ОТЖИГ И НОРМАЛИЗАЦИЯ СТАЛИ
3.1.1. Отжиг
Отжигом называется операция термической обработки, связанная с нагревом стали до определенной температуры, выдержкой и медленным охлаж-дением (с печью). Режимы отдельных видов отжига приведены на рис. 3.1.
|


|
|
|
|
|
|
|
|
|
|
|
|
|
|
|
|

Рис. 3.1. Виды отжига стали: а – рекристаллизационный (низкий);
б – диффузионный; в – полный; г – изотермический
Скорость охлаждения в печи при отжиге в зависимости от материала и вида изделий – не более 30 – 200 °С/ч. Чтобы изделия не покоробились, их выгружают при температуре 500 – 450°С, а затем охлаждают на воздухе.
Отжиг, в зависимости от назначения, – операция предварительная или окончательная. Основное назначение отжига – получение более равновесной структуры: снятие внутренних напряжений, улучшение или исправление структуры металла (измельчение зерна, устранение ликвации), снижение твердости, повышение пластичности, улучшение обрабатываемости резанием.
Рекристаллизационный отжиг применяют для восстановления исходной твердости, пластичности и ударной вязкости, которые изменились в результате холодной пластической деформации, т. е. для снятия наклепа.
Упрочнение металла под действием холодной пластической деформации называется наклепом, или нагартовкой. В металле резко возрастает плотность дефектов кристаллического строения и образуется определенная ориентировка зерен – текстура. Зерна деформируются, сплющиваются и из равноосных зерен превращаются в неравноосные (растягиваются в виде лепешки, блина).
Рекристаллизацией называют зарождение и рост новых равноосных зерен с меньшим количеством дефектов кристаллического строения при нагреве деформированной стали. Между температурным порогом рекристаллизации и температурой плавления имеется простое соотношение: Тр ≈ (0,3 – 0,4)∙Тпл, что составляет для углеродистых сталей 670 – 700 °С.
Рекристаллизационный отжиг углеродистой и низколегированной стали проводится при температуре до 700 °С с выдержкой после нагрева от 30 до
60 мин в зависимости от состава стали. После завершения рекристаллизации строение металла и его свойства становятся прежними (которые он имел до
деформации).
Низкотемпературный отжиг проводят для снятия внутренних остаточных напряжений при температуре до 700 °С в течение нескольких часов. Степень снятия напряжений определяется главным образом температурой нагрева, а не временем выдержки. В результате отжига уменьшаются особенно опасные остаточные растягивающие напряжения, снижается склонность к хрупкому разрушению, повышается сопротивление усталости и ударным нагрузкам, снижается склонность к межкристаллитной коррозии, стабилизируются размеры изделий и предотвращается их коробление. Низкотемпературному отжигу подвергают отливки, поковки, сварные изделия и детали, в которых из-за неравномерного охлаждения и по другим причинам возникли внутренние напряжения.
Гомогенизация (высокотемпературный, или диффузионный, отжиг) применяется для устранения дендритной (внутрикристаллической) ликвации в слитках или фасонных отливках главным образом из легированной стали. Ликвация усиливает анизотропию свойств, карбидную неоднородность, снижает относительное удлинение и ударную вязкость.
Для ускорения диффузии и получения однородного (гомогенного) металла нагрев производят до температуры 1100 – 1200 °С с выдержкой после нагрева от 8 до 20 ч. В результате такого высокотемпературного нагрева происходит интенсивный рост зерна. Перегрев устраняется дополнительным отжигом на мелкое зерно. Диффузионный отжиг сопровождается потерями металла на окалину и является малопроизводительной и дорогой операцией.
Полный отжиг, или отжиг на мелкое зерно, проводится только для эвтектоидной стали при температуре на 30 – 50 °С выше точки Ас3. При этом время нагрева и продолжительность выдержки зависят от состава стали, размеров изделий, способа укладки их в печь, типа нагревательной печи и т. п.
Назначение полного отжига – измельчение зерна, исправление структуры, максимальное снижение твердости и повышение пластичности, снятие внутренних напряжений. При этом отжиге происходит полная фазовая перекристаллизация. Медленное охлаждение обеспечивает распад аустенита при малой степени переохлаждения, получение высокой пластичности и минимальной твердости. Мелкое начальное зерно аустенита способствует получению при охлаждении мелкозернистой структуры с равномерным распределением феррита и перлита (рис. 3.2). Полному отжигу обычно подвергают сортовой прокат, поковки и фасонные отливки. Это операция длительная и малопроизводительная.
а б
Рис. 3.2. Структура стали 45: а – исходная; б – после полного отжига
Изотермический отжиг имеет преимущество перед полным – сокращается время отжига и получается более однородная структура, так как распад аустенита происходит при постоянной температуре во время выдержки, поэтому полный отжиг часто заменяют изотермическим.
Неполный отжиг используют для снижения твердости стали и улучшения обрабатываемости резанием. Заэвтектоидную сталь отжигу с полной перекристаллизацией подвергать нельзя, так как при медленном охлаждении из аустенитного состояния вторичный цементит выделяется по границам зерен в виде сетки и сталь становится хрупкой. Заэвтектоидную сталь подвергают только неполному отжигу с нагревом до 750 – 770 °С (несколько выше А1), выдерживают до прогрева по сечению и охлаждают.
При таком нагреве в аустените остается большое число нерастворившихся включений цементита, которые служат центрами кристаллизации при охлаж-дении во время аустенитно-перлитного превращения. В результате образуется структура зернистого перлита. Этот отжиг часто называют отжигом на зернис-тый перлит, или сфероидизацией.
Для сокращения времени отжиг на зернистый перлит можно произвести с изотермической выдержкой. После нагрева сталь медленно охлаждают (30 –
50 °С/ч) до 680 – 650 °С и выдерживают 1 – 3 ч для распада переохлажденного аустенита и сфероидизации карбидов. Последующее охлаждение производят на воздухе. Сталь со структурой зернистого перлита характеризуется наименьшей твердостью, наилучшей обрабатываемостью резанием и менее склонна к перегреву при закалке, поэтому инструментальная и шарикоподшипниковая сталь, как более твердая, должна поставляться со структурой зернистого перлита (рис. 3.3).
Рис. 3.3. Структура стали, отожженной на зернистый перлит
Доэвтектоидную сталь отжигают на зернистый перлит для получения максимальной пластичности перед холодной обработкой давлением (штамповкой, волочением и т. п.). Нагрев при неполном отжиге до более высокой температуры (800 °С) приводит к получению структуры пластинчатого перлита.
Циклический, или маятниковый, отжиг применяют для полной сфероидизации цементита стали. Сталь несколько раз попеременно нагревают на 10 – 15 °С выше A1 и охлаждают на 10 – 15 °С ниже A1 с кратковременной выдержкой после каждого цикла нагрева и охлаждения. Количество циклов нагрева и охлаждения зависит от химического состава стали. Пластинка карбида при каждом нагреве частично растворяется в аустените, а при охлаждении начинает расти. Растворяясь и «подрастая», кристалл карбида из пластинчатой принимает зернистую форму – происходит его сфероидизация.
3.1.2. Нормализация
Нормализацией называется операция термической обработки, связанная с нагревом доэвтектоидной стали до температуры на 30 – 50 °С выше точки Ас3, заэвтектоидной – на 30 – 50 °С выше точки Асm (для обеспечения аустенитной структуры), выдержкой и последующим ускоренным охлаждением на воздухе.
По сравнению с отжигом нормализация более производительна и экономична. В результате полной перекристаллизации стали в аустенит она измельчает структуру, повышает работу развития трещин, понижает порог хладноломкости.
Нормализация как промежуточная обработка аналогична отжигу, ее применяют для низкоуглеродистой стали вместо полного отжига. Однако нормализация не может заменить смягчающего отжига для среднеуглеродистой стали, которая при охлаждении на воздухе имеет повышенные твердость и прочность. Нормализацию часто используют для измельчения зерна стали перед закалкой.
Исправить структуру перегретой заэвтектоидной стали можно только нормализацией, она измельчает зерно, и при ускоренном охлаждении на воздухе цементит вторичный не успевает образовать грубую сетку по границам зерен. Следует отметить, что скорость охлаждения на воздухе зависит от массы изделия и отношения его поверхности к объему. Эти факторы сказываются на структуре и свойствах нормализованной стали.
ЗАКАЛКА И ОТПУСК СТАЛИ
Закалкой называется операция термической обработки, связанная с нагревом стали выше температуры фазовых превращений, выдержкой при этой температуре и последующим охлаждением со скоростью выше крити-ческой Vкp (в каком-либо охладителе).
Закалка – основной способ упрочняющей термической обработки конструкционной и инструментальной стали.
Цель закалки – образование мартенситной структуры (или бейнитной), обеспечивающей высокую твердость и прочность стали.
Основными технологическими свойствами при закалке стали являются закаливаемость и прокаливаемость. Закаливаемость – свойство стали приобретать высокую твердость в результате закалки. Прокаливаемость – свойство стали воспринимать закалку на определенную глубину от поверхности.
Выбор температуры нагрева под закалку углеродистой стали производится по диаграмме состояния железоуглеродистых сплавов (рис. 4.1).
Доэвтектоидную сталь нагревают до температуры на 30 – 50 °С выше критической точки А3, т. е. выше линии GS диаграммы. При таком нагреве исходная ферритно-перлитная структура перекристаллизуется в аустенит. Охлаждение со скоростью выше критической приводит к мартенситному превращению (А ® М). Такая закалка называется полной, так как при нагреве происходит полная перекристаллизация структуры стали в однофазное состояние.
Эвтектоидную и заэвтектоидную сталь подвергают неполной закалке,
т. е. нагревают до температуры на 30 – 50 °С выше критической точки A1 (линия PSK диаграммы). Эта температура постоянная, и интервал значений температуры для закалки будет 760 – 780 °С. При указанной температуре не происходит полной перекристаллизации стали в аустенит (П + Ц II→ А + Ц II).
Скорость охлаждения стали после нагрева и выдержки оказывает решающее влияние на результат закалки. Режим охлаждения должен быть таким, чтобы не возникали большие напряжения, приводящие к короблению изделия и образованию закалочных трещин. Эти напряжения складываются из терми-ческих и структурных.
При закалке углеродистой и некоторых низколегированных сталей в качестве охлаждающей среды применяют воду и водные растворы. Холодная вода – самый дешевый и интенсивный охладитель. К недостаткам этой охлаждающей среды относится образование «паровой рубашки». Перепад температуры между поверхностью и центром изделия при закалке в воде может привести к возникновению высоких термических напряжений, вызывающих коробление и образование трещин. Кроме того, с повышением температуры воды резко снижается ее охлаждающая способность. Увеличение охлаждающей способности воды достигается при использовании струйного или душевого (спрейерного) охлаждения. Для крупногабаритных изделий (рельсы, трубы и т. п.) применяется водовоздушная охлаждающая среда – смесь воды с воздухом, подаваемая в камеру под давлением через форсунки (водяной туман).
Низкая пластичность и значительные внутренние напряжения при закалке стали на мартенсит не позволяют использовать ее без проведения отпуска.
Отпуск – операция термической обработки, связанная с нагревом закаленной стали ниже значений температуры фазовых превращений, выдержкой при этой температуре и последующим охлаждением на воздухе.
Цель отпуска – снижение внутренних напряжений, возникших при закалке стали, и получение более равновесной структуры с заданными свойствами (твердостью, прочностью, ударной вязкостью и пластичностью).
Отпуск необходимо проводить непосредственно после закалки, так как закалочные напряжения через некоторое время могут вызвать появление трещин. Кроме того, остаточный аустенит стабилизируется, его устойчивость к отпуску повышается.
При нагреве вследствие диффузных процессов в структуре закаленной стали происходят фазовые превращения, они зависят от температуры отпуска и определяют его назначение.
Первое превращение при отпуске. Происходит в интервале температуры 80 – 200 °С. Атомы углерода, диффундируя из решетки мартенсита, спо-собствуют образованию тончайших пластинок эпсилон-карбида, когерентно связанных с альфа-твердым раствором. Степень тетрагональности решетки мартенсита уменьшается. Снижаются внутренние напряжения. Такая гетерогенная (неоднородная) структура называется отпущенным мартенситом, или мартенситом отпуска.
Второе превращение при отпуске. Дальнейший нагрев температуры до 200 – 300 °С вызывает превращение остаточного аустенита в отпущенный мартенсит. Уменьшается тетрагональность решетки мартенсита, диффузия углерода продолжается и частицы эпсилон-карбида увеличиваются, они начинают обособляться, превращаясь в цементит.
Третье превращение происходит при температуре 300 – 400 °С. Вследст-вие выделения углерода мартенсит становится ферритом, а эпсилон-карбид – цементитом. Снимаются внутренние напряжения. В результате диффузионного распада мартенсита в этом интервале температуры образуется высокодисперсная эвтектоидная смесь феррита и цементита – троостит отпуска.
Повышение температуры отпуска до 500 – 650 °С способствует коагуляции (укрупнению) и сфероидизации (округлению) карбидных частиц. Троостит отпуска превращается в сорбит отпуска – мелкую (дисперсную) смесь феррита и зернистого цементита.
При температуре отпуска 400 °С и выше при распаде мартенсита обра-зуется смесь феррита и цементита (перлит) разной дисперсности, поэтому эти структуры имеют те же названия, что и образующиеся из аустенита. Но перлит, образовавшийся при отпуске, имеет цементит не пластинчатой, а зернистой формы, что способствует повышению пластичности (ударной вязкости)
троостита отпуска и сорбита отпуска.
Температура отпуска – самый существенный фактор, который влияет на свойства стали. Твердость и прочность с повышением температуры отпуска снижаются, а пластичность и вязкость повышаются.
В легированной стали все процессы отпуска происходят, как правило, в области более высокой температуры, так как легирующие элементы замедляют диффузионные процессы. Так, распад мартенсита завершается при температуре 450 – 500 °С, а коагуляция специальных карбидов – при 600 – 680 °С. При некоторых условиях отпуска закаленных легированных сталей происходит их «охрупчивание» – потеря пластичности (отпускная хрупкость).
Отпускная хрупкость первого рода появляется при температуре порядка 300 °С у всех сталей независимо от их состава и скорости охлаждения при отпуске. Отпускная хрупкость второго рода проявляется после отпуска выше
500 °С в результате медленного охлаждения. Не все стали склонны к хрупкости второго рода, но хром, особенно в сочетании с никелем или марганцем, делает сталь особо чувствительной к условиям охлаждения при отпуске. Для предупреждения «охрупчивания» стали необходимо при проведении отпуска избегать интервала температуры отпускной хрупкости первого рода (300 – 350 °С). Стали, склонные к отпускной хрупкости второго рода, после отпуска следует охлаждать быстро (в воде или масле).
4.1.1. Основные способы закалки стали
Закалка в одном охладителе. Изделия из печи по конвейеру (транспортеру) поступают в закалочный бак с охлаждающей средой, где и находятся до полного охлаждения (рис. 4.2, кривая 1).
Этот способ применяется для изделий простых форм, изготовленных из углеродистой (охлаждение в воде) и легированной (охлаждение в масле) стали и является простым и наиболее распространенным способом как в единичном, так и в массовом производстве. Недостатком данного способа закалки является то, что в результате существенной разницы значений температуры нагретого металла и охлаждающей среды в закаленной стали наряду со структурными возникают значительные термические напряжения, вызывающие коробление детали, появление трещин и других дефектов.
Прерывистая закалка в двух охладителях. Изделие сначала быстро охлаждают до 400 – 300 °С в воде, а затем для окончательного охлаждения переносят в масло – «через воду – в масло». В интервале температуры мартенситного превращения сталь охлаждается более медленно, что способствует уменьшению закалочных напряжений (рис. 4.2, кривая 2).
![]() |
|
|
|
|
|
|
|
|
|
|
|
|
|
|
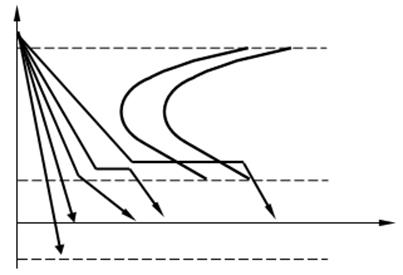
Рис. 4.2. Способы охлаждения при закалке стали: 1 – закалка в одном охладителе; 2 –прерывистая закалка в двух охладителях; 3 – ступенчатая закалка;
4 – изотермическая закалка; 5 – обработка холодом
Ступенчатая закалка. Нагретое изделие охлаждается погружением в ванну с температурой закалочной среды (расплавленные соли, селитры, щелочи) немного выше температуры начала мартенситного превращения (на 20 –
30 °С выше точки Мн) для данной стали. После выдержки, необходимой для выравнивания температуры по сечению, изделие охлаждают на воздухе. Продолжительность выдержки определяется по С-образной диаграмме и строго контролируется, чтобы не произошло промежуточного превращения аустенита. Изотермическая выдержка для выравнивания температуры по сечению спо-собствует снижению термических напряжений, а охлаждение на воздухе – структурных. Основное преимущество ступенчатой закалки – получение мартенситной структуры при минимальных закалочных напряжениях (рис. 4.2, кривая 3).
Изотермическая закалка. В отличие от ступенчатой изотермическая закалка обеспечивает не мартенситную, а бейнитную структуру. Изотермическую закалку целесообразно применять для деталей из легированной стали, склонной к короблению и образованию трещин. Так же, как и при ступенчатой закалке, охлаждение проводится в соляных ваннах с температурой на 20 –
30 °С выше точки мартенситного превращения Мн. Детали выдерживают в ванне в течение времени, необходимого для полного распада аустенита. При этом происходит превращение аустенита с образованием бейнита (игольчатого троостита). После изотермической выдержки детали охлаждают на воздухе, твердость стали – 45 – 55 HRC. Повышаются конструктивная прочность (на 25 – 30 %) и ударная вязкость (рис. 4.2, кривая 4).
Нагрев стали в жидких средах или в печи с защитной атмосферой, не вызывающих окисления, и охлаждение в расплавах щелочей позволяют получить без очистки или травления чистую поверхность изделий светло-серого цвета. Такую закалку называют светлой.
Обработка холодом. Применяется для легированной стали, у которой температура окончания мартенситного превращения Мк значительно ниже
0 °С. Если охладить эту сталь до комнатной температуры, то наряду с мартенситом в структуре оказывается значительное количество остаточного аустенита. Остаточный аустенит понижает твердость закаленной стали и может
вызвать нестабильность размеров готовых деталей, так как в процессе их работы может происходить превращение остаточного аустенита в мартенсит.
Для стабилизации размеров закаленных изделий и повышения их твердости проводится охлаждение до температуры Мк, в процессе которого аустенит превращается в мартенсит. Температура Мк легированной стали находится в широких пределах – от −40 до −196 °С (рис. 4.2, кривая 5). Обработке холодом подвергают измерительные инструменты, подшипники и другие особо точные изделия.
Закалка с самоотпуском. Изделие, нагретое под закалку, охлаждают не полностью, а через определенное время извлекают из охладителя. За счет тепла внутренних слоев верхний «холодный» слой разогревается до 200 – 250 °С, в результате чего происходит самоотпуск. Закалку с самоотпуском применяют для деталей ударного слесарного и кузнечного инструмента, которые должны иметь достаточно высокую твердость на поверхности и сравнительно вязкую сердцевину. Температуру отпуска определяют по цветам побежалости (цвет слоя окисла поверхности зависит от его толщины). Способ закалки с самоотпуском нашел применение в механизированном поточном производстве.
Закалка не является окончательной операцией термической обработки. Сразу же после закалки обязательно проводится отпуск. В зависимости от температуры его проведения различают несколько видов отпуска.
4.1.2. Виды отпуска стали
Низкий отпуск. Температура нагрева – 150 – 200 °С, выдержка – 1 – 1,5 ч. Снижаются внутренние напряжения. Мартенсит закалки переходит в мартенсит отпуска. Этот отпуск обеспечивает максимальную твердость стали и некоторое повышение прочности и ударной вязкости. Твердость (60 – 64 HRC) зависит от содержания углерода в стали. Низкому отпуску подвергают режущий и измерительный инструменты из углеродистой и низколегированной стали, а также детали после поверхностной закалки или химико-термической
обработки с целью повышения износостойкости и усталостной прочности.
Средний отпуск. Температура нагрева – 350 – 500 °С (чаще – 380 –
420 °С), выдержка – от 1 – 2 до 3 – 8 ч. Значительно снижаются внутренние нап-ряжения, мартенсит закалки переходит в троостит отпуска. Твердость –
40 – 45 HRC. Обеспечивается наилучшее сочетание предела упругости с пределом выносливости. Этот отпуск проводят в основном для пружин, рессор, мембран и подобных деталей, а также для штампового инструмента. Охлаждение после отпуска рекомендуется проводить в воде, что способствует образованию на поверхности изделий сжимающих остаточных напряжений, повышающих усталостную прочность.
Высокий отпуск. Температура нагрева – 500 – 680 °С, выдержка – 1 – 8 ч. Полностью снимаются внутренние напряжения. Структура стали в результате этого отпуска – сорбит отпуска, твердость – 25 – 35 HRC. Создается наилучшее соотношение прочности, пластичности и вязкости стали. Терми-ческую обработку, состоящую из закалки и высокого отпуска, называют улучшением (термическим). Проводится она для деталей (в основном из среднеуглеродистой конструкционной стали), у которых должна быть обеспечена повышенная конструктивная прочность (валы, оси, цельнокатаные колеса, бандажи и др.).
Искусственное старение. Закалка приводит к образованию пересыщенного твердого раствора – мартенсита. Всякий пересыщенный раствор неустойчив и будет распадаться с выделением избыточных фаз. Распад пересыщенного раствора связан с фазовыми, а следовательно, с объемными или линейными изменениями в стали. Это вызовет коробление изделий и изменение их размеров в эксплуатации. Для предупреждения коробления и изменения размеров точных инструментов, деталей станков, распределительных валов и т. п. проводят искусственное старение при температуре 120 – 150 °С. Выдержка составляет от 2 до 20 ч. Такой режим позволяет, не снижая твердости закаленной стали, стабилизировать структуру за счет выделения углерода в виде дисперсных карбидов.
Дата добавления: 2017-10-04; просмотров: 7639;