Технологія коксохімічного виробництва
Кокс – твердий матово-чорний, пористий продукт. З 1 т сухої шихти одержують 650-750 кг коксу. Він використовується головним чином у чорній і кольоровій металургії, ливарному виробництві, а також для газифікації, виробництва карбіда кальцію, електродів, як реагент і паливо в ряді галузей хімічної промисловості. Коксу необхідно мати достатню механічну тривкість, тому що він може руйнуватися в металургійних печах під тиском стовпа шихти, що порушує їхню нормальну роботу, знижує продуктивність і т. ін.; його теплотворна спроможність має становити 31,4-33,5 МДж/кг. Кокс одержують на коксохімічних заводах шляхом розкладання коксівного вугілля без доступу повітря. Показниками якості коксу є горючість і реакційна спроможність. Перший характеризує швидкість горіння коксу, другий – швидкість відновлення ним двоокису вуглецю. Обидва ці процеси гетерогенні, швидкість їх визначається не тільки складом коксу, але і його шпаристістю, тому що від неї залежить поверхня контакту взаємодіючих фаз. Якість коксу також характеризується вмістом у ньому сірки, золи, вологи і виходом летючих.
Сірка, що міститься в коксі, при доменній плавці переходить у чавун, погіршуючи його якість. Допустимий вміст сірки в коксі – 1,2-1,7 %. Зола у коксі – це баласт, і вміст її дорівнює приблизно 17 %. Вихід летючих речовин із коксу складає біля 1,0 %. У коксі припустимо до 5 % вологи, тому що збільшення вологості знижує його теплотворну спроможність.
Коксовий газ утворюється в кількості 310-340м3на 1 т сухого вугілля. Склад і вихід коксового газу визначаються головним чином температурою коксування. З камери, в якій відбувається коксування, виходить так називаний прямий коксовий газ, що містить газоподібні продукти, пари кам’яновугільної смоли, сирого бензолу і води. Після видалення з нього смоли, сирого бензолу, води й аміаку утворюється так називаний зворотний коксовий газ, що використовується як сировина для хімічних синтезів. Крім цього коксовий газ застосовується для обігріву коксових, сталеплавильних та інших печей.
Кам’яновугільна смола– в’язка чорно-бура, із специфічним запахом рідина, що містить біля 300 різноманітних речовин. Найціннішими компонентами смоли є бензол, толуол, ксілоли, фенол, крезоли, нафталін, антрацен, фенантрен, піридин, карбазол, кумарон та ін. Щільність смоли 1,7-1,20 г/см3. Вихід смоли складає від 3 до 4 % від маси сухого вугілля, що коксується. Склад смоли залежить головним чином від температури коксування, а вихід – від температури і природи вихідного вугілля. З підвищенням температури поглиблюється піроліз вуглеводнів, що знижує вихід смоли і збільшує вихід газу. З кам’яновугільної смоли виділяють біля 60 продуктів, використовуваних як сировину для виробництва барвників, фармацевтичних препаратів, інсектофунгіцидів, пластичних мас, хімічних волокон і т. ін.
Сирий бензол– це суміш, що складається із сірковуглецю, бензолу, толуолу, ксилолів, кумарону й інших речовин. Вихід сирого бензолу складає в середньому 1,1 % від маси вугілля. Вихід залежить від складу і властивостей вихідного вугілля і температурних умов процесу. При розгонці із сирого бензолу одержують індивідуальні ароматні вуглеводні й суміші вуглеводнів, що служать сировиною для хімічної промисловості.
Смола і сирий бензол є головними джерелами одержання ароматних вуглеводнів для хімічної промисловості.
Надсмольна вода являє собою слабкий водяний розчин аміаку й амонійних солей із домішкою фенолу, піридинових основ і деяких інших продуктів. З надсмольної води у процесі її переробки виділяється аміак, що разом з аміаком коксового газу використовується для одержання сульфату амонію і концентрованої аміачної води.
Коксування є одним із найстаріших хімічних виробництв. До середини XIX ст. коксування проводилося для виробництва коксу для металургії. З другої половини XIX ст. після одержання в Росії Н.Н. Зініним аніліну з нітробензолу знадобилися бензол, толуол, феноли, крезоли, нафталін, антрацен й інші продукти, що містяться в кам’яновугільній смолі та сирому бензолі. Кам’яновугільна смола й сирий бензол перетворюються з відходів виробництва на основні і найважливіші продукти. Майже на всіх заводах будуються установки, які вловлюють кам’яновугільну смолу і сирий бензол. Таким чином створюються єдині коксохімічні виробництва.
Сировиною для коксування служить спікливе вугілля, що дає тривкий і пористий металургійний кокс, наприклад, коксівне вугілля марки К. У промисловій практиці звичайно складається суміш-шихта, що складається не тільки з коксівного вугілля, але й з вугілля інших марок. Це дозволяє розширити сировинну базу коксохімічної промисловості, одержати якісний кокс і забезпечити високий вихід смоли, сирого бензолу і коксового газу. У вугіллі, що використовується для коксування, кількість вологи має бути в межах 5...9 %, золи – до 7 %, сірки – до 2 %.
Технологічний процес хімічного виробництва починається з підготовки сировини і готування шихти. Вугілля, що надходить на підприємство, розподіляється за складом і властивостями на групи, дробиться і перемішується, потім проходить стадію збагачення шляхом просівання, знепилення, флотації та інших процесів, здійснюваних для усунення сторонніх домішок.
Далі компоненти шихти піддаються сушінню й остаточному роздрібненню до крупності зерен не більш 3 мм. Підготовлені компоненти шихти подаються в змішувальні машини, а потім у бункери-накопичувачі вугільної вежі.
Готова шихта визначеними дозами висипається в бункери
завантажувального вагона, який доставляє її в камери коксової
батареї (рис. 6.1).
|
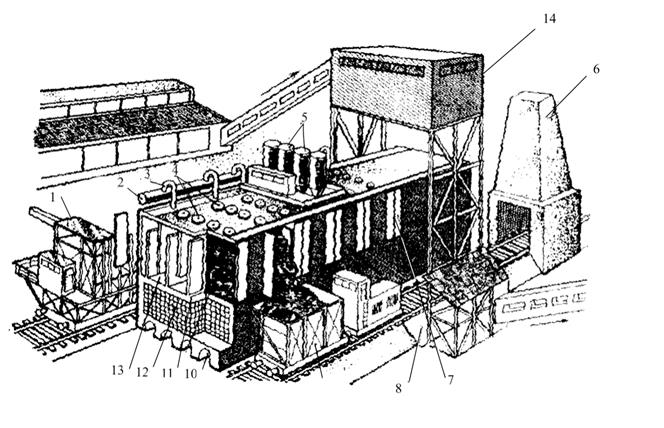
Рис. 6.1.Будова коксової батареї:
1 – коксовиштовхувач; 2 – газозбірник; 3 – стояк; 4 – люк;
5 – завантажувальний вагон; 6 – вежа для гасіння;
7 – герметичні двері; 8 – рампа; 9 – гасильний вагон;
10 – газопровід; 11 – коксова камера; 12 – регенератор;
13 – простінок; 14 – вугільна вежа.
Нагрівання вугілля супроводжується фізичними і хімічними перетвореннями: до 250°С випаровується волога, виділяються окис і двоокис вуглецю; біля 300ºС починається виділення парів смоли й утворення так званої пірогенетичної води; вище 350°С вугілля переходить у пластичний стан; при 500-550°Сспостерігається розкладання пластичної маси з виділенням первинних продуктів (газу і смоли) та її затвердіння з утворенням напівкоксу. Підвищення температури до 700°С призводить до розкладання напівкоксу, виділенню з нього газоподібних продуктів; вище 700°С переважно відбувається зміцнення коксу. Летючі продукти, стикаючись із розпеченим коксом, нагрітими стінками і склепінням камери, в якій відбувається коксування, перетворюються на складну суміш парів (переважно зі з’єднань ароматного ряду) і газів, що містять водень, метан та ін. Велика частина сірки вихідного вугілля і всіх мінеральних речовин залишається в коксі.
Устрій і робота коксових печей – апаратів непрямого нагрівання, в яких тепло нагрівальних газів до коксівного вугілля передається через стінку. Основним чинником, що визначає протікання процесу коксування, є підвищення температури, що необхідно для нагрівання шихти до температури сухої перегонки і проведення ендотермічних реакцій коксування. Підвищення температури обмежується зниженням виходу смоли і сирого бензолу, зміною складу продуктів коксування, порушенням тривкості вогнетривких матеріалів, використовуваних для кладки печей.
Коксова піч або батарея (рис. 6.1)складається з 61-69 паралельно працюючих камер 11, що являють собою довгі, вузькі канали прямокутного перетину, викладені з вогнетривкої цегли (динасу). Кожна камера вміщує від 15 до 23 т шихти, має передню й задню знімні двері, що у момент завантаження камери щільно закриті, а знімаються при розвантаженні коксу. У склепінні камери є завантажувальні люки 4, що відчиняються при завантаженні вугілля і закриваються на період коксування. Рейковим шляхом, розташованим над коксовими камерами, переміщується завантажувальний вагон 5, який через завантажувальні люки подає шихту в коксові камери. Уздовж одного із боків батареї рейковим шляхам переміщується коксовиштовхувач 1 – машина, що після закінчення процесу коксування розкриває двері камери і виштовхує кокс. З іншого боку рейковим шляхом переміщується гасильний вагон 9, що приймає розпечений кокс, транспортує його під вежу гасіння 6 і потім вивантажує на рампу 8. Нагрівання вугілля в камері відбувається через стінки камери димовими газами, що проходять обігрівальними простінками, розташованими між камерами. Гарячі димові гази утворюються в результаті спалювання доменного, зворотного коксового або рідше генераторного газів. Тепло димових газів, що виходять з обігрівального простінка, використовується в регенераторах 12 для нагрівання повітря і газоподібного палива, що надходять на обігрів коксових печей, у результаті чого збільшується тепловий ККД печі. При роботі коксової камери для забезпечення рівномірності прогріву вугільного завантаження необхідно правильно вибрати габарити камери і рівномірно розподілити нагрівальні гази в обігрівальному простінку. Ширина камери звичайно складає 400-450 мм. Довжина камери обмежується статичною міцністю простінків, утрудненням видалення коксу з камери, складністю розподілу газів в обігрівальному простінку. Довжина камери дорівнює приблизно 14 м. Висота камери визначається в основному умовами рівномірного обігріву її за висотою. З цього погляду задовільні результати утворюються якщо висота камери біля 5,5 м.
Рівномірний розподіл гріючих газів досягається поділом обігрівальних простінків вертикальними перегородками на ряд каналів, називаних вертикалами. Нагрівальні гази рухаються вертикалами, що віддають тепло стінкам камери й надходять у регенератори. Різниця температури між нагрівальними газами в обігрівальному каналі і вугільній шихті змінюється з часом. Після завантаження камери шихтою значення її велике, у холодну шихту в одиницю часу надходить велика кількість тепла, і вугілля біля стінок камер починае коксуватися. Проте середні прошарки шихти при цьому залишаються холодними.
У міру того, як вугілля прогрівається, різниця температур поступово зменшується, кількість переданого тепла в одиницю часу падає, але усе ж внаслідок безупинного притоку тепла від газів відбувається поступове підвищення температури за перетином камери. Тому створюється наступний стан матеріалів у камері під час коксування (рис.6.2):біля стінок формується прошарок коксу, далі при зниженні температури від стінок до осі камери розташовується прошарок напівкоксу, потім вугілля, яке ще в пластичному стані, і, нарешті, в центрі камери незмінна шихта. Через 12-14 годин температура за перетином вирівнюється, прошарки переміщуються до осі камери і поступово вугільне завантаження прококсовується. Таким чином, після закінчення процесу коксування нагрівальні устрої відключаються, стояки переключаються, до дверей камери підводиться виштовхувач, який вивантажує коксовий “пиріг” у гасильний вагон, що повільно рухається уздовж батареї. Виштовхувач навішує двері звільненої камери і рушає до наступної камери, а завантажувальний вагон відчиняє люки і завантажує нову дозу шихти.
Розвантаження-завантаження камери триває близько 15 хвилин, тому для раціонального використання механізмів кількість камер у батареї доводять до 70.
Вивантажений кокс піддається гасінню, через те, що при зіткненні з повітрям він загоряється.
Гасильний вагон доставляє його у вежу, де кокс після гасіння водою висипається на рампу, остигає протягом 20 хв. Остиглий кокс транспортується на сортування.
|
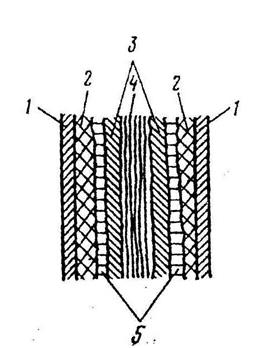
Вихід коксу становить 70-80% від маси шихти. Продуктивність однієї коксової батареї – біля 1500 т коксу на добу. Залежно від призначення кокс поділяється на доменний, ливарний, енергетичний (призначений для одержання феросплавів, карбіду кальцію, електродів, для агломерації залізних руд).
Вихід продуктів із 1 т шихти, %,
Дата добавления: 2021-07-22; просмотров: 656;