Бронзы оловянные. Методы определения меди – по ГОСТ 1953.1-79. Настоящий стандарт устанавливает гравиметрические электролитические методы определения меди в оловянных бронзах.
Оловянные бронзы
1.1 Общие сведения
Оловянными бронзами называются сплавы меди с оловом, диаграмма состояния представлена на рисунке 1.
Наибольшее практическое значение имеют сплавы, содержащие до 20 % Sn. Эта часть диаграммы состояния Cu - Sn представляет собой α - твердый раствор олова в меди, имеющий гранецентрированную кристаллическую решету. Структура бронзы с содержанием олова 7 % изображена на рисунке 2. Растворимость олова в меди изменяется от 15,8 % при 586 °С до 1 % при 200 °С. Причем в реальных условиях затвердевания и охлаждения (в песчаных и металлических формах) область α - твердого раствора значительно сужается (примерно до 6 %). В равновесии с α - твердым раствором по мере понижения температуры находятся β-, γ-, δ- и ε - твердые растворы: β - на основе соединения Cu5Sn с ОЦК решеткой, δ и γ - на основе Cu31Sn8 со сложной кубической решеткой и ε - на основе Cu3Sn с ГПУ решеткой. К числу однофазных сплавов относятся бронзы, содержащие до 5-6 % Sn. В бронзах с более высокой концентрацией олова при кристаллизации образуются α - и β - фазы. В процессе охлаждения β - фаза при 586 °С распадается с образованием эвтектоида α+γ, а γ - фаза при 520 С - с образованием эвтектоида α+γ. На этом обычно заканчиваются фазовые превращения в бронзах.
Рисунок 1 – Диаграмма состояния системы Cu – Sn
Рисунок 2 – Структура оловянной бронзы (7 % олова): а – ликвация в литом состоянии; б – однородные зерна α– твердого раствора после ковки и отжига. ×100
Механические свойства оловянных бронз достаточно высоки. С увеличением содержания олова возрастают прочность и твердость сплавов, но при этом снижается пластичность. Оловянные бронзы слабо чувствительны к перегреву и газам, свариваются и паяются, не дают искры при ударах, не магнитны, морозостойки и обладают хорошими антифрикционными свойствами. Высокие триботехнические характеристики оловянных бронз можно объяснить на основе теории самоорганизации. В поверхностных слоях оловянных бронз при трении происходит неравновесный процесс выделения олова из твердого раствора, что приводит к снижению коэффициента трения и интенсивности изнашивания.
Добавки фосфора к оловянным бронзам значительно улучшают их механические, антифрикционные и литейные характеристики. Для механических свойств оптимальным является содержание фосфора около 0,5 %. При больших концентрациях фосфора бронзы охрупчиваются, особенно при горячей прокатке. Однако в литейных антифрикционных бронзах возможно до 1,2 % Р. Небольшие добавки Zr, Ti, Nb, В улучшают механические свойства и обрабатываемость давлением в холодном и горячем состояниях.
Никель при его содержании до 1 % повышает механические свойства, коррозионную стойкость и измельчает зерно. Свинец значительно повышает антифрикционные свойства и обрабатываемость резанием, но снижает механические свойства. Структура оловянной бронзы с добавлением свинца изображена на рисунке 3.
Рисунок 3 – Структура литой оловянносвинцовистой бронзы. Темные включения свинца расположены между осями дендритов; × 200
Цинк, почти не влияя на механические свойства, улучшает технологические характеристики. Железо повышает механические свойства и температуру рекристаллизации, однако с увеличением его содержания ухудшаются технологические и коррозионные свойства бронз.
1.2 Оловянные бронзы, обрабатываемые давлением
Деформируемые бронзы подразделяют на следующие группы (ГОСТ 5017-74): оловянно-фосфористые БрОФ8-0,3, БрОФ6,5-0,4, БрОФб,5-0,15, БрОФ7-0,2, БрОФ4-0,25; оловянно-цинковую БрОЦ4-3 и оловянно-цинково-свинцовые БрОЦС4-4-2,5, БрОЦС4-4-4.
Из оловяннофосфористых бронз БрОФ8-0,3 и БрОФ6,5-0,4 изготавливают сетки для целлюлозно-бумажной промышленности, из БрОФ6,5-0,15 - ленты, полосы, прутки, детали подшипников и биметаллические изделия, из БрОФ7-0,2 - прутки, шестерни, зубчатые колеса, втулки и прокладки высоконагруженных машин, из БрОФ4-0,5 - трубки контрольно-измерительных и других приборов, манометрические пружины. Из оловянно-цинковой бронзы БрОЦ4-3 выпускают ленты, полосы, прутки, применяемые в электротехнике; токоведущие пружины, контакты штепсельных разъемов, пружинную проволоку для химической промышленности и точной механики; арматуру, шаберы для бумажной промышленности. Наконец из оловянно-цинково-свинцовых бронз БрОЦС4-4-2,5 и БрОЦС4-4-4 делают втулки и подшипники для автотракторной и автомобильной промышленности.
Оловянные бронзы, обрабатываемые давлением, поставляют, как и латуни, в мягком (отожженном), полутвердом, твердом и особо твердом состоянии. Бронзы БрОФ6,5-0,4, БрОФ6,5-0,15 и БрОЦС4-4-2,5 обрабатывают обычно в холодном состоянии (прокатка, волочение), а в горячем состоянии - лишь прессованием. Бронза БрОЦ4-3 хорошо обрабатывается давлением в горячем и холодном состоянии.
1.3 Литейные оловянные бронзы
Жидкотекучесть литейных оловянных бронз ниже, чем других бронз, однако они имеют незначительную объемную усадку, что позволяет получать из этих сплавов фасонные отливки. Оловянные шихтовые литейные бронзы в чушках (ГОСТ 614-97) служат шихтой: БрОЗЦ8С4Н1 - для литейной бронзы БрОЗЦ7С5Н; БрОЗЦ13С4 - для БрОЗЦ12С5; БрО4Ц7С5-для БрОЗ,5Ц7С5; БрО5Ц6С5-для БрО5Ц5С и БрО4Ц4С17. Перечисленные литейные бронзы (ГОСТ 613-79) применяют для литья антифрикционных деталей. Кроме того, бронзы БрОЗЦ12С5 и БрОЗЦ7С5Н используют для арматуры, работающей в воде и водяном паре давлением до 245 МПа (бронза БрОЗЦ7С5Н - в морской воде и маслах).
Литейные нестандартные бронзы БрО10, БрО19 ответственного назначения применяют для арматуры и фасонных отливок; БрО10Ф1 - для подшипников, шестерен и втулок ответственного назначения; БрО10Ц2 - для арматуры, подшипников, фасонных отливок; БрО8Ц4 - для частей насосов и арматуры; БрО6Ц6СЗ - для паровой и водяной арматуры; БрО8БС12 - для ответственных подшипников, работающих при высоких давлениях; БрО5С25 и БрО1С22 - для изготовления подшипников и втулок, работающих при малых нагрузках и больших скоростях, маслоуплотнительных колец; БрО6Ц6СЗ – для паровой и водяной арматуры. Бронзы БрО5С25, БрО1С22, БрО8С12 входят в группу свинцовых бронз, к которым относятся БрС30 (для подшипников, сальников), БрС60Н2,5 (для подшипников, фасонных отливок). Вследствие невысоких механических свойств двойные свинцовые бронзы применяют для втулок и подшипников в виде тонкого слоя на стальной основе. Свинцовые бронзы с повышенным содержанием олова (БрО8С12, БрО10С10, БрО10С2НЗ) характеризуются более высокими механическими свойствами, чем двойные свинцовые бронзы. Поэтому из этих бронз изготавливают втулки и вкладыши подшипников без стальной основы.
1.4 Коррозионная стойкость оловянных бронз
Оловянные бронзы стойки по отношению к атмосферной коррозии. В сельской местности скорость коррозии бронз БрО5 и БрО8 равна (1,5 - 8) 10-3 г/(м2 ∙ ч), в морской атмосфере – (0,1-2) 10-3 г/(м2 ∙ ч). В водяном паре при малых скоростях истечения скорость коррозии оловянных бронз < 2,5-10-3 г/(м2 ∙ ч), а при высоких скоростях истечения - < 0,9 г/(м2 ∙ ч). В перегретом до 250 °С водяном паре оловянные бронзы устойчивы до давления 2 Мпа.
В морской воде оловянные бронзы более стойки, чем медь и латуни. Быстрому разрушению подвергаются оловянные бронзы под действием рудничных вод, содержащих окислительные соли.
Сильное воздействие на оловянные бронзы оказывают соляная и азотная кислоты; менее активной является серная кислота. В растворах NaOH скорость коррозии составляет 0,25 г/(м2 ∙ ч), в растворах аммиака - 1,28-2,55 г/(м2 ∙ ч), в водных растворах этилового спирта скорость коррозии < 2,5-10-3 г/(м2 ∙ ч). Скорость коррозии оловянных бронз в сухом четыреххлористом углероде или хлористом этиле менее 2,5-10-3 г/(м2 ∙ ч), а в этих же средах в присутствии влаги - 1,28 г/(м2 ∙ ч).
При комнатной температуре кислород и сухие сернистый газ, газогалогены или их водородные соединения практически не влияют на оловянные бронзы. При высоких температурах коррозия в газогалогенах значительно возрастает. Скорость коррозии в сернистом газе при наличии влаги достигает 2,51 г/(м2 ∙ ч). Значительна скорость коррозии оловянных бронз и во влажных парах сероводорода при 100 °С 1,31 г/(м2 ∙ ч).
2 Оловянная бронза марки БрОЦС4-4-4
БрОЦС4-4-4 характеризуется высокими антифрикционными и коррозионными свойствами, хорошо обрабатывается резанием, обрабатывается давлением лишь в холодном состоянии. Из этих бронз изготавливаются ленты, полосы, кроме того применяются в качестве прокладок в подшипниках и втулках различных областях машиностроения. Структура указанной бронзы изображена на рисунке 4.
Рисунок 4 – Микроструктура бронзы БрОЦС4-4-4
Химический состав отображен в таблице 1
Таблица 1 – Химический состав в % материала БрОЦС4-4-4, ГОСТ 5017 - 2006
Fe | Ni | P | Al | Cu | Pb | Zn | Sb | Bi | Sn | Примесей |
До 0,05 | До 0,3 | До 0,03 | До 0,002 | 85-90,5 | 3,5 – 4,5 | 3-5 | До 0,002 | До 0,002 | 3-5 | Всего 0,2 |
Температура плавления составляет 1015°С, твердость материала: НВ 10-1 = 61 МПа, коэффициент трения со смазкой: 0,016, коэффициент трения без смазки: 0,26;
Таблица 2 – Механические свойства сплава БрОЦС4-4-4 при 20° С
Прокат | σВ, (МПа) | δ, (%) | ψ, (%) |
Сплав мягкий | 320-360 | 30-40 | |
Сплав твердый | 500-600 | 1-2 |
Таблица 3 – Физические свойства сплава БрОЦС4-4-4
Т, °С | Е ∙ 10-5, (МПа) | α ∙ 106, (1/Град) | ρ, (кг/м3) | R ∙ 109 (Ом ∙ м) |
0,72 | - | |||
- | 18,1 | - | - |
Где Е – нормальный модуль упругости;
α – коэффициент температурного расширения;
R – удельное электросопротивление;
Режимы обработки указанной бронзы следующие: температура отжига - 600° С, температура начала рекристаллизации – 400° С.
Таблица 4 – Изменение свойств бронзы БрОЦС4-4-4 при повышенных температурах
Наименование | Температура, ° С | |||
Предел прочности при растяжении, кг/мм2 | 32,5 | 30,1 | 27,5 | |
Относительное удлинение, % | 32,5 | 37,7 | 24,5 | |
Твердость по Бринелю, кг/мм2 | 50,4 | 50,4 | 45,0 | |
Ударная вязкость, кгс/см2 | 3,6 | 3,3 | 2,2 | 0,54 |
Зависимости механических свойств бронзы БрОЦС 4-4-4 от степени деформации и температуры отжига показаны на рисунке 5. Исходным материалом для испытаний послужили полосы толщиной 4 миллиметра, мягкие и твердые соответственно. Продолжительность отжига составляет 1 час.
Рисунок 5 – Зависимость механических свойств бронзы от степени деформации и температуры отжига
3 Деталь. Подшипник скольжения
Подшипник состоит из корпуса 1, вкладышей 2, смазывающих устройств 3 (рисунок 6).
Рисунок 6 – Конструкция подшипника скольжения
Основным элементом подшипника скольжения является вкладыш, который устанавливают в корпусе подшипника или непосредственно в станине или раме машины.
Подшипники скольжения делятся на разъемные и неразъемные (глухие). Разъемные подшипники нашли большее применение в машиностроении, так как облегчают монтаж валов.
Принцип работы подшипника скольжения: в подшипниках скольжения может быть полужидкостная и жидкостная смазка, переходящая последовательно одна в другую по мере возрастания угловой скорости вала от нуля до определенного значения. Вращающийся вал увлекает смазочный материал в клиновой зазор между цапфой и вкладышем и создает гидродинамическую подъемную силу, вследствие которой цапфа всплывает по мере увеличения скорости. В период пуска, когда скорость скольжения мала, большая часть поверхности трения разделена тонкой масляной пленкой. При увеличении скорости цапфа всплывает и толщина смазывающего слоя увеличивается, но отдельные выступы трущихся поверхностей остаются не разделенными смазочным материалом. Смазка в этом случае будет полужидкостная. При дальнейшем возрастании угловой скорости появляется сплошной устойчивый слой масла, полностью разделяющий шероховатости поверхностей трения. Возникает жидкостная смазка, при которой изнашивания и заедания отсутствуют.
Подшипники скольжения используются во многих отраслях машиностроения. Они имеют такие ценные свойства - работоспособность в широком температурном диапазоне, стойкость в химически активной среде, виброустойчивость, бесшумность, сохранение работоспособности при недостаточной смазке, а в специальных конструкциях — даже без смазки. В таких условиях малейшее нарушение балансировки ротора может вызвать разрушение подшипника и аварию машины, тогда как подшипники скольжения оказываются виброустойчивыми благодаря демпфирующим свойствам смазочного слоя. Так как этот эффект у подшипников с обычными цилиндрическими вкладышами ограничен, да к тому же такие подшипники плохо центрируют вал, то для усиления демпфирующей способности и обеспечения центровки вала усложняют конфигурацию рабочей поверхности подшипников (лимонные и многоклиновые вкладыши).
Потребность в виброустойчивых опорах настолько велика, что появилась необходимость в массовом централизованном изготовлении их на специализированных заводах.
Но не только для быстровращающихся валов опоры скольжения оказываются единственно возможными. Например, для паровых турбин и турбогенераторов, работающих длительное время без остановки, опоры скольжения в условиях жидкостного трения практически почти не подвержены износу. В химическом машиностроении опоры должны быть стойкими в агрессивной среде. И эта проблема разрешается соответствующим подбором материалов для подшипника скольжения, в частности, — применением оловянных бронз. В некоторых машинах опоры приходится располагать в местах, трудно доступных для смены смазки. И в этом случае ставят специальные подшипники скольжения, которые могут работать без смазки или с минимальным количеством ее весь срок службы.
4 Методы контроля качества оловянных бронз
Бронзы оловянные. Методы определения меди – по ГОСТ 1953.1-79. Настоящий стандарт устанавливает гравиметрические электролитические методы определения меди в оловянных бронзах.
2) Бронзы оловянные. Метод рентгенофлуоресцентного анализа – по ГОСТ 30608-98. Настоящий стандарт устанавливает рентгенофлуоресцентный метод количественного химического анализа проб оловянных бронз на содержание элементов.
3) Бронзы оловянные, обрабатываемые давлением. Марки. – по ГОСТ 5017-74. Настоящий стандарт распространяется на оловянные бронзы, обрабатываемые давлением, предназначенные для изготовления полуфабрикатов.
Изделия из оловянных бронз подвергают следующим механическим испытаниям:
1) Временное сопротивление и относительное удлинение после разрыва определяют в соответствии с нормативно-технической документацией.
2) Испытание на растяжение проводят в соответствии с ГОСТ 497—84.
3) Твердость по Бринеллю определяют в соответствии с ГОСТ 9012—59.
4) Испытание на усталость методом изгиба при вращении.
4.1 Испытание на растяжение
Испытание на растяжение, также известное, как испытание при растягивающей нагрузке, возможно, самый фундаментальный тип механических испытаний материала. Испытания на растяжение - просты, относительно недороги и полностью стандартизованы. Растяжение чего-либо быстро позволяет определить реакцию материала на силы, прилагаемые при растяжении. Испытания проводят на разрывной машине (рисунок 7).
Рисунок 7 – Разрывная машина Р – 100
При испытании на растяжение, согласно ГОСТ 1497, определяют сопротивление металла малым пластическим деформациям, характеризующееся пределом пропорциональности σпц, пределом упругости σу и пределом текучести σт (или σ0,2), а также сопротивление значительным пластическим деформациям, которое выражают временным сопротивлением σв.
При растяжении определяют и пластичность металла, то есть величину пластической деформации до разрушения, которая может быть оценена относительным удлинением образца δ и его относительным сужением ψ (после разрыва образца).
Механические свойства металлов в испытаниях на растяжение определяют, используя стандартные образцы, общий вид которых показан на рисунке 8.
Рисунок 8 – Общий вид стандартных образцов для испытания на растяжение: а - цилиндрический образец; б — плоский.
Машина для испытаний снабжена устройством, записывающим диаграмму растяжения. Эта диаграмма показывает зависимость между растягивающей нагрузкой, действующей на образец, и его деформацией (рисунок 9).
Рисунок 9 – Схема диаграммы растяжения: изменение удлинения образца в зависимости от нагрузки
4.2 Определение твердости по Бринеллю
Метод Бринелля — один из основных методов определения твёрдости. Этот метод относится к методам вдавливания. Испытание проводится следующим образом: вначале дают небольшую предварительную нагрузку для установления начального положения индентора на образце, затем прилагается основная нагрузка, образец выдерживают под её действием, измеряется глубина внедрения, после чего основная нагрузка снимается. В результате на поверхности образца образуется отпечаток в виде сферической лунки (рисунок 5а).
Рисунок 10 – Схема определения твердости по Бринеллю
При определении твёрдости методом Бринелля, в отличие от метода Роквелла, измерения производят до упругого восстановления материала. В качестве индентора используется стальной закаленный шарик, который вдавливают в испытуемый образец на специальном прессе (рисунок 6).
1 – наконечник; 2 – столик; 3 – рукоятка маховика; 4 – барабан; 5 – клавиша включения привода механизма нагружения; 6 – груз; 7 – сигнальная лампочка; 8 – тумблер; 9 – индикаторный прибор.
Рисунок 11 – Схема пресса Бринелля1
Диаметр отпечатка измеряют в двух взаимно-перпендикулярных направлениях с помощью микроскопа Бринелля — лупы со шкалой (рисунок 5б).На практике пользуются таблицей, в которой указаны значения твердости в зависимости от диаметра отпечатка. Диаметр шарика и нагрузку выбирают так, чтобы соблюдалось соотношениеd=(0,25…0,5)D,т.е. для разных материалов эти параметры различны.
Недостатки:
- Метод можно применять только для материалов с твердостью до 450 HB, если применять стальной закаленный шарик. Как альтернатива, применяют шарики из твёрдого сплава на основе карбида вольфрама (WC), это позволяет повысить верхний предел измерения твёрдости до 600 HBW.
- Твёрдость по Бринеллю зависит от нагрузки, так как изменение глубины вдавливания не пропорционально изменению площади отпечатка.
- При вдавливании индентора по краям отпечатка из-за выдавливания материала образуются навалы и наплывы, что затрудняет измерение, как диаметра, так и глубины отпечатка.
- Из-за большого размера тела внедрения (шарика) метод неприменим для тонких образцов.
Преимущества:
- Зная твёрдость по Бринеллю, можно быстро найти предел прочности и текучести материала.
- Так как метод Бринелля — один из самых старых, накоплено много технической документации, где твёрдость материалов указана в соответствии с этим методом.
- Данный метод является более точным по сравнению с методом Роквелла на более низких значениях твёрдости (ниже 30 HRC).
- Также метод Бринелля менее критичен к чистоте, подготовленной под замер твёрдости поверхности.
4.3 Испытание на усталость
В результате действия циклических напряжений металл «устает», прочность его снижается и наступает разрушение детали. Данное явление называется усталостью, а сопротивление усталости – выносливостью. Разрушение от усталости происходит всегда внезапно вследствие накопления металлом необратимых изменений, которые приводят к возникновению микроскопических трещин – усталости. Трещины усталости возникают в поверхностных зонах детали. Наличие на поверхности рисок, царапин, выбоин и других дефектов, вызывающих концентрацию напряжений, способствует образованию трещин усталости.
Для оценки устойчивости металлических материалов к действию циклических нагрузок испытанию подвергают гладкие образцы или образцы с надрезом (рисунок 13).
а) |
б) |
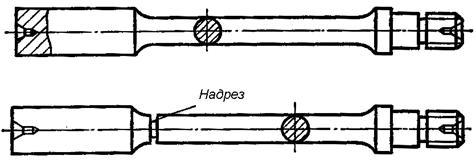
Рисунок 12 – Образцы для испытания на усталость по методу
консольного изгиба: а – гладкий: б – с надрезом
Распространенным методом испытания на усталость является изгиб при вращении. Схема испытания на машинах, работающих по методу консольного изгиба, показана на рисунке 14. Образец 1 закреплен одним концом во вращающемся от электродвигателя 3 патроне испытательной машины. Другой конец образца вращается в подшипнике, к которому подвешен груз 5. При вращении образец под действием подвешенного груза подвергается изгибу. При этом одни и те же внешние волокна будут подвергаться растяжению, а через полуоборот – сжатию и наоборот. Характер изменения напряжений при этом – синусоидальный. За один оборот напряжения от σmax через нуль изменятся до σmin, что соответствует полному циклу. Такой цикл, у которого максимальное и минимальное напряжения равны по величине и противоположны по знаку, называется симметричным.
Рисунок 13 – Схема машины для испытания на усталость по методу консольного изгиба
При испытании образец доводится до разрушения, при этом фиксируется число циклов до разрушения.
Основной характеристикой, определяемой при испытании на усталость материала, является предел выносливости – наибольшее напряжение, которое может выдержать материал без разрушения при произвольно большом числе перемен (циклов) нагрузки.
Для определения предела выносливости испытывают серию (не менее 10 штук) одинаковых образцов, изготовленных из одного и того же материала. Испытания проводят до разрушения образцов и фиксируют число циклов до разрушения. С уменьшением нагрузки число выдержанных циклов до разрушения возрастает.
По результатам испытаний строят кривую усталости в координатах максимальное напряжение – число циклов до разрушения N (рисунок 15). Кривая сначала резко снижается, а затем приближается к прямой, параллельной горизонтальной оси. Максимальное напряжение, не вызывающее разрушения при бесконечно большом числе перемен нагрузки, соответствует пределу выносливости.
Рисунок 14 – Кривая усталости
Результаты усталостных испытаний сильно зависят от состояния поверхности испытуемого образца. Для получения воспроизводимых результатов необходимо при изготовлении образцов обеспечивать высокое качество поверхности, что достигается шлифованием или полированием поверхности.
5 Модели упрочнения и разрушения при растяжении
Рассмотрим процесс растяжения поликристаллического образца. На рисунке 10 изображена типичная зависимость механического напряжения σ от относительного удлинения ε при растяжении образца. Кривая имеет 3 характерных участка. Участок 0-1 соответствует упругим обратимым деформациям, когда выполняется закон Гука. Участок 1-2 соответствует необратимым пластическим деформациям; если в точке А прекратить деформацию, то состояние образца станет соответствовать точке В. Участок 2-3 соответствует разрушению образца. Часто вблизи точки 1 кривая имеет "зуб текучести" - пунктирная кривая. Его происхождение связано с точечными дефектами, которые скапливаются вблизи дислокаций, в таких местах, что уменьшаются деформации и плотность энергии вблизи дислокации, из-за чего дислокацию труднее сдвинуть при пластической деформации на новое место, где ее энергия будет больше.
Рисунок 15 – Зависимость напряжения σ от относительного удлинения ε при растяжении образца
Попытки рассчитать предел текучести без учета дислокаций приводили к завышенным на 2-4 порядка значениям. Эксперименты показывают, что пластическая деформация происходит в первую очередь вдоль так называемых плоскостей скольжения (рисунок 11). Если к верхней плоскости приложить усилие, то атомы сместятся, и появится сила упругости, равная приложенной. С этой силой будет связана энергия деформации, которая будет возрастать до тех пор, пока атомы верхней плоскости не окажутся "над" атомами нижней плоскости - в точке В. При дальнейшем смещении атомам будет уже выгоднее "спуститься" в положения С. Таким образом верхняя плоскость может проскользнуть на новое положение. Следы таких проскальзываний хорошо видны на поверхности тщательно отшлифованных монокристаллов в виде "ступенек" после пластической деформации.
Рисунок 16 – Схема деформации кристалла за счет скольжения верхней плоскости атомов относительно нижней
Дислокационный механизм пластической деформации объясняет наблюдаемые на опыте значения предела текучести σт и σв, а также и возрастание зависимости σ(ε) на участке 1-2 (рисунок 15). При деформации сначала перемещаются менее сильно закрепленные дислокации, затем - более закрепленные, также при деформации увеличивается число дислокаций и прочих дефектов.
Предел текучести материала сильно зависит от плотности дислокаций в нем (рисунок 17). Видно, что предел текучести σт оказывается больше при очень малых значениях плотности дислокаций ρD и, наоборот, при больших плотностях дислокаций ρD. Увеличение σт при больших ρD связывают с взаимодействием дислокаций друг с другом и с другими дефектами кристаллической решетки.
Рисунок 17 – Схематическая зависимость предела текучести от плотности дислокации
В настоящее время используют ряд способов увеличения прочности материалов, большинство из них связаны с введением дополнительных препятствий движению дислокаций. Такими препятствиями являются различные дефекты:
1) выделения другой фазы;
2) точечные дефекты и их скопления;
3) большие количества дислокаций, тормозящие движение дислокаций за счет взаимодействия друг с другом;
4) ближний порядок в расположении атомов.
Напряжение необходимое для развития вязкого разрушения, превышает значение предела текучести материала, используемого при расчётах прочности деталей и конструкций. Поэтому случаи вязкого разрушения в практике эксплуатации сравнительно редки. Изучение вязкого разрушения важно для определения правильных режимов многих технологических операций: прессование, волочение, глубокая вытяжка и др. процессов, связанных со значительными пластическими деформациями.
Особенности пластического разрушения:
1. Большая величина пластической деформации, необходимая для распространения вязкой трещины.
2. Процесс может быть остановлен на любой стадии, если действующее напряжение снизится, его значение будет ниже напряжения течения материала перед трещиной.
Закономерности разрушения в поликристаллах:
1. Шейка в виде точки - наблюдается в высокопластичных металлах с ГЦК решёткой, сужение поперечного сечения перед разрушением составляет 100%.
2. Чашечный излом, т.е. излом конус - чашечка, наблюдается в менее пластичных поликристаллических металлах и является наиболее характерным.
Этот тип разрушения наблюдается наиболее часто и используется под термином «пластичное» (вязкое).
При однократном нагружении при нагрузке вплоть до временного сопротивления, характерным является внутрезёренное распространение трещины, однако может быть и межзёренное.
Вязким, как и другим изломам, свойственно неоднородность строения. Даже в пределах одного зерна разрушение происходит неоднородно, например, частично по плоскости скола с образованием гладкой блестящей фасетки в изломе, частично по другим поверхностям, деформированным в процессе разрушения. Макроскопический вид поверхности излома используют для оценки степени вязкости металла. В соответствии с теорией механики разрушения, вязкость является тем механическим свойством, которое наиболее тесно связанно с сопротивлением разрушению, т.е. с сопротивлением распространения трещины. Работа распространения трещины характеризует надёжность материала.
6 Модели упрочнения и разрушения при усталости
Повышение сопротивления усталости при кратковременных перегрузках объясняется деформационным упрочнением, происходящим при пластических деформациях микрообъемов материала, сходным с упрочнением при наклепе.
Деформационное упрочнение обусловлено взаимодействием параллельных или лежащих в параллельных плоскостях сдвига дислокаций. При этом единственным источником упрочнения являются дислокационные диполи, вызывающие направленные искажения, блокирующие перемещение дислокаций. Стадия легкого скольжения заканчивается образованием достаточно большого количества диполей. Существует некоторая критическая плотность дислокаций, по достижению которой скольжение происходит по вторичным системам скольжения, что приводит к резкому росту упрочнения за счет взаимодействия пересекающихся дислокаций. При этом плотность дислокаций с увеличением деформации возрастает быстрее, чем линейная функция. На этой стадии упрочнения эффекты динамического возврата незначительны, поэтому деформационное упрочнение, как и на стадии легкого скольжения, соответствует линейному закону.
При скольжении дислокации испытывают тормозящее воздействие со стороны леса дислокаций. Поэтому при деформации образуются дислокационные скопления. Таким образом, по мере развития деформаций по разным причинам усиливается торможение дислокаций, вызывающее рост напряжений. Возрастание прочности, наблюдаемое при повышении уровня перегрузок до известного предела, можно объяснить прогрессивным увеличением числа микрообъемов, подвергающихся пластической деформации, и увеличением интенсивности дисперсионного упрочнения. На определенной стадии процесс упрочнения прекращается. Это наступает при таком уровне и частоте перемен напряжения, когда в материале возникают необратимые внутри - и межкристаллитные повреждения, нарушающие сплошность материала.
Усталостное разрушение является длительным процессом накопления повреждений: зарождения и развития трещин. Кроме того, его отличительная особенность та, что усталость металлов наблюдается при напряжениях как выше, так и значительно ниже обычного предела текучести материалов.
Существует несколько механизмов зарождения трещин:
1) Механизм Коттрелла-Халла предусматривает образование выступов и впадин на поверхности в результате скольжения по двум системам плоскостей (рисунок 16).
а – исходное состояние; б – работа источника М1 в прямом полуцикле;
в – работа источника М2 в прямом полуцикле; г – работа источника М1 в
обратном полуцикле; д – работа источника М2 в обратном полуцикле.
Рисунок 18 – Механизм образования поверхностных выступов и впадин при циклическом нагружении (механизм Коттрелла – Халла)
За время одного полуцикла напряжения источник М1 генерирует дислокации, образующие на поверхности ступеньку А одного направления. Затем в том же полуцикле начинает действовать источник М2 в другой плоскости скольжения, в результате работы которого на поверхности возникает ступенька В противоположного направления, а первый источник М1 смещается относительно своей плоскости скольжения. При обратном полуцикле напряжения источник М1 образует ступеньку С, не совпадающую по направлению со ступенькой А и отстоящую от нее на величину смещения, вызванного действием источника М2 за прямой полуцикл напряжения. Аналогичным образом действие источника М2 вызывает при обратном полуцикле появление ступеньки D, смещенной относительно В и не совпадающей с ней по направлению. Образовавшиеся таким образом впадины и выступы растут при последующих циклах нагружения.
Механизм Коттрелла—Халла объясняет возникновение выступов и провалов в соседних полосах скольжения, однако, согласно этой модели отдельная полоса скольжения должна приводить к появлению либо впадины, либо выступа по всей длине ее пересечения с поверхностью, что не всегда подтверждается экспериментальными наблюдениями.
Механизм Мотта связывает образование выступов на поверхности с циклическим движением винтовой дислокации (рисунок 17), которая за время первого полуцикла перемещается по одной поверхности полосы скольжения, а затем путем поперечного скольжения переходит к другой поверхности и движется вдоль нее при обратном полуцикле в противоположном направлении. В конце этого полуцикла дислокация снова возвращается на исходную поверхность в результате поперечного скольжения и контур ее движения, таким образом, замыкается. Следствием такого движения является перемещение объема материала, ограниченного контуром параллельно линии дислокации, на расстояние, равное ее вектору Бюргерса.
Рисунок 17 – Образование выступов при циклическом движении винтовой дислокации по механизму Мотта
Механизм Мотта не может объяснить одновременное образование выступов и провалов. Кроме того, реализация схемы Мотта должна предусматривать действие некоторого запирающего механизма, который преобразует колебательное движение дислокации в движение по замкнутому контуру.
Общепринято деление процесса усталостного разрушения материалов на четыре стадии:
Стадия 1 — инкубационная— связана с накоплением локальных объёмов с предельной плотностью дислокаций в циклически деформируемом материале. Для зарождения усталостного разрушения (появления трещин) необходима пластическая деформация, которая проявляется в виде полос скольжения, выходящих на поверхность деформируемого тела.
Стадия 2 — зарождения трещины– период накопления обратимой повреждаемости в пределах отдельных зёрен, образование субмикротрещин в полосах скольжения, у границ блоков, зёрен и двойников, около частичек второй фазы, включений в результате слияния дислокаций и вакансий, а также возникновения разрывов, обусловленных концентрацией напряжений. Процесс протекает все более неравномерно — субмикротрещины растут и сливаются, превращаясь в микротрещины.
Стадия 3 — докритическое развитие трещины– период стабильного роста трещины. Третья стадия начинается, когда одна из микротрещин, находящаяся в наиболее благоприятных условиях, пересекает границу одного, а затем нескольких зёрен и перерастает в макротрещину. Разрушение, которое было вначале более или менее равномерно распределено в деформируемом материале (главным образом в его приповерхностном слое), постепенно
<== предыдущая лекция | | | следующая лекция ==> |
Putting a New Twist on Optical Communications | | | ТИПЫ ПОРОД-КОЛЛЕКТОРОВ |
Дата добавления: 2016-12-27; просмотров: 4493;