Процессы, завершающие получение
Нитратов целлюлозы
На стадии стабилизации окончательно формируются характеристики нитратов целлюлозы. Однако после стабилизации нитраты целлюлозы имеют значительный разброс физико-химических показателей (содержания азота, вязкости, дисперсности и др.). При современном техническом уровне изготовить партию нитратов целлюлозы, однородную по всему объему, практически невозможно. Различия в физико-химических показателях отдельных порций нитратов целлюлозы при их изготовлении обусловлены нестабильностью как исходного сырья, так и технологического процесса. В результате нитраты целлюлозы после фазы нитрации неоднородны по содержанию азота, после предварительной стабилизации – по вязкости и растворимости, после измельчения – по дисперсности и т.д. Поэтому в производстве после окончательной стабилизации возникает необходимость смешения отдельных порций (частных или малых партий) нитратов целлюлозы в одну общую партию.
Общие партии должны отвечать по своим физико-химическим показателям требованиям нормативной документации. При этом следует учитывать, что чем больше объем общей партии нитратов целлюлозы и она имеет большую физико-химическую однородность, тем легче обеспечить, например, требуемые физико-химические и баллистические характеристики порохов.
Частные партии в производстве смесевых пироксилинов смешиваются не только в целях их усреднения, но и обеспечения в определенных соотношениях двух разных пироксилинов: №1 с содержанием азота не менее 13,09 % и растворимостью 4 – 10 % и №2 с содержанием азота 11,76 – 12,35 % и растворимостью 96 – 99 %, для получения партий смесевого пироксилина соответствующих марок.
Перемешивание нитратов целлюлозы ведется в водной среде с массовой долей около 10 %. Поэтому по окончании перемешивания и физико-химического анализа смесевую партию подают на водоотжим. Перед водоотжимом водная суспензия нитратов целлюлозы подогревается до 55 – 70 °С, что благоприятно сказывается на отделении воды в результате уменьшения ее поверхностного натяжения.
В производстве порохов нитраты целлюлозы хорошо пластифицируются под действием растворителя при содержании в них 2 – 4 % воды. При существующих механических способах отделения воды от нитратцеллюлозной взвеси (центрифугирования, прессования и фильтрации) достигнуть требуемой влажности невозможно. Необходимая влажность достигается сушкой, однако процесс сушки длителен и опасен. Оптимальным был признан способ удаления воды из нитратов целлюлозы, основанный на вытеснении (замещении) ее спиртом, – обезвоживание.
Перед обезвоживанием нитратцеллюлозную взвесь с массовой долей 6 – 14 % отжимают от воды до влажности 28 – 32 %. Такая влажность обусловлена требованием минимального разбавления отработанного спирта и минимальной его подачей на фазу рекуперации.
При разделении взвеси прессованием на прессах до влажности нитратов целлюлозы 28 – 32 % происходит их уплотнение до 800 – 900 кг/м3. Такая плотность усложняет дальнейшую их переработку. При вакуумной фильтрации достигается средняя плотность 600 – 650 кг/м3, при этом влажность нитратов целлюлозы составляет 37 – 40 %. Такая влажность также неблагоприятно влияет на дальнейшую переработку. Поэтому для разделения нитратцеллюлозной взвеси используется метод центрифугирования как наиболее рациональный. Этот метод обеспечивает получение влажности нитратов целлюлозы 28 – 32 % при плотности 500 – 600 кг/м3.
На большинстве заводов водоотжим всех марок нитратов целлюлозы вписывается в технологический поток их производства. Обезвоживание пироксилинов спиртом ведут в технологическом потоке их переработки (в производстве пороха).
4 Технологическая схема
производства нитратов целлюлозы
Проведенный в предыдущем разделе анализ основных явлений и процессов, протекающих при получении нитратов целлюлозы с использованием нитрующей системы HNO3 – H2SO4 – H2O, позволяет сделать вывод, что производство нитратов целлюлозы состоит из следующих технологических фаз:
– подготовка целлюлозы;
– приготовление нитрующей рабочей кислотной смеси (РКС);
– нитрация целлюлозы;
– отделение полученных нитратов целлюлозы от отработанной кислотной смеси (ОКС);
– рекуперация адсорбированной нитратами целлюлозы отработанной кислотной смеси;
– предварительная стабилизация;
– измельчение нитратов целлюлозы (для высокоазотных нитратов);
– окончательная стабилизация;
– формирование общих партий;
– водоотжим.
Кроме основных технологических фаз, с целью уменьшения потерь сырья и охраны окружающей среды производство нитратов целлюлозы всегда включает вспомогательные фазы, к которым относятся:
– регенерация отработанной кислотной смеси;
– улавливание нитрозных газов с получением слабой азотной кислоты;
– санитарная очистка отработанных газов;
– нейтрализация и очистка сточных вод.
![]() |
Принципиальная технологическая схема производства нитратов целлюлозы, которая устанавливает взаимосвязь между фазами, представлена на рис.8.
|
Технологический процесс производства нитратов целлюлозы можно описать следующим образом.
Исходная целлюлоза поступает на фазу подготовки, где производится ее рыхление (для волокнистой целлюлозы марок ХЦ и ЦА) или резка (для бумажного полотна марки РБ) и сушка. Разрыхленная (измельченная) и высушенная целлюлоза подается на фазу нитрации.
Предварительно готовится рабочая кислотная смесь, которая с фазы приготовления также подается на фазу нитрации.
После смешения целлюлозы с рабочей кислотной смесью и завершения процесса нитрования (реакции этерификации) полученные нитраты целлюлозы отделяются от отработанной кислотной смеси. Часть отработанной кислотной смеси подается на фазу приготовления рабочей кислотной смеси, где происходит ее корректировка свежими азотной и серной кислотами и возврат в технологический цикл. Избыток отработанной кислотной смеси поступает на фазу регенерации кислот. Нитраты целлюлозы после отделения отработанной кислотной смеси, содержащие адсорбированные кислоты, подаются на фазу рекуперации этих кислот. По завершению рекуперации адсорбированных кислот образовавшаяся водная взвесь нитратов целлюлозы поступает на фазу предварительной стабилизации.
На фазе предварительной стабилизации разрушаются сульфоэфиры и другие побочные продукты, образовавшиеся при нитрации целлюлозы, частично нейтрализуются свободные кислоты. На этой фазе может происходить также деполимеризация нитратов целлюлозы и снижение их вязкости. Для полного удаления свободных кислот (преимущественно серной) нитраты целлюлозы измельчаются (высокоазотные) и подаются на фазу окончательной стабилизации.
В процессе окончательной стабилизации нитратов целлюлозы путем щелочных и нейтральных промывок полностью нейтрализуются кислоты и удаляются водорастворимые нестойкие примеси, образовавшиеся при измельчении или автоклавной обработке. Одновременно с этим при необходимости нитраты целлюлозы доводятся до требуемой вязкости и степени полимеризации.
Стабилизированные нитраты целлюлозы в виде водной взвеси поступают на фазу формирования общих партий, где подобранные по результатам анализа порции (частные партии) нитратов целлюлозы смешиваются в общую партию с требуемыми характеристиками.
Полученная общая партия нитратов целлюлозы подается на водоотжим и готовые нитраты целлюлозы с влажностью 28 – 32 % направляются в пороховое производство или по другому назначению.
Технологические процессы на каждой из рассмотренных фаз в зависимости от вида и марки получаемых нитратов целлюлозы могут иметь разные режимы и свои особенности, включая аппаратурное оформление. Подробные сведения о производстве конкретных видов нитратов целлюлозы приводятся в следующих разделах. Вспомогательные фазы, как правило, являются общими для производства всех видов нитратов целлюлозы.
На вспомогательных фазах проводятся регенерация кислот, входящих в состав отработанной кислотной смеси, утилизация нитрозных газов с получением азотной кислоты, санитарная очистка отработанных газов, а также нейтрализация и очистка сточных вод, образующихся в производстве. Технологические процессы на этих фазах также сопровождаются сложными химическими и физико-химическими явлениями (см. раздел 7).
5 Производство смесевого
пироксилина
Смесевой пироксилин состоит из пироксилина №1 и пироксилина №2, которые отличаются физико-химичес-кими свойствами. Поэтому производство смесевого пироксилина до фазы формирования общих партий, по существу, включает две параллельные технологические линии. После фазы окончательной стабилизации они объединяются в одну (рис. 9).
|
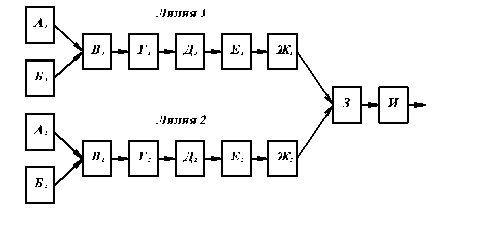
5.1. Фаза подготовки целлюлозы
Целлюлоза, поступающая на фазу нитрации, должна быть разрыхленной и сухой, что улучшает ее впитывающие свойства и соответственно равномерность нитрации. Поэтому на фазе подготовки целлюлозы выполняется комплекс операций: разрыхление (для целлюлозы марок ХЦ и ЦА), резка (для марки РБ), сушка и транспортирование целлюлозы на фазу нитрации. Эти операции в настоящее время выполняются с использованием кипоразрыхлителя или резательного станка и пневмотранспортного сушильного агрегата. Последний позволяет совмещать сушку целлюлозы с ее транспортированием на фазу нитрации.
Кипоразрыхлитель представляет собой ленточный конвейер с системой трех валков, на поверхности которых имеются зубья. Два валка служат для рыхления подаваемой с помощью конвейера кипы, третий сбрасывает разрыхленную целлюлозу в эжекторную воронку пневмотранспортного агрегата.
Станок резки состоит из узла раската рулонов, узлов продольной и поперечной резки, механизма укладки полотна после продольной резки и подачи его на поперечную резку. Резка полотна осуществляется дисковыми ножами специальной конструкции.
Сушильной камерой пневмотранспортного сушильного агрегата является труба длиной 120 – 150 м, по которой целлюлоза подается нагретым воздухом с фазы подготовки целлюлозы на фазу нитрации. Ввод целлюлозы в трубу осуществляется с помощью эжекторной (конфузорно-диффузорной) воронки.
Эжекторная воронка представляет собой загрузочный конус (собственно воронка), соединенный с трубой, через которую проходит воздух в направлении, перпендикулярном оси конуса. Входная часть трубы сужается, образуя сопло – конфузор, выходная – расширяется в виде диффузора. При движении воздуха через трубу в нижней части загрузочного конуса создается пониженное давление (разрежение), что позволяет воздуху захватывать и транспортировать целлюлозу.
![]() |
Технологическая схема фазы подготовки целлюлозы приведена на рис. 10.
|
Подготовка целлюлозы осуществляется следующим образом. Кипы волокнистой целлюлозы марки ЦА и ХЦ после снятия упаковки подаются на кипоразрыхлитель 1. Разрыхляясь до насыпной плотности 0,034 – 0,035 т/м3, целлюлоза через воронку 2 поступает в пневмотранспортную трубу 4.
При использовании целлюлозы марки РБ рулоны бумажного полотна устанавливаются на резательный станок 3. Образующаяся после резки бумажная сечка также через эжекторную воронку поступает в пневмотранспортную трубу.
При транспортировании к бункеру-дозатору 5, расположенному на фазе нитрации, целлюлоза сушится до
влажности 4 – 5 %. Воздух на сушку забирается через фильтр 6 и подается вентилятором 7. Нагрев воздуха до 55 – 120 ºС осуществляется в калориферной установке 8. Входя в бункер-дозатор 5, воздух теряет скорость, и целлюлоза оседает. Отработанный воздух, содержащий до 1,5 % (от транспортируемой целлюлозы) пыли, проходит через пылевую камеру 9, где на сетчатой поверхности оседает ее основная масса. Мелкие фракции пыли целлюлозы улавливаются в циклоне 10, из которого воздух отсасывается с помощью хвостового вентилятора 11.
Пыль целлюлозы, образующаяся при рыхлении целлюлозы, из кипоразрыхлителя, отсасываемая вентилятором 13, улавливается в циклоне 12.
Подготовленная целлюлоза из бункера-дозатора 5 дозируется непосредственно в нитраторы или выгружается в тележки-тушильники (при ручной загрузке нитраторов).
Типовой технологический режим подготовки целлюлозы:
– расход воздуха – температура воздуха: | – 8500 м3/ч; |
– при входе в сушилку – на выходе из сушилки | – 85 ºС, – 45 ºС; |
– влажность целлюлозы: – на входе в сушилку – на выходе из сушилки | – 8 – 10 %, – 4 – 5 %; |
– скорость воздуха | – 15 – 16 м/с; |
– концентрация целлюлозы в пневмотрубе | – 0,12 – 0,15 кг/м3. |
Дата добавления: 2016-06-15; просмотров: 2571;