Технология сборки машин
Сборочные работы, в зависимости от типа производства, составляют от 20 до 40% общей трудоемкости изготовления машины. Эти работы обычно требуют значительных затрат физического труда слесарей сборщиков. Если в условиях массового производства, например, автомобилей, широко применяются средства автоматизации и механизации сборочных процессов, то в индивидуальном и мелкосерийном производстве, особенно при создании уникальной техники, экспериментальных экземпляров новых машин, проблемы автоматизации сборочных работ практически не решены.
В зависимости от типа производства и вида изделия сборка может быть организована различным способом.
При массовом производстве наиболее эффективной является подвижная поточная сборка, при которой изделие перемещается по специализированным рабочим местам, где выполняются простейшие сборочные операции. Такие места могут быть оснащены специальными средствами механизации или быть полностью автоматизированы. (При такой форме организации сборки выпускают изделия бытовой техники, компьютеры, боеприпасы…). Такую форму организации сборки предложил Генри Форд, решая задачу массового выпуска автомобилей. При сборке автомобиля количество сборочных операций довольно велико, поэтому длина такого конвейера составляет сотни метров, а с учетом конвейеров сборки отдельных узлов автомобиля – многие километры. Конечно, внутри производственных зданий такие конвейеры располагается во много рядов и на нескольких уровнях по высоте. В то же время продолжительность элементарных сборочных операций при сборке автомобиля составляет не более нескольких минут, что позволяет обеспечить малый такт выпуска изделия (обычно с конвейера, менее чем через минуту, сходит собранный автомобиль).
При производстве крупногабаритных изделий (электрогенераторов, турбин, самолетов, судов, станков…) применяют поточную стационарную сборку. В этом случае изделия, находящиеся в различных стадиях сборки, располагаются неподвижно, на специальных стапелях, а специализированные рабочие места (бригады рабочих с соответствующим оборудованием) перемещаются от изделия к изделию, производя соответствующие сборочные операции.
В условиях единичного и мелкосерийного производства такие виды сборки экономически не оправданы и сборка обычно выполняется бригадами высококвалифицированных специалистов, производящих все действия по сборке, регулировке и требуемым испытаниям. При этом трудоемкость сборки и продолжительность существенно выше. Так постройка подводной лодки по индивидуальному проекту может занимать до нескольких лет. Во время же второй мировой войны поточная сборка подводных лодок позволяла Германии выпускать одну подводную лодку в день, в США же производилось в день до нескольких судов водоизмещением 10000т.
Сборка заключается в соединении сопрягаемых сборочных единиц и деталей путем приведения в соприкосновение основных баз – сопрягаемых поверхностей. Такие поверхности определяют положение деталей относительно друг друга, выполняются с наибольшей точностью и определяют во многом качество машины. Так суппорт токарного станка устанавливается на направляющих поверхностях станины и может перемещаться по ним в одном направлении. От точности этих поверхностей станины будет зависеть точность (прямолинейность) перемещения суппорта – одна из важнейших характеристик качества станка.
В процессе сборки детали соединяется неподвижно или подвижно относительно друг друга. Такие соединения могут быть разъемными, когда соединение можно разобрать, например, для замены детали, узла (соединения по подвижным и переходным посадкам, резьбовые) и неразъемными, когда разборка невозможна без разрушения какого-либо элемента (заклепочные, сварные, клеевые…).
В процессе сборки требуется производить ряд специфических операций, которые требуют затрат энергии и имеют определенную временную продолжительность, уменьшение которой, также как и при обработке деталей, наталкивается на физические ограничение.
Конечно, время завертывания винта можно уменьшить, повысив скорость вращения специального инструмента, но возникающие динамические нагрузки, при определенной скорости, приведут к разрушению либо винта, либо резьбы. Автомобилистам известно, что время завинчивания винта для крепления колеса вручную доходит до 1 минуты, с применением же специального механизированного инструмента на автомобильном заводе время завинчивания всех четырех винтов не превышает 1 секунды, т.е. уменьшено до предела.
Время же реализации таких соединений как сварное, клеевое определяются особенностями протекания теплофизических, металлургических, химических процессов.
Сложность современных машин (количество деталей самолета, судна может достигать нескольких миллионов) определяла бы очень большую продолжительность процесса последовательной сборки «деталь за деталью».
Поэтому сборку ведут параллельно во времени, собирая узлы изделия, группы деталей, которые монтируют на базовую деталь (или узел). Так собранная турбина устанавливается в корпус корабля, причем одновременно в корпус могут монтироваться и управляющая аппаратура, вооружение (пушки, ракетные установки и т.д.). В корпус самолета (планер) устанавливается собранный двигатель, который обычно и производится даже на другом предприятии.
Узел машины это сборочная единица, которая имеет самостоятельные функции, которые могут быть испытаны вне машины. Например, топливный насос, масляный фильтр и т.д. В соответствии с этим узлы могут быть унифицированы, производиться самостоятельно и применяться в различных машинах. Сборочные единицы, называемые группами, обычно самостоятельных функций не имеют и выделяются из общей сборки по принципу удобства соединения деталей в группу в отдельном процессе, с целью сокращения общего времени сборки машины.
Для построения технологического процесса сборки технологами производится анализ конструкции машины для выявления составляющих ее узлов, деталей, возможности вычленения групп деталей, сборка которых возможна отдельно. Конечно, при проектировании машины конструктор должен уделять внимание технологичности машины, возможности сборки ее в параллельных во времени процессах. Если машина спроектирована неправильно, то никакие усилия технолога по оптимизации технологии ее изготовления не приведут к положительным результатам.
Поэтому конструктор при проектировании машины должен руководствоваться определенными стандартными правилами.
Так требования к составу сборочной единицы предполагают:
- расчленение ее на рациональное число частей с учетом принципа агрегатирования;
- виды используемых соединений деталей и узлов должны позволять автоматизацию или механизацию сборочных работ;
- сборка изделия не должна предполагать применения сложного технологического оснащения;
- конструкция сборочной единицы должна предусматривать базовую составную часть, которая является основой для расположения других составных частей; , и т.д.
Среди многих требований, обеспечивающих технологичность машины, наибольшее значение имеет требование взаимозаменяемости всех ее узлов и деталей. Принцип взаимозаменяемости, закладываемый при проектировании искусственных объектов, не используется природой. Как известно, каждый природный организм уникален и приходится предпринимать специальные усилия в случае замены отдельных частей живых организмов. На первом этапе развития машинного производства, вплоть до начала 20-го века, многие машины создавались в процессе пригонки отдельных деталей друг к другу.
Например, размеры шеек вала задавались в виде номинальных, без регламентации допуска на изготовление, а размер подшипниковой втулки задавался с требованием выполнить его по полученной шейке вала с определенным зазором. В этих условиях изготовить подшипниковую втулку можно было только после изготовления вала. Это увеличивало цикл изготовления машины и не позволяло производить ее ремонт с использованием запасных частей. Хотя принцип взаимозаменяемости был известен со средних веков, и даже был внедрен в России при производстве огнестрельного оружия еще по указу Петра 1, появление первых стандартов и его широкое применение относится именно к началу 20-го века.
Несмотря на кажущуюся эффективность взаимозаменяемости, применение этого принципа имеет ряд ограничений, так как в ряде случаев значительно удорожает изготовление машины. Это связано с тем, что качество функционирования отдельных узлов и машины в целом зависит от отклонений замыкающих звеньев, которые определяются допускаемыми отклонениями всех входящих в размерную цепь звеньев (рис.2.1).
|
|
|




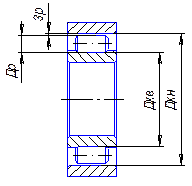
Рис.2.1
Так в роликовом подшипнике качения должен быть зазор Зр между роликами 1 и кольцами 2 и 3, что обеспечивает свободу движения подшипника. В то же время большая величина этого зазора резко снижает качество подшипника, так как приводит к «болтанке» установленного в нем вала, значительным динамическим нагрузкам (ударам), нарушает точность кинематических связей деталей, установленных на валу с другими деталями машины. Но этот зазор возникает в процессе сборки подшипника и зависит от точности изготовления его деталей, причем максимальная и минимальная, возможная величина этого зазора равны:
Зр макс = (Дкн макс – Дкв мин – Др мин)/2
Зр мин = (Дкн мин - Дкв макс – Др макс)/2
Для повышения качества подшипников колебания зазора стремятся свести к минимуму, но это требует чрезвычайно точного выполнения всех его деталей, что привело бы к значительному (на порядки) его удорожанию. Поэтому, даже в этом простейшем случае, от принципа полной взаимозаменяемости приходится отказываться и применять так называемую селективную (с использованием отбора) сборку. В этом случае допуски на изготовление отдельных деталей можно расширить, но потом, перед сборкой детали сортируют на отдельные группы, подбирая в этих группах истинные размеры так, чтобы при сборке получить минимальные колебания зазоров в подшипниках. Естественно, что часть (по теории вероятности очень малая) деталей не найдет себе применения, но эти потери с лихвой окупятся за счет снижения точности обработки отдельных элементов.
В реальных машинах размерные цепи могут состоять из десятков взаимосвязанных размеров и полная взаимозаменяемость, часто не только экономически не оправдана, а даже невозможна. Поэтому, на практике, при сборке машин применяют не только метод подбора, но и метод пригонки, когда отдельные элементы обрабатывают «по месту» с учетом требуемых размеров замыкающего звена.
Методы достижения точности замыкающих звеньев размерных и кинематических цепей при сборке машин в соответствии со стандартами подразделяются:
- метод полной взаимозаменяемости, основанный на расчете размеров замыкающего звена по максимальным и минимальным допустимым размерам составляющих размерную цепь звеньев (метод максимум -минимум). Этот метод обеспечивает полную взаимозаменяемость, но требует довольно точного выполнения размеров составляющих звеньев (деталей) и применим в массовом и крупносерийном производстве, когда число размеров, входящих в размерную цепь невелико.
- При методе неполной взаимозаменяемости допуски на размеры составляющих звеньев расширяют (чтобы удешевить производство деталей), По теории вероятностей отклонения размеров составляющих звеньев (реальных деталей) на практике при сборке могут компенсировать друг друга (детали с отклонениями в большую сторону с деталями имеющими отклонения в меньшую сторону. Кроме того, размеры с отклонениями близкими к центру поля допуска встречаются значительно чаще, чем с крайними предельными отклонениями. Такой принцип обеспечения взаимозаменяемости рационально применять в серийном и массовом производстве, при сложных многозвенных размерных цепях.
- Метод групповой взаимозаменяемости применяют при создании соединений высокой точности, когда полная взаимозаменяемость либо недостижима, либо связана с чрезвычайно большими затратами. В этом случае детали изготавливают по расширенным допускам, а потом сортируют на группы (например, при производстве подшипников качения). Такая сборка целесообразна в массовом и крупносерийном производстве.
- Сборка методом пригонкитрудоемка и применяется в единичном и мелкосерийном производстве. Метод регулирования снижает трудоемкость пригонки и требует применения в конструкции специальных регулирующих устройств, которые могут несколько усложнять конструкцию машины.
Машина, состоящая из множества деталей, которые группируются в узлы, подузлы, группы деталей может быть собрана множеством способов, вплоть до последовательной сборки «деталь за деталью».
Выбор же оптимального технологического процесса является сложной задачей, для решения которой приходится применять многие математические методы (линейное и нелинейное программирование, теорию массового обслуживания и т.д.). Причем оптимизация технологии сборки требует построения целевой функции, в качестве которой может использоваться минимальная себестоимость изделия, время производства изделия или различные комбинации этих функций.
При построении технологического процесса сборки машины используется ряд практических правил, суммирующих накопленный производственный опыт. Общая сборка машины начинается с установки базирующей детали или базирующей сборочной единицы машины, роль которой обычно выполняет корпусная деталь. Это может быть рама, станина, корпус, основание и т.д.
Базирующую деталь устанавливают или закрепляют в удобном для сборки положении. Иногда эту деталь закрепляют в специальном приспособлении, которое либо увеличивает жесткость детали, либо позволяет ее поворачивать или перемещать требуемым при сборке способом.
При поточной подвижной сборке это приспособление, зачастую, перемещается вместе с изделием до завершения процесса сборки. Иногда же оно позволяет закреплять изделие до окончания процесса сборки и перемещать собранное изделие в рабочую среду (судостроительный стапель).
При сборке отдельных узлов также выявляется базовая деталь, которую принимают за основу при сборке узла.
При разработке процесса сборки необходимо учитывать доступность места сборки, поэтому, в первую очередь, устанавливают узлы и детали, минимально затрудняющие установку последующих узлов и деталей. При этом необходимо учитывать возможность размещения монтажного инструмента.
Следует подчеркнуть, что, несмотря на широкие возможности комбинаторики в выборе технологического процесса сборки машины, возможности качественной, производительной сборки закладываются на стадии проектирования конструктором.
Разработанную последовательность сборки машины изображают в виде графической схемы сборки (рис.2.2). На схему общей сборки наносятся условные обозначения деталей и сборочных единиц, поступающих на общую сборку. Схема наглядно показывает, в какой последовательности на базовую деталь устанавливаются узлы и детали. Нарушение последовательности, предусмотренной этой схемой недопустимо.
Рис.2.2
Кажется очевидным, что разборку машины можно произвести в обратном порядке, однако в процессе сборки могут применяться неразъемные соединения. Целью же разборки может быть дефектация машины после испытаний, упаковка для отправки заказчику, в тех случаях, когда разобранная машина более транспортабельна, ремонт. Поэтому для разборки машины составляются специальные схемы, соответствующие целям разборки.
Такое схематическое представление технологического процесса сборки отличается наглядностью и, зная продолжительность и стоимость выполнения отдельных операций сборки, можно легко оценить время сборки машины и стоимость процесса.
При определении времени выполнения отдельных операций сборки, производимых с применением ручного труда, используются статистические экспериментальные оценки. При этом, конечно, определение норм времени должно производиться с учетом средних возможностей слесарей сборщиков.
Трудоемкость процессов сборки обуславливает разработку средств ее механизации и автоматизации. В настоящее время, особенно в условиях массового и крупносерийного производства широко применяются промышленные роботы, позволяющие в ряде случаев полностью освободить человека от выполнения сборочных операций. Возможности промышленных роботов, хотя и совершенствуются с каждым годом, но до настоящего времени значительно уступают возможностям человека. Поэтому изделия для автоматической сборки, зачастую, проектируют, учитывая достигнутые возможности автоматизации сборочных процессов. Так, многие резьбовые соединения оказалось целесообразным переводить на сварные, клеевые, заклепочные, которые значительно проще выполняются автоматами. В то же время ремонтопригодность таких изделий значительно снижается.
Многие знают, что в настоящее время при ремонте бытовой техники, оказывается рациональным заменять целые агрегаты, ремонт которых либо невозможен, либо экономически неоправдан.
Высокий уровень автоматизации сборочных операций достигнут в настоящее время только в условиях массового и крупносерийного производства, хотя требования рынка определяют необходимость выпуска изделий максимально удовлетворяющих индивидуальным требованиям потребителя. Так известно, что обладание людьми одинаковыми вещами, вызывает чувство некоторого дискомфорта. Производство же отличающихся друг от друга вещей в условиях поточного производства существенно усложняет технологические задачи. Первые попытки, решить эту проблему, предприняты на заводах, производящих автомобили Мерседес. В настоящее время их собирают в условиях максимально автоматизированной поточной сборки, по индивидуальным заказам, когда входящие в сборку узлы могут варьироваться, исходя из требований заказчика. Так, определенный кузов может оснащаться теми или иными сидениями, радиоэлектронным оборудованием и т.д. Это требует решения сложнейших задач логистики, которое стало возможным при применении современных средств вычислительной техники.
Вопросы для самопроверки:
1. Какие изделия собирают в условиях поточной подвижной сборки?
2. В каком типе производства сборка осуществляется в основном с применением ручного труда?
3. Какие виды соединений деталей машин применяют при сборке?
4. Чем отличаются сборочные единицы – узлы машины от сборочных единиц – групп?
5. В чем состоит принцип агрегатирования при проектировании машины?
6. В каком типе производства и при каких прочих условиях рационально применять принцип полной взаимозаменяемости?
7. Какие машины рационально собирать, используя метод пригонки отдельных ее частей?
8. Могут ли отличаться технологические методы, используемые при сборке машины от методов, используемых при ее разборке?
9. С какой целью машины разбирают?
10. Какие основные средства автоматизации сборочных работ используются в настоящее время?
Образец карты тестового контроля:
1. В каких условиях собирают бытовые холодильники:
а). В условиях подвижной поточной сборки;
б). В условиях стационарной поточной сборки;
в). В условиях стационарной сборки на стапеле;
2. Чем является карбюратор при сборке автомобиля:
а). узлом;
б). подузлом;
в). группой;
3. Какой из видов соединения при сборке является разъемным?
а). болтовое;
б). заклепочное;
в). клеевое;
4. Какие виды машин рационально собирать в условиях поточной стационарной сборки:
а). корабли;
б). самолеты;
в). фотоаппараты;
5. При производстве каких изделий используется принцип групповой взаимозаменяемости:
а). подшипников качения;
б). авторучек;
в). уникальных телескопов;
Дата добавления: 2020-10-14; просмотров: 570;