Ремонт и изготовление деталей центробежных насосов
Ремонт валов. Во время эксплуатации валов возможны следующие дефекты: искривление вала; излом вала; выработка посадочных мест под подшипники качения, посадочных мест муфт, шестерен; шлицевых, шпоночных соединений; износ крепежной резьбы.
Искривление вала устраняют термическим, механическим или термомеханическими способами.
Термическую правку проводят на двух опорах. После выявления изогнутого участка вал поворачивают выпуклой стороной вверх и проводят интенсивный нагрев до 500 - 550°С, предварительно закрыв вал асбестовым листом с вырезом, равным по длине 0,15 диаметра вала и по окружности - 0,3 диаметра вала.
Во время нагрева вал еще больше прогибается в направлении первоначального изгиба, а при остывании выпрямляется. По окончании нагрева во избежание закалки вал закрывают асбестом.
После охлаждения вал проверяют индикатором, при необходимости правку повторяют. Продолжительность нагрева должна быть пропорциональна диаметру вала, твердости металла и стреле прогиба, так как излишний нагрев может привести к нежелательному прогибу. По окончании правки места, подвергшиеся нагреву, отжигают для устранения внутренних напряжений. Отжиг производится нагревом при температуре 350оС
Механическая правка заключается в механическом воздействии на вал (со стороны изгиба), и производят ее на токарном станке, прессе или специальном приспособлении. Суппортом токарного станка исправляют небольшие прогибы у валов диаметром 50 – 60 мм. Вал, зажатый в центрах токарного станка, поворачивают выпуклой стороной к суппорту, которым нажимают на него в противоположном прогибу направлении. При исправлении чеканкой вал устанавливают в центрах так, чтобы вогнутая сторона была обращена кверху, а к месту максимального прогиба подводят жесткую опору с подкладкой из дерева или меди. По вогнутой стороне производят чеканку молотком весом 1 – 2 кг. Вал допускается к монтажу, если после правки он имеет биение не более 0,03 мм. Изогнутые валы исправляют также термомеханическим способом, который заключается в нагреве вала до температуры 500 - 550°С и механическом воздействии на него со стороны, противоположной изгибу. Однако термомеханическая правка применяется редко, так как имеет много недостатков.
Сломанные валы сваривают, предварительно сцентровав их различными способами. Небольшие повреждения центровых отверстий исправляют зачисткой шабером, значительные повреждения - сверлением и раззенковкой резцом или центровым сверлом. Правильность установки вала проверяют индикатором.
При сопряжении вала с подшипником скольжения, который заливают при ремонте, шейку вала обрабатывают до ремонтного размера. Искажения шейки вала от геометрической формы, задиры, царапины устраняют обточкой и шлифованием.
При необходимости восстановления шейки вала под подшипники качения, муфты и другие сопрягаемые детали вал наплавляют (рис. 8.1) или металлизируют, а также проверяют на отсутствие кривизны и обтачивают до номинального размера. При большом износе поверхностей вала его протачивают и восстанавливают приваркой разрезных втулок (рис. 8.2).
|
|
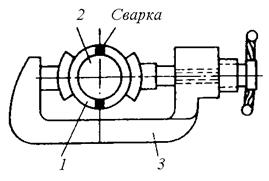
Резьбу, имеющую небольшие повреждения, исправляют на токарном станке. При большом износе ее стачивают, наваривают металл и нарезают новую резьбу.
При малом износе шпоночные пазы подправляют фрезой, увеличивая ширину шпонки, при значительном износе разработанные места заваривают и фрезеруют канавки заново. Иногда фрезеруют шпоночную канавку на новом месте под углом 90° по отношению к старой.
Заплечики и их галтели должны быть строго перпендикулярны к оси вала; их износ исправляется на токарном станке резцом; галтели восстанавливаются протачиванием или шлифованием. Круги для шлифования предварительно заправляют по радиусу галтелей.
Защитные втулки вала. В местах интенсивного износа валов часто устанавливают защитные втулки.
Конусность и волнистость втулок исправляют без демонтажа шлифованием на круглошлифовальном станке или на токарном станке с установкой на суппорте шлифовальной головки. Демонтированная втулка обрабатывается на оправке.
Изготовление защитных втулок требует соблюдения следующих основных требований:
- обеспечить точность размеров, внутренний диаметр посадочных мест - по 2 - му классу точности;
- внутренние и наружные цилиндрические поверхности должны быть концентричными (допускается биение 0,025мм);
- обеспечить чистоту обрабатываемых поверхностей; наружная поверхность и торец – по 7-му классу чистоты;
- торцы втулок должны быть строго перпендикулярны к оси (допускаемое биение 0,02 мм).
Втулки изготавливаются из старых печных труб или стального проката. При обработке втулки из проката заготовку устанавливают с самоцентрирующий патрон токарного станка, подрезают торец и намечают центровое отверстие. Затем проводят наружное обтачивание на 3 мм менее номинального для наплавки, сверление и расточку внутренней поверхности, наплавку твердого сплава на поверхности, термообработку для снятия напряжения при температуре 700 – 850оС. Далее проводится шлифовка наплавленной поверхности, окончательная расточка внутренней поверхности и нарезка резьбы.
Заготовки для втулок берутся с припуском на 5 – 6 мм, так как при наплавке происходит усадка сплава на 5 – 6 мм. Для облегчения шлифовки наплавленной поверхности втулка предварительно обрабатывается на токарном станке при температуре 400 – 500оС.
Уплотнительные кольца рабочих колес и корпуса. Основное требование при обработке уплотнительных колец - концентричность посадочных и уплотнительных поверхностей. Это достигается обработкой поверхностей с одной установки.
После наплавки кольца твердым сплавом оно обрабатывается на токарном станке, расточенное по заданному размеру кольцо напрессовывается на ступицу рабочего колеса. Окончательная обработка наружной поверхности кольца проводится после установки рабочего колеса на оправку или на вал насоса. Уплотнительные кольца обрабатываются по 2-му классу точности (шлифование после чернового и чистового обтачивания) и по 3-му (чистовое обтачивание с повышенной точностью после чернового обтачивания или шлифования после чернового обтачивания).
Ремонт корпуса насоса. Ремонт деталей корпуса производится в основном электросваркой.
Корпусы насосов из углеродистой стали, с толщиной стенки до 40 мм перед сваркой не подогреваются, при толщине более 40 мм применяется местный нагрев до температуры 250оС. Корпусы насосов из легированной стали (Х5М) перед заваркой подогреваются независимо от толщины стенки, а после заварки отжигаются. Для заварки обнаруженных раковин в корпусе создаются чашеобразная форма с отлогими стенками.
Если невозможно провести заварку с внутренней стороны, место раковины просверливают, вставляют пробку и обваривают снаружи.
Дефекты в чугунных корпусах заваривают специальными электродами для чугуна. Концы трещин перед заваркой сверлят. Обнаруженные свищи высверливают, в отверстиях нарезают резьбу и ввинчивают пробку.
Отремонтированные путем сварки корпусы опрессовываются на давление Рисп = 1,25 Рраб.
При испытании насосов с горизонтальным разъемом наружная сторона покрывается раствором мела; после его высыхания внутрь корпуса укладывается ветошь, обильно смоченные керосином. При наличии трещин или пор через 1 – 2 ч на наружной поверхности появятся пятна.
Незначительные риски, забоины, вмятины и прокорродированные места на привалочных поверхностях плоскости разъема устраняются зачисткой шабером. При значительных дефектах на поверхности плоскостей разъема последние протачиваются.
Износ посадочных мест корпуса устраняются проточкой на станке или на месте установки при помощи специального приспособления.
Привалочные поверхности внутренних корпусов двухкорпусных насосов шабрятся и проверяются по краске.
Рабочие колеса. Стальные рабочие колеса при износе ремонтируются с применением электросварки. Чугунные рабочие колеса при обнаружении недопустимого износа заменяются.
Рабочие колеса, как правило , поступают с машиностроительных заводов, но при необходимости они могут быть изготовлены в ремонтных цехах. Требования к точности обработки всех рабочих колес заключаются в следующем:
- допуски на обработку принимаются по 2 – 3–му классу точности, внутренние поверхности колеса должны быть чистыми, без наплывов и неровностей;
- соосность между расточкой под вал и пояском под уплотняющее кольцо должна быть в пределах 0,05 мм;
- разностенность боковых фланцев колеса допускается не более 0,5 мм;
- между осью канала на выходе и торцом ступицы со стороны всасывания размер должен быть выдержан по проектному допуску;
- необходимо, чтобы торцы ступицы были параллельны друг другу и перпендикулярны к оси расточки; допуск на параллельность принимается 0,04 мм;
- после ремонта или изготовления рабочие колеса подлежат статической балансировке; снятие металла при балансировке производится на боковых поверхностях фланцев, вблизи выходных рамок лопаток.
Ремонт подшипников скольжения. Подшипники скольжения ремонтируют в случае: искажения поверхности трения по сравнению с первоначальной геометрической формой; появления задирав и рисок на поверхности трения; частичного или полного выплавления, а также отслаивания баббита; образования трещин.
При ремонте неразъемных подшипников выпрессовывают втулки или растачивают их отверстия для запрессовки новой втулки. Изношенные втулки заменяются на новые.
Ремонт вкладышей подшипников скольжения заключается в наплавке отдельных дефектных мест или перезаливка вкладыша антифрикционным сплавом. При ослаблении вкладыша в корпусе подшипника определяют радиальный и боковые зазоры между подшипником и шейкой вала. Износ нижней половинки подшипника измеряют скобой, боковые зазоры - щупом, а верхний зазор - свинцовым оттиском или щупом. Путем промазки вкладыша керосином проверяют прилегание баббита к вкладышу, а с помощью краски - прилегание вкладыша к корпусу. В случае необходимости корпус шабрят. Качество шабрения определяют по числу пятен краски (на 1 см2 поверхности должно быть одно пятно). Осевой зазор между вкладышем и корпусом подшипника проверяют щупом. Суммарный осевой зазор должен быть не более 1 мм. Износ торцевых поверхностей исправляют наплавкой.
Дефекты вкладышей исправляют напайкой после выполнения следующих подготовительных операций. Сначала расчищают шабером дефектные места, удаляют все рыхлости и посторонние включения. Обезжиривают в 10%-ном растворе щелочи, нагретом до 60 - 80°С, и промывают горячей водой. Затем поверхности, подлежащие пайке, смачивают водным раствором хлорида цинка и подогревают вкладыш в печи или паяльной лампой до 150 - 180°С. Напайку ведут небольшими участками. Отдельные небольшие участки шлаковых включений зачищают до чистого металла и проверяют смежные с дефектами места. При наличии большого участка шлаковых включений подшипник перезаливают. Если во вкладыше не обнаружено нарушения сплошности заливки или отслаивания, ремонт ограничивается восстановлением зазора, уменьшением толщины прокладок между вкладышами и последующим шабрением.
При значительном износе вкладышей или при расслоении баббита их перезаливают. Перезаливка вкладышей состоит из следующих операций: промывки вкладыша, выплавке старого баббита, осмотра и ремонта вкладышей, обезжиривания, травления, лужения, подготовки баббита к заливке, заливки, расточки залитых вкладышей и пригонки вкладышей к валу.
Подшипники промывают 10%-ным водным раствором каустической соды, затем в горячей воде для очистки вкладышей от смазки и грязи.
Нагревают вкладыши в печах или паяльной лампой. Вкладыш, с которого удалены старый баббит и полуда, обезжиривают. Обезжиривают поверхности подшипников 10 - 15% раствором щелочи, подогретым до 80 - 90°С. Качество обезжиривания проверяют чистой водой. Если капля воды растекается, поверхность обезжирена хорошо.
После обезжиривания протравливают вкладыши. В результате травления удаляют оксиды, и на поверхности образуются мельчайшие неровности, что обеспечивает хорошее сцепление полуды и баббита с поверхностью вкладыша. Травление производят 50%-ным водным раствором соляной кислоты в течение 10 мин, после этого вкладыш промывают 10%-ным раствором щелочи и горячей воды. Затем вкладыш вторично протравливают насыщенным раствором хлорида цинка, добавляя к нему хлорид аммония (из расчета 50 г на 1 л раствора). При протравливании подшипник должен быть прогрет до 180 - 220°С.
Лужение производят чистым оловом (для баббита Б-83) или сплавом “третником” (2 части свинца и 1 часть олова). Можно применять припой ПОСС4-6. Подшипник погружают в припой или протирают палочкой припоя. Затем наносят полуду. Правильно нанесенная полуда имеет тускло-серебристый цвет. Если полуда собирается в капли, поверхность подшипника подготовлена плохо. В этом случае подшипник покрывают флюсом (хлоридом цинка), нагревают до 150 -180°С и опускают в расплавленную полуду на 5 мин.
Поверхности, не подлежащие полуде, покрывают изолирующим раствором (на 1 л воды 0,5 г жидкого стекла или столярного клея и
800 г мела).
Подшипники большого размера лудят методом протирки. Для этого подшипник нагревают до 60 - 70°С, смачивают раствором соляной кислоты, протирают и промывают водой. Затем подшипник смачивают травленой кислотой, посыпают порошком нашатыря (хлоридом аммония), нагревают до 240 - 270°С и палочкой припоя наносят тонкий слой полуды, которая должна равномерно покрывать поверхность и не стекать с нее. Луженую поверхность протирают паклей с порошком нашатыря. После лужения незамедлительно заливают баббитом для того, чтобы предотвратить появление на слое полуды оксидных пленок.
Перед заливкой баббит нагревают до 375 - 400°С в зависимости от его марки. Важно не допустить перегрева баббита, так как в этом случае сплав дает крупнозернистую структуру и обладает плохими механическими свойствами. Вкладыш до заливки нагревают до 200 - 250°С.
Баббит в подшипниках заливают вручную или центробежным способом. При заливке вручную собранные вкладыши устанавливают на чугунную плиту, внутрь вставляют стержень. Чтобы стержень после заливки легче вынимался, его покрывают графитом.
При центробежном способе луженый вкладыш устанавливают в специальное приспособление и приводят во вращение. После этого заливают расплавленный баббит в подшипник, стараясь распределять его ровным слоем по поверхности.
После остывания вкладыш снимают со станка и проверяют качество заливки. Поверхность баббита должна быть гладкой и иметь серебристый цвет. Желтый цвет или зернистость указывают на перегрев баббита. В этом случае подшипник подлежит переливке. Неглубокие раковины ремонтируют путем наплавки.
Плотность сцепления баббита с поверхностью вкладыша проверяют отстукиванием молотком. Для расточки залитого вкладыша с каждой стороны разъема укладывают прокладки толщиной, равной зазору между валом и верхним вкладышем.
После расточки пришабривают вкладыши по валу. На шейку вала устанавливают подшипник, затягивают и проворачивают. Вскрыв подшипник, шабрят места, покрытые краской, до получения равномерно распределенных отпечатков краски на дуге под углом 60 - 80° (до пяти пятен на 1 см2 поверхности).
На боковых поверхностях нижнего вкладыша делают развалы. По концам оставляют узкие полоски длиной 10 - 15 мм для прилегания вкладыша к валу.
Верхний вкладыш шабрят так, чтобы одно пятно приходилось на 1 см2. Зазоры между верхним вкладышем и валом проверяют щупом или оттисками свинцовых пластинок. Эти зазоры в зависимости от диаметра вала должны составлять:
Диаметр вала, мм | 30 - 80 | 80 - 120 | 120 - 180 | 180 - 250 |
Зазор, мм | 0,1 - 0,16 | 0,12 - 0,20 | 0,16 - 0,28 | 0,20 - 0,40 |
Боковой зазор должен быть равен половине верхнего. Радиус галтели вала и радиус закругления по торцам вкладышей проверяют шаблонами. В зависимости от диаметра вала они должны соответствовать следующему:
Диаметр вала, мм | ||||||||
Радиус закругления вала, мм | 1,5 | |||||||
Радиус вкладыша, мм | 2,5 |
Ремонт подшипников качения.При обнаружении дефектов подшипники качения заменяют на новые.
Для выяснения пригодности подшипников к работе выявляют следующие дефекты: раковины и выщербленные места на шариках и роликах; разрывы на сепараторах, степень износа гнезд сепараторов; раковины, трещины, шелушения на беговых роликах.
Проверяют также размеры осевого и радиального зазоров в подшипниках.
Предельные радиальные зазоры в подшипниках приведены ниже:
Диаметр вала, мм | ![]() | 50 - 100 | 100 - 200 | > 200 |
Зазор, мм | 0,1 | 0,2 | 0,3 | 0,4 |
Предельные осевые зазоры в подшипниках приведены в табл. 8.1.
Если при осмотре будет установлено, что подшипники находятся в хорошем состоянии, ограничиваются их чисткой и промывкой.
Иногда наблюдается провертывание внутренней обоймы подшипника на валу. В этом случае вал наплавляют или металлизируют, а затем проворачивают. Не рекомендуется накернивание посадочной поверхности вала под подшипник.
Таблица 8.1. предельные осевые зазоры в подшипниках
Диаметр вала, мм | Зазоры, мм | |
легкая серия | легкая широкая, средняя и средняя широкая серии | |
![]() | 0,03 – 0,1 | 0,04 – 0,11 |
30 - 50 | 0,04 - 0,11 | 0,05 - 0,13 |
50 - 80 | 0,05 - 0,13 | 0,06 - 0,15 |
80-120 | 0,05 – 0,15 | 0,07 – 0,18 |
Заусенцы и забоины на посадочных поверхностях вала удаляют “бархатным” напильником, шабером и наждачным полотном.
Долговечность подшипника в значительной степени зависит от посадки обоймы и наличия смазки. Внутреннюю обойму подшипника устанавливают на вал на плотную посадку, чтобы обойма не проворачивалась при вращении вала. Она должна упираться в буртик вала.
Напрессовывают подшипники вручную с помощью выколоток, оправок и специальных приспособлений, наиболее часто применяют медную выколотку и молоток.
Во избежание перекосов удары по внутреннему кольцу наносят попеременно с разных сторон. Перед установкой новые подшипники промывают в бензине или специальной эмульсии-растворителе для удаления предохранительной смазки.
Для посадки на вал подшипников большого диаметра их нагревают в минеральном масле до 80 - 90°С, что значительно облегчает процесс сборки.
В случае слабины подшипника в корпусе подшипникового узла наплавляют гнездо или завтуливают его с последующей расточкой.
В отдельных случаях предусмотрены съемные втулки по наружной обойме подшипника, которые в случае дефекта можно заменить. Для разборки подшипниковых узлов и съема подшипников используют съемники разных конструкций (рис. 8.3).
|
Ремонт соединительных муфт. Для соединения соосных валов применяют муфты различных конструкций: зубчатые, пальцевые, кулачковые, крестовые, тарельчатые, продольно-свертные (рис. 8.4).
Зубчатые муфты применяют для соединения насосов с электродвигателями. При их использовании допускается небольшое смещение одного вала относительно другого.
Пальцевые муфты применяют для компенсации возникающих при эксплуатации радиальных и осевых смещений валов, а кулачковые - для компенсации осевых смещений.
Тарельчатые муфты используют при передаче больших мощностей. Для этих муфт требуется тщательная центровка агрегатов и строгая перпендикулярность расположения торцов полумуфт относительно вала. Продольно-свертные муфты применяют для жесткого соединения валов.
Несмотря на различие муфт, для большинства из них используют общие методы ремонта. Чаще всего муфты насаживают на вал по напряженной или плотной посадке.
Ступицу муфты, имеющую износ по внутреннему диаметру, наваривают (или завтуливают) и протачивают.
Радиальное биение проверяют индикатором и в случае необходимости устраняют проточкой. Допустимое биение должно быть не больше 0,02 - 0,03 мм.
При разработке шпоночный паз прострагивают. При увеличении его ширины на 10% от минимальной шпоночный паз заваривают. Затем прострагивают или изготавливают новый шпоночный паз под углом 90° относительно старого.
В зубчатых муфтах (см. рис. 8.4, а) подвержены износу зубья, поэтому при ремонте проверяют зазоры в зацеплении и степень их износа. При отсутствии запасной муфты зубья наваривают и обрабатывают на станке. Нельзя заменять отдельно ступицу или полумуфту, так как при этом вся муфта быстро выйдет из строя. При сборке муфты между фланцами устанавливают прокладку из плотной бумаги.
При эксплуатации пальцевых муфт (см. рис. 8.4, б) возможны следующие дефекты: износ неметаллических колец, пальцев, посадочных мест установки пальцев. При ремонте дефектные пальцы и втулки заменяют. Посадочные места под пальцы, развертывают под больший размер.
У кулачковых муфт (см. рис. 8.4, в) быстро изнашиваются пакеты (сухари), которые при ремонте заменяют новыми, изготавливаемыми из резины или прорезиненной ленты. При длительной эксплуатации изнашиваются кулачки; по краям кулачков образуются заусенцы. Кулачки ремонтируют наплавкой и механической обработкой.
|
Крестовые муфты (см. рис. 8.4, г) ремонтируют так же, как и кулачковые, кроме этого заменяют неметаллическую вставку.
В тарельчатых муфтах (см. рис. 8.4, д) возможны срез болтов или их изгиб, смятие резьбового соединения, разработка отверстий под болты и посадочных отверстий в дисках. В этом случае проводят развертку отверстий под болты большего диаметра или на болты устанавливают переходные втулки.
У продольно-свертных муфт при эксплуатации увеличивается посадочное отверстие, разрабатывается шпоночный паз и деформируется шпонка. Муфты со значительным износом заменяют новыми.
Уравновешивающий диск контролируют на наличие, задирав, забоин, наклепа и износа сопрягаемой с валом поверхности. Зазор с валом должен быть в пределах 0,3 – 0,7 мм, площадь прилегания поверхности – не менее 70;, шероховатость поверхности – 0,3 мм.
Упорный диск не должен иметь повреждений рабочей поверхности; допускается разнотолщинность до 0,01 мм, шероховатость - до 0,04 мм. Посадка диска должна быть с натягом до 0,01 мм или с зазором до 0,01 мм. При ослаблении посадки диска его следует заменить.
Стопорное кольцо контролируют визуально и по краске. Местные дефекты (забоины, задиры), не нарушающие размеров посадки, должны быть устранены. Площадь прилегания должна быть более 30%, шероховатость – до 0,3 мм.
Уравновешивающее седло и стопорную втулку визуально проверяют по краске на степень прилегания торцовых поверхностей; она должна быть не менее 80%. Забоины, задиры поверхностей должны быть зачищены. Контролируют наружный диаметр седла и соответствие его установленному допуску.
Уравновешивающую втулку контролируют на наличие, задирав и забоин поверхностей, износа наружного и внутреннего диаметров. Зазор на уравновешивающем поршне должен быть в пределах 0,3 – 0,7 мм.
Дистанционную и стопорную втулки контролируют по размерам внутреннего и наружного диаметров. Задиры, забоины в пределах допускаемых размеров детали должны быть устранены. Непараллельность торцевых поверхностей должна составлять до 0,01 мм, площадь их прилегания – не менее 80%.
Уплотнительное кольцо проверяют на износ рабочих поверхностей, который должен быть не более 0,4 мм. Перемещая кольцо в корпусе, проверяют, не произошло ли ослабление его посадки. Местные дефекты (задиры, забоины) не должны занимать площадь более 15% рабочей поверхности, а шероховатость поверхности допускается до 0,3 мм.
Дистанционное кольцо проверяют на наличие наклепа торцевых поверхностей; по краске контролируют площадь прилегания; при уменьшении ее до 0,3% кольцо следует заменить.
Сборка.На сборку подают детали, прошедшие дефектовку и ремонт, соответствующие техническим требованиям и полностью готовые к сборке. Сборку корпуса (на примере насоса типа КВН) выполняют в определенной последовательности. Укладывают вал наоса, на нем устанавливают первое рабочее колесо, дистанционную и стопорную втулки и другие детали. При сборке применяют только деревянный молоток. Вал насоса смазывают для облегчения последующей сборки. При сборке следует замерять зазоры между рабочим колесом и дистанционной втулкой и результаты замера вносить в формуляр. Необходимый зазор можно регулировать установкой прокладок между рабочим колесом и дистанционной втулкой.
На разъем корпуса с крышкой наносят уплотняющую мастику и устанавливают диафрагму. Затем на вал монтируют уравновешивающий поршень, распорное кольцо, уравновешивающий диск и второе распорное кольцо, далее надевают крышку, на плоскость разъема ее с диафрагмой наносят уплотняющую мастику, слегка затягивают крепежные гайки и проверяют правильность установки крышек.
При перемещении вала в сторону всасывания уравновешивающий диск должен плотно прилегать к седлу. На вал надевают защитную втулку и закручивают муфтовую гайку. Зазор между уравновешивающим диском и седлом должен быть не более 0,05 – 0,1 мм.
Установив верхнюю половину опорного подшипника, измеряют зазоры в нем; они должны составлять вверху 0,10 – 0,16 мм, по бокам 0,03 – 0,08 мм. Результаты заносят в формуляр./
Установив крышку корпуса подшипника, проверяют натяг подшипника, который должен быть в пределах 0,01 – 0,03 мм. Аналогичные операции выполняют в опорном подшипнике со стороны нагнетания.
После сборки упорного подшипника устанавливают две индикаторные головки перпендикулярно плоскости упорного подшипника на концах одного диаметра и, вращая ротор, замеряют биение упорного подшипника; оно не должно превышать 0,02 мм.
С помощью индикатора проверяют осевой разбег ротора в упорном подшипнике путем перемещения ротора до упора. Разбег должен оставлять 0,2 – 0,3 мм. Результаты всех измерений заносят в формуляр.
В сальниковую камеру вставляют набивочные кольца так, чтобы разрез каждого последующего кольца был смещен на 90о по отношению к разрезу предыдущего. Число набивочных колец должно быть таким, чтобы набивка не доходила до наружного торца корпуса сальника на 5 мм.
Набивка прижимается при медленном затягивании гаек. Окончательную подтяжку сальника выполняют после обкатки насоса.
Таблица . Характерные неисправности в работе центробежных насосов и способы их устранения
Неисправности | Причина неисправностей | Способы устранения |
Прекращение подачи жидкости после пуска насоса | Недостаточное заполнение насоса жидкостью | Повторить заливку |
Неплотности приемного клапана | Осмотреть клапан и устранить неисправности | |
Неплотность во всасывающем трубопроводе или сальниках насоса (при этом вакуумметр показывает нуль) | Осмотреть трубопровод и сальники и устранить непотности | |
Неправильное направление вращения или недостаточное число оборотов | Проверит двигатель | |
Большая высота всасывания | Проверить по вакуумметру и осмотреть всасывающий трубопровод | |
Наличие воздуха или газа в корпусе насоса | Вновь залить насос | |
Закупорка трубки гидравлического уплотнения сальника | Осмотреть и прочистить трубку | |
Засорение всасывающего фильтра (сетки) | Осмотреть и очистить фильтр | |
Потребление насосом большой мощности при его пуске | Открыта задвижка на напорном трубопроводе | Закрыть задвижку на время пуска |
Засорилась трубка, отводящая жидкость от разгрузочного устройства | Осмотреть и очистить трубку | |
Неправильно установлены рабочие колеса или разгрузочный диск | Проверить и устранить неправильную сборку | |
Заедание уплотнительных колец | Проверить вращение ротора от руки; если ротор вращается туго, устранить заедание | |
Перегорел предохранитель одной из фаз электродвигателя трехфазного тока | Осмотреть предохранитель и заменить новым | |
Уменьшение подачи насоса в процессе работы | Уменьшение числа оборотов | Проверить двигатель и устранить обнаруженные неисправности |
Просачивание воздуха во всасывающую трубу или в корпус насоса через сальник | Проверить трубопровод, подтянуть или сменить набивку сальника | |
Неисправности | Причина неисправностей | Способы устранения |
Уменьшение подачи насоса в процессе работы | Увеличение сопротивлений в напорном трубопроводе | Проверить все задвижки и места возможных засорений трубопровода и очистить их |
Увеличение высоты всасывания | Проверить по вакууммометру, а также осмотреть фильтр и всасывающую трубу | |
Засорение рабочего колеса | Осмотреть и прочистить колесо | |
Механические повреждения: износ уплотняющих колец и повреждение рабочего колеса | Сменит поврежденные детали | |
Уменьшение напора насоса в процессе работы | Уменьшение числа оборотов | Проверить двигатель и при обнаружении неисправностей устранить |
Наличие воздуха в жидкости | Проверить всасывающую трубу, подтянуть или сменить набивку сальника | |
Повреждение напорного трубопровода | Прикрыть задвижку напорного трубопровода и осмотреть его | |
Механические повреждения: износ уплотняющих колец и повреждение рабочего колеса | Сменит поврежденные детали | |
Перегрузка двигателя | Число оборотов выше расчетного | Проверить двигатель и при обнаружении неисправностей устранить |
Подача насоса выше допустимой (напор меньше расчетного) | Прикрыть задвижку на напорном трубопроводе | |
Механические повреждения двигателя или насоса | Проверить двигатель и насос, устранить обнаруженные неисправности | |
Вибрация и шум в насосе | Неправильная установка агрегата | Проверить агрегат |
Частичное засорение рабочего колеса | Осмотреть и прочистить насос | |
Механические повреждения: прогиб вала, заедание вращающихся частей и износ подшипников | Сменить поврежденные детали | |
Ослабление креплений на напорной и всасывающих трубах | Подтянуть крепления | |
Чрезмерная высота всасывания | Остановить насос и принять меры к уменьшению вакуумметрической высоты всасывания | |
Неисправности | Причина неисправностей | Способы устранения |
Вибрация и шум в насосе | Явление кавитации | Не изменяя числа оборотов, уменьшить подачу прикрытием (дросселированием) напорной задвижки, уменьшить подачу снижением числа оборотов двигателя, уменьшить сопротивления во всасывающем трубопроводе и герметизировать его соединения и увеличить подпор (при отрицательной высоте всасывания – подпоре» |
Дата добавления: 2016-06-29; просмотров: 7759;