ОСАЖДЕНИЕ ПОД ДЕЙСТВИЕМ ЦЕНТРОБЕЖНОЙ СИЛЫ (ОЦС)
ОЦС применяется для разделения пылей, суспензий и эмульсий. Чтобн осуществить зтот процесе, к осаждаемым частицам необходимо приложить центробежные силы, что достигается введением разделяемого потока в поле действия центробежннх сил.
Для создания поля центробежных сил в технике используется два приема: 1) обеспечивают вращательное движение потока жидкости (газа) в неподвижном аппарате; 2) поток направляют во вращающийся аппарат, где перерабатываемые продукты вращаются вместе с аппаратом. В первом случае происходит циклонный процесс, а во втором – отстойное центрифугирование.
Физическая сущность ОЦС заключается в том, что во вращающемся потоке на взвешенную частицу действует центробежная сила, направляющая ее к периферии от центра по радиусу со скоростью, равной скорости осаждения ×w0 (рис.4.7). Окружная скорость несущего частицу потока ×wr . Частица движется а результирующей скоростью ×wр по траектории abc и оседает на стенках аппарата.
Процесс осаждения протекает под действием центробежной силы
(4.3)
|
Если вспомнить, что сила тяжести без учета подъемных (архимедовых) сил составляет:
Gg = m×g (4.4)
Из сопоставления уравнений (3) и (4) следует:
(4.5)
т.е. центробежная сила больше силы тяжести в w2r/g×r раз. В производственных процессах соотношение между wr и r таково, что центробежная сила не меньше, чем на два порядка превышает силу тяжести.
Циклонный процесс используется преимущественно для разделения пылей, однако находит свое применение и для разделения суспензий (гидроциклоны).
Сущность циклонного процесса заключается в том, что поток, несущий взвешенные частицы, вводят в аппарат тангенциально через входную трубу (рис. 4.8) с рассчитанной скоростью 10 – 40 м/сек. В случае газов и 5 – 25 м/сек в случае жидкостей. Благодаря тангенциальному вводу и наличию центральной выводной трубы поток начинает вращаться вокруг последней, совершая при прохождении через аппарат несколько оборотов. Под действием возникающих центробежных сил взвешенные частицы отбрасываются к периферии, оседают на внутренней поверхности корпуса 1, а затем опускаются в коническое днище 2 и удаляются из аппарата через патрубок. Освобожденный от взвешенных частиц поток выводится из циклона через выводную трубу.
Рис. 4.8. Схема устройства циклона: Рис. 4.9 Схема отстойной центри-
1 – корпус; 2 – коническое днище. фуги периодического действия
с ручной выгрузкой осадка.
Отстойное центрифугированиеприменяется преимущественно для разделения суспензий и эмульсий во вращающихся аппаратах, называемых отстойными центрифугами.
Процесс осаждения в центрифугах характеризуется теми же законами, что и осаждение в циклонах, а следовательно и все приведенные выше формулы справедливы и для них.
Центрифуги различают по принципу действия (периодические, непрерывные); по способу выгрузки материала (с ручной и механизированной выгрузкой) и по расположению вала (вертикальные, горизонтальные, наклонные).
Схема простейшей отстойной центрифуги с вертикальным расположением вала показана на рис.4.9. Центрифуга рассчитана на ручную выгрузку осадка.
Основные части этой центрифуги – сплошной барабан 2, насаженный на вращающийся вал 1, и кожух 3. Под действием центробежной силы твердые частицы осаждаются из суспензии, подаваемой в центрифугу, и отлагаются в виде сплошного осадка на стенке барабана; осветленная жидкость переливается в кожух и удаляется из него через расположенный внизу патрубок. По окончании отстаивания центрифугу останавливают и выгружают осадок вручную.
|
перемещается к окнам 5, перетекает в кожух 4 и удаляется через нижний
![]() |
патрубок. Осадок непрернвно перемещается в барабане справа налево при помощи шнека, которнй вращается со скоростью, иесколько меньшей, чем скорость вращения барабана. Через окна 2 осадок выбрасывается в кожух и выводится из центрифуги через распо-ложенный внизу патрубок.
Отстойные центрифуги для разделения эмульсий называются сепараторами. В промышленности широко применяются одно- и многокамерные, а также тарельчатые сепараторы. Так же, как и центрифуги, они имеют барабан, насаженный на вертикальный вал с приводом.
Осаждение под действием электрического полявзвешенных в газе твердых и жидких частиц имеют существенные преимущества с другими способами осаждения. Так, при электрическом осаждении частиц небольших размеров им удается сообщить значительный электрический заряд и благодаря этому осуществить процесс осаждения очень малых частиц, который невозможно провести под действием силы тяжести или центробежной силы.
Физическая сущность электроосаждения состоит в следующем. Газовый поток, содержащий взвешенные частицы, ионизирут. При этом они приобретают электрический заряд. При прохождении ионизированного газового потока в электрическом поле между двумя электродами заряженные частицы перемещаются к противоположно заряженным электродам и оседают на них.
В промышленности злектроосаждение взвешенннх частиц из газа проводится следующим способом. Газовий поток направляется внутрь трубчатых (или между пластинчатыми) положительних злектродов, которые заземляются. Внутри трубчатых злектродов (рис. 4.11, а) или между пластинчатими електродами (рис. 4.11, б) натягиваются тонкие проволоки, являющиеся катодами.
![]() | ![]() | ![]() |
а б
Рис. 4.11. Формы алектродов: а — трубчатые; б — пластинчатые
Если соединить алектродн с источником постоянного тока, создающего на злектродах разность потенциалов 4—6 кв/см, и обеспечить плотность тока 0,05—0,5 ма/м длины катода, то запыленими газ при пропусканий его между электродами почти полностью освобождается от взвешенных частиц.
В процессах злектроосаждения происходят следующие злектрические явления. Вследствие высокой разности потенциалов на электродах и неоднородности злектричского поля (сгущение силовых линий у электрода с меньшей поверхностью — катода) в слое газа у катода образуется односторонний поток электронов, направленый к аноду. В этом слое в результате соударений электронов с нейтральними молекулами газ ионизируется. Внешним признаком ионизации является свечение слоя газа или образование «короны» у катода.
При ионизации образуются как положительнне, так и отрицательные ионы; положительные ионы остаются вблизи «короны», а отрицательные направляются с огромной скоростью к аноду, встречая и заряжая на своем пути взвешенные в газе частицы.
Получившие отрицательннй заряд взвешенные частицы под действием злектрического поля перемещаются к аноду. Скорость движения взвешенных частиц, получивших заряд, невелика; она зависит от размера частиц и гидравлического сопротивления газовой среды. Обычно скорости злектроосаждения колеблются в пределах от нескольких сантиметров до нескольких десятков сантиметров в секунду.
Скорость злектроосаждения несколько увеличивается под влиянием «злектрического ветра», возникающего вследствие передачи импульса движущихся ионов газа газовой среде и взвешенным частицам.
Аппаратн для злектроосаждения называют в технике злектро-фильтрами. Злектрофильтры по форме злектродов делятся на трубчатие и пластинчатые. Трубчатий злектрофильтр показан на рис. 4.12. Запыленный газ поступает в аппарат через газоход и распределяется по трубчатим электродам 1, внутри которнх находятся коронирующие злектроды 2. Они подвешены на общей раме З, опирающейся на изоляторы 5. Осаждающиеся на внутренней поверхности трубчатых электродов частицы стряхиваются ударным приспособлением 4 и собираются в нижней части аппарата. Очи-щенный газ удаляется через газоход.
Аналогично предыдущему устроен пластинчатый злектрофильтр (рис. 4.13). В этом аппарате коронирующими злектродами служат проволоки 1, а осадительными — пластины 2, выполненные из проволочной сетки.
|
|
В зависимости от характера осаждаемнх из газа частиц, различают сухие и мокые злектрофильтры. Первые применяют для очистки газов от пыли, а вторые — от мельчайших капель жидкости, взвешенных в газе.
Фильтрование
Фильтрование- разделение жидких или газовых неоднородных систем путем пропускания их через пористую перегородку, способную пропускать жидкость или газ и задерживать взвешенные частицы.
Движущей силой процесса фильтрования является разность давлений перед фильтром и после него или центобежная сила, оказывающая давление на фильтр. Соответственно этому различают фильтрование под действием перепада давления, или просто фильтрование, и центобежное фильтрование, или центрифугирование.
В качестве фильтрующих материалов в промышленных аппаратах применяют естественные и искусственно изготовляемые зернистые и пористые тела: песок, гравий, ткани, сетки, пористую керамику, пористые пластические массы и т.д. Фильтры, работающие под давлением, называются нагнетательными, а под разряжением – всасывающие.
Схема фильтра, в котором осуществляется фильтрование под действием перепада давления с отложением осадка приведена на рис. 4.14.
![]() | |||
| |||
![]() ![]() |
Фильтрование под действием центробежной силы проводится на фильтрующих центрифугах. Барабан этих центрифуг с перфорированной стенкой выкладывается изнутри мягким пористым материалом, выполняющим роль фильтрующей перегородки. При вращении барабана осадок откладывается на внутренней (боковой) поверхности барабана, а удаление осветвленной жидкости осуществляется через фильтрующую перегородку и отверстия в барабане.
По технологическому признаку фильтрующую аппаратуру подразделяют на газовые фильтры (для очистки газов), жидкостные фильтры (для разделения суспензий) и фильтрующие центрифуги (также для разделения суспензий).
4.4.4. Перемешивание в жидкой среде
Перемешивание в жидкой среде – создание необходимого поля скоростей потоков жидкости в аппаратуре путем сообщения жидкости определенной энергии. Применяется для получения эмульсий и суспензий, а также для интенсификации тепловых, диффузионных и химических (биохимических) процессов. Преимущественное значение в химической и нефтехимической промышленности имеет механическое перемешивание. Интенсивность перемешивания определяется количеством энергии, вводимой в единицу объема перемешиваемой среды в единицу времени. Интенсивность перемешивания обуславливает характер движения данной жидкости в аппарате.
Механическое перемешивание осуществляется при помощи мешалок различного типа. Мешалка чаще всего представляет собой ту или иную комбинацию лопастей, насаженных на вращающийся вал. Различают лопастные, пропеллерные и турбинные мешалки. На рис. 4.15 показаны наиболее распространенные пропеллерные и турбинные мешалки.
|
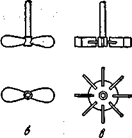
Пневматическое перемешивание осуществляется путем пропускания газа через слой перемешиваемой жидкости. Сжатый газ (обычно воздух) поступает в аппарат наполненный жидкостью. Газ распределяется барботером, представляющим собой ряд горизонтально расположенных у днища аппарата перфорированных труб. Обычно трубы изогнуты по окружности или спирали.
Циркуляционное перемешивание проводится многократным прокачиванием жидкости через систему аппарат – циркуляционный насос – аппарат. Соответственно принятой кратности циркуляции (отношению секундной производительности циркуляционного насоса к объему жидкости в аппарате) обеспечивается та или другая интенсивность перемешивания.
Псевдоожижение
Псевдоожижение– П. твердого зернистого материала называют приведение его в такое состояние, при котором его свойства по многим показателям приближаются к свойствам жидкости; такое состояние достигается в результате пропускания через слой свободно лежащего твердого зернистого материала восходящего потока газа или жидкости. Псевдоожиженный слой принимает форму вмещающего его аппарата, его поверхность гооризонтальна. Обнаруживаются и другие свойства, присущие жидкостям – текучнсть, «вязкость» и поверхностное натяжения. Тела, имеющие меньший удельный вес, чем псевдоожиженный слой, в нем, а больший – тонут.
Широкое применение техника псевдоожижения нашла в связи с рядом важных преимуществ. Твердый зернистый материал в псевдожиженном состоянии вследствие текучести можно перемещать по трубам, что позволяет многие периодические процессы осуществлять непрерывно. Благодаря интенсивному перемешиванию твердых частиц в псевдожиженном слое выравнивается поле температур, устраняется возможность значительных локальных перегревов, хотя при этом происходит уменьшение движущей силы процесса.
Процессы, в которых псевдоожижение широко применяется:
1) Химические: каталитический крекинг нефтепродуктов, гетерогенные каталитические реакции, газификация топлива, обжиг сульфидных руд и т.д.
2) Физические и физико-химические: сушка мелкозернистых, пастообразных и жидких материалов, адсорбционная очистка газов, нагрев и охлаждение газов и др.
3) Механические: обогащение, классификация, гранулирование, смешение и транспортировка зернистых материалов.
Гидродинамическая сущность процесса псевдоожижения заключается в следующем. Если через слой зернистого материала, расположенного на поддерживающей перфорированной решетке аппарата, проходит поток псевдоожижающего агента (газа или жидкости), то состояние слоя оказывается различным в зависимости от скорости этого потока.
При плавном увеличении скорости от «0» до некоторого первого критического значения происходит обычный процесс фильтрования, при котором твердые частицы неподвижны (рис. 4.16, а). На графике процесса псевдоожижения (рис.4.17), называемом кривой псевдоожижения и выражающем зависимость перепада статического давления в слое зернистого материала от скорости псевдоожижающего агента, процессу фильтрации соответствует восходящая ветвь ОА.
Δр
![]() |
А В
ΔрСП
а б в 0 WПС Wy W
|
|
Переход от режима фильтрации к состоянию псевдоожижения соответствует на кривой псевдоожижения критической скорости псевдоожижающего агента Wпс (точка А, рис. 4.17, называемой скоростью начала псевдоожижения.
Начиная со скорости псевдоожижения и выше сопротивление слоя DРсп сохраняет практически постоянное значение и зависимость DР = f(W) выражается прямой АВ, параллельной оси абсцисс. Это объясняется тем, что с ростом скорости псевдоожижающего агента контакт между частицами уменьшается и они получают большую возможность хаотического перемешивания по всем направлениям. При этом возрастает среднее расстояние (просветы) между частицами, т.е. увеличивается порозность слоя, а следовательно его высота h. Порозность неподвижного слоя e0 – это отношение
e0 = (V0 – V) /V0,
где Vи V0– объем неподвижного слоя и объем частиц.
В зависимости от свойств псевдожижающего потока и его скорости можно наблюдать несколько стадий процесса псевдоожижения. При скоростях псевдоожижающего агента, незначительно превышающих критическую скорость Wпс, т.е. при W ³ Wпс, наблюдается так называемое однородное («спокойное») псевдоожижение (рис. 4.16,б).
По мере роста скорости при псевдоожижении газов в слое возникают компактные массы газа («пузыри», «каверны»), интенсивно турбулизирующие твердые частицы и образующие всплески зернистого материала на поверхности. При этом наблюдаются значительные пульсации статического и динамического напора псевдоожижающего агента. Такой характер гидродинамики слоя называется неоднородным псевдоожижением (рис. 4.16, в).
Наконец, при достижении некоторого второго критического значения скорости Wу, называемой скоростью уноса, твердые частицы начинают выноситься из слоя и их количество в аппарате уменьшается. Порозность такого слоя стремится к 1, и сопротивление слоя правее точки В (рис. 4.16) также падает.
Рассмотренный нами график называют кривой идеального псевдоожижения.
На практике действительная кривая псевдоожижения отличается от идеальной кривой (крутизной восходящей ветви и всплеском давления при начале псевдоожижения, определяемых, в основном, плотностью упаковки твердых частиц).
В настоящее время в связи с огромной важностью процессов псевдоожижения разрабатываются все новые и новые аппараты, учитывающие специфические особенности взаимодействующих веществ.
Наряду с обычными цилиндрическими аппаратами нашли широкое применение конические аппараты. Значительная скорость псевдоожижающего агента внизу аппарата дает возможность работать без поддерживающей решетки, что особенно важно для высокотемпературных процессов, агрессивных сред, а также при использовании комкующихся и слипающихся материалов.
Аппараты с псевдоожиженным слоем, как и все остальные технологические аппараты, могут быть периодического и непрерывного действия. В периодически действующих аппаратах твердые частицы не выводятся до своей полной отработки.
В аппаратах непрерывного действия осуществляется противоток зернистого материала, т.е. происходит постоянный вывод отработанных твердых частиц их замена их свежим зернистым материалом.
В тех случаях, когда нужно получить противоток зернистого материала и псевдоожижающего агента, в аппаратах непрерывного действия применяется последовательное секционирование на каскад последовательно расположенных слоев. В таких секциях происходит переход твердой фазы с верхних слоев на нижние под действием силы тяжести, либо через специальные перетоки, либо через отверстия в провальных тарелках, живое сечение которых составляет 15 – 30%.
Тепловые процессы
4.4.1. Общая характеристика тепловых процессов
Технологические процессы, скорость протекания которых определяется скоростью подвода или отвода тепла, называются тепловыми процессами, а аппаратура, предназначенная для проведения этих процессов, называется тепловой, или теплоисполъзующей, аппаратурой. К тепловым процессам относятся нагревание, охлаждение, испарение и конденсация.
Нагревание — повышение температуры перерабатываемых материалов путем подвода к ним тепла.
Охлаждение — понижение температуры перерабатываемых материалов путем отвода от них тепла.
Конденсация — сжижение паров какого-либо вещества путем отвода от них тепла.
Испарение — перевод в парообразное состояние какой-либо жидкости путем подвода к ней тепла.
Частным случаем испарения является весьма широко распространенный в химической технике процесс выпаривания — концентрирования при кипении растворов твердых нелетучих веществ путем удаления жидкого летучего растворителя в виде паров.
В тепловых процессах взаимодействуют не менее чем две среды с различными температурами, при этом тепло передается самопроизвольно (без затраты работы) только от среды с большей температурой к среде с меньшей температурой.
Среда с более высокой температурой, отдающая при теплообмене тепло, называется теплоносителем, среда с более низкой температурой, воспринимающая при теплообмене тепло, называется холодильным агентом (хладоагентом).
В химической технике приходится осуществлять тепловые процессы при самых различных температурах — от близких к абсолютному нулю до нескольких тысяч градусов. Для каждого конкретного процесса, протекающего в определенном интервале температур, подбираются наиболее подходящие теплоносители и хладоагенты. Выбранные теплоносители и хладоагенты должны быть вполне химически стойкими в рабочих условиях процесса, не давать отложений на стенках аппаратов, не вызывать коррозии аппаратуры и легко транспортироваться по трубам.
Перечень наиболее распространенных в химической технике теплоносителей и хладоагентов с указанием условий их применения приведен в табл. 4.1.
Таблица 4.1.
Наиболее распространенные теплоносители (хладоагенты)
Теплоносители (хладоагенты) | Рабочие условия в установках | |
Температура, 0С | Давление, атм. | |
Азот, кислород, воздух | До – 210 | До 200 |
Этан, этилен, фреоны | От – 70 до – 150 | До 40 |
Вода | От 0 до 100 От 100 до 374 | 1 – 225 |
Насыщенный водяной пар | От 0 до 250 | От 1 до 40 |
Дымовые (топочные) газы | От 420 до 1000 | |
Твердые теплоносители (шамот, и др) | До 1500 |
Основной характеристикой любого теплового процесса является количество передаваемого в процессе тепла; от этой величины зависят размеры тепловой аппаратуры. Основным размером теплового аппарата является теплопередающая поверхность, или поверхность теплообмена.
Часто в процессе теплообмена нагреваемые или охлаждаемые материалы изменяют агрегатное состояние: испаряются, конденсируются, плавятся или кристаллизуются. Особенности таких процессов теплообмена заключаются в том, что тепло подводится к материалам или отводится от них при постоянной температуре и распространяется не в одной, а в двух фазах.
5.4.2. Нагревание
Нагревание широко применяется в химической технике для ускорения многих массообменных процессов и химических превращений. В зависимости от температурных и других условий проведения процесса применяются разнообразные методы нагревания. Для каждого конкретного процесса приходится выбирать наиболее оправданный в технологическом и экономическом отношении метод нагревания.
Наибольшее распространение в химической технике получили следующие методы нагревания: водяным паром, топочными газами, промежуточными теплоносителями, электрическим током.
НАГРЕВАНИЕ ВОДЯНЫМ ПАРОМ
Для нагревания применяется преимущественно насыщенный водяной пар при абсолютных давлениях до 10—12 ат. Использование пара большего давления требует сложной и дорогостоящей аппаратуры, что, как правило, экономически не оправдывается. Соответственно абсолютному давлению 10—12 атнагревание насыщенным водяным паром ограничено температурой —180°С. В процессе нагревания насыщенный пар конденсируется, выделяя при этом тепло, равное теплоте испарения жидкости.
Довольно широкому распространению способа нагревания водяным паром способствовали преимущества этого метода обогрева, а именно:
1) большое количество тепла, выделяющегося при конденсации единицы водяного пара (539—476 ккал на 1 кг конденсирующегося пара при абсолютных давлениях соответственно 1—12 ат);
2) равномерность обогрева, так как конденсация пара происходит при постоянной температуре.
Нагревание «острым» паром.При нагревании «острым» паром водяной пар вводится непосредственно в нагреваемую жидкость; конденсируясь, он отдает тепло нагреваемой жидкости, а конденсат смешивается с жидкостью.
Для одновременного нагревания и перемешивания жидкости пар вводится через барботер — трубу с рядом небольших отверстий. Барботер располагают на дне резервуара в виде спирали (рис. 4.18)
![]() |
![]() |
|
При обогреве «острым» паром происходит неизбежное разбавление нагреваемой жидкости конденсатом — водой. Обычно этот способ применяют для нагревания воды и водных растворов.
Нагревание «глухим» паром.Если нагреваемая жидкость взаимодействует с водой, контакт между ними недопустим или нельзя разбавлять нагреваемую жидкость, применяют нагревание «глухим» паром. В этом случае жидкость нагревается паром через разделяющую их стенку в аппаратах с рубашками, со змеевиками и т. д.
Греющий «глухой» пар целиком конденсируется и выводится из парового пространства нагревательного аппарата в виде конденсата. Температура конденсата может быть принята с достаточной точностью равной температуре насыщенного греющего пара.
Дата добавления: 2021-07-22; просмотров: 502;