Метод измерения твердости по Бринеллю
Сущность метода заключается во вдавливание шарика диаметром
(стального закаленного или из твердого сплава) в образец или изделие под воздействием нагрузки
, приложенной перпендикулярно поверхности образца, в течение определенного времени и измерении диаметра отпечатка
после снятия нагрузки (рис. 2.1, а).
Диаметр образующегося сферического отпечатка измеряется лупой-компаратором (с помощью микроскопа). На рис. 2.2 показан общий вид микроскопа МПБ-3, предназначенный для измерения твердости по Бринеллю.
Рис. 2.2. Микроскоп МПБ-3 |



Для случая измерения нагрузки в килограммах:
. (2.1)
Для случая измерения нагрузки в ньютонах:
, (2.2)
где ; (2.3)
– угол вдавливания, т.е. угол между двумя радиусами шарика, проведенными к концам отпечатка (рис. 2.3).
Рис. 2.3. Схема вдавливания шарика в образец или изделие
Согласно формулам (2.1) и (2.2) для получения одинаковой твёрдости при использовании шариков различных диаметров (ГОСТ допускает применение диаметром 1,0; 2,0; 2,5; 5,0 и 10 мм) необходимо, чтобы угол вдавливания (рис. 2) оставался неизменным при постоянном отношении нагрузки к квадрату диаметра шарика, которое обозначается через величину
:
, кг/мм2, (2.4)
Н/мм2. (2.5)
Для выбора значений при испытании различных материалов рекомендуется пользоваться данными табл. 2.1. Определившись значением
и диаметром шарика
, используемого при испытаниях, по табл. 2.2 выбирают нагрузку
.
Согласно ГОСТу твёрдость по Бринеллю, при использовании шарика =10 мм под нагрузкой
=29420 Н (3000 кг) с продолжительностью выдержки под нагрузкой от 10 до 15 секунд, обозначается цифрами, характеризующими величину твёрдости, и буквами
, например: 185
. При других условиях испытания после букв
указывается условие испытания в следующем порядке: диаметр шарика, нагрузка и продолжительность выдержки под нагрузкой, например: 185
5/750/20 – твёрдость по Бринеллю, определённая с применением шарика
=5 мм, при нагрузке
=750 кг и продолжительности выдержки под нагрузкой 20 с. Размерность числа твёрдости во всех случаях опускается.
Таблица 2.1. Значения коэффициента
Металлы и славы | ![]() | ![]() |
Железо, сталь, чугун и другие высокопрочные сплавы | 96…450 | |
Титан и его сплавы | 50…220 | |
Алюминий, медь, никель и их сплавы | 32…200 | |
Магний и его сплавы | 16…100 | |
Подшипниковые сплавы | 2,5 | 8…50 |
Олово, свинец | 3,2…20 |
Таблица 2.2. Значения нагрузки ,Н (кг)
Диаметр шарика ![]() | ![]() | |||||
2,5 | ||||||
294,2 (30) | – | 98,07 (10) | 49,03 (5) | 24,52 (2,5) | 9,81 (1) | |
(120) | – | 392,3 (40) | 196,1 (20) | 98,07 (10) | 39,23 (4) | |
2,5 | (187,5) | – | 612,9 (62,5) | 306,0 (31,2) | 153,0 (15,6) | 60,80 (6,2) |
(750) | – | (250) | (125) | 612,9 (62,5) | 245,2 (25) | |
(3000) | (1500) | (1000) | (500) | (250) | 980,7 (100) |
Диаметр шарика и нагрузку следует выбирать так, чтобы диаметр отпечатка находился в пределах . При несоблюдении этих требований необходимо изменить условия испытаний (
и
).
Следует иметь в виду, что по Бринеллю нельзя определять твёрдость очень мягких (
) и очень твёрдых материалов (
). В мягких материалах шарик погрузится очень глубоко, диаметр отпечатка будет близок к диаметру шарика
и перестанет служить критерием твёрдости. Наоборот, если твёрдость материала будет очень большой, величина отпечатка получится маленькой и края его будут столь нечёткими, что не удастся точно измерить диаметр отпечатка, к тому же шарик может получить остаточную деформацию, искажающую результаты испытания.
Рис. 2.4. Схема измерения отпечатка |
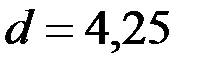
По числу твердости вычисляют предел прочности материала, поскольку между пределом прочности (см. п. 1) и числом твердости НВ различных металлов существуют эмпирические зависимости (см. Приложение 7.2).
Дата добавления: 2016-05-31; просмотров: 2782;