Автоматизация контроля
Автоматизация контроля является одним из наиболее сложных вопросов комплексной автоматизации технологических процессов. Она осуществляется по двум принципиально различным направлениям: путем автоматизации послеоперационного (пассивного) контроля и технологического (активного) контроля. Второе направление – направленное на активизацию контроля – является наиболее прогрессивным и перспективным направлением, поскольку качество продукции обеспечивается самим технологическим процессом.
При пассивном контроле контрольные устройства фиксируют размеры деталей или сортируют их по размерам, не оказывая воздействия на ход технологического процесса.
Примером могут служить контрольно–сортировочные автоматы, которые будут рассмотрены далее в этой теме.
При активном контроле контрольные устройства оказывают воздействие на ход технологического процесса, т.е. активно вмешиваются в технологический процесс. Эти системы относятся к замкнутым системам автоматизации, т.е. к системам с обратной связью.
Блок схема замкнутой системы автоматизации может быть представлена следующим образом:
Размер обрабатываемой детали контролируется с помощью преобразователя ПР. В зависимости от действительного размера преобразователь подает сигналы на СУ, где сравнивается с заданным сигналом.
Величина рассогласования заданного сигнала и сигнала обратной связи усиливается усилителем и попадает в исполнительный орган, в результате чего-либо меняется режим резания, либо подается команда на остановку станка.
Поэтому активным контролем называется метод контроля, по результатам которого вручную или автоматически осуществляется воздействие на ход технологического процесса.
К активному контролю относится, например, контроль при обработке методом пробных проходов; контроль, по результатам которого вручную подналаживаются станки – автоматы; управление процессом обработки по результатам измерения параметров заготовки (для получения заданных размеров, а также для стабилизации сил резания или времени обработки).
К средствам активного контроля относятся устройства для автоматического регулирования режимов резания обработки (например, для стабилизации мощности, затрачиваемой при резании, что соответствует условию наибольшей производительности). Это также системы компенсации износа круга методом его правки перед чистовыми проходами, это контроль в процессе обработки, регулирование размеров с помощью подналадочных систем.
Таким образом, любое измерение, в результате которого осуществляется определенное воздействие на тот или иной процесс, можно отнести к активному контролю.
Особое внимание сейчас уделяется развитию средств автоматического активного контроля. Его внедрение позволяет повысить качество продукции, сократить время обработки деталей путем интенсификации режимов резания и исключения остановок станка для промежуточных измерений, уменьшить затраты на окончательный послеоперационный контроль.
В зависимости от метода измерения средства активного контроля разделяются на устройства, основанные на прямом методе измерения, и устройства, основанные на косвенном методе измерения.
При прямом методе измерения контролируется непосредственно размер изготавливаемой или изготовленной детали. База измерения при этом совпадает с поверхностью контролируемой детали.
При косвенном методе контролируется не размер детали, а положение поверхности измеряемой детали, или положение режущей кромки инструмента, или исполнительных органов станка по отношению к базе установки прибора.
Рассмотрим это на примере плоского шлифования (рис. 29.1).
|
|
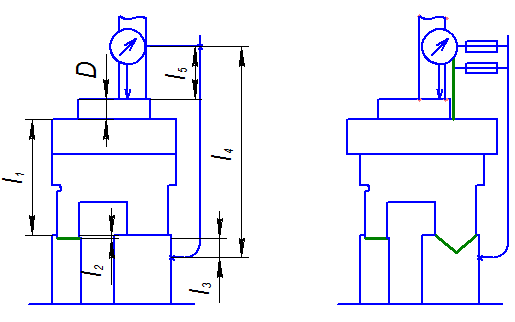
Рис. 29.1. Схема плоского шлифования с активным контролем: а) косвенный метод измерения, б) прямой метод измерения
При косвенном методе измерения в измерительную цепь помимо размера контролируемой детали включаются размерные параметры самого станка. В данном случае размер является замыкающим, и его точность зависит от точности размерной цепи, т.е.
.
При прямом методе измеряем непосредственно размер и нет той длинной измерительной цепи, что имели при косвенном методе. Точность обработки в этом случае в основном зависит от тепловых деформаций обрабатываемой детали, погрешности самого прибора и толщины слоя металла, снимаемого с детали за один проход.
Таким образом, косвенный метод менее точен, чем прямой, поскольку получаются более длинные, чем при прямом, размерные цепи.
По выполняемым функциям средства активного контроля размеров могут быть разделены на 4 группы:
1) устройства, контролирующие детали непосредственно в процессе обработки (приборы управляющего контроля);
2) подналадчики;
3) блокирующие устройства (измерительные «заслоны»);
4) устройства контроля заготовок до обработки.
Дата добавления: 2017-06-13; просмотров: 1713;