Технологичность формы корпуса
2.1. Общие сведения
До 70-х 80-х годов форму и обводы корпуса выбирали исходя из требований к мореходным и эксплуатационным качествам судна. Подавляющее большинство судов имело лекальные обводы. Это приводило к большому объему плазовых работ, большой номенклатуре оснастки (постели, шаблоны и др.), большому объему гибочных работ, сложности сборочных и сварочных работ. Использование лекальных обводов сдерживало применение механизированных и автоматизированных линий. Требование производства – максимальное упрощение формы корпуса – находится в противоречии с требованиями эксплуатации; следовательно, упрощение формы обводов не должно ухудшать (или должно незначительно ухудшать) мореходные качества при значительном снижении трудоемкости изготовления деталей, узлов, секций и корпуса в целом.
Упрощение формы обводов позволяет:
· сократить и упростить плазовые и разметочные работы;
· свести к минимуму или даже ликвидировать гибочные работы;
· уменьшить количество отходов;
· увеличить объем автоматизированных и механизированных операций при изготовлении деталей, сборке и сварке конструкций в цехе и на стапеле;
· уменьшить производственные площади при сборке и сварке секций;
· увеличить количество унифицированных и стандартных деталей и элементов конструкций корпуса судна;
· сократить номенклатуру оснастки для сборки и сварки секций, проверочных работ на стапеле;
· улучшить условия прокладки трубопроводов, кабельных трасс, размещения механизмов и оборудования;
· улучшить использование объема внутренних помещений судна.
Упрощение обводов корпуса идет по следующим направле-ниям:
· применение цилиндрической вставки;
· отказ от подъема днища;
· отказ от седловатости и погиби палуб;
· создание корпусов с цилиндрическими и коническими поверхностями, т. е., разворачи-ваемыми на плоскость;
· создание криволинейной по-верхности с использованием спрямленных шпангоутов (рис. 2.1);
· спрямление шпангоутов и ватерлиний и получение плоскогранной формы корпуса – наиболее радикальное направление.
2.2. Влияние формы корпуса на мореходные качества и технологичность
2.2.1. Подъем днища
На сопротивление движению воды подъем днища не влияет, а трудоемкость изготовления секции возрастает за счет необходимости установки набора под малку; невозможно использовать ПМЛ.
2.2.2. Радиус скулового закругления
Радиус скулового закругления незначительно влияет на скорость хода судна, но оказывает влияние на возможность применения ПМЛ. Большой радиус закругления обуславливает необходимость устанавливать крайние продольные ребра жесткости под малку. Радиус закругления следует назначать равным (или несколько меньшим) высоте междудонного ространства. В этом случае продольные балки устанавливаются перпендикулярно обшивке. Такой радиус закругления позволяет проектировать смежные с закруглением днищевые и бортовые секции плоскими, что позволяет изготавливать их на ПМЛ. К тому же облегчается стыковка бортовых секций с днищевыми.
Полный отказ от скулового закругления позволяет перейти к плоскогранным обводам корпуса судна, что будет рассмотрено ниже.
2.2.3. Погибь и седловатость палуб
Палубы обычно имеют лекальные обводы, т. е. погибь и седловатость, что связано с необходимостью скатывания воды. Седловатость палубы в носу создает дополнительную плавучесть, уменьшает продольную качку и заливаемость при ходе на волнии.
Отказ от седловатости и погиби, позволяет изготавливать палубные секции плоскими со всеми вытекающими последствиями:
· возможность использования ПМЛ снижает трудоемкость изготовления секций и узлов на 30 – 40%, стоимость ПМЛ для изготовления плоской секции ниже, чем для изготовления лекальных секций;
· ликвидация гибочных работ сокращает трудоемкость операций по изготовлению деталей на 12 – 15% ;
· унификация конструктивных решений снижает количество типоразмеров и увеличивает число деталей в партии;
· повышается коэффициент использования материалов с 0,85 до 0,9, а затраты на материалы снижаются на 3 – 4 % от общей стоимости корпуса;
· трудоемкость изготовления секций снижается на 9% по сравнению с секциями, имеющими погибь в одном направлении, и 19% – по сравнению с секциями, имеющими погибь в двух направлениях;
· возможно внедрение групповой технологии при изготовлении узлов и секций.
Отрицательные последствия отсутствия седловатости можно компенсировать увеличением минимального надводного борта на величину:
ΔН = 0,75Zср,
где Zср – среднее значение изменения седловатости
Zср=0,012 L/3 +10
Таким образом, относительный запас плавучести составляет около 7 – 8% либо за счет погиби, либо за счет увеличения надводного борта.
Лекальную погибь и седловатость палуб можно также заменить отрезками прямых, однако целесообразнее отказаться от нее совсем.
2.2.4. Цилиндрическая вставка
Результаты экспериментов по определению влияния цилиндрической вставки на ходкость показали:
· положение и длина цилиндрической вставки являются важнейшими показателями формы, влияющими на ходкость судна;
· суда с разными по длине цилиндрическими вставками могут иметь близкие по величине сопротивления движению;
· при определенных условиях увеличение длины цилиндрической вставки и, соответственно, увеличение продольной полноты не увеличивает сопротивление движению;
· длины носовой и кормовой частей цилиндрической вставки влияют на различные составляющие сопротивления: длина носовой части – на волновое сопротивление, а длина кормовой – на сопротивление формы.
Отношение длин носовой части цилиндрической вставки к кормовой Lцн/Lцк влияет на интерференцию волн – его уменьшение снижает волновое сопротивление.
В результате проведенных в разных странах исследований на моделях судов была получена зависимость оптимальной длины цилиндрической вставки от коэффициента общей полноты. Также были получены оптимальные значения положения цилиндрической вставки относительно миделя.
Оптимальная длина носового заострения при значениях коэффициента общей полноты δ = 0,7 – 0,75:
Lн ≈ v2/0,41g = 0,042 v2.
Оптимальное значение минимальной величины кормового заострения:
Lк min = 4,08(βBd)1/2,
где: β – коэффициент полноты ватерлинии; B – ширина судна; d – осадка.
Увеличение длины цилиндрической вставки снижает стоимость судна, упрощает и ускоряет постройку, улучшает условия внутреннего расположения.
Применение цилиндрической вставки позволяет снизить трудоемкость следующих операций:
· разметка металла с изготовлением шаблонов – упрощается разметка, снижается потребность в шаблонах;
· резка металла – трудоемкость снижается за счет увеличения длин прямолинейных кромок;
· гибка металла – значительно сокращается трудоемкость за счет уменьшения лекальности (сокращается количество гнутых листов, значительная часть гнутых листов имеет не сложную, а простую кривизну, что позволяет использовать для их гибки гибочные вальцы вместо гидравлических прессов);
· секционная сборка – снижается трудоемкость на подготовку оснастки и за счет упрощения стыковочных и пригоночных работ;
· секционная сварка – уменьшается длина свариваемых кромок, увеличивается возможность применения автоматической сварки;
· корпусосборочные работы – снижается трудоемкость подготовки стапельной оснастки, пригоночных и проверочных работ;
· сварочные работы на стапеле – трудоемкость снижается за счет возможности использования автоматической сварки и прямолинейности кромок;
· трубопроводные работы – уменьшается объем гибки и облегчается сборка труб за счет увеличения прямолинейности трасс трубопроводов.
2.2.5. Плоскогранные суда
Как уже говорилось, наиболее радикальный способ упрощения обводов – создание полностью плоскогранных судов.
Исследования, проведенные в разных странах еще в средине ХХ века, показали, что при малых числах Фруда потери скорости у плоскогранных речных судов почти не происходит. С тех пор баржи и другие тихоходные речные суда строят с упрощенными (плоскогранными) обводами.
В 60-х годах ХХ века в разных странах проводились теоретические исследования и модельные испытания, а затем были построены морские суда с упрощенными обводами (первые из них: танкера типа "Крым", БМРТ типа "Меридиан" (рис.2.3 и 2.4) – СССР, "Мини-балкер" – Япония, и др.).
Проводились также модельные испытания и судов с полностью плоскогранными обводами, которые показали, что если придерживаться определенных правил при проектировании таких корпусов, то падение скорости при низких числах Фруда (или увеличение буксировочного сопротивления) незначительно – около 2,5% при ходе в грузу, но возрастает до 12% при ходе в балласте.
В ФРГ были спроектированы и построены суда с полностью плоскогранными обводами: танкера типа "Пионер" и контейнеровозы типа "Контейнер-Пионер" со скоростями хода соответственно 15 – 17 и 19 – 20 узлов. Проекции "корпус" этих судов показаны на рис. 2.5 и 2.6. Интересно, что скорости реальных судов оказались выше, чем рассчитанные по модельным испытаниям на 0,52 и 1,31 узла соответственно. Согласно модельным испытаниям скорость контейнеровоза с лекальными обводами должна была составить 18,11 узла, а с упрощенными обводами – 18. Но на ходовых испытаниях контейнеровоз с плоскогранным корпусом показал скорость 18,68 узла. Почему – это до сих пор загадка, т. к. аналогичных судов с лекальными обводами построено не было.
|
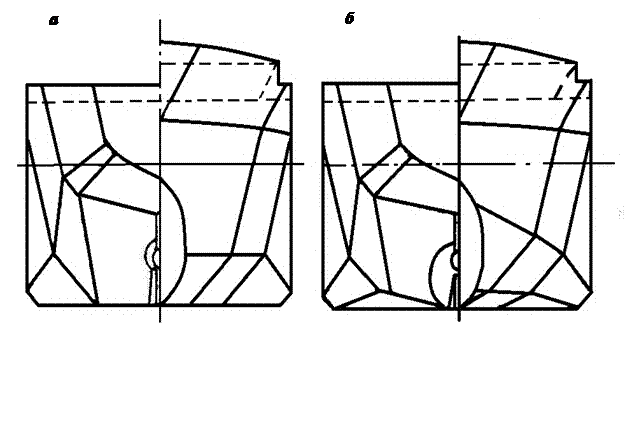
Строились суда с плоскогранными обводами и в CCCР, например, в Николаеве на Черноморском судостроительном заводе, рис. 2.7.
Рис. 2.7. Судно с плоскогранными обводами
По результатам модельных испытаний можно сделать следующие выводы о влиянии плоскогранных обводов на мореходные качества:
· при соблюдении определенных рекомендаций при проектировании, скорость хода падает незначительно – 2,5% при ходе в грузу и 12% при ходе в балласте;
· влияние мелководья на мореходные качества более значительно, чем для судов с лекальными обводами;
· падение скорости на волнении меньше, чем у судов с лекальными обводами (при длине волны, равной длине между перпендикулярами и ветре в 7 баллов падение скорости для модели судна с упрощенными обводами составило 54%, с лекальными – 60 – 65%);
· уменьшается вертикальная и килевая качка;
· влияние бульба на мореходные качества более значительно.
В 70-е годы вырисовывались перспективы широкого внедрения плоскогранных судов. Однако резкое удорожание топлива и увеличение эксплуатационных расходов заставило считаться даже с незначительным увеличением сопротивления движению и потерей скорости хода. В результате в настоящее время плоскогранные суда не получили распространения. Однако, многие ведущие кораблестроители считают, что можно строить суда с прямыми обводами, не уступающими по ходкости судам с лекальными обводами, если будут выдерживаться определенные рекомендации при проектировании таких корпусов.
Вот некоторые из них:
· линии слома корпуса должны совпадать с линиями тока жидкости;
· углы слома в носу для судов с числом Фруда Fr ≤ 0,2 должны быть не менее 170˚, для судов с Fr > 0,2 – не менее 179˚, в корме (на конце линии обтекания) углы слома должны быть не менее 120˚;
· угол перехода от днища к скуле должен быть не менее 45˚.
Нам же, с точки зрения технологичности, необходимо выявить влияние плоскогранной формы корпуса на такие показатели, как трудоемкость и стоимость его изготовления.
Проработки для морских судов показали, что трудоемкость изготовления плоскогранных корпусов разных типов снижается на 6,5 – 9%, а стоимость всего судна – всего на 1,4%, что не компенсирует увеличение эксплутационных затрат от потери скорости хода. Но, следует отметить, что в этих расчетах трудоемкости не были учтены использование унифицированных деталей и секций и возможность широкого использования механизированных линий. Кроме того, необходимо продолжать поиск таких форм, которые не будут вызывать потери скорости.
С другой стороны, бессистемное манипулирование плоскими гранями ради снижения потерь скорости хода может не только не снизить, но даже повысить трудоемкость изготовления корпуса.
Например, трудоемкость изготовления плоскогранной бортовой секции, изображенной на рис.2.8 б ниже трудоемкости изготовления лекальной секции (вариант "а") на 10% при условии их изготовления без применения механизированных поточных линий и на 33% – с применением ПМЛ. А трудоемкость изготовления секции по варианту "в" ниже трудоемкости изготовления варианта "а" с применением ПМЛ всего на 14%, а без применения ПМЛ – даже выше на 10%.
В заключение отметим, что в настоящее время суда проектируют с максимально возможным упрощением формы корпуса, но только не плоскогранные. Это вызвано дальнейшим ростом цен на нефть и нефтепродукты что, в свою очередь, делает непозволительным такую роскошь, как потеря скорости хода даже 0,1 – 0,2 узла.
Дата добавления: 2021-05-28; просмотров: 476;