Многоэлектродная и многодуговая наплавка
Большой объем наплавочных работ требует разработки и применения более производительных механизированных приемов наплавки. Не говоря о ручной, даже автоматическая однодуговая наплавка под флюсом часто не обеспечивает требуемой производительности.
Повысить производительность можно за счет применения многоэлектродной наплавки (рис. 1.4). При многоэлектродной наплавке одновременно осуществляется подача нескольких электродов, подключенных параллельно к одному выводу источника сварочного тока (рис. 1.4, а). В отличие от многоэлектродной сварки при наплавке электроды располагают не вдоль шва, а в линию, перпендикулярную движению наплавочного аппарата. Дуга периодически перемещается с одного электрода на другой; при этом образуется общая сварочная ванна с небольшой глубиной проплавления основного металла, и формируется широкий валик. Повышение производительности достигается за счет применения большей силы тока без опасного увеличения глубины проплавления и за счет формирования широких валиков.
|
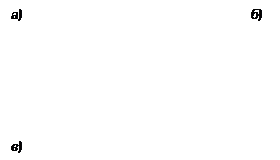
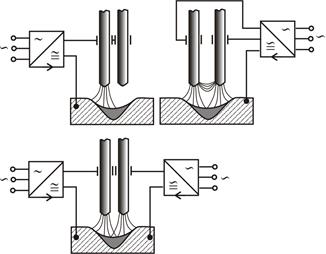
На практике часто используют наплавку двумя одновременно горящими дугами с общим и раздельным плавильным пространством; расщепленным электродом и наплавку трехфазной дугой (рис. 1.4, б, в) [8]. Изменяя характер воздействия дуги на жидкий металл сварочной ванны, можно при той же мощности добиваться существенного изменения глубины ее проплавления и ширины.
Размеры сварочной ванны при наплавке несколькими электродами с общим подводом тока определяются главным образом величиной силы тока, приходящейся на один электрод. На рис. 1.5 показана форма сварочной ванны при наплавке на одинаковых параметрах режима одним, двумя и тремя электродами [9]. Увеличение числа электродов при неизменной силе тока позволяет уменьшить глубину проплавления основного металла, увеличить ширину и сократить длину сварочной ванны. Изменение формы ванны, достигаемое таким путем, используется при многоэлектродной наплавке плоских поверхностей или тел вращения большого диаметра.
С другой стороны, увеличение числа электродов позволяет увеличить производительность наплавки путем увеличения силы тока, без ухудшения качества наплавленного слоя.
При многодуговой наплавке (рис. 1.4, в) применяется одновременно несколько наплавочных аппаратов или один аппарат с несколькими изолированными друг от друга электродами, причем каждый электрод питается от отдельного источника тока. Каждая дуга может формировать свой валик, общая ванна при этом не образуется. Производительность наплавки повышается за счет применения нескольких сварочных дуг сравнительно небольшой мощности при обслуживании процесса одним оператором.
![]() |
Повысить производительность и рассредоточить тепловложение в основной металл, уменьшив глубину проплавления, можно применяя известный способ многоэлектродной наплавки (рис. 1.6) [16].
В этом способе расстояния между электродами (а и в) являются главными факторами, определяющими, при прочих равных условиях, глубину проплавления и долю основного металла в наплавленном покрытии. Кроме того, сообщая дополнительное колебательное движение наплавочной головке, удается получить валик шириной до 120 мм. Производительность процесса при скорости наплавки 1,9¸2,2 мм/с (7¸8 м/час) достигает
40 кг/час [16].
Однако для этого способа характерны значительные трудности в управлении процессом, в обеспечении необходимого качества формирования поверхности наплавленного слоя и снижении доли основного металла в наплавленном, которая достигает 30 %, что в целом ограничивает его применение.
К недостаткам описанных выше способов широкослойной наплавки следует отнести высокую сложность механизмов перемещения электродов за счет необходимости электрической изоляции отдельных электродов, сложности обеспечения одновременной надежной и стабильной их подачи (рис. 1.7) [70], трудоемкость заправки электродов в механизм подачи и стабильность возбуждения дуги в начале процесса.
![]() |
Устранить или существенно уменьшить указанные недостатки можно, применив наплавку ленточным электродом.
Дата добавления: 2016-10-26; просмотров: 3565;