A lot of machine details in their function time are repeatedly subjected to variable loads stresses in time.
For example, the carriage axle working in the bend and rotating together with the wheels suffer changing cyclically stresses although the external forces conserve their values and directions. The axle fibers are either in tension or in compression.
It is highly significant that under the action of the repeated changing loads the fracture occurs as the result of the gradual fracture development called the fatigue fracture. The term «fatigue» is obliged by its origin to the erroneous assumption of the first investigators of this nature about the fact that under the action of variable stresses the metal structure changes.
In the present it is established that the metal structure under the action of the periodical loads does not change. The fracture fatigue nature is conditioned by the peculiarity of the molecular and crystalline substance structure. Apparently, it is concluded in the heterogeneity of the material structure. The separate metal crystal has a different strength in different directions. Therefore, the plastic deformations arise in a separate crystal under certain stresses.
Under the repeated loads and unloadings the strain-hardness arises and the material brittleness increases. Finally, the material ability to the hardness is exhausted and the microcrack arises on one of the crystal sliding planes under the large number of the load reiteration. The appeared crack itself becomes the powerful concentration of stresses and becomes the place of final failure with the consideration of the increasing section weakening.
Two zones in the section where the failure takes place can be clearly differed: the zone with the smooth close-sitting surface (the zone of the gradual crack fatigue development) and the zone with the rough surface.
In Fig. 11.1 the photograph of the destroyed rail section is represented. It is visible that the smooth close-fitting surface arisin as the result of the gradual crack fatigue development around the internal crack which was left in the rail after its rolling; further there is a rough section surface where the final failure of the rail took place due to the large reduction of its section.
Fig. 11.1.
The defect of the internal material structure (the internal cracks, the slag inclusions and the like) and the defect of the detail surface treatment (scratches, traces from the chisel or the grinding stone and so on).
The process of the gradual material damage accumulations under the actions of the variable stresses leading to the property change, the crack formation, its development and failure is called the fatigue and the failure on account of the fatigue crack diffusion is called the fatigue failure.
The material property to resist to the fatigue is called the fatigue strength.
The researches show that the breakdown of the machine parts in the majority cases occurs because of the fatigue crack.
In a general case loads and the stresses can change in time under very complicated laws. The variable stresses can have the stationary and non-stationary modes.
Under the non-stationary mode the change law of stresses in time can be any.
Under the stationary mode the change stresses in time have a repeated (periodical) character. In a certain interval of time (period) the precise repetition of stresses takes place.
The total combination of the consequent stress values for one period of its change, under regular loading is called the stress cycle.
The curves of changing in time of normal and shear stresses in the motor bent axie at one revolution are presented in Fig. 11.2 a, b. As we see the stresses change by a very complicated law but they have a periodical (cyclic) character.
The influence of the stress change curve shape on the fatigue strength is studied insufficiently but this influence is small and the value of the maximum and minimum cycle stresses and their relation play a decisive role. Therefore in future we will suppose that the stress change in time arises accordingly to the law near to the sinusoid (Fig. 11.3 a).
The cycle of variable stresses is characterized:
1) by the maximum algebraic stress value of the cycle
2) by the minimum algebraic stress value of the cycle
3) by the average stress of the cycle
a) |
b) |
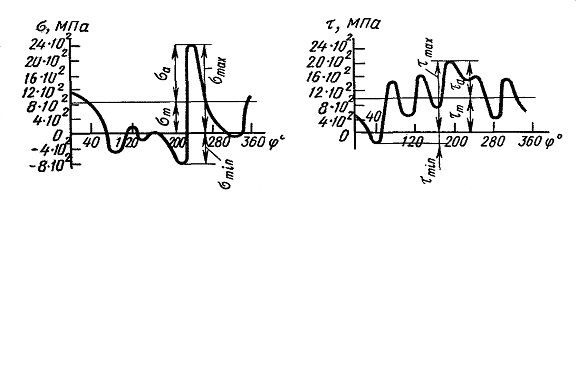
Fig. 11.2.
(11.1)
The average stress of the cycle is the constant cycle component in time (positive or negative);
4) by the cycle stress amplitude
(11.2)
the cycle stress amplitude is the maximum (positive) value of the stress cycle component;
5) by the coefficient of the cycle asymmetry of the stresses
(11.3)
The cycles having the same value R are called similar.
а) b) c) d) |
Fig. 11.3.
From the formulas (11.1), (11.2) and Fig. 11.3 we see that
(11.4)
(11.5)
In the case if we have the symmetrical stress cycle (Fig. 11.3 b). Under that
The stress cycle represented in Fig. 11.3 c is called pulsating.
For this case we have
The constant statically stress (Fig. 11.3 d) we can consider as a special case of a variable one with the characters
Any symmetrical stress cycle can be represented by the sum of the symmetrical cycle with the maximum stress which is equal to the amplitude of the given cycle and the constant stress which is equal to the middle stress of the given cycle (Fig. 11.3 a). All given terms and relations after the replacement into
remain in force for the case of the variable shearing stress.
11.2. Fatigue (Wohler’s) curve under the symmetrical cycle. Fatigue strength
For the design analysis under the action of the repeated variable stresses, it is necessary to know the mechanical material characteristics. They are determined by the test way with the specimen fatigue on a special machine.
The specimen test under the symmetrical stress cycle is the most simple and widespread one. The principle machine scheme for the specimen test in bending is shown in Fig. 11.4.
The specimen 1 is fixed in chuck 2 of the machine spindle rotating with some angular velocity. Pillow 3 through which the force F passes the constant direction is placed at the specimen end. It is easy to see that under it the specimen is subjected to the bending action with the symmetrical cycle. Indeed, the tension stress acts at the most dangerous point A of the section I-I because the cantilever bends the concave downward. However, after that as the specimen rotates on half revolution, the point A will be down in the compressive zone and the stress will be equal to
The point A will be up again after the next half revolution of the specimen and so on. Under the passage through the neutral axis the stress at the point A will be equal to zero.
The test is taken in the following sequence. Take 10 similar specimen usually of the diameter 6-10 mm with a polished surface. The first specimen is loaded up to the considerable stress in order to destroy it under the comparatively small revolution number N1 (the cycle).
Besides the maximum cycle stress for the maximum stress point of the section is kept in mind. In bending, it is known, the maximum stress arises at the extreme section points and it is determined by the formula
Fig. 11.4. Fig. 11.5.
The test results are put on the diagram which is drawn in coordinates (Fig. 11.5).
The point A appears on the diagram with the coordinates N1 and after the test of the first specimen.
Then the second specimen is tested under a smaller stress Naturally it is destroyed under the larger cycle number N2. On the diagram the point B is put with the coordinates N2 and
and so on.
Having tested all specimens and having united the points A, B, C and so on by smooth lines, we get a curve ABCD which is called the fatigue (Wohler’s) curve.
This curve is typical as it goes practically horizontally (the region CD) starting from some stress. It means that under some stress the specimen can bear an infinitely large cycle number N2 not being destroyed. The experience of the steel specimen test under the normal temperature shows that if the specimen has not been destroyed up to the cycle
(it is approximately 54 h under 3000 r.p.m.) the specimen is not destroyed and under more protracted test.
A preliminary given maximum duration of the test in the fatigue is called the test base.
For steel specimens in usual conditions the test base is equal to 106 cycles.
The maximum cycle stress in the absolute value under which the fatigue rupture doesn’t occur up to the test base is called the fatigue strength For symmetrical cycles R=-1 in this case the fatigue strength is denoted by
The limited fatigue strength term is introduced for details of the limited function period as the maximum (by absolute value) cycle stress corresponding to the given cycle number is less than the base number.
Analogically the tests are carried out on other machines, the limits of the fatigue under the axial forces action in torsion
and under the combined deformations are found.
At the present for many materials the fatigue strength is found and represented in the reference book. It can be seen from these data that for the majority metals the fatigue strength of the symmetrical cycle is less than the yield point.
Дата добавления: 2020-10-25; просмотров: 443;