Методы определения припусков на обработку
Методы определения припусков:
- опытно-статистический
- расчетно-аналитический.
По первому методу общие и операционные припуски определяются по данным таблиц, составленных на основе обобщения и систематизации производственных данных передовых заводов (некоторые из них стандартизированы). Табличные значения припусков во избежание получения брака завышены и не учитывают конкретных условий обработки (последовательности выполнения операций, схем базирования и др.).
Расчетно-аналитический метод основан на учете конкретных условий выполнения ТП обработки путем выявления и анализа факторов, влияющих на величину припуска. К таким факторам относятся:
- величина микронеровностей поверхности ;
- глубина дефектного слоя поверхности h;
- пространственные отклонения поверхностей (коробление и кривизна поверхности, эксцентричность оси отверстия, несовпадение положения осей и т.д.);
- погрешность установки заготовки .
Из факторов, влияющих на величину припуска, относятся к предшествующей обработке, и им присваивается индекс , относится к выполняемой обработке и имеет индекс
.
На рис. 4.1. показано схематичное изображение величины минимального припуска и факторов, влияющих на его величину.
Минимальный промежуточный припуск на выполняемый переход в общем виде определяют по формуле:
. (4.1)
Пространственные отклонения и погрешности установки представляют собой векторы, их суммируют по правилу сложения векторов. При обработке плоских поверхностей, когда имеются коллинеарные векторы:
, (4.2)
при обработке поверхностей вращения, когда невозможно предвидеть направление векторов суммирование производится по правилу квадратного корня:
. (4.3)
Минимальный припуск на обработку плоскостей
. (4.4)
Для поверхностей вращения припуск считается на диаметр:
. (4.5)
Рис. 4.1. Факторы, влияющие на величину припуска |
Частные формулы для конкретных случаев обработки:
- при обработке цилиндрической поверхности заготовки, установленной в центрах
; (4.6)
- при обработке отверстий плавающей разверткой и при протягивании
, (4.7)
- при обработке, целью которой является уменьшение шероховатости поверхности (полирование, суперфиниширование)
Рис. 4.2. Схема образования максимального и минимального припуска |
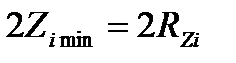
- при шлифовании заготовок после их термической обработки в расчетных формулах будет отсутствовать слагаемое .
Величина припуска, снимаемого с поверхности каждой детали партии, зависит от ряда случайных факторов и поэтому является случайной величиной. При однопроходной обработке деталей на предварительно настроенных станках в результате упругих деформаций технологической системы имеет место явление копирования. Оно заключается в том, что при обработке заготовки с меньшим размером (рис. 4.2) выдерживаемый размер
получится меньшим и наоборот, большему размеру заготовки
соответствует большее значение выдерживаемого размера
. Таким образом, действительные припуски на обработку в партии заготовок будут
Рис. 4.2. Схема образования максимального и минимального припуска |
колебаться вследствие колебаний размеров заготовок, а также твердости их материала.
Зависимости для минимального и максимального припусков наружных поверхностей (рис. 4.2) имеют вид:
, (4.9)
, (4.10)
, (4.11)
где - допуск на размер заготовки;
- допуск на выполняемый размер.
Номинальный припуск для наружного размера
, (4.12)
где - нижнее отклонение размера заготовки;
- нижнее отклонение размера детали.
Ориентировочно на практике 60 % суммарного припуска отводится для черновой, а остальная часть (40 %) – для чистовой обработки; при черновой, получистовой и чистовой обработке припуск составляет, соответственно, 45, 30 и 25 % общего припуска.
Дата добавления: 2016-06-29; просмотров: 7783;