Изготовление формы глубокой печати
Изготовление формы глубокой печати отличалась чрезвычайно большой сложностью и нестабильностью технологических операций.
Наиболее широкое распространение в начале внедрения способа глубокой печати в производство получил так называемый пигментный способ копирования.
По этой технологии копия и форма изготавливались непосредственно на формном цилиндре (рис. 6.80).
Рис. 6. 80. Схематический разрез формного цилиндра глубокой печати:
1 – стальной цилиндр; 2 – слой никеля (5–10 мкм); 3 – основной слой меди;
4 – разделительный слой 1 мкм (серебряный или др.);
5 – медная рубашка (80–100 мкм)
Растр для глубокой печати по устройству, назначению и способу применения резко отличается от растра высокой печати. Растр глубокой печати предназначается прежде всего для создания микрокапиллярной структуры на поверхности печатной формы. Микрокапиллярная структура позволяет удержать в ячейках жидкую краску, которая применяется в глубокой печати. С другой стороны, перемычки растра, находящиеся на поверхности печатной формы, создают опору для ракеля при очистке печатной формы от избытка краски. Таким образом изображение на печатной форме разбито растром на одинаковые по размеру ячейки, и структура оттиска, например шрифта, имеет характерный пилообразный контур (рис. 6.81).
Рис. 6.81. Оттиск шрифта,
полученный способом глубокой печати
Пленочный растр для глубокой печати имеет прозрачные линии и черные квадратные клетки между ними (рис. 6.82). Линии растра располагаются под углом 45° к сторонам стеклянной пластины и пересекаются друг с другом под прямым углом. Ширина линий относится к ширине промежутков между ними как 1 : 3; 1 : 3,5 или 1 : 4 (в зависимости от вида продукции). Таким образом, растр для глубокой печати представляет собой систему весьма тонких прозрачных линий с относительно большими непрозрачными клетками. Существуют и другие варианты растров для глубокой печати. Так, например, иногда практически применяются растры, черные элементы которых имеют форму не квадратов, а ромбов. Однако сущность использования растра для получения опорных линий не изменяется.
Рис. 6.82. Схема растра глубокой печати
Применяется растр в глубокой печати не при фотографировании оригинала, а при копировании на светочувствительную поверхность, причем он должен находиться в полном контакте с этой поверхностью. В результате копирования и травления формы глубокой печати с применением растра на ней получается система пересекающихся под прямым углом линий, не тронутых травлением.Между этими линиями расположены углубленные печатающие элементы, заполняемые в процессе печатания жидкой краской. В наиболее распространенном варианте формы глубокой печати площадь этих элементов (точек ) на всех участках печатной формы одинаковая, а глубина различная в зависимости от тональности изображения: оттиск с такой формы состоит из точек одинакового размера, но различной насыщенности.
Процесс изготовления формы глубокой печати включает две стали копирования. Вначале на пигментную бумагу копируется растр, а потом копируется полутоновой диапозитив. После двухступенчатого копирования копия переводился на цилиндр, который затем помещался в ванну с водой, где происходило проявление копии. На следующем этапе цилиндр после соответствующей корректировки изображения копии перемещали в ванну с травящим раствором, в которой происходило вытравливание медной рабочей рубашки на заданную глубину. Медь травится хлорным железом, и количество ванн для травления копии могло достигать 4–5. В каждой ванне был свой раствор определенной плотности, что позволяло провести травление меди более равномерно. Процесс травления мог продолжаться несколько часов, и в случае какой-либо ошибки форма практически уходила в брак. Краткая схема изготовления печатной формы с использованием пигментной бумаги показана на рисунке 6.83.
1. Очувствляют пигментную бумагу и помещают ее в копировальную раму.
2. Копируют растр, при этом под прозрачными ячейками происходит задубливание пигментно-желатинового слоя.
3. Второе копирование. Копируют полутоновой диапозитив, происходит задубливание пигментно-желатинового слоя обратно пропорционально оптическим плотностям диапозитива.
4. Проявление в воде. Незадубленные участки вымываются, образуется рельефная копия (рис. 6.83в).
5. Травление FeCl3. Травление производят в нескольких ваннах с различной плотностью раствора. Чем меньше толщина пигментно-желатинового слоя, тем быстрее проникает раствор и, следовательно, на большую глубину вытравливается медная рубашка. Так происходит формирование печатающих элементов формы глубокой печати (рис. 6.83д).
а |
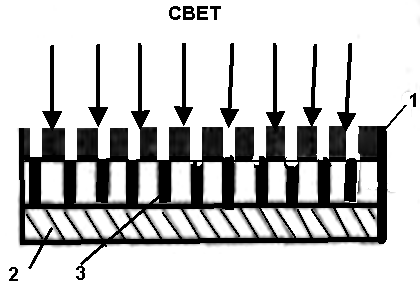
б |
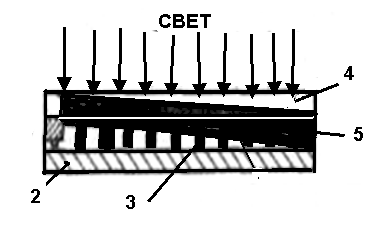
в |
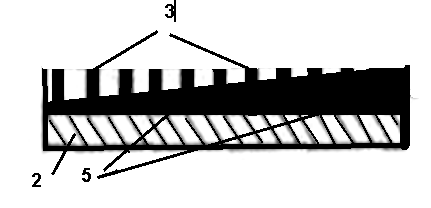
г |
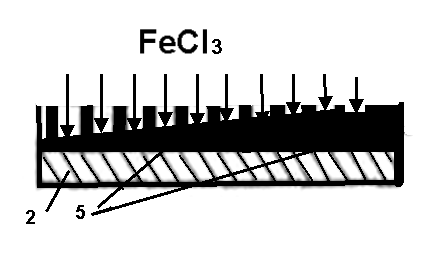
д |
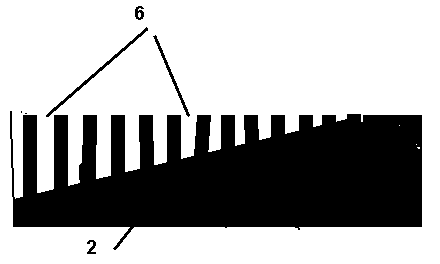
Рис. 6.83. Схема изготовления формы глубокой печати при применении пигментной бумаги: а – копирование растра; б – копирование диапозитива; в – проявление;
г – травление; д – готовая форма; 1 – растр; 2 – медная рубашка; 3 – задубленные
желатиновые перегородки; 4 – полутоновой диапозитив; 5 – задубленный желатин
после копирования диапозитива; 6 – вытравленные ячейки печатающих элементов
Трудоемкость процесса изготовления значительно снизилась после 1960 г., когда фирмы Hell выпустила электронные автоматы для гравирования форм глубокой печати HelioKlishograph T200 и K202 (рис. 6.84). Этот автомат гравировал медную рубашку.
В отличие от классического способа глубокой печати, здесь различная оптическая плотность на оттиске достигается за счет разных площадей растровых точек при примерно одинаковой глубине печатающих элементов. Эта технология получила название «способ глубокой автотипии»(рис. 6.85).
Рис. 6.84. Электронно-гравировальный автомат HelioKlischograph K202
Рис. 6.85. Печатная форма, полученная электронным гравированием:
а – в разрезе; б – в плане до нанесения краски; в – в плане после нанесения краски;
1 – печатающие элементы; 2 – пробельные элементы
С 1985 г. при изготовлении формных цилиндров глубокой печати стали использоваться цифровые гравировальные устройства, получающие сигнал не со сканируемой аналоговой фотоформы, а от компьютера. Технология «Компьютер – формный цилиндр» в глубокой печати распространился раньше, чем технология «Компьютер – печатная форма» в офсетной печати.
Для целей прямого гравированиябыли испытаны системы с использованием теплового воздействия электронного и лазерного излучения применительно к различным материалам-основам. Электронное излучение оказалось очень эффективным, однако слишком дорогим по реализации в силу необходимости применения вакуумной техники. По экономическим причинам такие системы еще не выпускаются.
В 1995 г. была представлена автоматическая гравировальная установка Laserstar фирмы Max Datwyler с использованием лазера. В ней, однако, цилиндр должен быть покрыт цинком (вместо меди) в связи с его лучшей поглощающей способностью, особенно на длине волны 1064 нм (Nd:YAG–лазер). Это решение привело к необходимости перестройки других стадий обработки цилиндров, а следовательно, к большим инвестициям.
Дата добавления: 2017-04-05; просмотров: 3414;