РАСЧЕТ И АНАЛИЗ ПРОДОЛЖИТЕЛЬНОСТИ ПРОИЗВОДСТВЕННОГО ЦИКЛА СЛОЖНОГО ПРОЦЕССА
Рассмотрим пример сборки изделия А.
На участке осуществляется сборка двигателя. Режим работы - двухсменный. Продолжительность рабочей смены - 8 ч. Время на плановые ремонты и переналадку рабочих мест составляет 2 %. Месячная программа выпуска: Nв = 700 шт. Число рабочих дней в месяце: Др = 21 Потери рабочего времени на плановые ремонты: Ар = 2% номинального фонда времени. Необходимо определить календарно-плановые нормативы, выполнив следующие расчеты и построения:
1. Построить веерную схему сборки двигателя;
2. Определить размер партии изделий;
3. Установить удобопланируемый ритм запуска партий изделий в производство;
4. Рассчитать число партий, запускаемых в течение планового периода;
5. Определить продолжительность операционного цикла сборки партии двигателей;
6. Продолжительность операционного цикла по сборочным единицам;
7. Число рабочих мест и количество рабочих;
8. Построить цикловой график сборки изделия без учета загрузки рабочих мест, график загрузки рабочих мест, закрепив операции за рабочими местами и уточненный цикловой график с учетом загрузки рабочих мест;
9. Определить продолжительность производственного цикла и опережения запуска-выпуска по сборочным единицам и деталям для циклового и уточненного циклового графика;
10. Сделать соответствующие выводы.
Таблица 3 - Технологический процесс сборки изделия «А»
Условное обозначение сборочной единицы | № операции | Штучное временя(ti), мин. | Подготови-тельно-заключитель-ное время (tп.з.i,), мин. | Подача сборочной единицы к операции | Размер партии изделий (N), шт. | Длительность операционного цикла партии изделий, ч. | Длительность операционного цикла сборочной единицы, ч. |
АВ1 | 7,0 | ||||||
АВ2 | 16,5 | ||||||
АВ | 4,7 | ||||||
АБ | 15,9 | ||||||
12,4 | |||||||
4,7 | |||||||
АА | 7,0 | ||||||
16,6 | |||||||
А | 11,3 | ||||||
7,6 | |||||||
9,5 | - | ||||||
Итого: | 113,2 | - |
Структура производственного цикла сложного процесса определяется составом операций и связей между ними. Состав операций зависит от номенклатуры деталей, сборочных единиц и технологических процессов их изготовления и сборки. Взаимосвязь операций и процессов обуславливается веерной схемой сборки изделия и технологией его изготовления. Веерная схема сборки изделия показывает, какие узлы, подузлы и мелкие сборочные единицы можно изготавливать параллельно независимо друг от друга, а какие только последовательно.
1. Построение веерной схемы сборки (рис. 32).
А 9®10®11 |
АА 7®8 |
АБ 4®5®6 |
АВ |
АВ1 |
АВ2 |
Рис. 32. Веерная схема сборки изделия А
При решении вопроса о размерах партии необходимо исходить из экономически оптимального размера. Работа большими партиями позволяет реализовать принцип партионности и обеспечить:
возможность применения более производительного процесса, что снижает затраты на изготовление изделий;
уменьшение подготовительно-заключительного времени, приходящегося на единицу продукции;
сокращение потерь времени рабочих-сборщиков на освоение приемов работы (приноравливание к работе);
упрощение календарного планирования производства.
Эти факторы способствуют росту производительности труда рабочих и снижению себестоимости продукции.
Однако в единичном и серийном производствах, где за каждым рабочим местом закрепляется выполнение нескольких операций и где преобладает последовательный вид движения предметов труда, с ростом размера партии повышается степень нарушения принципа непрерывности, поскольку увеличивается время пролеживания каждой сборочной единицы, т.е. возрастает продолжительность производственного цикла изготовления партии изделий, число сборочных единиц, находящихся в заделе и на хранении (т.е. незавершенное производство).
Эти противоположные факторы, связанные с реализацией принципа (партионности) и нарушением принципа (непрерывности), с увеличением партии изделий требуют определения такого её размера, при котором сочетание экономии от реализации первого принципа и потерь от нарушения второго, было бы рациональным с экономической точки зрения. Такой размер партии принято называть экономически оптимальным.
2. Определение оптимального размера партии изделий.
Определение оптимального размера партии изделий является одним из важнейших календарно-плановых нормативов при организации серийного производства, так как все остальные календарно-плановые нормативы устанавливаются на партию предметов труда.
На предприятиях обычно используются упрощенный метод расчета исходя из приемлемого коэффициента потерь рабочего времени на переналадку и текущий ремонт рабочих мест (Аоб). Как правило, величину этого коэффициента принимают в пределах от 0,02 для крупносерийного и до 0,1 для мелкосерийного и единичного производства (или от 2 до 10%).
Определим минимальное число изделий в партии по формуле:
Nmin =
где tп.з.i – подготовительно-заключительное время на i-ой операции;
m – количество операций;
ti – время на каждой i-ой операции.
Полученный результат рассматривается как минимальная величина партии изделий. За максимальную величину можно принять месячную программу выпуска изделий (сборочных единиц). Применительно к рассматриваемому примеру получим
Nmin = =86 штук
Nmax = Nв = 700 штук
Таким образом, в результате проведенных расчетов устанавливаем пределы нормального размера партии изделий:
Nmin ≤ NH ≤ Nmax
Предельные размеры партии изделий корректируются, исходя из минимального размера.
3. Определение удобопланируемого ритма запуска партий изделий в производство.
Корректировка минимального размера партии изделий начинается с установления удобопланируемого ритма (Rр) – периода чередования партий изделий.
Если в месяце:
20 рабочих дней, удобопланируемыми ритмами будут 20, 10, 5, 4, 2, 1.
21 день, то удобопланируемыми ритмами будут 21, 7, 3, 1;
22 дня, то такими ритмами будут 22, 11, 2, 1.
Период чередования партий изделий рассчитывается по формуле:
Rp =
где Др – число рабочих дней в месяце.
Период чередования составит
Rp = дня
Если по расчету получается дробное число, то из ряда удобопланируемых ритмов выбирают ближайшее большее целое число (Rпр).
Из удобопланируемых ритмов 21, 7, 3, и 1 выбираем ближайшее большее значение
Rпр = 3 дня
Далее в соответствии с принятым периодом чередования корректируем размер партии изделий по формуле:
Nн = Rпр∙ = 3∙
= 100 штук
Выполняется условие 86 < 100 < 700.
Нормальный размер партии изделий должен быть кратным месячной программе выпуска изделий.
4. Определение числа партий, запускаемых в течение планового периода.
Число партий в месяц (X) определяем по формуле
X =
X = = 7 партий
5. Определение продолжительности операционного цикла сборки партии изделий.
Продолжительность операционного цикла партии изделий по каждой операции (tnci) рассчитывается по формуле
tnci =
Для сборочной единицы АВ1
tnc1 = =12 час.
Аналогично выполняются расчеты по другим операциям, и результаты вписываются в графу 7 табл. 3.
6. Определение продолжительности операционного цикла по сборочным единицам.
Продолжительность операционного цикла партии изделий по сборочным единицам определяется по формуле
tc.ед =
где k – число операций, входящих в сборочную единицу.
Для сборочной единицы АБ
tc.ед= 27 + 21 + 8 = 56 час.
Аналогично выполняются расчеты по другим сборочным единицам, результаты вписываем в графу 8 таблицы 4.
Таблица 4
Условное обозначение сборочной единицы | № операции | Штучное временя(ti), мин. | Подготови-тельно-заключитель-ное время (tп.з.i,), мин. | Подача сборочной единицы к операции | Размер партии изделий (N), шт. | Длительность операционного цикла партии изделий, ч. | Длительность операционного цикла сборочной единицы, tc.ед ч. | |
АВ1 | 7,0 | |||||||
АВ2 | 16,5 | |||||||
АВ | 4,7 | | 8 | |||||
АБ | 15,9 | |||||||
12,4 | ||||||||
4,7 | ||||||||
АА | 7,0 | |||||||
16,6 | ||||||||
А | 11,3 | |||||||
7,6 | ||||||||
9,5 | - | |||||||
Итого: | 113,2 | - | - |
7. Определение числа рабочих мест.
Необходимое число рабочих мест для сборки изделий рассчитывается по формуле
Ср =
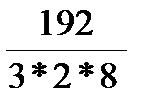
2 смены по 8 час.
где Rпр = 3 дня;
8. Определение количества рабочих
Необходимое количество рабочих определяется по формуле
Чсп = Ср∙Ксм∙Kсп ,
где
Kсп – коэффициент, учитывающий списочную численность (принимается Ксп= 1.1).
Для рассматриваемого примера
Чсп = 4∙2∙1.1 = 9 чел.
9. Построение циклового графика сборки изделия без учета загрузки рабочих мест; графика загрузки рабочих мест.
Построение циклового графика сборки изделия «А» без учета загрузки рабочих мест ведется на основе веерной схемы сборки (рис. 32) и продолжительности циклов сборки каждой i-й операции и каждой сборочной единицы (табл. 4 гр.7, 8).
График строится в порядке, обратном ходу технологического процесса, начиная с последней операции (рис. 33, часть а), с учётом того, к какой операции поставляются сборочные единицы. Продолжительность цикла этого графика будет минимальной.
Условное обозначение сборочной единицы | tсб.ед., час. | Опережение, час. | Ритм, дни, смены | ||||||||||||||||||
Rпр=3 дня | Rпр=3 дня | ||||||||||||||||||||
выпуска | запуска | ||||||||||||||||||||
а). Цикловой график сборки изделия «А» (без учета загрузки рабочих мест) | |||||||||||||||||||||
А | |||||||||||||||||||||
АА | |||||||||||||||||||||
АБ | |||||||||||||||||||||
АВ | 3 Id4t1ZQLESZFSNRkeDjoDUKCVYJTf+jDrFnMx8KgFfGzFn6hPDi5H2bUUtIAVjFCJ3vbES7ARi7o 4gwHpQTD/raaUYwEg+flrR09If2NUCsQ3lu7cXs7jIeTk8lJv9PvHU86/TjPO0+n437neJo8GeRH +XicJ+88+aSfVpxSJj3/29FP+n83WvtHuBvaw/AfhIoeogdFgeztfyAd2u47vZuZuaKbmfHV+QmA aQ/B+5fpn9P9fYi6+36MfgEAAP//AwBQSwMEFAAGAAgAAAAhANY3TcveAAAACQEAAA8AAABkcnMv ZG93bnJldi54bWxMj0FLw0AQhe+C/2EZwVu7SbFVYyZFRMGTaCuF3rbJmMRmZ+Puton+ekc86HHe PN77Xr4cbaeO5EPrGCGdJqCIS1e1XCO8rh8mV6BCNFyZzjEhfFKAZXF6kpuscgO/0HEVayUhHDKD 0MTYZ1qHsiFrwtT1xPJ7c96aKKevdeXNIOG207MkWWhrWpaGxvR011C5Xx0swvV6mLtnv99cpO3H 9uv+PfaPTxHx/Gy8vQEVaYx/ZvjBF3QohGnnDlwF1SFM0lS2RITZ4hKUGH6FHcJcBF3k+v+C4hsA AP//AwBQSwECLQAUAAYACAAAACEAtoM4kv4AAADhAQAAEwAAAAAAAAAAAAAAAAAAAAAAW0NvbnRl bnRfVHlwZXNdLnhtbFBLAQItABQABgAIAAAAIQA4/SH/1gAAAJQBAAALAAAAAAAAAAAAAAAAAC8B AABfcmVscy8ucmVsc1BLAQItABQABgAIAAAAIQCTCYmVagIAAIcEAAAOAAAAAAAAAAAAAAAAAC4C AABkcnMvZTJvRG9jLnhtbFBLAQItABQABgAIAAAAIQDWN03L3gAAAAkBAAAPAAAAAAAAAAAAAAAA AMQEAABkcnMvZG93bnJldi54bWxQSwUGAAAAAAQABADzAAAAzwUAAAAA "> 3 | ||||||||||||||||||||
АВ2 | |||||||||||||||||||||
АВ1 | |||||||||||||||||||||
Тц.сб. | =88 | ч | |||||||||||||||||||
Номер операции | Номер раб.места | б). График распределения по рабочим местам | |||||||||||||||||||
А | 9,10,11 | IV | d hXi3VHMuRJgUIVGT4dGgPwgJVglO/aEPs2a5mAqDVsTPWviF8uDkfphRF5IGsIoROtvbjnABNnJB F2c4KCUY9rfVjGIkGDwvb+3oCelvhFqB8N7ajdu7UW80G86GSSfpH806SS/PO8/m06RzNI+fDvIn +XSax+89+ThJK04pk57/7ejHyd+N1v4R7ob2MPwHoaKH6EFRIHv7H0iHtvtO72Zmoejm1Pjq/ATA tIfg/cv0z+n+PkTdfT8mvwAAAP//AwBQSwMEFAAGAAgAAAAhABiWhc3fAAAACgEAAA8AAABkcnMv ZG93bnJldi54bWxMj8FOwzAMhu9IvENkJG5b0gIDStMJIZA4IdgQEresMW1Z45QkWwtPjxEHONr+ 9Pv7y+XkerHHEDtPGrK5AoFUe9tRo+F5fTe7ABGTIWt6T6jhEyMsq8OD0hTWj/SE+1VqBIdQLIyG NqWhkDLWLToT535A4tubD84kHkMjbTAjh7te5kotpDMd8YfWDHjTYr1d7ZyGy/V45h/D9uU06z5e v27f03D/kLQ+Ppqur0AknNIfDD/6rA4VO238jmwUvYZZps4Z1ZAvchAM/C42TKqTHGRVyv8Vqm8A AAD//wMAUEsBAi0AFAAGAAgAAAAhALaDOJL+AAAA4QEAABMAAAAAAAAAAAAAAAAAAAAAAFtDb250 ZW50X1R5cGVzXS54bWxQSwECLQAUAAYACAAAACEAOP0h/9YAAACUAQAACwAAAAAAAAAAAAAAAAAv AQAAX3JlbHMvLnJlbHNQSwECLQAUAAYACAAAACEA4wI9gGoCAACHBAAADgAAAAAAAAAAAAAAAAAu AgAAZHJzL2Uyb0RvYy54bWxQSwECLQAUAAYACAAAACEAGJaFzd8AAAAKAQAADwAAAAAAAAAAAAAA AADEBAAAZHJzL2Rvd25yZXYueG1sUEsFBgAAAAAEAAQA8wAAANAFAAAAAA== "> | ||||||||||||||||||
АА, АБ | 6,7,8 | III | |||||||||||||||||||
АБ | 4,5 | II | |||||||||||||||||||
АВ,АВ1,АВ2 | 1,2,3 | I | |||||||||||||||||||
в). Уточненный цикловой график сборки изделия «А» | |||||||||||||||||||||
А | |||||||||||||||||||||
АА | |||||||||||||||||||||
АБ | |||||||||||||||||||||
АВ | |||||||||||||||||||||
АВ2 | |||||||||||||||||||||
АВ1 | |||||||||||||||||||||
Тц.сб.=96 ч.
Рис. 33. Цикловой график сборки изделия «А»
Однако условия производства и ограниченные ресурсы требуют выполнения определенных работ последовательно, на одном и том же рабочем месте, стенде все это приводит к изменению циклового графика и, как правило, к смещению запуска на более ранние сроки и, как следствие, к увеличению продолжительности цикла.
Для достижения равномерности загрузки рабочих мест и рабочих-сборщиков необходимо закрепить операции за рабочими местами. С этой целью на каждое рабочее место набирается объем работ, продолжительность операционного цикла которых не должна превышать пропускную способность рабочих мест на протяжении принятого периода чередования (табл. 5).
Таблица 5 - Закрепление операций за рабочими местами
Номер рабочего места | Номер операции, закреплённой за рабочим местом | Условное обозначение сборочной единицы | Суммарная продолжительность операционного цикла, ч | Пропускная способность рабочего места за Rпр = 48 ч. | Коэффициент загрузки рабочего места |
IV | 9,10,11 | А | |||
III | 6,7,8 | АА, АБ | |||
II | 4,5 | АБ | |||
I | 1,2,3 | АВ, АВ1 АВ2 |
10. Построение циклового графика с учетом загрузки рабочих мест сборки изделия «А».
График строится на основе циклового графика без учета загрузки рабочих мест (рис. 33, часть а). При этом периоды выполнения циклов отдельных операций графика должны были проецироваться на соответствующие рабочие места на графике (рис. 33, часть б). В этом случае сохраняется продолжительность производственного цикла на графике, построенном без учета загрузки рабочих мест. Однако не всегда удается это осуществить. В нашем случае сдвинут срок начала выполнений 4, 5, 6, 1. Сдвиг работ на более раннее начало повлёк за собой увеличения продолжительности производственного цикла, и появилось пролёживание сборочных единиц. На этом же графике (рис. 33, часть в) необходимо провести производство второй, третьей и последующих партий изделий до тех пор, пока не заполниться полностью период чередования партий изделий. Заполненный период чередования и представляет собой стандарт-план, так как именно здесь показаны стандартные, повторяющиеся сроки проведения отдельных операций сборки каждым рабочим сборщиком.
Построение уточненного циклового графика сборки изделия «А» и определение фактической продолжительности производственного цикла, которая обычно немного больше минимальной, так как выполнение некоторых операций сдвинуто на более ранние сроки. Уточненный график сборки изделий «А» (рис. 33 (часть в) строится на основе графиков, приведенных на рис. 33 (часть а, б) по этому графику определяется фактическая продолжительность производственного цикла сборки партии изделий. В рассматриваемом примере эта величина составляет 96 ч. Волнистая линия на рис. 33 (часть в) показывает время смещения запуска соответствующих сборочных единиц АБ и АB1.
Важным календарно-плановым нормативом является опережение запуска-выпуска сборочных единиц изделия «А». Расчёт этого норматива ведётся непосредственно на самих графиках в третьей и четвёртой колонках рис. 33 (части а, в). В связи с необходимостью смещения запуска сборочных единиц АБ и АВ1 на более ранние сроки (рис. 33 часть в) изменилось и опережение запуска-выпуска этих сборочных единиц, а продолжительность производственного цикла на 8 ч. больше, чем на первоначальном графике.
Дата добавления: 2018-05-10; просмотров: 2716;