Резервуарная группа
По отечественным и зарубежным нормам в системах ГЗТ должно быть не менее 3-х резервуаров с внутренним антикоррозионным покрытием, оснащенных общим промышленным оборудованием, а также плавающим топливозаборным оборудованием.
В настоящее время в системах ГЗТ находят применение следующие типы резервуаров:
Вертикальные наземные сварные с избыточным давлением 0,002 МПа и вакуумом до 0,0025 МПа вместимостью от 100 до 1000 м3;
Горизонтальные наземные и подземные сварные, рассчитанные на избыточное давление до 0,04 МПа вместимостью от 3 до 100 м3;
Вместимость каждого из резервуаров, как правило, должна соответствовать суточной потребности в заправке топливом ВС в пиковые периоды использования ГЗТ [20]. В соответствие с отечественной и зарубежной практикой рекомендуется применение одинаковых по вместимости и конструкции резервуаров, оборудование которых должно обеспечивать прием, отстаивание и выдачу топлива [19-20].
В системах ЦЗС высокой и средней производительностиобычно используются вертикальные цилиндрические резервуары (рис. 17-18), а в упрощенных системах с суточным расходом не более 100 м3 – горизонтальные резервуары (рис. 18). Основные характеристики вертикальных резервуаров рулонной сборки со щитовой кровлей приведены в таблице 11.
Таблица 11 - Основные технические характеристики вертикальных цилиндрических резервуаров
Показатель | Условный объем резервуара, м3 | |||||||
Вместимость резервуара, м3 | ||||||||
Диаметр, мм | ||||||||
Высота, мм | ||||||||
Общая масса металла, т | 7,334 | 11,311 | 12,655 | 18,199 | 24,212 | 41,301 | 63,238 | 90,422 |
Вертикальные резервуары устанавливаются только наземно на специальном песчаном основании.
|
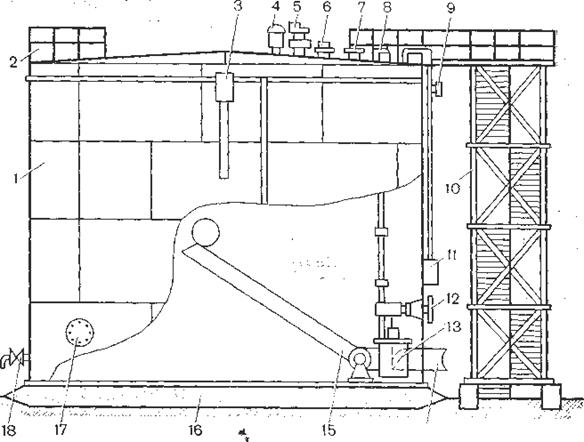
Рисунок 17 - Вертикальный резервуар и его оборудование:
1 — корпус; 2 — ограждение; 3 — пеногенератор; 4 — предохранительный (гидравлический) клапан; 5 — дыхательный клапан механический; 6 — замерный люк; 7 — световой люк; 8 — сниженный пробоотборник; 9 — сигнализатор предельного уровня; 10 — лестница; 11 — указатель уровня; 12 — управление хлопушкой; 13 — хлопушка; 14 — приемо-раздаточный патрубок; 15 — плавающее топливозаборное устройство; 16 — песчаное основание; 17 — люк-лаз; 18 — сифонный кран
Наиболее перспективными являются вертикальные резервуары (рис. 18) с конусными днищами и гладкими внутренними поверхностями. Это обеспечивает надежный и удобный сбор и последующее удаление из резервуара продуктов отстоя, а также удобное нанесение на стенки антикоррозионных покрытий. Типовые проекты предусматривают строительство таких резервуаров емкостью 400, 700, 1000, 2000, 3000 и 5000 м3 с внутренними антикоррозионными покрытиями.
Рисунок 18 - Вертикальный резервуар с коническим днищем и дополнительным оборудованием:
1 - приемо-раздаточный патрубок; 2 - днище коническое; 3 - плавающее топливозаборное устройство; 4 - сливная труба; 5 - вентиль; 6 - присоединительное устройство; 7 - плавающий понтон; 8 - огневой предохранитель; 9 - воздушный фильтр; 10 - механический дыхательный клапан
Горизонтальные резервуары устанавливают наземно, полуподземно и подземно. Предпочтение отдается наземной установке, так как создаются благоприятные условия для работы насосных станций (обеспечивается подпор) и отпадает необходимость в применении самовсасывающих насосов. Кроме того, при наземной установке значительно улучшаются условия эксплуатации и обслуживания резервуаров при проведении регламентных работ. При наземной установке резервуары размещаются на фундаментах, а при подземной и полуподземной - на песчаном основании.
Если в местах установки резервуаров имеются грунтовые воды, то при подземной установке размещаются на бетонных фундаментах, к которым они крепятся специальными бандажами. Основные технические данные горизонтальных резервуаров приведены в таблице 12.
Таблица 12 - Основные технические характеристики горизонтальных цилиндрических резервуаров
Показатель | Условный объем резервуара, м3 | |||||
Вместимость резервуара, м3 | 10,5 - 11,5 (–) | 25,4-28,5 (26,5-28,5) | 50,2-54,4 (51,7-54,6) | 73,4-83,4 (74,6-84,8) | 97,5-100,6 (98,9-101,4) | |
Наружный диаметр, мм | 220 (–) | 2862-2870 (2862-2870) | 2862-2870 (2862-2870) | 3238-3250 (3238-3250) | 3238-3250) (3238-3250) | |
Наружная длина, мм | 2823 - 3073 (–) | 4035-4274 (4645-4924) | 7885-8383 (8545-9130) | 8958-10126 (9590-10758) | 11888-12132 (12520-12764) | |
Общая масса металла, кг | 1013 - 1049 (–) | 1772-1898 (1831-1894) | 3148-3339 (3200-3343) | 4181-4499 (4250-4583) | 5305-5375 (5311-5405) | |
Примечание. В скобках указаны размеры резервуаров с коническими днищами. | ||||||
Для заполнения и опорожнения резервуаров, а также для надежного хранения топлива и правильной эксплуатации резервуаров на них устанавливают специальное оборудование, изготовляемое по соответствующим ГОСТ. Это оборудование включает: световой люк, люк-лаз, дыхательные и предохранительные клапаны, замерный люк, сифонные краны, хлопушки с устройствами для их управления, указатели уровня, огневые предохранители и другое оборудование. Выбор оборудования резервуаров производится в зависимости от их конструкции, пропускной способности приемораздаточных устройств и подачи насосных станций.
Для расходных резервуаров систем ЦЗС этого оборудования недостаточно, так как к ним предъявляются более жесткие требования к обеспечению выдачи топлива из верхних, наиболее отстоявшихся слоев; надежной защите топлива от попадания в него пыли и влаги из атмосферы, а также продуктов коррозии, которые могут образовываться на внутренних стенках резервуаров. Для выполнения этих требований на расходных резервуарах необходимо устанавливать дополнительное специальное оборудование, а внутренние их поверхности покрывать антикоррозионными материалами.
В качестве дополнительного оборудования используются: плавающие топливозаборные устройства для верхнего забора топлива, воздушные фильтры, устройства для удаления отстоя, а также плавающие крыши и понтоны (см. рис. 19).
Рисунок 19 - Типовая: схема размещения технологического оборудования на наземном горизонтальном цилиндрическом резервуар:
1 - дыхательный клапан (на группу резервуаров); 2 - воздухопровод; 3 - уровнемер; 4 - мостик; 5 - болт крепления тросом управления заборной трубой; 5 - патрубок; 7 - аварийный клапан (дыхательный); 8 - трос управления заборной трубой; 9 - люк-лаз (500 мм); 10 - поплавок заборной трубы; 11 - заборная труба; 12 - всасывающая магистраль; 13 - 25 мм клапан слива отстоя; 14 -опора; 15 - стальная накладка; 16 - приемный трубопровод
В международных требованиях [26] не предусматривается применение для ГЗТ резервуаров с плавающими крышами и понтонами. Авиатопливо должно храниться в горизонтальных и вертикальных резервуарах с неподвижной крышей. Новые резервуары должны быть сконструированы таким образом, чтобы не допустить попадание в них воды и грязи, также должен быть обеспечен легкий слив отстоя из резервуаров. Для горизонтальных резервуаров должен быть предусмотрен минимальный угол наклона в отношении 1:50 в сторону устройства слива отстоя, а вертикальные резервуары должны иметь конусообразное днище с наклоном 1:30 к центру отстойника.
Для внутренних поверхностей резервуаров в качестве антикоррозионных покрытий применяются: металлизация, эмалирование, лакокрасочные материалы, стеклопласт на основе полиэфирных и эпоксидных смол.
Резервуары, имеющие антикоррозионные покрытия из диэлектрических материалов, оборудуются устройствами для отвода статического электричества с поверхности топлива. Ниже рассматривается основное стандартное и дополнительное оборудование резервуаров.
Приемо-раздаточный патрубок 1 (рис. 20) предназначен для заполнения резервуара или выдачи из него топлива. Он вваривается в нижний пояс корпуса 3 резервуара. Диаметр патрубка выбирается с учетом расхода, с которым заполняется резервуар. Зависимость диаметра патрубка от расхода представлена в таблице 13.
Таблица 13 – Основные характеристики оборудования резервуаров
Оборудование | Марка | Размеры, мм | Пропускная способность, м3/ч | |
Условный диаметр | Диаметр фланца | |||
Приемо-раздаточные патрубки | ППР-80 | До 50 | ||
ППР-100 | 50—100 | |||
ППР-150 | 100-200 | |||
ППР-200 | 200 - 300 | |||
ППР-300 | 600 - 1200 | |||
Плавающие | ПУВ-100 | 70 - 120 | ||
топливозаборные устройства | ПУВ-150 | 150 - 200 | ||
ПУВ-250 | 300 - 500 | |||
Хлопушки | Х-80 | – | ||
Х-100 | – | |||
Х-150 | – | |||
Х-200 | – | |||
Х-250 | – | |||
Х-300 | – | |||
Механические дыхательные | КД-50 | До 25 | ||
клапаны | КД-100 | 60-72 | ||
КД-150 | 118 - 142 | |||
КД-200 | 206 - 240 | |||
КД-250 | 244 - 304 | |||
Гидравлические | КПСА-100 | |||
предохранительные клапаны | КПСА-150 | |||
КПСА-200 | ||||
КПСА-250 | ||||
КПСА-350 | ||||
Огневые предохранители | ОПЛ-50 | – | ||
ОПЛ-80 | – | |||
ОПЛ-100 | – | |||
ОПЛ-150 | – | |||
ОПЛ-200 | – | |||
ОПЛ-250 | – |
Количество приемо-раздаточных патрубков может быть различным и зависит от расчетного расхода или обусловливается технологическими требованиями.
Рисунок 20 – Приемно-раздаточное оборудование резервуаров
В расходных резервуарах систем ЦЗС на раздаточном патрубке должно быть установлено плавающее топливозаборное устройство 10. Это требование для вертикальных резервуаров является обязательным. Плавающее топливозаборное устройство ПУВ (рис. 21) предназначено для выдачи из резервуара наиболее чистого, отстоявшегося топлива из верхнего слоя. Оно представляет собой подъемную трубу 5, один конец которой соединен шарниром 6 с приемо-раздаточным патрубком 1 и хлопушкой 2, а другой оборудован поплавком 4, удерживающим трубу в верхнем слое топлива. Плавающие топливозаборные устройства изготовляются с диаметром условного прохода 100, 150 и 250 мм, с пропускной способностью соответственно 70 - 120, 150 - 200 и 300 - 500 м3/ч.
Рисунок 21 – Плавающее топливозаборное устройство
Хлопушка (см. рис. 20) предназначена для предотвращения утечки топлива из резервуара в случае неисправности задвижки на трубопроводе. Она устанавливается на приемо-раздаточном патрубке внутри резервуара. Хлопушка перекрывает проходное сечение патрубка под действием собственной силы тяжести и давления столба топлива. Диаметр хлопушки определяется диаметром приемо-раздаточного патрубка. В таблице 13 приведены марки хлопушек и размеры их диаметра. При выдаче топлива из резервуара хлопушка открывается при помощи механизма бокового управления.
Рисунок 22 - Приемо-раздаточное оборудование резервуаров
Механизм бокового управления хлопушкой (см. рис. 22) имеет вал 7, на наружном конце которого закреплен штурвал 4, а на внутреннем - барабан 8, соединенный тросом с хлопушкой 12. В месте прохода вала 7 через стенку резервуара установлено сальниковое устройство 6. При вращении штурвала 4 вращается барабан 8, на который наматывается прикрепленный к нему трос 11, и открывает хлопушку 12. Для удержания хлопушки в открытом положении имеется стопор 5, фиксирующий штурвал. В случае обрыва троса 11 пользуются аварийным тросом, один конец которого прикреплен к хлопушке, а другой выведен и закреплен у светового люка.
Перепускное устройство (см. рис. 22) предназначено для облегчения открытия хлопушки за счет выравнивания давления топлива по обе стороны хлопушки. Перепускное устройство устанавливают на резервуарах высотой более 5 м. При меньшей высоте устанавливать его нецелесообразно, так как давление столба жидкости будет небольшим. Перепускное устройство состоит из трубки 2 диаметром 25 мм и вентиля. Один конец трубки вварен в приемо-раздаточный патрубок, а другой - в стенку резервуара. Перепускное устройство выпускают одного типа независимо от диаметра приемо-раздаточного патрубка.
Световой люк предназначается для доступа обслуживающего персонала, проветривания и освещения резервуара при ремонтных и зачистных работах. Кроме того, он используется при подъеме хлопушек при повреждении троса управления. Световой люк устанавливают на кровле резервуара над приемо-раздаточным патрубком с хлопушкой. В резервуарах емкостью свыше 2000 м3 делают два световых люка. Для резервуаров других объемов количество световых люков принимают по числу приемо-раздаточных патрубков. Диаметр люка в свету 500 мм.
Люк-лаз предназначен для доступа обслуживающего персонала в резервуар при его осмотре, зачистке и ремонте. Он также служит для вентиляции резервуара. Люк-лаз расположен диаметрально противоположно световому люку. Узлы люк-лаза в отличие от светового усилены, так как он расположен в нижнем поясе корпуса резервуара, где имеется значительное гидростатическое давление. Резервуары емкостью свыше 2000 м3 имеют два люка-лаза. Диаметр люка-лаза ПЛ-500 в свету 500 мм. Световые люки и люки-лазы должны быть прочными и герметичными, обычно их делают сварными, а для уплотнения применяют специальные прокладки.
Замерный люк (рис. 23) предназначен для замера уровня топлива в резервуаре рулеткой, а также для взятия проб пробоотборниками. Он устанавливается на кровле резервуара и крепится к его замерному патрубку фланцем 7. Замерный люк состоит из корпуса 5, кулисы 4, крышки 3, маховика 2, прокладки 1 и педали 6. Крышка 3, подвешенная к кулисе 4, прижата к корпусу маховичком 2. Отведя в сторону маховичок и нажав ногой на педаль 6, открывают отверстие люка. Замерные люки выпускаются с диаметром условного прохода 100 мм для горизонтальных резервуаров и 150 мм - для вертикальных резервуаров.
Рисунок 23 – Замерный люк
Механический дыхательный клапан (рис. 24) предназначен для поддержания внутри резервуара установленной величины избыточного давления или разрежения, которые образуются при заполнении резервуара и выдаче из него топлива, а также при изменении объема газов в паровом пространстве резервуара вследствие колебания температуры. Величина избыточного давления и вакуума зависит от прочности крыши и не должна превышать допустимых пределов. На рис. 24 изображен наиболее распространенный дыхательный клапан, допускающий повышение давления в паровоздушном пространстве резервуара не более чем на 190 мм вод. ст. и разрежения не более 25 мм вод. ст. Необходимо также учитывать, что пропускная способность дыхательного клапана при прохождении через него паровоздушной смеси должна соответствовать пропускной способности приемо-раздаточного патрубка. Если пропускная способность дыхательного клапана будет меньше пропускной способности приемо-раздаточного патрубка, создадутся условия для возрастания избыточного давления или разряжения выше допустимых, что может привести к разрушению кровли резервуара. Если максимальная пропускная способность одного дыхательного клапана недостаточна, устанавливают два клапана.Величины пропускной способности клапанов приведены в таблице 13.
Принцип работы клапана заключается в том, что при достижении в паровоздушном пространстве резервуара избыточного давления выше установленного клапан 8 под воздействием этого давления открывается и выпускает паровоздушную смесь и атмосферу через правую камеру, прикрытую огнезащитной сеткой.
Рисунок 24 – Механический дыхательный клапан:
1 - седло клапана; 2 - клапан впускной; 3 - крышка; 4 - прокладка; 5 - маховичок;
4 - рычаги крышек, 7 - корпус; 8 - клапан выпускной; 9 - сетка.
При разряжении клапан 2 под давлением наружного воздуха поднимается, обеспечивая поступление воздуха в резервуар через левую камеру. Как только внутри резервуара установится расчетная величина избыточного давления или разрежения, соответствующие клапаны закрываются под воздействием силы тяжести.
Конструкция указанного дыхательного клапана имеет недостаток: тарелки клапана при работе в условиях низких температур могут примерзать к седлам и клапан окажется неработоспособным. Этот недостаток может быть устранен путем изоляции смерзающихся поверхностей фторопластом. Для этого на каждой тарелке клапана закрепляется фторопластовая пленка, седла изолируются фторопластовыми пластинами, штоки обертываются фторопластовыми пластинами и устанавливаются в направляющих трубках, изготовленных из фторопласта.
Кроме указанных дыхательных клапанов, используются непримерзающие мембранные дыхательные клапаны типа НДКМ, которые отличаются от существующих дыхательных клапанов типа КД тем, что имеют другое конструктивное исполнение и обладают в 3 - 5 раз большей пропускной способностью при одинаковом диаметре присоединительного патрубка. Это позволяет сократить число клапанов, устанавливаемых на резервуаре. Конструкция клапана позволяет производить широкое регулирование пределов его срабатывания: при вакууме от 20 до 70 мм вод. ст., а при давлении от 100 до 200 мм вод. ст. Дыхательные клапаны НКДМ имеют присоединительные патрубки с диаметром условного прохода 150, 200, 250 и 350 мм.
Предохранительный гидравлический клапан (рис. 25) предназначен для тех же целей, что и механический дыхательный клапан и выполняет его роль при выходе последнего из строя или при нарушении технологического режима. Он работает по принципу гидравлических затворов, т. е. столб малоиспаряющейся жидкости препятствует свободному выходу паровоздушной смеси из резервуара и входу в него атмосферного воздуха. В качестве такой жидкости может быть использовано соляровое масло или дизельное топливо. Клапан срабатывает при избыточном давлении 200 мм вод. ст. и при разрежении 40 мм вод. ст.
Рисунок 25 - Предохранительный гидравлический клапан:
1 – пробка; 2 - сливная труба; 3 - корпус клапана; 4 - колпак; 5 - труба; 6 - растяжка; 7 - крышка; 8 - воронка; 9 - щуп
Клапан в резервуаре должен устанавливаться строго горизонтально (по присоединительному фланцу). Он заливается жидкостью после установки его на резервуар, причем до уровня, определенного предварительной регулировкой на давление и разрежение сжатым воздухом. Зависимость пропускной способности предохранительного клапана от диаметра его условного прохода представлена в таблице13.
Огневой предохранитель (рис. 26) предназначен для предотвращения попадания внутрь резервуара открытого пламени или искр, которые могут проникнуть в резервуар вместе с атмосферным воздухом через механический дыхательный или предохранительный гидравлический клапан. Он устанавливается на патрубках между резервуаром и указанными клапанами. Огневой предохранитель состоит из корпуса 2 с фланцами 1, и съемными боковыми крышками 3. Внутри корпуса помещен пакет из пластин, изготовленных из латуни или другого металла, обладающего высокой теплоемкостью. Принцип работы огневого предохранителя заключается в том, что при попадании в него пламени или искр от них отбирается пакетом тепло и их огнеопасность теряется.
Рисунок 26 – Огневой предохранитель
Огневые предохранители выпускаются с условным диаметром 50, 100, 150, 200 и 250 мм. Выбор размеров огневых предохранителей производится с учетом размеров дыхательных и предохранительных клапанов.
Сифонный кран (рис. 27) предназначен для слива отстоя воды и остатка топлива из резервуара и устанавливается в нижнем поясе резервуара на расстоянии 350 мм от днища. Существуют два типа сифонных кранов: СК-50 и СК-80 с диаметрами условного прохода 50 и 80 мм соответственно. На вертикальных резервуарах емкостью до 4000 м3 используются сифонные краны СК-50, а на резервуарах большей емкости - краны СК-80.
Рисунок 27 – Сифонный кран
Для горизонтальных резервуаров сифонные краны промышленностью не выпускаются. Для них используются сифонные краны вертикальных резервуаров с. незначительной доработкой.
Конструктивно сифонный кран для вертикальных резервуаров представляет собой составную трубу с изогнутым коленом 6. В месте прохода прямого участка трубы через стенку резервуара установлен сальник 5. На наружной части трубы смонтирован кран 2 и поворотная рукоятка 3. Наружная часть сифонного крана закрывается кожухом 1, снабженным замком 4. На конце изогнутого колена приварен кольцевой козырек 7. В нерабочем положении сифонный кран, как правило, устанавливается изогнутым коленом вверх, это исключает случаи примерзания колена 6 в слое отстоявшейся воды и обеспечивает промывку крана топливом от возможных остатков воды по окончании слива. В рабочем положении при сливе отстоя из резервуара сифонный кран с помощью рукоятки 2 устанавливается изогнутым коленом вниз, а кран 2 открывается.
Отстоявшаяся вода под воздействием давления столба топлива будет вытекать из резервуара. Кольцевой козырек 7 препятствует вытеканию чистого топлива вместе со сливаемой водой.
На рис. 28 показаны индивидуальные дренажные устройства наземных горизонтальных резервуаров. Слив отстоя производится в передвижную емкость при открытом вентиле. Дренажное устройство для подземных горизонтальных резервуаров показано на рис. 28, в. В этом случае слив отстоя осуществляется принудительно, т. е. с помощью насосов в передвижную емкость.
Рисунок 28 - Дренажные устройства горизонтальных резервуаров (уклон 1:40):
а ,б – для наземных резервуаров, в – для подземных резервуаров ; 1 – вентиль; 2 - сливная труба; 3 - присоединительные устройства
Система централизованного слива обеспечивает: своевременный контроль образования продуктов отстоя; освобождение резервуаров от остатков топлива перед их зачисткой или ремонтом; сокращение потерь топлива при сливных операциях; снижение пожароопасности, улучшение санитарного состоя-бия территории резервуарного парка и облегчение условий труда обслуживающего персонала при производстве сливных работ, особенно в осенне-зимний период.
Система централизованного слива (рис. 29) включает сливной узел резервуара А; узел слива отстоя Б и трубопроводы, связывающие их. Сливной узел резервуара предназначен для герметичного соединения сифонного крана с трубопроводом при слипе отстоя или остатка топлива из резервуара. Они изготовляются двух типов: с герметичной и негерметичной воронкой. В парном случае воронка изготавливается из труб, а во втором - из листового металла.
Рисунок 29 - Принципиальная схема системы централизованного слива отстоя
из резервуаров
Сливной узел резервуара с герметичной воронкой (рис. 30) состоит из хвостовика 5, сифонного крана 8, передвижной крышки 9 с рукояткой 2, воронки 10 и переходника 4 со штифтом 7. Герметичность соединения переходника 4 с хвостовиком 5 обеспечивается резиновыми уплотнительными колодками 6, герметичность соединения передвижной крышки 9 с переходником - резиновыми кольцами 3, а с воронкой 10 - резьбовым соединением с прокладкой 1. Нижняя часть воронки приварена к сливному трубопроводу 11.
При сливе отстоя из резервуара крышка 9 должна быть передвинута в верхнее положение. По окончании сливных работ, а также при освобождении резервуара от остатка топлива крышку 9 следует установить в нижнее положение и плотно навинтить на воронку 10.
Рисунок 30 - Сливной узел резервуара с герметичной воронкой
Сливной узел резервуара с негерметичной воронкой (рис. 31) предусматривает подвижное соединение верхнего конца переходника 6 с хвостовиком 8 сифонного крана 11, а нижнего со сливным трубопроводом 1 - жесткое. Крышка 4 воронки 3 в этом случае выполняется съемной. При сливе отстоя из резервуара крышка 4 снимается и открываются задвижки 2 и 7. При освобождении резервуара от остатка топлива открывается только задвижка 5. Переходник 6 фиксируется на хвостовике 8 с помощью штифта 10, а герметичность соединения достигается резиновыми кольцами 9. Конструкция обоих типов сливных узлов резервуаров позволяет производить поворот сифонных кранов в рабочее и нерабочее положения с помощью поворотной рукоятки.
Рисунок 31 - Сливной узел с негерметичной воронкой
Узел слива отстоя (см. рис. 29) предназначен для: приема отстоя, сливаемого из резервуаров 1 и 25; забора остатка топлива и прием его из резервуаров 1 и 25 при подготовке их к зачистке или ремонту и других операций, о которых будет сказано ниже. Он состоит из горизонтальных подземных резервуаров 7, самовсасывающего насоса 8 (например, типа СВН-80), сетчатого фильтра 11, фильтра 13 типа ТФ-2М, присоединительных наконечников 9, сливных воронок 14, 19 и задвижек 10, 12, 15, 16, 17, 18, 20, 21, 22 и 23. -
Принцип работы централизованной системы со сливным узлом, имеющим герметичную воронку, заключается в том, что при сливе отстоя из резервуаров 1 и 25 сифонные краны 2 и 24 устанавливаются в рабочее положение, задвижки 20, 16, 18 открываются, крышка переходника свинчивается с воронки и передвигается в рабочее положение, затем открывается запорная арматура, установленная на сифонных кранах. Продукты отстоя под действием столба топлива будут поступать из резервуаров 1 и 25 по трубопроводу 6 в резервуар 7. Одновременно осуществляется визуальный контроль сливаемого продукта.
После окончания слива отстоя сифонные краны 2 и 24 устанавливаются в нерабочее положение и закрываются, передвижная крышка плотно навинчивается на воронку, а задвижки 20, 16 и 18 закрываются.
Освобождение резервуаров 1 и 25 от остатков топлива при их подготовке к зачистке или ремонтным работам осуществляется принудительно: сифонные краны устанавливаются в рабочее положение и открываются задвижки 20, 17 и 18, затем включается насос 8. Сливаемый остаток подается насосом 8 в заранее подготовленный чистый резервуар 7, емкость которого должна соответствовать объему сливаемого остатка топлива.
Кроме указанных операций система централизованного слива обеспечивает слив отстоя из ТЗ (открыты задвижки 15, 17, 18 или 10, 17 и 18); выдачу отстоя или остатков топлива из резервуаров 1 и 25 в передвижные резервуары (открыты задвижки 10 или 12), (открыты задвижки 12, 16, 18 или 10, 16, 22); забор и выдачу отстоя или остатка топлива из резервуаров 1 и 25 в передвижные резервуары (открыты задвижки 10 или 12).
Указатель уровня (рис. 32) предназначен, для контроля уровня топлива в резервуаре с отсчетом показаний у резервуара или на пульте дистанционного управления склада ГСМ аэропорта.
Указатель уровня типа УДУ-5П состоит из счетного механизма 1, трубы 2, системы блоков 3 с гидравлическим затвором, приставки для дистанционного отсчета показаний, металлической ленты 6, поплавка 7, направляющих тросов 5. Направляющие тросы крепятся к резервуару верхним 4 и нижним 8 креплениями. Поплавок 7 соединен со счетным механизмом 1 лентой 6, которая выведена к нему через герметичную блочную систему 3 и трубу 2. Принцип действия указателя заключается в том, что при заполнении или опорожнении резервуара поплавок 7 перемещается по вертикальным направляющим тросам 5 вместе с уровнем топлива.
Рисунок 32 - Указатель уровня типа УДУ-5П
С поплавком перемещается и лента, которая приводит в движение маховик счетного механизма и его стрелку. Одновременно с этим передается вращение и на контактный механизм дистанционной приставки, сигналы от которой поступают на пульт дистанционного управления. В настоящее время выпускается аналогичный прибор более совершенной и надежной конструкции УДУ-10.
Сниженный пробоотборник предназначен для полуавтоматического отбора средней пробы из вертикальных резервуаров. Они выпускаются трех типов: ПСР-4, ПСР-5 и ПСР-7. На наземных вертикальных резервуарах с максимальной высотой 12 м и резервуарах с понтонами с такой же высотой устанавливаются пробоотборники ПСР-4, ПСР-7 соответственно, а на заглубленных резервуарах с максимальной высотой 7 м - пробоотборник ПСР-5.
Пробоотборник ПСР-4 (рис. 33) состоит из сливного крана 1, пробоотборной трубки 2, воздушной трубки 3, воздушного насоса 7, сильфонного клапана 9 с входным отверстием 8. Для монтажа пробоотборника в резервуаре предусматривается монтажный люк 6 и горловина 4. Нижняя часть пробоотборника монтируется в нижнем поясе резервуара 5. Пробоотборная трубка 2 в верхней части сообщается с паровоздушным пространством резервуара, а нижний конец ее выведен из резервуара и перекрыт краном 1. Верхняя часть трубки 3 заглушена, а нижняя выведена из резервуара и присоединена к насосу 7.
Рисунок 33 – Сниженный пробоотборник ПСР-4
При отборе проб в трубку 3 с помощью воздушного насоса 7 нагнетается воздух и создается давление, под воздействием которого открываются сильфонные краны 9, обеспечивая поступление топлива через отверстие 8 в трубку 2. Снизив давление в трубке 3, открывают кран 1 и сливают в сосуд топливо, находящееся в трубке 2.
Насосные станции
Насосные станции (насосные агрегаты) систем ЦЗС располагаются непосредственно за группой расходных резервуаров на расстояниях, обоснованных гидравлическими расчетами и противопожарными требованиями. Они предназначены для забора топлива из расходных резервуаров и подачи его по трубопроводной сети системы ЦЗС через фильтрационные пункты к заправочным агрегатам с определенными расходом и избыточным давлением, необходимым для заправки обслуживаемых типов самолетов.
Для каждой насосной станции количество насосов определяется из расчета обеспечения одновременной заправки самолетов в часы пик, а типы насосов подбираются в зависимости от характера трубопроводной сети, применяемого оборудования и приемистости заправочных точек (горловин или штуцеров) обслуживаемых типов самолетов.
В насосных станциях систем ЦЗС используются преимущественно центробежные насосы, причем независимо от производительности системы как минимум предусматриваются два насоса, один из которых может быть резервным и при необходимости - рабочим. Устанавливать один насосный агрегат, рассчитанный на максимальную производительность системы, неэкономично, так как при меньшем количестве одновременно заправляемых самолетов работа такого агрегата будет нерентабельной, если в его конструкции не предусмотрено изменение подачи с соответствующим уменьшением затрат электроэнергии.
Наибольшее распространение получили насосные станции с группой параллельно установленных насосов, автоматически включающихся для подачи топлива в зависимости от количества одновременно заправляемых самолетов.
Современные стационарные ГЗТ работают по принципу высокого и низкого давления в топливоподающих трубопроводах. Соответственно рассчитываются и подбираются насосные группы ГЗТ, их напорные характеристики и суммарная подача топлива. В системах ГЗТ с высоким давлением в магистралях напор, создаваемый насосами, должен обеспечивать необходимое давление в трубопроводных магистралях, раздаточных колонках и агрегатах заправки до бортовых штуцеров ВС включительно с учетом их приемных способностей при групповой заправке нескольких ВС.
В системах ГЗТ с низким давлением насосная станция должна поддерживать постоянное давление, компенсируя потери в трубопроводах до приемного рукава агрегата заправки, который должен иметь собственный топливный насос, обеспечивающий заправку топливом ВС. В системах обоих типов потеря давления на участках между входом в приемный рукав агрегата заправки и бортовым штуцером ВС составляет около 80% суммарный потери напора насосных станций.
Для расчета требуемой подачи насосной станции ГЗТ и определенного внутреннего диаметра магистрального трубопровода и всей трубопроводной сети в начале определяется требуемая производительность системы ГЗТ. Согласно отечественным нормативным документам производительность системы ГЗТ определяется по формуле:
(2.1)
где Qгзт – истинная производительность ГЗТ, м3/ч;
q – расчетная производительность заправки топливом ВС по группам или типам, м3/ч;
Uз – максимальная интенсивность поступления ВС по группам или типам, ед/ч;
tз – расчетная продолжительность заправки топливом ВС каждой группы или типа, ч;
I = 1,2,3 …n – количествогрупп или типов ВС, подлежащих заправке топливом из системы ГЗТ;
По зарубежному опыту при выборе насосов, их количества и характеристик рекомендуется учитывать следующие аспекты [28]:
Максимальная производительность системы ГЗТ в расчете на один насос или подача одного насоса не должны превышать 4500 л/мин;
Число насосов в группе, включенных по параллельной схеме не должно превышать шести;
При необходимости развития на ГЗТ большой производительности создаются две групп насосов, соответственно подключаемых к разным участкам раздаточных систем, например, на перронах для разных типов ВС.
В составе каждой группы насосов один из них или дополнительный насос меньшей производительности должны поддерживать постоянно расчетное давление в трубопроводных магистралях системы, чтобы компенсировать потери и обеспечивать готовность системы к работе.
На входе во всасывающую линию каждого насоса должен быть установлен фильтр грубой очистки топлива от твердых частиц загрязнения для защиты оборудования насоса, а в напорной линии после каждого насоса в отечественной и зарубежной практике, как правило, устанавливаются фильтры-водоотделители с пропускной способностью, равной подаче насоса и необходимая арматура. Таким образом, образуется автономный насосно-фильтрационный блок, который для технического обслуживания насоса или фильтра-водоотделителя можно временно перекрыть, не прерывая работу всей системы ГЗТ. Кроме того, в зависимости от конкретных условий могут устанавливаться индикаторы контроля температуры корпуса насоса. Типовая схема компоновки одной из групп насосов приведена на рис. 34.
|
|
|
|
|
Дата добавления: 2020-07-18; просмотров: 985; |