РУЧНАЯ ДУГОВАЯ СВАРКА ПОКРЫТЫМИ ЭЛЕКТРОДАМИ
Ручная дуговая сварка покрытым электродом – это способ сварки плавлением, при котором дуга горит между плавящимся металлическим электродом и сварочной ванной, поверхность которой защищается от воздуха за счет расплавления электродного покрытия. Подача электрода в ванну и его перемещение вдоль стыка производится сварщиком вручную (рис. 22)
Рис. 22. Схема ручной сварки покрытым электродом:
1 – сварочная дуга; 2 – электрод; 3 - электрододержатель;
4 – сварочные провода; 5 – источник питания; 6 – свариваемая
деталь; 7 – сварочная ванна; 8 – сварной шов; 9 – шлаковая корка
Областью применения ручной дуговой сварки очень широка, это впервую очередь конструкции из различных видов стали и цветных сплавов с короткими криволинейными швами, всех типов сварных соединений и в любых пространственных положениях с толщиной соединяемых элементов от 1 до 175мм.
Достоинствами способа являются:
- его универсальность;
- возможность сварки в монтажных условиях;
- дешевизна оборудования и сварочных материалов.
Однако у этого способа есть и ряд недостатков:
- нестабильность процесса сварки, и как следствие низкое качество шва;
- низкая производительность;
- воздействие вредных факторов, таких как, излучения и аэрозоли, на здоровье сварщиков;
- самые высокие затраты на обучение персонала.
Типы сварных соединений, полученных ручной дуговой сварки, описывает ГОСТ 5264-80.
К параметрам режима сварки относятся: Iсв- сила сварочного тока, А; Uд- напряжение на дуге, В; род и полярность тока; dэ- диаметр и марка электрода.
Методика расчета параметров режима сварки для стыковых соединений из углеродистой стали с толщиной деталей меньше или равной 5мм.
dэ=S/2+1, мм, (2)
Iсв=(20+6 ·dэ) ·dэ, А, (3)
Uд=12+3·lд, В, (4)
lд=(dэ+2)/2, мм, (5)
Для конструкций с толщиной стенки > 5мм сначала рассчитывают количество проходов, при этом диаметр электрода для сварки корневого шва назначается на единицу меньше чем для заполняющего, а затем рассчитываются параметры режима сварки для каждого прохода.
Марка электрода выбирается исходя из механических свойств и химического состава основного материала. Обязательным условием является то, что механические свойства сварного шва должны быть не ниже свойств основного материала (таблица 1).
Таблица 1
Тип электрода | Механические свойства при нормальной температуре | Содержание в наплавленном металле, % | |||||
Металла шва или наплавленного металла | сварного соединения, выполненного электродами диаметром менее 3 мм | ||||||
Временное сопротивление разрыву dв кгс/мм2 | Относительное удлинение d5, % | Ударная вязкость aн кгс·м/см2 | Временное сопротивление разрыву dв кгс/мм2 | Угол загиба, град. | серы | фосфора | |
Не менее | Не более | ||||||
Э38 | |||||||
Э42 | 0,040 | 0,045 | |||||
Э46 | |||||||
Э50 | |||||||
Э42А | 0,030 | 0,035 | |||||
Э46А | |||||||
Э50А | |||||||
Э55 | |||||||
Э60 | |||||||
Э70 | |||||||
Э85 | |||||||
Э100 | |||||||
Э125 | |||||||
Э150 |
Электрод представляет собой стержень из сварочной проволоки диаметром от 1,6 до 12мм, и длиной от 150 до 450мм с нанесенным на него керамическим покрытием. Чаще всего используются электроды dэ=2…4мм и длиной 350-450мм, чем меньше dэ, тем меньше его длина (рис 23). Покрытие электрода обеспечивает:
- легкое зажигание и устойчивое горение дуги;
- получение металла шва требуемого химического состава;
- равномерное расплавление стержня и покрытия электрода;
- высокую производительность при небольших потерях электродного металла на угар и разбрызгивание;
- получение плотных беспористых швов, не склонных к образованию горячих трещин;
- легкую отделяемость шлаковой корки от поверхности шва;
- минимальную токсичность при сварке.
рис 23.
1 - стержень; 2 - участок перехода, 3 - покрытие; 4 - контактный торец без покрытия
Один из концов стержня освобожден от покрытия для его зажатия в электродо-держателе с обеспечением электрического контакта. Второй конец только слегка очищен для облегчения зажигания дуги посредством контакта с изделием. На контактный торец электрода может быть нанесен слой ионизирующего вещества, облегчающего возбуждение сварочной дуги, состав которого должен соответствовать предусмотренному стандартом или техническими условиями на электроды конкретной марки.
Покрытый электрод, несмотря на внешнюю конструкционную простоту, имеет достаточно сложную технологическую и металлургическую систему. Металлургические процессы, протекающие в нем при плавлении, сложны и отличаются от металлургических процессов, протекающих при выплавке стали. Они характеризуются своей кратковременностью, малым объемом реагирующих веществ, высокой температурой в зоне сварки и интенсивностью взаимодействия между металлом, шлаком и газом.
В дуге происходит не только расплавление, но и испарение железа и содержащихся в нем различных химических элементов. Активно протекают окислительные процессы и процессы поглощения расплавленным металлом азота, кислорода и водорода. В результате сложных окислительно-восстановительных реакций, протекающих как в газовой среде, так и на границе ее раздела с металлом, а также между металлом и шлаком, происходит легирование, окисление и раскисление металла, образующего сварной шов.
Химический состав шлакообразующей основы покрытия электродов определяет главным образом технологические свойства шлака. Соотношения компонентов покрытия выбирают таким образом, чтобы обеспечить достаточно низкую температуру плавления и низкую вязкость шлака, а также короткий интервал его затвердевания.
Все электроды по ГОСТ 9467-75 делятся на типы. Для углеродистых и низколегированных сталей предусмотрено 9 типов: Э38, Э42, Э50…Э60. Для сварки легированных конструкционных сталей – 5 типов: Э70, Э80, Э100…Э150. Для сварки легированных теплоустойчивых сталей тоже 9 типов: Э-09М, Э-09МХ. Э-10Х5МФ и др.
Тип электрода обозначается буквой “Э” и цифрой, указывающей гарантируемый предел прочности металла шва в кгс/мм2. Буква А в обозначении указывает, что металл шва, наплавленный этим электродом, имеет повышенные пластические свойства, например Э42А, Э50А. Такие электроды применяют для сварки более ответственных конструкций.
Каждому типу электрода соответствует несколько марок электродов. Например, типу Э42 соответствует ОМА-2, АНО-6, МЭЗ-04 и др. Марка электрода – это специфическое название, данное ему разработчиком, предприятием-производителем или держателем патента. Она, как правило характеризует стержень и покрытие. Покрытие электродов выполняет несколько функций (табл.2
Таблица 2.
Функции | Назначение компонентов | Компоненты |
1. Стабилизация дуги | Ионизирующие | Мел, мрамор, двуокись титана, поташ, окиси и соли щелочных и щелочно- земельных металлов |
2. Защита сварочной ванны | Газообразующие | Органические вещества: крахмал, декстрин, мука, древесные опилки, целлюлоза. Минеральные вещества: карбонаты кальция, бария и др. |
Шлакообразующие | Мел, мрамор, марганцевая руда, кварцевый песок, доломит, полевой шпат, титановый концентрат. | |
3. Улучшение структуры шва | Раскисляющие | Ферросилиций, ферромарганец, ферротитан, алюминий, графит и др. |
Феррованадий, феррохром, ферромолибден, закись никеля, окислы меди и др. | ||
4. Повышающие прочность обмазки | Связующие | Жидкое стекло (силикат калия и натрия), лаки (бакелитовый), целлюлоза, крахмал. |
Пластифицирующие | Минеральные вещества на основе глин: каолин, бентонит, целлюлоза, крахмал. |
По видам покрытия электроды подразделяются: с кислым покрытием – условное обозначение «А», с рутиловым – «Р», с целлюлозным – «Ц», с основным – «Б», и прочие – «П».
Кислые покрытия (АНО-1, СМ-5) содержат руды в виде окислов железа и марганца. При плавлении они выделяют кислород, для ослабления его действия в покрытия вводят раскислители. Однако наплавленный металл имеет малую вязкость и пластичность, и понижение содержания легирующих элементов. Электроды с кислым покрытием рекомендуются для сварки малоответственных конструкций.
Рутиловые покрытия (АНО-3, МР-3, ОЗС-4) имеют основным компонентом рутилдвуокись титана, он же является шлакообразующим элементом. Электроды с этим покрытием являются универсальными и позволяют вести сварку на любом роде тока по плохо очищенным поверхностям.
Целлюлозные покрытия (ВСЦ-1, ВСЦ-2, ОМА-2) содержат главным образом органические компоненты, но у них тонкий слой шлака, поэтому они рекомендуются для сварки небольших толщин.
Основные покрытия (УОНИ-13/45,УОНИ-13/55) составлены на основе плавикового шпата и мрамора. Отсутствие в составе этого покрытия оксидов железа позволяет широко легировать наплавленный металл и получить хорошие механические свойства сварного шва. Они применяются для сварки больших толщин. Чаще всего при РДС используют электроды с основным видом покрытия, но они требуют постоянного тока и обратной полярности.
Электроды классифицируются согласно ГОСТ 9466-75.
Условное обозначение электродов включает: тип, марку, диаметр, назначение, вид покрытия, его толщину, механические свойства наплавленного металла, полярность и пространственное положение.
Условное обозначение электродов представлено на (рис. 24)
|
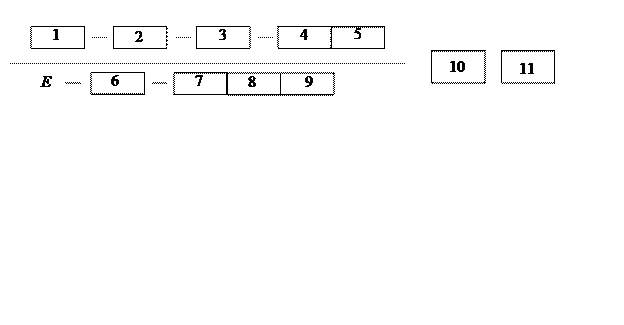
ПРИМЕРЫ УСЛОВНЫХ ОБОЗНАЧЕНИЙ:
Электроды типа Э42А по ГОСТ 9467-75, марки УОНИИ-13/45, диаметром 3,0 мм, для сварки углеродистых и низколегированных сталей У, с толстым покрытием Д, с установленной по ГОСТ 9467-75 группой индексов, указывающих характеристики наплавленного металла и металла шва, 43 2(5), с основным покрытием Б, для сварки во всех пространственных положениях 1 на постоянном токе обратной полярности 0:
- на этикетках или в маркировке коробок, пачек и ящиков с электродами;
Электроды УОНИИ-13/45-3,0 ГОСТ 9466-75 - в документации.
Электроды типа Э-09Х1МФ по ГОСТ 9467-75, марки ЦЛ-20, диаметром 4,0 мм, для сварки легированных теплоустойчивых сталей Т, с толстым покрытием Д, с установленной по ГОСТ 9467-75 группой индексов, указывающих характеристики наплавленного металла и металла шва, 27, с основным покрытием Б, для сварки во всех пространственных положениях 1 на постоянном токе обратной полярности 0:
- на этикетках или в маркировке коробок, пачек и ящиков с электродами;
Электроды ЦЛ-20-4,0 ГОСТ 9466-75 - в документации.
Электроды типа Э-10Х25Н13Г2Б по ГОСТ 10052-75, марки ЦЛ-9, диаметром 5,0 мм, для сварки высоколегированных сталей с особыми свойствами В, с толстым покрытием Д, с установленной по ГОСТ 10052-75 группой индексов, указывающих характеристики наплавленного металла и металла шва, 2075, с основным покрытием Б, для сварки в нижнем, горизонтальном на вертикальной плоскости и вертикальном снизу вверх положениях 3 на постоянном токе обратной полярности 0:
- на этикетках или в маркировке коробок, пачек и ящиков с электродами;
Электроды ЦЛ-9-5,0 ГОСТ 9466-76 - в документации.
Электроды типа Э-11Г3 по ГОСТ 10051-75, марки ОЗН-300У, диаметром 4,0 мм, для наплавки поверхностных слоев с особыми свойствами Н, с толстым покрытием Д, с установленной по ГОСТ 10051-75 группой индексов, указывающих характеристики наплавленного металла, 300/33-1, с основным покрытием Б, для наплавки в нижнем положении 4 на постоянном токе обратной полярности (0):
- на этикетках или в маркировке коробок, пачек и ящиков с электродами:
Электроды ОЗН-300У-4,0 ГОСТ 9466-75 - в документации.
Основным условием для получения качественного сварного соединения при ручной дуговой сваркой является устойчивость процесса сварки. Ее обеспечивают источники питания сварочной дуги. Ручная дуговая сварка может вестись как на постоянном, так и на переменном токе. Следовательно, при ручной дуговой сварки могут применяться источники переменного тока (трансформаторы) и постоянного тока (выпрямители, преобразователи, генераторы).
Но любой источник питания для ручной дуговой сварки должен обладать следующими требованиями:
- напряжение холостого хода должно быть достаточным для легкого возбуждения дуги. Максимально допустимое напряжение холостого хода для источников постоянного тока - 90В, переменного – 80В;
- напряжение на дуге должно быстро изменяться и восстанавливаться в зависимости от длины дуги. Время реагирования не должно превышать 0,05 с;
- ток короткого замыкания не должен превышать сварочный на 40-50%, при этом источник тока должен выдерживать длительные короткие замыкания;
- мощность источника тока должна быть достаточной для выполнения сварочных работ.
Для ручной дуговой сварки рекомендуется использовать источники питания с крутопадающей ВАХ (рис. 25)
Рис. 25. Падающая внешняя характеристика
источника сварочного тока
При выборе источника питания для ручной дуговой сварки остается предпочтение источникам постоянного тока, т.к. при их использовании дуга горит более стабильно, но они имеют большую массу, сложнее в обслуживании и дороже. В последнее время все большую популярность приобретают инверторные источники питания из-за малого веса, стабильности и широкого диапазона регулирования сварочного тока.
Дата добавления: 2016-11-04; просмотров: 14776;