Повышения безопасности работ.
Радикальным средством обеспечения безопасности производственных процессов и оборудования являются механизация и автоматизация.
М е х а н и з а ц и я – это замена ручных операций применением машин и механизмов. При этом достигается не только повышение производительности труда, но и освобождение человека от выполнения тяжелых, трудоемких работ. Кроме того, механизация производственных процессов создает предпосылки для их автоматизации.
А в т о м а т и з а ц и я – высшая форма организации производства, при которой функции контроля за производственными процессами и управления (частично или полностью) ими передаются приборам и автоматическим устройствам. Это позволяет полностью исключить воздействие вредных и опасных факторов на человека, т.е. обеспечить наилучшие условия труда.
Основной целью механизации является повышение производительности труда за счет освобождения человека от выполнения тяжелых трудоемких операций, что приводит также к снижению утомляемости трудящихся и повышению безопасности их труда. Хотя, с другой стороны, применение механизмов зачастую приводит к появлению новых опасных зон, причинителей травм и травмирующих факторов, изменяя соотношение основных причин травматизма.
Анализ травматизма при использовании средств механизации аварийно-спасательных работ показывает, что появление новых опасных и вредных факторов в разрабатываемой технике чаще всего обусловлено недостаточным вниманием конструкторов к вопросам охраны труда, в первую очередь к прогнозированию возможных сопутствующих вредностей и причинителей травм.
В зависимости от степени оснащения производственных процессов техническими средствами механизация может быть частичной или комплексной. Комплексная механизация является основой для а в т о м а т и з а ц и и производственных и технологических процессов.
Цель автоматизации производства – повышение производительности труда, улучшение технико-экономических показателей, создание условий для повышения безопасности технологии ведения АСДНР, улучшения производственной среды. Огромное значение с точки зрения обеспечения безопасности аварийно-спасательных работ имеет применение робототехники, особенно в зонах интенсивного воздействия опасных химических веществ, радиоактивных веществ, ионизирующих излучений.
Различают автоматизацию частичную, комплексную и полную.
Частичная автоматизация– автоматизация одного или нескольких отдельных звеньев производственного процесса. Применяется в случаях, когда непосредственное управление слишком сложно для человека или осуществляется в условиях, опасных для его жизни или здоровья.
Комплексная автоматизация предполагает автоматизацию основных звеньев производственного процесса, управление которыми и контроль осуществляются автоматически с помощью технических средств по заданной программе при общем наблюдении человека-оператора за работой всего комплекса.
Полная автоматизация передает функции человека-оператора управляющим машинам. При этом исключаются ошибки, связанные с несовершенством работы человека.
Следует отметить, что механизация и автоматизация трудовых процессов снижают тяжесть труда только по величине энергозатрат, т.е. они заменяют тяжелый физический труд трудом о п е р а т о р а.
Однако управление современными машинами, сложными техническими комплексами, различными видами транспорта, как правило, нельзя отнести к легкому труду. Этот вид труда осуществляется в условиях ограниченной подвижности, он связан с длительными статическими мышечными нагрузками, которые являются наиболее утомительными.
Труд оператора сопровождается большим эмоциональным напряжением, вызванным повышенной ответственностью за результаты труда, необходимостью восприятия большого объема информации и принятия решений в условиях ограниченного времени.
Труд оператора при систематическом переутомлении приводит к нарушениям нервной и сердечно-сосудистой систем организма. При этом утомление само по себе вызывает снижение внимания и скорости реакций оператора, что приводит к росту травматизма и аварийности. В режиме оператора при АСДНР работают экскаваторщики, водители-крановщики, экипажи инженерных машин и др.
Основными причинами ошибок в работе оператора являются следующие: недостаток информации в аварийных ситуациях; дефицит времени на принятие решений; неадекватная реакция в стрессовой ситуации (влияние стресса усугубляется страхом, обусловленным повышенной ответственностью, неуверенностью в себе, недостатком знаний и опыта).
В этой связи неоценима роль обучения и повышения квалификации личного состава. Большая часть названных причин, не связанных с личностными качествами, может быть исключена в результате обучения, доведения до автоматизма действий оператора в аварийных ситуациях.
По мере внедрения сложной техники современное производство аварийно-спасательных работ требует все более высокой квалификации личного состава. С другой стороны, развитие механизации, автоматизации и дистанционного управления позволяет сократить (или даже исключить) пребывание людей в опасных зонах, снизить содержание вредных веществ в воздухе рабочей зоны, уровни шума, вибраций и других вредностей, т.е. создает реальные предпосылки улучшения условий труда.
Таким образом, механизация производственных процессов и их автоматизация, наряду с положительными моментами, приводят к появлению новых проблем в области охраны труда. При создании сложного высокомеханизированного и автоматизированного оборудования важнейшее значение для обеспечения точности и безопасности его работы приобретают эргономические и психофизиологические требования.
Роль человека-оператора в системе управления поясняет рис.1.1. Здесь представлена простейшая (одноконтурная) схема замкнутой системы человек–машина. Процесс регулирования представляет собой ряд переходов воздействий от одного звена к другому. Обратная связь служит для отражения изменения состояния звеньев, что позволяет человеку контролировать правильность своих действий.
С развитием автоматизации функции регулирования все в большей степени передаются автоматам и система человек – машина становится сложнее. Но в любом случае информация об управляемом объекте поступает на индикаторы, за которыми наблюдает человек. Задачами оператора в такой системе являются контроль за работой системы автоматического регулирования, предупреждение аварий, выявление неисправностей, принятие мер по их устранению.
Наиболее важные требования к оператору в системе управления – скорость реакции, точность его действий и надежность работы. Оператор может
Рис. 1.1. Структурная схема системы человек–машина:
И – индикаторы; О – оператор; ОУ – органы управления; М – машина; 1, 2, 3, 4 – переходы воздействий от одного звена к другому; 5 – обратная связь
выступать в роли приемника, анализатора, ретранслятора информации или исполнителя, – скорость реакции оператора определяется временем полного цикла регулирования, т.е. временем, в течение которого объект переводится из исходного состояния в заданное.
Математически процесс регулирования описывается некоторой функцией времени. Для простой одноконтурной системы (рис.1.1) время цикла регулирования представляет собой сумму времени задержки сигнала во всех звеньях:
, (1.1)
где Т – время цикла регулирования; п – число звеньев в системе управления (в нашем случае п=3 – индикатор, орган управления, машина) ; ti - время задержки сигнала в i-м звене; To– время задержки сигнала оператором от момента поступления сигнала до ответа на него действием.
При конструировании систем управления следует учитывать, что по времени задержки сигнала оператором значительно больше времени задержки машинных звеньев, то есть:
(1.2)
Время реакции человека исчисляется десятыми долями секунды, секундами и даже иногда минутами, в то время как – обычно на два-три порядка меньше.
Для обеспечения надежного и точного управления машиной информация, поступающая оператору, должна соответствовать пропускной способности человека. Оптимальное значение количества информации для человека составляет 0,1-5,6 бит/с. Увеличение количества информации снижает скорость ее восприятия, оператор допускает ошибки в приеме и передаче сигналов. Уменьшение потока информации приводит к монотонности работы, снижению эмоционального тонуса, в результате также увеличивается число ошибок (рис.1.2). Ошибки в работе оператора ведут к снижению производительности труда, повышенному травматизму и авариям. В этом смысле большое значение имеет тренировка, но и она не исключает вероятности ошибок.
На надежность работы оператора отрицательно влияют неблагоприятные санитарно-гигиенические условия труда, шум, вибрация и т.п. Наиболее рациональный путь повышения надежности его работы – оптимальное согласование оператора с машиной и создание комфортных условий работы.
Для этого необходимо правильно организовать рабочее место, т.е. место постоянного или периодического пребывания работающего для наблюдения и ведения производственных процессов. Организация рабочего места включает в себя:
выбор рабочей позы;
определение рабочих зон;
размещение органов управления, индикаторов, инструментов, материалов и заготовок, необходимых для работы.
Рабочая поза. Правильная рабочая поза имеет большое значение для сохранения работоспособности и обеспечения безопасности. Она зависит от характера работы – движения должны быть экономичными, легкими, безопасными и производительными. Поза является правильной, если проекция общего центра тяжести находится в пределах площади опоры (рис.1.3а). Если это условие не соблюдается (рис.1.3б), рабочая поза вызывает дополнительные статические нагрузки на мышцы. Это приводит к быстрому утомлению, снижению работоспособности, профессиональным заболеваниям, таким, как искривление позвоночника, расширение вен, плоскостопие и другим, а также может приводить к травматизму.
При организации рабочего места следует учитывать работу мышц. Так, если в процессе работы задействована небольшая группа мышц, то более предпочтительной является сидячая поза, при работе большой группы мышц – стоячая. Отсюда ясно, что при управлении техникой, автотранспортными средствами водитель (механик), оператор (крановщик, экскаваторщик) выполняет операции сидя, а работа с аварийно-спасательным инструментом выполняется в стоячем положении. При этом, если при прямой позе сидя тяжесть мышечной работы принять равной 1,0, то при прямой позе стоя работа составляет 1,6; при наклонной позе сидя – 4,0; при наклонной позе стоя – 10,0.
Рабочая зона. Пространство рабочего места по характеру или частоте осуществляемых в нем движений следует подразделять на зоны, соответствующие оптимальному полю зрения работающего. Рабочая зона определяется дугами, которые может описать рука, поворачивающаяся в плечевом или локтевом суставе при полном сгибании и разгибании, на уровне рабочей поверхности. Движением рук управляет мозг человека в соответствии с коррекцией глаз, поэтому зону, удобную для действия обеих рук, необходимо совмещать с зоной, удобной для обзора.
Рабочие места должны проектироваться также с учетом антропометрических данных – усредненных размеров человеческого тела, характерных для данного региона или группы населения (рост, длина рук, ширина плеч, высота колен и т.п). Если размещение органов управления не соответствует физическим данным человека, то работа становится неоправданно утомительной.
![]() |
|

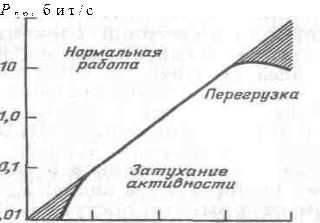
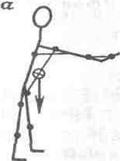
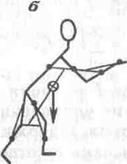
На рис.1.4 показаны структурные схемы рабочих зон для сидячей и стоячей работы. Зоны, обозначенные цифрами, оцениваются следующим образом.
Зона 1 – в ней хорошо работают обе руки и хорошо осуществляется зрительный контроль. В этой зоне следует размещать органы управления, которыми оператору приходится пользоваться чаще всего или производить наиболее точные и быстрые движения; она наилучшим образом подходит для точных мелких сборочных работ.
Зоны 2 и 3 – хорошо доступны для одной и мало доступны для другой руки; зрительный контроль затруднен. Здесь удобно размещать инструменты и материалы, которые рабочий берет только одной рукой или органы управления, за которыми не требуется постоянного визуального наблюдения.
Зона 4 – менее доступная зона, используется как запасная к зонам 2 и 3.
Зоны 5 и 6 – доступны только для левой или правой руки. В ней можно размещать инструменты и материалы, редко используемые в трудовом процессе или органы управления, которыми пользуются не глядя.
| |||||||||
|
|
| |||||||
![]() | |||||||||
![]() |
Органы управления. Типичные факторы, которые надо учитывать при проектировании органов управления, – рабочая поза оператора; расположение органов управления, их размер и форма; характер выполняемых движений; сопротивление усилию оператора (отношение величины перемещения органа управления к перемещению указателя индикатора); воздействие производственной среды (температура, влажность, вибрация и т.п.).
Система управления может быть ручной или ножной. Ручное управление является наиболее предпочтительным, причем более удобными для человека являются движения к себе или от себя. Также следует иметь в виду, что движения к себе более быстрые, но менее точные, а от себя – более точные, но менее быстрые. Ножные органы управления используются тогда, когда требуются большие усилия и низкая точность: включение-выключение, грубая регулировка параметров и т.п.
Точность движений обязательно требует определенного момента сопротивления регулятора: для рукоятки 3–17 Н/м, для ножных педалей 20 – 80 Н/м. Если управление регулятором не требует усилий, то оператор "не чувствует" его и действует неточно.
При ручном управлении максимальные усилия достигаются при захватывании рычагов на уровне плеча в положении стоя и на уровне локтя в положении сидя (рис.3.5). Органы управления, которыми пользуются чаще, следует располагать также на высоте между локтем и плечом.
Форма и размеры органов управления должны быть согласованы с размерами и биомеханическими особенностями руки человека. Для различных операций лучше использовать регуляторы, действующие по различному принципу: перекидные, кнопочные, клавишные, поворотные и др.
При дистанционном управлении манипуляторы должны воспроизводить движения, требующие минимального переосмысливания со стороны оператора.
Опыт показывает, что время выполнения операции возрастает с удалением оператора от объекта воздействия. Для сокращения этого времени эффективно используется промышленное телевидение.
Важнейшим средством повышения точности и скорости действий оператора являются структурное соответствие в расположении приборов и органов управления, а также естественные связи направлений движения. Как показано на рис.3.6, движение индикаторной стрелки, соответствующее возрастанию контролируемого параметра, осуществляется по часовой стрелке и вращение регулятора, обеспечивающее возрастание параметра, производится в этом же направлении. Когда направление движения регуляторов соответствует направлению перемещения указателей индикаторов, число ошибок уменьшается в 2 – 3 раза за счет снижения вероятности грубых ошибок при рефлекторных движениях при управлении.
Рис. 1.6. Естественные связи направлений движения управляющих органов
Если на панели управления необходимо разместить более 25 – 30 приборов, то их следует компоновать в две или более зрительно отличающиеся группы для облегчения чтения показании. В случаях, когдана панели размещаются и органыуправления, и индикаторы, их следует монтировать так, чтобы индикаторы располагались в центральной части, а органы управления – на периферии.
Дата добавления: 2016-06-22; просмотров: 3362;