форсированных нагрузках за счет использования гидроаппаратуры. Недостатки устройства: 1) функциональная ограниченность (исследуется только трение скольжения); 2) гидроаппаратура существенно усложняет и удорожает установку; 3) использование датчика износа видится неэффективным, поскольку температурные деформации материалов при нагреве из-за трения, как правило, превышают величины износа; 4) отсутствие контроля температуры при испытаниях может привести к неадекватным выводам, касающихся оценки износостойкости материалов.
В патенте [9], описана новая конструкция известной трехшариковой машины трения, предназначенной для проведения испытаний смазочных материалов, разработанной в Сибирской государственной автомобильно-дорожной академии. В развитие ранее известных технических решений [10, 11] новая трехшариковая машина трения скольжения (рис. 1.35) содержит электродвигатель 1, ременную передачу 2, приводной вал 3, муфту 4 приводного вала 3, узел трения, включающий исследуемые шары 5, установленные на опорной поверхности, опорный подшипник 6, опору 7, скользящую втулку 8, на которую воздействует система нагружения в виде двуплечного рычага 9, груза 10 и опорного конуса 11, при этом машина трения снабжена тиристорной системой 12, соединенной с источником питания 13 и с электродвигателем 1, поворотной втулкой 14, в которой выполнен вертикальный паз 15, напротив которого жестко закреплен упор 16, при этом в опоре 7 выполнен вертикальный паз 17, в котором размещен направляющий штифт 18, закрепленный на скользящей втулке 8, причем в верхней части скользящей втулки 8 жестко закреплена вертикальная стойка 19, в верхней части которой закреплена тензобалка 20, проходящая через вертикальный паз 15 поворотной втулки 14 и контактирующая с упором 16 поворотной втулки 14, при этом узел трения включает три шара 5, установленных в сепараторе 21 и закрепленных прижимной крышкой 22 посредством болтового соединения 23, а междушарами 5 и прижимной крышкой 22 установлены стальные шлифованные прокладки 24.
Рис. 1.35. Четырехшариковая машина трения.
Муфта 4 снабжена фланцем 25, на котором закреплены пальцы 26, нижние концы которых размещены в отверстиях 27, выполненных в прижимной крышке 22 узла трения с возможностью вертикального перемещения, а опорная поверхность шаров 5 выполнена в виде плоского стального кольца 28, зафиксированного на поворотной втулке посредством стопорного винта 29, причем в центре сепаратора 21 установлен штифт 30, обеспечивающий центрирование прижимной крышки 22 относительно сепаратора 21, а между муфтой 4 приводного вала 3 и прижимной крышкой 22 узла трения установлен шар 31 для обеспечения самоустановки узла трения с шарами 5 относительно плоской поверхности кольца 28.
Перед началом приработки собирают узел трения следующим образом. Шары 5устанавливаются в сепараторе 21, поверх шаров 5 устанавливается шлифованная прокладка 24, на которую устанавливается прижимная крышка 22 и затягивается посредством болтового соединения 23. Равномерное выступание шаров 5 относительно нижней торцевой поверхности сепаратора 21 регулируется усилием затяжки болтового соединения 23 и контролируется микрометром измерением расстояния от верхней торцевой поверхности прижимной крышки 22 до выступающей поверхности шаров 5. После регулировки выступа шаров 5 на рабочую поверхность кольца 28 наносится индустриальное масло И-52А (ГОСТ 20799-88), на которую устанавливаются шары 5 узла трения. Затем устанавливается груз 10, в соответствии с режимом проведения приработки, в результате чего скользящая втулка 8, опорный подшипник 6, поворотная втулка 14 с плоским кольцом 28 и узлом трения перемещаются вверх, при этом пальцы 28 муфты 4 входят в отверстия 27, выполненные в прижимной крышке 22, а узел трения самоустанавливается посредством шара 31 с шарами 5 относительно поверхности трения кольца 28. Затем включается электродвигатель 1, число оборотов которого регулируется тиристорной системой 12. Приработка ведется в соответствии с заданным режимом. После приработки двигатель 1 выключается и узел трения расстыковывается, для чего снимается груз 10, при этом узел трения с кольцом 28, поворотной втулкой 14, опорным подшипником 6 и скользящей втулкой 8 опускается вниз и пальцы 26 муфты 4 выходят из отверстий 27, выполненных в прижимной крышке 22. Таким образом, узел трения отсоединяется от привода (от муфты 4).
После этого узел трения снимается с поверхности трения кольца 28, с поверхности шаров 5 удаляется масляная пленка и узел трения помещается на рабочий стол горизонтального компаратора ИЗА-2 и производится измерение пятен износа на шарах 5 с погрешностью до 1 мкм. После чего снимается кольцо 28 с поворотной втулки 14, устанавливается новое кольцо 28 и фиксируется посредством стопорного винта 29. Замена кольца 28 связана с тем, что в процессе приработки на нем появляется износ, который может в дальнейшем повлиять на результаты испытаний. Необходимо отметить, что изготовление кольца 28 значительно проще по сравнению с опорной поверхностью чашки (как это выполнено в прототипе) и удобно для профилографирования поверхности трения. Затем на поверхность трения кольца наносится испытуемый смазочный материал, узел трения шарами 5 устанавливается на кольцо 28. После установки узла трения устанавливается груз 10 в соответствии с режимом проведения испытаний, при этом скользящая втулка 8, опорный подшипник 6, поворотная втулка 14 с плоским кольцом 28 и узлом трения перемещаются вверх, при этом пальцы 26 муфты 4 входят в отверстия 27, выполненные в прижимной крышке 22, аузел трения самоустанавливается посредством шара 31 с шарами 5 относительно поверхности трения кольца 28. Затем включается электродвигатель 1, число оборотов которого в соответствии с заданным режимом проведения испытаний регулируется посредством тиристорной системы 12. Испытания проводят в течение 15 минут. После проведения испытаний двигатель 1 выключается, узел трения расстыковывается, как это описано ранее, и снимается с поверхности трения кольца 28, промывается поверхность шаров 5, затем узел трения помещается на рабочий стол горизонтального компаратора ИЗА-2 и производится измерение пятен износа на шарах 5. В процессе испытания происходит увеличение исходного пятна износа (определенной после приработки) и уменьшение от центра шаров 5 до поверхности трения кольца 28. За конечный результат испытания принимается средняя величина вертикального износа шара 5.
Тиристорная система 12 позволяет регулировать число оборотов двигателя 1 и стабилизирует число оборотов двигателя 1 при изменении величины нагрузки, что позволяет повысить точность проведения испытаний. Кроме того, регулировка числа оборотов и нагрузки дает возможность приблизить условия испытания у реальным условиям работы узлов трения машин, то есть расширяет функциональные возможности трехшариковой машины трения скольжения. Момент трения, возникающий при изнашивании поверхности трения шаров 5 и кольца 28, передается на тензобалку 20, закрепленную вертикальной стойке 13, которая, в свою очередь, закреплена на скользящей втулке 8. Упор 16, жестко закрепленный на поворотной втулке 14 при работе узла трения, вызывает деформацию тензобалки 20 и посредством измерительной аппаратуры определяется момент трения, а коэффициент трения определяется из значения момента по известным формулам.
Предложенная конструкция трехшариковой машины трения скольжения позволяет упростить проведение испытаний, поскольку опорная поверхность в предложенной конструкции выполнена в виде кольца 28, который удобен при изготовлении, при профилографировании поверхности трения и при смене кольца. Кроме того, предложенная конструкция позволяет стабилизировать заданную скорость скольжения и повысить таким образом точность проведения испытаний. Необходимо отметить, что в прототипе нижние шары и верхний шар работают в разных трибологических условиях, то есть имеет место нестационарный режим трения, в предложенной конструкции пара трения - шары 5, кольцо 28 работает в условиях трения скольжения - граничной смазки.
Несмотря на ряд оригинальных технических решений, основным недостатком вышеприведенного устройства является функциональная ограниченность только четырехшариковой схемой испытаний. Кроме того, можно отметить излишнюю сложность устройства.
Ряд заявок на патенты содержат частные технические решения, позволяющие максимально приблизить условия испытаний к эксплуатационным режимам работы реальных узлов трения. Так, в заявке [12] испытуемые образцы размещают в рабочей среде, соответствующей реальным условиям работы материалов.
В патенте [13] описано устройство для моделирования процессов изнашивания при высоких контактных давлениях и динамических нагрузках в режиме знакопеременных скоростей, возникающих при взаимном перемещении контактирующих деталей (рис. 1.36)
Рис. 1.36. Установка для испытаний материалов на износ.
Устройство для испытания на износ содержит корпус 1 с расположенным на нем приводом возвратно-поступательного движения 2 образца 3. На корпусе 1 расположена стойка рычагов 4, к которой прикреплены узлы статического 5 и динамического нагружения 6. Узел статического нагружения 5 выполнен в виде рычага, жестко связанного с контробразцом 7, на котором закреплен груз 8. Узел динамического нагружения 6 выполнен в виде рычага, на котором закреплен груз 9, пальца 10, передающего нормальную составляющую динамической нагрузки на образец 3, кулачка привода 11, задающего закон изменения динамической нагрузки, вращающегося со скоростью w и винта 12.
В Институте прикладной механики УрО РАН разработана машина трения [14] (рис. 1.37). Машина трения содержит основание 1, держатель 2 плоского образца 3, каретку горизонтального перемещения 4, размещенную в линейных направляющих, установленных на основании 1, каретку вертикального перемещения 5 с держателем 6 образца 7, размещенную в линейных направляющих, установленных на каретке 4, уравновешивающее устройство, включающее гибкий элемент 8, ролик 9, закрепленный на оси 10 каретки 4, противовес 11; измеритель силы нагружения 12, выполненный в виде тензометрического датчика силы; нагружающее устройство, включающее стакан 13, внутри которого находится пружина 14, упирающаяся одним концом в дно стакана 13, а другим в измеритель силы нагружения 12; привод нагружения, размещенный на каретке горизонтального перемещения 4, включающий электродвигатель 15, ходовой винт 16, гайку 17, жестко связанную со стаканом 13 нагружающего устройства; привод возвратно-поступательного перемещения, установленный на основании 1, включающий электродвигатель 18, ходовой вингт 19, гайку 20, жестко связанную с кареткой горизонтального перемещения 4; управляющий компьютер 21, согласующее устройство 22, аналого-цифровой преобразователь 23, усилитель аналогового сигнала 24, блок управления 25 приводом нагружения.
Как и в предыдущих патентах, недостатком данной конструкции является функциональная ограниченность, поскольку имеется возможность реализовать только одну схему трения «палец-плоскость». Кроме того, сбор данных только с датчика нормального нагружения образца является недостаточным и сильно уменьшает информативность испытаний.
Одно из последних изобретений в области создания машин трения содержится в патенте [15]. Техническая задача данной машины - увеличение функциональных возможностей за счет обеспечения широкого диапазона нагрузок и повышения точности контроля нагрузки и компенсации естественного износа как системы нагружения, так и испытуемого образца.
Рис. 1.37. Машина трения УрО РАН.
Машина для испытания материалов на трение и износ содержит основание с приводной станцией и установленные на основании приводной узел с испытательной камерой, измерительный узел, нагружающее устройство с приводом, измерительно-вычислительный комплекс, состоящий из компьютера, согласующего устройства, блока управления приводом. Причем нагружающее устройство состоит из гидравлического демультипликатора и двух электромеханических шариковых винтов-гаек, разгруженных посредством гидроаккумулятора.
Недостаток машины помимо ее функциональной ограниченности состоит в чрезвычайной сложности и дороговизне исполнения.
Относительно простое устройство для испытания материалов на трение содержится в патенте [16].
Устройство (рис. 1.38) содержит основание 1, приводной элемент 2, держатель 3 с закрепленным на нем контробразцом 4, держатель испытуемого образца. Держатель испытуемого образца состоит из двух дисков 6 и 7. На внутренней поверхности верхнего диска выполнен цилиндрический выступ 8 с коническим наконечником 9, при этом на поверхности верхнего диска выполнены сквозные резьбовые отверстия 10. На внутренней поверхности нижнего диска 7 выполнены глухие ступенчатые отверстия 11 для цилиндрического выступа 8 с коническим наконечником 9. На поверхности нижнего диска 7 выполнены отверстия 12 для крепежных элементов 13, соединяющие диски между собой.
Рис. 1.38. Машина для испытаний на трение.
Высота цилиндрического выступа 8 превышает глубину отверстия 11, обеспечивая зазор между дисками в собранном виде 1,5-2 мм, между отверстиями 12 и крепежными элементами также имеется зазор. Наличие зазоров и выбор высоты цилиндрического выступа, превышающего глубину отверстия, обеспечивает свободное качание верхнего диска относительно нижнего диска. На внешней поверхности нижнего диска 7 выполнен паз 14 для размещения и крепления испытуемого образца 15, а над верхней плоскостью верхнего диска расположен узел прижима 16, обеспечивающего требуемое давление на держатель испытуемого образца.
Основным недостатком данной машины является малая информативность и функциональность, поскольку отсутствуют датчики, определяющие триботехнические характеристики испытываемых сопряжений (силу трения), а если бы такой датчик был установлен, то его результаты были бы искажены, поскольку к трению образца по контртелу будет дополнительно накладываться трение держателя по основанию.
Дата добавления: 2020-12-11; просмотров: 630;