Прокатное производство.
Прокатка– это обработка давлением, при которой исходная заготовка (слиток или отливка) под действием сил трения непрерывно втягивается между вращающимися валками и пластически деформируется с уменьшением толщины и увеличением длины, а иногда и ширины. Почти 90% всей выплавляемой стали и значительная часть цветных металлов подвергается прокатке. В зависимости от формы и расположения валков, а также заготовок по отношению к ним различают продольную, поперечную и поперечно-винтовую прокатки (рис. 5.3).
|




|
|
|


|

|


|

|
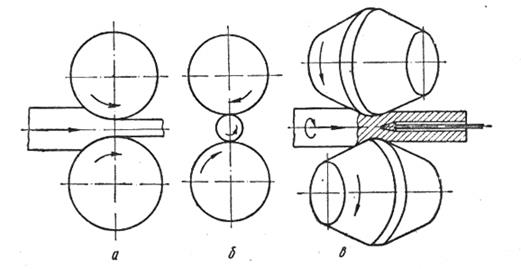
Рис. 5.3. Схема основных видов прокатки
а – продольная; б – поперечная; в – поперечно-винтовая
1 – заготовка; 2 – валки; 3 – оправка
При продольной прокатке (рис. 5.3,а) заготовка 1 деформируется между двумя валками 2, вращающимися в разные стороны, и перемещается в направлении, перпендикулярном осям валков.
При поперечной прокатке (рис. 5.3,б) валки 2 вращаются в одном направлении, а заготовка 1, имеющая форму тела вращения, перемещается параллельно осям валков и обжимается по образующей с увеличением длины и уменьшением площади поперечного сечения.
При поперечно-винтовой прокатке (рис. 5.3,в) валки 2 расположены под углом друг к другу, вращаются в одну сторону и при обжатии заготовки 1 сообщают ей вращательное и поступательное движения.
В промышленности поперечную прокатку используют главным образом для получения специальных периодических профилей. Винтовую прокатку широко применяют для получения пустотелых трубных заготовок.
Инструментом прокатки являются валки, которые могут быть не только гладкими (рис. 5.4), но и с фигурными вырезами – ручьями. Совокупность соответствующих вырезов в верхнем и нижнем валках образуют калибр. Калибры могут быть открытыми и закрытыми (рис. 5.4). Пример калибров различного вида проката приведен на рис. 5.5. Комплект прокатных валков со станиной называют рабочей клетью.
![]() ![]() | ![]() |
Рис. 5.4. Прокатные валки и калибры: а – гладкий; б – с фигурными вырезами; в – калибр открытый; г – калибр закрытый | Рис. 5.5. Схемы калибров для получения различного вида проката 1 – полоса; 2 – швеллер; 3 – двутавр; 4 – уголок равнополочный; 5 – уголок неравнополочный; 6 – тавр |
По числу и расположению валков в клетях, прокатные станы подразделяют на дуо-, трио-, кварто-, многовалковые и универсальные (рис. 5.6).
Рис. 5.6. Рабочие клети прокатных станов:
а – дуо; б – трио; в – кварто; г – многовалковый; д – универсальные
Производство проката разделяют на две основные стадии:
1) получение полупродукта (блюмов, слябов и заготовок) из слитка;
2) получение готовых изделий из полупродуктов.
Блюмы – заготовки квадратного сечения от 450×450 до 150×150 мм2, получаемые на блюминге в результате прокатки слитков, предварительно подогретых до 13000С.
Слябы – заготовки прямоугольного сечения максимальной толщины до 350 мм и шириной до 2300 мм, идущие для прокатки на толстый лист.
На рис. 5.7 представлена технологическая схема прокатки литых слитков и заготовок и получения из них готового проката: толстых и тонких листов, рельсов, балок, швеллеров, угловой и круглой стали, проволоки и т.п.
После прокатки на слябинге часть проката направляется на заготовочные станы. Полученные полосы режут на мерные куски необходимой длины – сутунки. Последующая обработка включает отделочные операции: зачистку, травление, удаление поверхностных дефектов. Полученные заготовки направляются на сортовые и листопрокатные станы. На сортовых станах заготовка после нагрева в печах последовательно проходит прокатку в 7…15 калибрах, в последнем из которых получают требуемый профиль (рис. 5.8).
Рис. 5.7. Общая схема технологического процесса в прокатных цехах
Рис. 5.8. Последовательность проката рельса на сортопрокатном стане
Современная технология позволяет получать непрерывной холодной прокаткой листы толщиной менее 0,1 мм с суммарным обжатием до 80…90% без промежуточной термической обработки.
Прокаткой освоено производство бесшовных и сварных труб как из стали, так и цветных металлов. Бесшовные изготовляют диаметром 30…650 мм с толщиной стенки от 2 до 160 мм, сварные – диаметром от 5 до 2500 мм.
Возможно получение профилей специального назначения. Например, шары для подшипников, заготовки для шатунов, цельнокатаные вагонные колеса и др.
Форму поперечного сечения продукции, получаемой при прокатке, называют профилем. Совокупность форм и размеров профилей называют сортаментом.
Сортамент проката подразделяется на группы: сортовой прокат, листовой, трубы и профили специального назначения (рис. 5.9).
В свою очередь, сортовой прокат по форме сечения разделяют на простой (рис. 5.9, п.1…4): круг, квадрат, шестигранник, полоса и др.; фасонный (рис. 5.9, п.5…9, рис. 5.10) – уголки, тавры и двутавры, рельсы, швеллеры, арматура и др. и сложный специальный(рис. 5.9, п.10…13): шпунтовый, зетовый, кольцо автообода, автообод и др.
Листовой прокат подразделяют на толстолистовой (4 мм и более) и тонколистовой (менее 4 мм). Помимо листов с гладкой поверхностью промышленностью выпускается листовая сталь с ромбическим и чечевичным рифлением (рис. 5.11), которая в основном применяется в качестве настила рабочих площадок и ступеней металлических лестниц.
К продукции «крупносортная сталь» относятся: круглая сталь диаметром более 30 мм; квадратная сталь со стороной квадрата свыше 30 мм; полосовая сталь шириной более 56 мм; угловая равнополочная сталь размером 50х50 мм и более; угловая неравнополочная размером 70х45 мм и более; периодическая арматура Æ32 и более.
![]() |
![]() ![]()
![]()
| |||||||
Рис. 5.9. Профили сортовой стали: 1 – квадратный; 2 – круглый; 3 – полосовой; 4 – шестигранный; 5 – угловой; 6 – тавровый; 7 – балочный (двутавровый); 8 – швеллерный; 9 – рельсовый; 10 – шпунтовый; 11 – зетовый; 12 – кольцо автообода; 13 – автообод | ||||||||
Рис. 5.10.Арматурный прокат а) арматура гладкая класса А-I (A240); б), в) арматура периодического профиля: – класса А-II (А300) (б); – класса A-III (А400), A-IV (А600), A-V (А800), A-VI (А1000) (в) |
|
|

К продукции «среднесортная сталь» относятся: круглая сталь диаметром от 20 до 30 мм включительно; квадратная сталь со стороной квадрата от 20 до 30 мм включительно; полосовая сталь шириной 50…56 мм включительно; угловая равнополочная сталь размерами 36х36, 40х40, 45х45 мм; угловая неравнополочная размерами 45х28, 50х32, 56х36, 63х40 мм; периодическая арматура Æ20…28.
К продукции «мелкосортная сталь» относятся: круглая сталь диаметром 10…19 мм включительно; квадратная сталь со стороной квадрата 10…19 мм включительно; полосовая сталь шириной 12…45 мм включительно; угловая равнополочная сталь размерами 20х20, 25х25, 28х28, 32х32 мм; угловая неравнополочная размерами 25х16, 32х20, 40х25 мм; периодическая арматура Æ10…18 мм.
Используя сортовой прокат, можно изготовить составное сечение элемента конструкции (рис. 5.12), а также путем последующей технологической обработки листового или полосового проката (гибки, сварки и пр.) изготовить вторичный профиль (гнутые уголок, швеллер, профнастил, С-образный профиль, зетовый профиль, W-профиль, гнутосварные трубы квадратного и прямоугольного сечения, электросварные трубы прямошовные, сварные двутавры, просечно-вытяжные листы, стальные канаты и др.) (рис. 5.13).
Рис. 5.12. Основные типы прокатных стальных профилей
а – сортамент (предельные размеры в мм): 1-2 – уголки равнополочный и неравнополочный; 3 – двутавр; 4 – то же, широкополочный; 5 – швеллер; 6 – то же с параллельными гранями полок; 7 – широкополочный тавр; 8 – труба;
б – примеры составных сечений
|
|
|
|
|
|
|
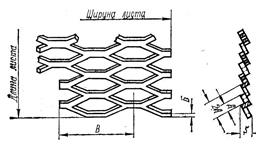
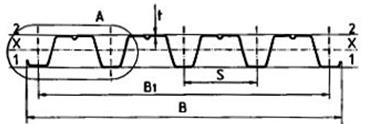
|
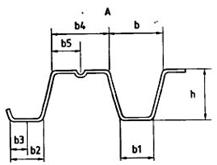
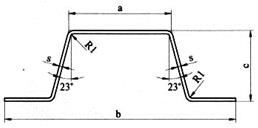
Рис. 5.13. Основные виды вторичного профиля
а – гнутый уголок; б – гнутый швеллер; в – С-образный профиль;
г – гнутосварная труба прямоугольного сечения; д – зетовый профиль;
е – просечно-вытяжной лист; ж – профилированный лист; и – W-профиль
Волочение.
Волочение– это процесс протягивания прутка или трубы через постепенно сужающееся отверстие волоки (рис. 5.1 б). Волочильный инструмент изготовляют из закаленной стали, твердых сплавов ВК2, ВК3, ВК6, ВК8, а для прецизионных изделий – из алмаза. При волочении поперечное сечение заготовки уменьшается, а ее длина соответственно увеличивается.
Волочение осуществляется главным образом в холодном состоянии и редко в горячем. Исходным материалом могут быть горячекатный пруток, сортовой прокат, проволока, трубы. Волочением обрабатывают стали, цветные металлы и сплавы. В результате волочения можно получить профили весьма точных размеров и формы, как правило, с гладкой блестящей поверхностью: тонкую проволоку диаметром 5…10 мм, тонкостенные трубы, фасонные профили и т.д. Можно получать проволоку с минимальным диаметром до 0,002 мм. Применяют волочение и для калибровки сечения и повышения качества поверхности. Волочение обеспечивает высокую точность размеров, малую шероховатость поверхности и большую степень упрочнения. После волочения изделия, как правило, не обрабатываются.
Основной инструмент при волочении сплошных профилей – волоки различной конструкции, а при волочении полых профилей – волоки и оправки к ним (рис. 5.14).
Волока 1 закрепляется в обойме 2 на жесткой волочильной доске. Волока имеет четыре зоны: входную – I, рабочую (деформирующую) – II, калибрующую (очко или поясок) – III и выходную – IV. Калибрующая зона обычно имеет цилиндрическую форму. Остальные зоны – конические.
Угол рабочего конуса деформирующей зоны выбирают в пределах 10…200, в зависимости от вида изделия и свойств деформируемого металла.
До начала волочения конец заготовки заостряют, пропускают через очко, захватывают тяговым механизмом волочильной машины, протягивающим ее через волоку, подвергая при этом деформации – обжатию и вытяжке. В зависимости от способа осуществления тяги волочильные машины подразделяются на цепные и барабанные (рис. 5.15). Основными элементами стана цепного типа является станина 1, механизм перемещения тележки 5, цепь 4, тележка с захватом 3, стойка для крепления инструмента (волоки) 2. Длина протягиваемого изделия ограничивается длиной станины и не превышает 15 м. Скорость волочения – до 2 м/с.
Барабанные станы в зависимости от назначения могут быть однобарабанными и многобарабанными. Первые применяют при волочении проволоки средних и больших диаметров Ø4…25 мм и, реже, труб. В станах многократного волочения обработка происходит последовательно в нескольких волоках (до 30 волок). Скорость волочения может достигать 20 м/с. Степень деформации при волочении, как правило, не превышает 30…35%, коэффициент вытяжки μ за один проход – 1,25…1,45.
|
|
|
|
|
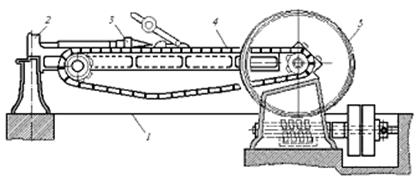
Рис. 5.15. Схема волочильного стана цепного типа
1 – станина; 2 – волока; 3 – волочильная тележка; 4 – цепь;
5 – привод волочильной тележки.
Прессование.
Прессованиемназывают процесс выдавливания находящегося в контейнере металла через одно или несколько отверстий в матрице с площадью меньшей, чем поперечное сечение исходной заготовки. Прессование обычно применяют для обработки цветных металлов и сплавов, но иногда и сталей, т.к. реализуется наиболее благоприятная схема нагружения – всестороннее сжатие.
Исходный материал для прессования – литые или прокатанные заготовки. Прессованием можно получать профили различного сечения (рис. 5.16), в том числе и прутки Ø5…300 мм, трубы Ø18…350 мм с толщиной стенок 1,5…50 мм. Различают два метода прессования: прямой и обратный (рис. 5.17).
При прямом методе прессования (рис. 5.17, а) заготовка 3 помещается в контейнер 4 пресса. С одной стороны контейнера посредством матрицедержателя 2 закреплена матрица 1 с выходным отверстием. С другой стороны контейнера имеется пуансон 5 с пресс-шайбой 6 на конце.
При обратном методе прессования (рис. 5.17, б) в контейнер 4 вместо пресс-шайбы входит полый пуансон 5 с матрицей 1 на конце.
При обратном прессовании отходы металла уменьшаются на 5…6 % и снижается усилие прессования. Однако этот метод имеет ограниченное применение из-за сложности конструкции пресса и удаления изделия из полого пуансона.
При прессовании труб (рис. 5.17, в) заготовка 3, помещенная внутрь контейнера 4, сначала прошивается стальной иглой 7. Передний конец иглы проходит через всю заготовку и выходит через отверстие матрицы 1. Между стенками отверстия матрицы и наружной поверхностью иглы образуется кольцевой зазор. При движении пуансона 5 вместе с пресс-шайбой 6 в направлении матрицы металл выдавливается в кольцевой зазор и принимает форму трубы 8.
![]() | ![]() |
Рис. 5.16. Примеры прессованных профилей | Рис. 5.17. Методы прессования: а – прямой; б – обратный; в – прессование трубы |
Методом прессования обычно получают изделия из предварительно нагретых заготовок, однако в последние годы широко применяют холодное прессование, которое обеспечивает получение точных профилей без последующей механической обработки. Этим методом получают изделия из металлов и сплавов, высокопластичных в холодном состоянии.
Свободная ковка.
Ковкойназывают процесс свободной деформации металла под циклическими ударами молота или воздействием пресса. Различают машинную и ручную свободную ковку. Ручную ковку применяют главным образом при ремонтных и сборочных работах. Машинную ковку производят с применением кузнечно-прессовых машин. Мелкие и средние по массе поковки (до 750 кг) изготовляют на молотах, а крупные (до 350 т) – на прессах. Изделия, получаемые ковкой (ограждения лестниц и балконов, крепежные детали и т.д.), зачастую требуют дальнейшей механической обработки.
Основные операции ковки (рис. 5.18): осадка, протяжка, раскатка на оправке, гибка, скручивание, рубка, пробивка, прошивка и кузнечная сварка.
Осадка – уменьшение высоты заготовки при увеличении площади ее поперечного сечения, производимая бойками или осадочными плитами.
Протяжка – удлинение заготовки или ее части за счет уменьшения площади поперечного сечения. Разновидностями протяжки являются раскатка и протяжка на оправке.
Раскатка – увеличение диаметра кольцевой заготовки при вращении за счет уменьшения ее толщины с помощью бойка и оправки.
Рис. 5.18. Операции ковки:
а – осадка; б – протяжка; в – раскатка; г – протяжка на оправке;
д – гибка; е – закручивание; ж – рубка; з – пробивка; и – прошивка.
Гибка – образование или изменение углов между частями заготовки или придание ей криволинейной формы.
Скручивание – поворот части заготовки вокруг продольной оси.
Рубка – полное отделение части заготовки.
Пробивка – образование в заготовке отверстия с удалением материала в отход путем сдвига.
Прошивка – получение полостей в заготовке за счет вытеснения материала.
Кузнечная сварка – образование неразъемного соединения под действием давления в нагретом состоянии.
Для получения крупных поковок массой до 300 т заготовками служат слитки массой до 350 т. Для более мелких поковок в качестве заготовок применяют прокат круглого либо квадратного сечения.
Ковку применяют в штучном и мелкосерийном производстве.
Дата добавления: 2020-11-18; просмотров: 801;