Машины и оборудование для приготовления кормов и кормовых смесей.
1.Все существующие корма составляют три основные группы: растительного происхождения, животного происхождения и промышленного производства. Они, в свою очередь, делятся на подгруппы: грубые, сочные, концентрированные, рыбные, мясные, молочные, комбинированные корма, кормовые добавки и пищевые отходы. В таблице 5.1 дана классификация кормов по видам и назначению.
Таблица 5.1- Классификация кормов по видам и назначению
Группа | Подгруппа | Наименование |
Растительного происхождения | Грубые | Сено Солома Веточный корм |
Сочные | Зеленые корма Силос (комбисилос) Сенаж Плоды бахчевых культур Корнеклубнеплоды Жом Водоросли | |
Концентрирован-ные | Зерно злаковых и бобовых культур Патока кормовая (меласса) Дрожжи Травяная мука Жом сухой | |
Животного происхождения | Рыбные | Отходы переработки рыбы Рыбная мука |
Мясные | Мясокостная мука | |
Молочные | Обрат и сыворотка | |
Промышлен-ного происхождения | Комбинирован-ные корма | Комбикорма |
Кормовые добавки | Минеральные (соли, макро и микро-элементы) Синтетические азотосодержещие (мочевина и др.) Премиксы (витаминные, минеральные и т.д.) | |
Пищевые отходы | От сети общественного или индивидуального питания и др. |
2.Абсолютные размеры или крупность частиц измельченного корма обусловлены зоотехническими требованиями. Однако для энергетической оценки процесса измельчения этого недостаточно и требуется знать степень измельчения. Степень измельчения определяется отношением средних размеров частиц исходного материала к среднему размеру частиц продукта измельчения.
Энергоемкость процесса измельчения зависит от выбора способа воздействия рабочих органов машины на материал.
Теория измельчения рассматривает два комплекса основных вопросов:
- изучает функциональные зависимости между затратой энергии (работы) на разрушение материала и степенью измельчения, что дает возможность выявить эффективность рабочего процесса измельчения в зависимости от принятой технологии, применяемых типов машин и выбранных режимов их работы.
- изучает закономерности в распределении частиц по крупности с целью отыскания наиболее простых и в то же время достаточно надежных методов определения средних размеров частиц, величины их удельной поверхности и численных значений степени измельчения.
В данном курсе любой процесс производственного разрушения материала принято называть процессом измельчения. В этом смысле под термином "дробление" следует понимать более грубое измельчение, осуществляемое, как правило, ударом.
Измельчение - есть процесс разделения твердого тела на частицы механическим путем, т. е. путем приложения внешних сил, превосходящих силы молекулярного сцепления. Образование новых поверхностей составляет основное содержание всякого процесса измельчения. Следовательно, измельчение можно рассматривать как процесс производства (приращения) новых поверхностей частиц корма.
Для сравнения развитости поверхности частиц сыпучих материалов пользуются величиной удельной поверхности. Удельной поверхностью материала называется суммарная поверхность всех частиц, заключенных в единице массы (м2 /кг) или объёма (м2/ м3).
Суммарная полезная работа, затраченная на процесс измельчения материала и отнесенная к единице объема или массы, называется удельной работой измельчения.
На основании разработанных теорий измельчения: объемной - В. Л. Кирпичевым (1877 г.) и поверхностной - П. Р. Риттингером (1867 г.), академик П. А. Ребиндер в 1928 г. объединил обе теории: вывел уравнение и назвал его основным законом измельчения, из которого следует, что полная работа измельчения равна сумме работы деформации в деформируемом объеме разрушаемого материала и работы образования новых поверхностей. Это уравнение используется лишь для качественного исследования рабочих процессов и сравнительных расчетов с целью выявления относительной величины работы, затрачиваемой на измельчение.
Как правило, измельченные частицы имеют неправильную форму и оцениваются несколькими размерами. Для практических целей крупность частиц оценивают характерным размером - "диаметром".
Учитывая разнообразность и сложность формы зерен разных культур, наиболее удобно обозначить их размеры величиной эквивалентного диаметра (DЭ). Это диаметр шара, объем которого равен действительному объему зерна.
Значение эквивалентного диаметра находят при экспериментальном определении среднего объема зерен путем погружения 1000 шт. после их взвешивания (натуры зерна) в мензурку с жидкостью (толуол, бензин, ксилол).
Если объемы одного зерна V3, а объем равновеликого шара , то величина эквивалентного диаметра зерна будет равна:
(5.1)
Крупность всей массы сыпучего материала оценивают по содержанию в ней классов (фракций) определенных размеров, т. е. по гранулометрическому составу.
Гранулометрический состав измельченных кормов можно определить при помощи следующих анализов: микроскопического (для частиц менее 50 Мк), седиментометрического (5..56 Мк) и ситового (крупнее 40Мк) .
При ситовом анализе экспериментально определяется модуль помола с использованием решетного классификатора (прибора Макарова, рис. 5.1.). В него устанавливают металлические (пробивные) сита с диаметром отверстий, равным 1,2,3 и 4 мм. Навеску в 100 г измельченного продукта высыпают на верхнее сито классификатора и встряхивают в течение 3...5 мин. Затем остатки продукта взвешивают с соответствующих сит, начиная с поддона определяют массу фракций Ро,Р1,Р2,РЗ,Р4.
Рисунок 5.1-Технологическая схема решетного классификатора.
Результаты взвешивания подставляют в формулу 5.2. и находят средневзвешенный диаметр (модуль) частиц измельченного продукта:
, мм (5.2)
где М - модуль помола, мм;
0,5…3,5 - средний размер отверстий двух смежных сит, мм;
Р0, Р1... - масса остатка соответственно на поддоне и ситах классификатора,
г.;
G - масса пробы (навески), г.
Отождествляя модуль с эквивалентным диаметром шара, находят его объем.
3.Машины для измельчения стебельных кормов бывают специализированные (соломорезки, силосорезки и измельчители грубых кормов - ИГК-З0Б) и универсальные (соломосилосорезки - РСС-6Б). По конструкции режущего аппарата они делятся на барабанные и дисковые. По общей конструкции, определяющей принцип их использования - на стационарные и передвижные.
Процесс резания стебельных кормов представляет собой частный вид измельчения и поэтому подчинен общим законам разрушения материалов под действием внешних сил, превосходящих силы молекулярного сцепления. Однако этот процесс имеет свои специфические особенности и поэтому он более полно излагается в теории резания лезвием.
Теорию резания лезвием разработал В. П. Горячкин (1928-1935 гг). Дальнейшее развитие она получила в трудах В. А. Желиговского, Г. И. Бремера, А. Н. Карпенко, В. А. Зяблова, Е. М. Гутьяра, М. П. Горбунова, М. В. Сабликова и др.
При резании лезвием материал разрушается в основном под действием давления непосредственно вершины двухгранного угла рабочей части ножа (лезвия) В этом случае грани лезвия (фаски) существенного влияния на процесс резания не оказывают, а сам процесс резания происходит без снятия стружки.
Процесс резания лезвием состоит из двух этапов. Первый этап -уплотнение материала ножом (упругие деформации), второй этап -перерезание стеблей (пластические деформации).
В. П. Горячкин установил, что в процессе резания лезвием решающее значение имеет скользящее (боковое) движение ножа, так как оно понижает предел нормального давления на материал, необходимого для возбуждения процесса резания и обеспечивает более чистый срез (перепиливающее действие), так как предел прочности сдвига меньше предела прочности сжатия.
В. А. Желиговский выделяет три характерных случая резания лезвием (рисунок 5.2).
В первом случае резание материала производится только нормальной силой (рисунок 5.2 а) без бокового перемещения ножа (рубка материала). Угол скольжения t = 0.
Рисунок 5.2-Характерные случаи резания:
а) без скольжения - рубка;в) с недостаточным скольжением;с) со скольжением.
Во втором случае (рисунок 5.2, в) кроме нормального давления (и нормальной составляющей скорости) имеет место и боковая сила (касательная составляющая скорости), но она еще не может вызвать скользящего движения лезвия по частицам материала, так как угол скольжения меньше угла трения ( о< t < j).
Третий случай (рисунок 5.2, с). Угол скольжения больше угла трения, т. е.
Ðt > Ðj. Резание производится нормальной силой N с участием боковой силы Т. Лезвие перемещается относительно материала со скоростью ut в боковом направлении и этим обеспечивается эффект перепиливания.
Таким образом, для рабочего процесса соломосилосорезок основное значение имеют такие параметры, как нормальное давление ножа на материал и боковое скользящее движение ножа.
Изобразим схему режущего аппарата дисковой соломосилосорезки РСС-6Б (рисунок 5.3).
Ножи установлены на диске под углом к радиусу (Ðg) , благодаря чему обеспечивается резание со скольжением.
u=w*r
Рисунок 5.3 - Схема режущего аппарата дисковой соломосилосорезки
РСС-6Б
Пусть нож движется по направлению вектора окружной скорости u (она перпендикулярна радиусу-вектору r). Разложим окружную скорость на нормальную составляющую - un (направленную перпендикулярно лезвию ножа (а-а) и касательную ut (направленную вдоль лезвия ножа).
Угол между радиусом-вектором r и касательной к лезвию ножа (а-а) называется углом скольжения t . Угол между векторами окружной скорости u и нормальной составляющей скорости un равен углу скольжения t (угол между взаимно перпендикулярными сторонами). Тангенс угла скольжения t (отношение тангенциальной составляющей скорости ut к нормальной составляющей скорости un ) называется коэффициентом скольжения:
(5.3)
Коэффициент скольжения e указывает долю участия бокового скользящего движения ножа в общем процессе резания.
При работе режущего аппарата дискового типа материал сечением АБВГ перерезается лезвием ножа (а-а) на участке rS. Для преодоления силы сопротивления необходимо приложить усилие Р. Сила резания Р за счет бокового скользящего движения ножа отклоняется от нормали (n-n) на угол трения j . Угол j носит название угла скользящего резания.
Разложим силу резания Р на нормальную составляющую N (вдоль нормали n-n) и касательную (вдоль лезвия - а-а). Тангенс угла трения j (или угла скользящего резания) (отношение касательной силы Т к нормальной N) называется коэффициентом скользящего резания:
(5.4)
Академик В. А. Желиговский доказал, что для процесса резания имеет
значение не абсолютная величина касательной силы, а ее соотношение с нормальной силой, определяемое коэффициентом скользящего резания. Этот коэффициент для ржаной соломы изменяется от 0,7 до 0,4 при изменении нормального давления, при котором начинается процесс резания, в пределах 20...200 Н.
Необходимо отметить, что коэффициент скольжения e и коэффициент скользящего резания ¦1 зависят друг от друга. И эта зависимость выражается
(5.5)
где k - коэффициент пропорциональности, равный 0,176...0,325.
При увеличении коэффициента скольжения e возрастает и значение коэффициента скользящего резания ¦1 .
Защемление материала между лезвием и противорежущей пластиной призвано обеспечить нормальное протекание процесса резания, чтобы материал не выскальзывал, а был надежно защемлен в режущей паре.
Рассмотрим условия, при которых будет обеспечено надежное защемление материала (рисунок 5.4).
Рисунок 5.4-Условие защемления материала в режущей паре
Угол между лезвием ножа и противорежущей пластиной называется углом защемления х. В режущей паре находится материал круглого сечения. Пусть в момент начала защемления материала угол трения оказался таким, что сила резания Р будет перпендикулярна биссектрисе угла защемления х. Тогда из перпендикулярности сторон двух треугольников можно определить х/2=j или x=2/j . Это предельно допустимый угол раствора, так как при его увеличении проекция силы Р не будет равна нулю и даст составляющую, которая вытолкнет материал из раствора наружу. Следовательно, режущая пара защемляет материал, если угол раствора меньше или равен двойному углу j скользящего резания.
В несимметричной режущей паре имеются два угла скользящего резания: j1 - угол трения лезвия ножа по материалу и j2 - угол трения материала по кромке противорежущей пластины. В этом случае полное защемление наступит, когда
(5.6)
где jmin - наименьший из углов j1, и j2,
По экспериментальным данным в дисковых соломорезках принимают х= 40...50° и в барабанных - х=24...30°.
Важнейшим параметром режимов резания является удельное давление ножа на материал. Удельным давлением называется нормальное давление ножа на материал, достаточное для возбуждения процесса резания и отнесенное к единице длины нагруженного участка лезвия, т. е.
(5.7)
Для случая резания рубкой, когда отсутствует скользящее движение ножа, удельное давление будет иметь максимальную величину (q0).
Для различных кормов q0 колеблется в пределах:
для соломы - (5...12) 103 н/м, травы - (4...8) 103 н/м, листостебельной массы подсолнечника - (3...13) 103 н/м.
Удельное давление изменяет свое значение в зависимости от технологических факторов (влажности), кинематических (скорости резания, угла скольжения) и конструктивных факторов режущей пары и ее технического состояния в процессе эксплуатации: угла резания α, угла установки ножа b, угла заточки ножа g, остроты лезвия d и зазора в режущей паре (рисунок 5.5).
2…3мм dmax
|
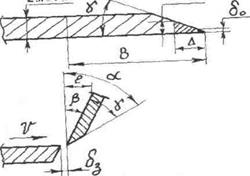
Рисунок 5.5 -Острота лезвия ножа (а), угол резания и зазор в режущей паре (б).
Угол резания a представляет собой сумму двух углов - угла установки b и угла заточки ножа g . Оптимальный угол резания ножа устраняет вредные сопротивления и создает наиболее выгодные условия резания.
Если материал движется со скоростью u по противорежущей пластине, то при постоянной частоте вращения диска с ножами эта скорость определяет длину резки l. Подаваемый вальцами материал не будет упираться торцом в переднюю грань ножа только в том случае, если нож наклонить так, чтобы его верхняя часть спинки отошла на длину резки l за время прохода ножа всего сечения горловины. Поэтому угол установки ножа b имеет целью устранить излишние сопротивления от трения поступающей массы корма о переднюю грань
ножа. Угол установки ножа рассчитывается так. Путь, пройденный диском с ножами за один оборот и материалом, откладывается на диаграмме в масштабе (рисунок 5.6). Из полученного треугольника находится расчетный угол установки ножа.
(5.8)
Отсюда
Рисунок 5.6 - Схема к определению угла установки ножа.
Угол заточки ножа у соломосилосорезки принимают в пределах 12...30°. Нижний предел угла заточки обусловлен прочностью материала, а верхний - экономичностью режимов резания.
Острота лезвия оценивается толщиной его рабочей кромки d0 которая должна быть 20...40 мКм. При затуплении лезвия допускается увеличение d0 до 100 мКм, после чего нож подлежит перезаточке. Чтобы восстановить начальную остроту, необходимо снять полоску шириной
. При ширине зоны закалки ножа В=30 мм количество переточек n равно:
Ножи соломосилосорезок изготовляют из стали марок У9, 65Г и 70Г. Твердость лезвий после термообработки должна быть не менее HRC = 50...55.
Зазор между лезвием ножа и противорежущей пластиной для дисковых аппаратов устанавливается в пределах 0,5... 1 мм, а для барабанных - 1,5...4,6 мм.
4.Корнеклубнемойки по конструкции рабочих органов делятся на кулачные (бильные), барабанные, дисковые и шнековые. Они могут быть стационарными и передвижными. По организации рабочего процесса они могут быть периодического и непрерывного действия.
Рабочий процесс всех моек основан на отделении загрязнений в воде при трении корнеклубнеплодов друг о друга, о кожух и рабочие органы машины. Вода служит также и для удаления в осадок отдельных частиц грязи.
Известные конструкции корнеклубнерезок делятся по назначению на корнерезки и корнетерки. Корнерезки бывают или в виде отдельных машин, выполняющих лишь одну операцию - резку корнеклубнеплодов, или в виде составной части агрегата, выполняющего две или несколько операций обработки корнеклубнеплодов.
Корнеклубнерезки классифицируются:
- по форме рабочей части - на дисковые, барабанные и лопастные центробежные;
- по расположению ножей относительно продукта - на вертикальные и горизонтальные;
- по принципу действия различают машины с режущими рабочими органами и ударного действия - это жестко или шарнирно закрепленные молотки, фрезы, зубья (штифты). Они довольно энергоемкие и образуют много мезги, поэтому в последнее время в корнерезках используют ножи.
Отличительной особенностью дисковых и барабанных режущих аппаратов является то, что у них процесс резания происходит путем движения ножей относительно продукта, а у центробежных - материал измельчения подводится к неподвижным ножам.
Рабочий орган корнерезок - резец, имеющий форму клина. В соответствии с теорией клина (И. Тиме) процесс образования стружки (резка) при резании (ККП) корнеклубнеплодов протекает следующим образом.
![]() |
В первый момент клин с углом внедряется в материал под действием силыР,сжимая его на пути а.
В следующий момент, когда сила Р достигает некоторого предела, происходит скалывание
элемента стружки по длине , которая всегда больше пути α.
Рисунок 5.7- Схема внедрения клина
Проведенные исследования позволили установить, что линия скалывания несколько опережает лезвие клина: вначале она углубляется в толщу материала, а затем направляется под некоторым углом вверх. Однако до поверхности разрыв не доходит, и скалываемые элементы получаются связанными между собой (стружка скалывания).
Усадки или укорочения элемента стружки при резании ККП не наблюдается, т.е. .
Путь сжатия а и длина элемента стружки - зависят от физико-механических свойств материала и геометрии клина.
Резание ККП происходит без скольжения, т.к. угол трения материала о
нож (клин) довольно большой ( = 35...40° ). Осуществление резания со скольжением привело бы к значительному увеличению габаритов рабочих органов.
Длина элементов стружки ( ) зависит от ее толщины (h) и угла резания (
) и почти не зависит от скорости резания и толщины ножа.
Для измельченияККП могут применяться ножи различной формы:
- плоские с прямым сплошным или гребёночным лезвием (рисунок 5.8);
- плоские с криволинейным лезвием;
-совочкообразные.
Ножи изготовляют из инструментальной углеродистой стали 99 или марганцовистой стали 65Г и 70Г. Разрабатывая теорию клина, академик В.П.Горячкин предложил известную рациональную формулу, которая может быть применена для общего сопротивления резания
Рисунок 5.8 - Схема ножа
P=P0+k*b*h+e*b*h*u2, Н (5.9)
где P0 - некоторое постоянное сопротивление, учитывающее конструктивные
параметры ножа, не зависящие от сечения стружки;
k,e - коэффициенты пропорциональности
b,h- ширина и толщина срезаемой стружки, мм;
u2 - скорость резания, м/с.
,
где - сопротивление деформации срезаемого слоя,Н;
- сопротивление, зависящее от скорости резания и обусловленное необходимостью отбрасывания сколотой стружки в сторону со скоростью u:
Как видно из графика, Pскор- третий член формулы имеет очень малое значение.
![]() ![]() ![]() |
Рисунок 5.9 - Схема распределения усилий резания по составляющим
сопротивлений при a =17° для кормовой свеклы (по Г.И. Новикову)
Следует заметить, что при изменении угла резания от 17 до 30° суммарное сопротивление почти не изменяется.
Процесс резания ККП клином протекает с переменным усилием: в пер вый момент перед врезанием усилие равно 0, затем при уплотнении по мере продвижения ножа по пути сжатия оно достигает max и в момент скалывания снова падает до нуля.
В общем случае производительность (подачу) любой корнерезки можно определить через массу материала, срезаемую одним ножом за один оборот Vсr, числа одновременно работающих ножей Z и частоту вращения рабочего органа (барабана, диска) - n, то есть
Рисунок 5.10 - Процесс резания клином
кг/ч (5.10)
Объем продукта, срезаемого одним ножом за один оборот рабочего органа (диска, барабана, крылача), будет
м3 (5.11)
где r - объемная масса корнеклубнеплодов, кг/м3;
F - площадь описанная ножом или материалом по отношению ножа, м2;
h - толщина резки (стружки), м;
Kk - конструктивный коэффициент использования длины ножа
(Kk = 0,7...0,8);
K3- коэффициент использования рабочей площади диска ( K3 = 0,6...0,8).
Величина F для дисковых корнерезок определяется согласно схемы (рисунок 5.11) F=
Для центробежных (дисковых) корнерезок величина площади F зависит от пути движения материала 2pR в камере резания и длины ножаL. Рабочая площадь равна F=2pRL
И окончательно:
Производительность дисковой корнерезки будет равна
, кг/ч (5.12)
.
Рисунок 5.11- Схема к определению площади F.
Рисунок 5.12 - Схема к определению площади F в центробежной
корнерезке.
Производительность центробежной корнерезки
кг/ч
5.Влаготепловая и химическая обработка кормов предназначена для повышения поедаемости, питательности и усвояемости его животными, а также уничтожения вредных соединений и болезнетворных бактерий, которые могут вызвать заболевания (грибки, плесень). Влаготепловой обработке подвергаются грубые корма, корнеклубнеплоды, зерно, отходы крахмального и маслобойного производства, корма животного происхождения. Химической обработке подвергают чаще солому.
Установки, машины и агрегаты для тепловой обработки кормов классифицируются по следующим признакам.
1). По назначению - для обработки грубых кормов, корнеклубнеп-лодов и пищевых отходов.
2). По виду источника теплоты - паровые, электрические.
3). По технологическому назначению - запарники, варочные, сушильные.
4). По способу выполнения технологического процесса - непрерывного и периодического действия.
5). По условиям эксплуатации - стационарные и передвижные.
Влаготепловая обработка кормов всегда связана с передачей тепла от более нагретой среды (теплоносителя) к менее нагретой (кормам) в различного рода тепловых аппаратах непрерывного или периодического действия.
Тепловые явления в процессе запаривания и варки кормов носят прерывистый характер и чередуются между собой.
Изменение тепловых явлений во время запаривания для аппарата периодического действия изобразим графически (рисунок 5.13).
Рисунок 5.13 - График рабочего процесса запарника периодического
действия
На участке О1А осуществляется подвод пара на нагревание корма. Идет интенсивный теплообмен между паром и холодным кормом, сопровождающийся образованием конденсата. В точке А теплообмен прекращается, корм нагревается почти до температуры (96°С), прекращается образование конденсата, появляется парение их запарника (интервал времени: от 40 до 100 минут). Подача пара прекращается в точке А.
На участке АВ корм допаривается(разваривается) за счет теплоты, накопленной продуктом (интервал 30...60 мин.).
От точки В идет разгрузка аппарата и охлаждение продукта и запарника.
Из графика видно, что теплоту, идущую на обработку продукта, можно уменьшить за счет сокращения времени на разгрузку следующей порции в точке О2.
Вся теплотаQ, подведенная в запарник, расходуется на нагревание продукта Qпр, на нагрев стенок запарника Qст. и на потери теплоты в окружающую среду 0ср.-Суммируя их, получим уравнение теплового баланса:
Дж (5.13)
Из курса теплотехники известно, что теплота, необходимая для нагревания любого тела равна:
Дж (5.14)
где Мпр - масса продукта, кг;
Спр - удельная теплоемкость корма, Дж/кг.К;
tкон, t нач - конечная и начальная температура корма, К. Теплота, расходуемая на нагрев стенок аппарата:
Дж (5.15)
где М ст - масса запарника, кг;
Сст - удельная теплоемкость материала стенок, Дж/кгК;
t1 кон -t1нач - конечная и начальная температура стенок, К.
Стальные запарники выгоднее, с точки зрения затрат теплоты, так как удельная теплоемкость стали - 0,48, а сосновых досок - 2,72.
Количество теплоты, затрачиваемое на компенсацию потерь в окружающую среду, определяется по формуле:
, Дж (5.16)
где F - площадь поверхности запарника, м2;
k - суммарный коэффициент теплоотдачи поверхности запарника (за счет
конвекции и лучеиспускания), Дж/м 2·k
t - продолжительность теплоотдачи, ч;
t ст - средняя температура поверхности стенок, К;
tвозд - средняя температура окружающего воздуха, К.
Потребное количество пара при запаривании корма определяется из уравнения теплового баланса. Если в качестве теплоносителя используется водяной пар, полностью конденсирующийся в запарнике, то уравнение примет вид:
кг (5.17)
где i" - энтальпия пара, Дж/кг;
х - степень сухости пара (при отсутствии сухопарника x=0,06);
i' - энтальпия конденсата, Дж/кг.
Энтальпия (теплосодержание) конденсата:
Дж/кг (5.18)
где c к - удельная теплоемкость конденсата, Дж/кгК
c к =4,19х103, Дж/кгК;
tк - температура конденсата (на 5...8 К меньше температуры пара), К.
В технологических расчетах линий тепловой обработки кормов пользуются опытными значениями удельного расхода пара, представляющими собой отношение массы пара к массе корма: П/Мпр .
Для существующих конструкций запарников суммарный удельный расход пара (с учетом нагрева стенок и компенсации потерь теплоты) при запаривании корнеклубнеплодов равен 0,16...0,20; соломы -0,4...0,5; при нагреве воды от 10 до 100°С - 0,2 кг/кг.
При запаривании грубых кормов (соломы, мякины) удельный расход пара выше, так как нужно учесть затраты на нагревание воды (при увлажнении соломы в отношении 1:1).
6.Дозирование - это процесс отмеривания заданного количества материала (порции) с требуемой точностью. Степень точности обусловлена зоотехническими и технологическими требованиями, а также обосновывается экономическими соображениями. Дорогостоящие и дефицитные корма дозируют с более высокой точностью, чем стебельные и корнеплоды. Наиболее строгую точность дозирования обеспечивают при производстве белково-витаминных и минеральных добавок. Здесь малейшее отклонение от норм, предусмотренных в рецепте для отдельных компонентов, может привести не только к нарушению пищеварения и заболеванию животных, но и даже к их гибели.
В поточных технологических линиях дозаторы могут представлять собой отдельные самостоятельные машины или рабочие органы, встроенные в другие машины.
Дозаторы классифицируются по следующим признакам:
1) По способу дозирования: объемные и массовые (весовые). Объемные дозаторы проще по устройству, но дают малую точность дозирования, (погрешность достигает 10...12%). Массовые дозаторы позволяют получить высокую точность дозирования (погрешность всего 1...3%). Однако они сложны по устройству и дороги.
2) По способу выдачи заданного количества материала: порционные (из разнообразных кормов) и непрерывного действия (для сухих сыпучих компонентов).
3) По назначению: для дозирования сухих сыпучих, влажных рассыпных и жидких кормов.
4) По типу рабочих органов: барабанные, ленточные, шнековые, тарельчатые, вибрационные, плунжерные, секторные, шиберные, мерные емкости, шлюзовые.
5) По уровню автоматизации: с ручным управлением, полуавтоматические и автоматические. Последние могут работать по разомкнутому и замкнутому циклам.
По разомкнутому циклу дозаторы работают как исполнительные механизмы, обеспечивающие выдачу заданного количества вещества независимо от изменения его параметров.
При работе по замкнутому циклу подача вещества изменяется по управляющим сигналам системы автоматического регулирования, следящей за ходом процесса.
6) По способу регулирования дозы: изменением частоты вращения, рабочей длины барабана, длительности дозирования, поперечного сечения слоя корма, скорости движения кормоносителя, объема мерной емкости, количества мерных емкостей и т.д.
Наибольшим разнообразием конструкций отличаются дозаторы, предназначенные для комбикормов и других сыпучих кормов.
Для приготовления смесей из концентрированных кормов в
хозяйствах, как правило, применяют объемные дозаторы - барабанные, тарельчатые, шнековые, мерные емкости и массовые - бункерные с противовесом.
Для дозирования готовых комбикормов при раздаче их животным получают распространение объемные дозаторы: секторные, шиберные, плунжерные, грейферные, ленточные и мерные емкости.
Для дозирования влажных рассыпных кормов обычно используют ленточные или шнековые транспортеры, включаемые в работу на строго определенное время или имеющие устройства для регулирования расхода.
Для объемного дозирования жидких кормов используют мерные емкости разных конструкций.
В процессе работы дозаторы должны выполнять следующие функции.
1) Обеспечить выдачу заданного количества материалов с требуемой точностью, т.е. обеспечивать расход материала в пределах установленного допуска.
Qз
, (5.19)
гдеQ3- заданная доза;
- величина допуска. Для этого есть три варианта решения:
- без регламентации времени выдачи (для сухих концентрированных кормов);
- выдача за минимальный промежуток времени (для скоропортящихся кормов);
- с выдачей за строго определенное время.
2) Обеспечить расход непрерывным потоком с целью поддержания заданной подачи материала Q(t)
, выдаваемого за промежуток времени
t.
3) Обеспечивать заданный расход одного из исходных компонентов смеси.
В общем случае процесс непрерывно-поточного дозирования состоит в обеспечении выдачи через отверстие непрерывным потоком с переменной скоростью некоторого материала.
Следовательно:
Qp=f(t),
где Qp - расход по параметру - времени t, кг/с.
В процессе дозирования осуществляется контроль и регистрация текущих значений расхода, а также интегрирование этих значений с целью учета количества выданного материала.
При объемном непрерывном дозировании основным показателем работы дозатора является его объемный расход Qv определяемый по формуле:
м3/с (5.20)
где Sотв - площадь сечения проходного отверстия, м2;
uср-средняя скорость истечения материала через проходное отверстие, м/с.
Из формулы видно, что регулирование расхода дозатора можно осуществлять тремя способами: изменением проходного отверстия; скоростью потока и комбинированным способом.
При весовом дозировании основным показателем работы дозатора является его массовый расход
кг/с (5.21)
где r - плотность материала, кг/м3.
Изменение расхода дозаторов порционного действия может быть достигнуто либо за счет увеличения порции q выдаваемого материала (рисунок 5.14, а) на величину Dq=(q2-q1) Dt1, либо за счет увеличения числа порций, выдаваемых за единицу времени при сохранении размера порции (рис. 5.14, б), т.е. Dq = q1( Dt1+Dt2).
![]() |
![]() |
Рисунок 5.14 -Способы регулирования расхода дозатора:
а - увеличение выдаваемой порции;
б - увеличение количества порций в единицу времени.
Увеличение подачи дозаторов непрерывного действия происходит за счет увеличения порции.
Дозирование - процесс случайный, и самопроизвольное отклонение любого из трех сомножителей (Sотв,ucp,r в формуле 5.21) ведет к отклонению значений расхода от заданной величины, <
Дата добавления: 2018-11-26; просмотров: 3758;