Некаталитические процессы и реакторы
ГОМОГЕННЫЕ ПРОЦЕССЫ И РЕАКТОРЫ
Гомогенные процессы в газовой фазе особенно характерны для органической технологии и в ряде случаев реализуются испарением органических веществ с последующей обработкой паров газообразными реагентами — хлором, кислородом, диоксидом серы, оксидами азота; соответственно происходят химические реакции хлорирования, окисления, сульфирования, нитрования и т. д. Часто применяют парофазный пиролиз, т. е. нагревание паров органических веществ без доступа воздуха с целью получения новых продуктов; при пиролизе происходит расщепление сложных молекул с образованием свободных радикалов, предельных и непредельных углеводородов, которые вступают в реакции полимеризации, конденсации, изомеризации и др. Пиролиз жидких и газообразных веществ называется также крекингом. Примером промышленных газофазных процессов может служить термическое и фотохимическое хлорирование углеводородов для получения органических растворителей, ядохимикатов и других продуктов органического синтеза.
В технологии неорганических веществ газофазные гомогенные процессы осуществляются, например, в производстве серной, азотной и соляной кислот. Так, в парах сжигают серу в печах камерного типа для получения диоксида серы; получают оксид азота из воздуха в условиях низкотемпературной плазмы (103—105 К)
N2 + O2 = 2NO.
В низкотемпературной плазме осуществляется также электрокрекинг углеводородов, например метана с целью получения ацетилена, синтез озона из кислорода и др.
В производстве азотной кислоты в газовой фазе идет окисление оксида азота в диоксид по суммарному уравнению
2NO + O2 = 2NO2.
В газовой фазе идет синтез хлороводорода из водорода и хлора в производстве соляной кислоты по экзотермической реакции
Н2 + С12 = 2НС1
Гомогенные процессы в жидкой фазе применяют в промышленности чаще, чем газофазные. Скорость химических реакций в жидкой фазе, как правило, в тысячи раз выше, чем в газах (при той же температуре), но скорость диффузии в жидкостях значительно меньше, чем в газах, вследствие высокой вязкости жидкости. Коэффициент диффузии в газах составляет 0,1—1 см2/с, а в жидкостях 10–4 — 10–5 см2/с.
К гомогенным процессам в жидкой фазе относятся, например, реакции нейтрализации и обменного разложения в технологии минеральных солей. В жидкой фазе осуществляют ряд процессов в технологии органических веществ: получение простых и сложных эфиров, полимеризация в растворах и расплавах, щелочное плавление бензолсульфокислот в производстве фенола, отдельные стадии сернокислотной гидратации этилена в производстве этилового спирта и др.
В гомогенных средах — газовой и жидкой — многие процессы идут по цепному механизму: окисление, полимеризация и пиролиз углеводородов, галогенирование углеводородов, синтез хлороводорода из элементов и др.
На скорость гомогенных процессов в газовой и жидкой фазах влияют концентрации реагирующих компонентов, давление, температура и перемешивание.
Подавляющее большинство реакций протекает в несколько стадий. Скорость всей реакции обычно лимитируется скоростью самой медленной стадии, которая и определяет порядок реакции.
Классический пример параллельных химических реакций — окисление аммиака в производстве азотной кислоты.
При последовательных реакциях образовавшийся промежуточный продукт в результате дальнейших реакций дает конечный продукт. Последовательно происходят многие реакции органического синтеза, например хлорирование, нитрование, сульфирование и окисление углеводородов.
Влияние давления. Повышение давления ускоряет газовые реакции аналогично повышению концентрации реагентов, так как с ростом давления увеличиваются концентрации компонентов.
|
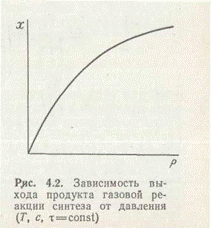
Небольшое повышение давления мало влияет на скорость процессов в жидкой фазе, однако скорости многих реакций в жидкой среде сильно увеличиваются при весьма высоких давлениях. Так, при давлении в несколько сотен мегапаскалей скорость процессов полимеризации некоторых мономеров увеличивается в десятки раз.
Влияние температуры. Повышение температуры вызывает ускорение гомогенных реакций в соответствии с уравнением Аррениуса.
При повышении температуры ускоряются и диффузионные процессы. Однако повышение температуры ограничивается условиями равновесия, возникновением побочных реакций и другими причинами. Для всех процессов стремятся установить наиболее рациональную температуру, при которой затраты на нагревание окупаются ускорением процессов.
Влияние перемешивания. Перемешивание имеет наибольшее значение для жидкостных процессов, поскольку скорости диффузии в жидкостях в десятки и сотни тысяч раз меньше, чем в газах.
Реакторы для гомогенных процессов. Основные типы гомогенных реакторов приведены на рис. 2.
|
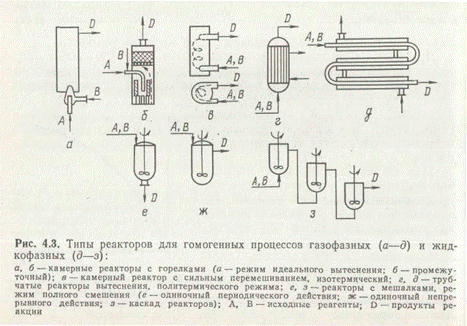
Газофазные процессы проводят, как правило, в камерных и трубчатых реакторах. Часто применяют пламенные реакторы — горелки и камеры сгорания, в которых для смешивания газовых реагентов имеются специальные устройства — сопло, эжектор, центробежный смеситель и др. Камерные реакторы используются для синтеза хлороводорода (рис. 2а), для сжигания серы, термического хлорирования метана (рис. 2б), термоокислительного пиролиза метана и др.
По гидродинамическому режиму некоторые камерные реакторы, например с центробежным смесителем (рис. 2в), приближаются к полному смешению, а некоторые — к идеальному вытеснению (рис. 2а). Камерные реакторы обычно футерованы кислотоупорным или жароупорным материалом; горелки выполняют из легированных сталей или специальных металлов (например, тантал для синтеза НС1 из элементов). Трубчатые реакторы выполняют в виде газовых теплообменников (рис. 2г) или охлаждаемых реакторов типа труба в трубе (рис. 2д) и работают при режиме идеального вытеснения.
Для проведения жидкофазных процессов наиболее характерны реакторы с различными перемешивающими устройствами. Периодические процессы ведут обычно в одиночных резервуарах с механическими мешалками и другими видами перемешивания (рис. 2е) или в автоклавах. Для непрерывных жидкофазных процессов применяют проточные реакторы — одиночные с перемешиванием (рис. 2ж), каскад реакторов с мешалками (рис. 2з), а также реакторы вытеснения такие же, как и для газофазных процессов, например охлаждаемый трубчатый реактор вытеснения (рис. 2д). Жидкофазные гомогенные реакторы применяются для реакций обмена в растворах (например, нейтрализация), этерификации, диазотирования, полимеризации, поликонденсации и др.
ЗАКОНОМЕРНОСТИ ГЕТЕРОГЕННЫХ ПРОЦЕССОВ
Гетерогенные процессы характеризуются наличием двух или более взаимодействующих фаз, поэтому они протекают с переносом вещества через поверхность раздела фаз. При этом межфазный массоперенос может быть или самостоятельным процессом, или сопровождать химическое превращение взаимодействующих компонентов. В первом случае происходят чисто физические или физико-химические изменения, такие, как абсорбция, адсорбция, десорбция, кристаллизация, испарение, плавление и т. п., а во втором — химические реакции, осложненные массообменом.
Равновесие и скорость гетерогенных процессов. Эти параметры представляют собой функцию многих переменных, и поэтому количественная оценка гетерогенных процессов весьма сложна.
Равновесие в гетерогенных химических процессах, так же как и в гомогенных, определяет выход готового продукта. На гетерогенное равновесие влияют температура, давление, концентрация реагирующих компонентов и т. п. Равновесие фаз определяется правилом фаз.
Для определения фазового равновесия, в особенности в системах жидкость — твердое (Ж—Т), применяют диаграммы фазового состояния.
Реакторы для гетерогенных превращений в системе Г—Ж. Такие реакторы являются типовой химической аппаратурой, в которой на химических заводах осуществляют как физические процессы и операции (испарение, дистилляцию и ректификацию, промывку газов, теплообмен), так и хемосорбционные процессы (в производстве минеральных кислот, соды, органических веществ). Основные типы реакторов для взаимодействий между жидкостями и газами показаны на рис. 3.
|
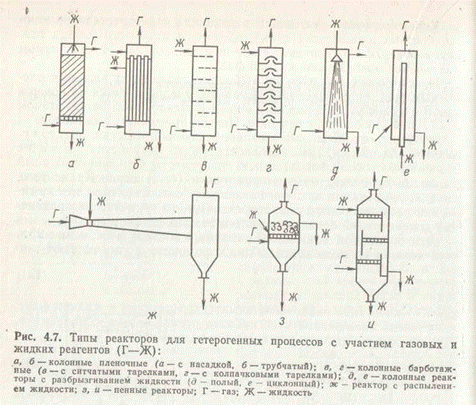
Реакторы типа а—б работают при режиме, близком к идеальному вытеснению, в—е — при режиме вытеснения по газу и смещения по жидкости, а ж—и — при режиме, близком к полному смешению. Фактически все эти реакторы работают при промежуточных режимах, в той или иной мере приближающихся к идеальным моделям перемешивания.
Конструктивное оформление реакторов для осуществления газожидкостных процессов (Г—Ж) зависит от принятого метода развития поверхности контакта газовой и жидкой фаз, т. е. приемом увеличения поверхности жидкой фазы.
Насадочная колонна (башня с насадкой) является пленочным реактором (рис. 4).
|
|
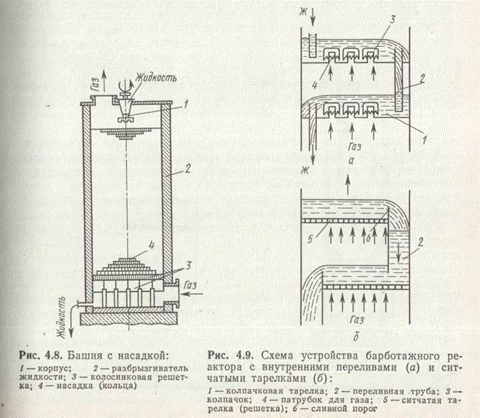
Жидкость распределяется по поверхности насадочных тел тонкой пленкой и стекает вниз противотоком взаимодействующему с ней газу. Иногда применяется прямоток. Реактор состоит из колонны, колосниковой решетки, поддерживающей насадку, насадки и оросительного устройства. Насадка должна иметь большую удельную поверхность, большой свободный объем, быть легкой, механически прочной и дешевой. Кроме того, насадка должна оказывать минимальное сопротивление потоку газа и хорошо смачиваться жидкостью. Применяется насадка различной формы: кольца из стали или керамики с равными размерами высоты внешнего диаметра (hXd=100xl00 или 50X50 или 25Х25 мм). Для интенсификации работы реактора увеличивают скорости потоков газа и жидкости.
Насадочные колонны — наиболее распространенные реакторы для абсорбционно-десорбционных процессов, их широко применяют в производстве серной кислоты, азотной кислоты, при переработке коксового газа, в ряде производств органического синтеза и т. п.
Барботажный реактор (рис. 5) может иметь от одной до нескольких десятков колпачковых или ситчатых тарелок в зависимости от характера процесса Г—Ж, от заданного КПД реактора и требуемой селективности. На каждой тарелке происходит диспергирование газа в объеме жидкости путем барботажа, т. е. пропускания пузырьков газа через слой жидкости, протекающей по тарелке. На каждой тарелке фазы взаимодействуют по принципу перекрестного тока, но по высоте колонны соблюдается принцип противотока. Барботажные реакторы тоже широко применяются в химической технологии — при концентрировании кислот в производстве соды, при переработке нефти, для процессов дистилляции и ректификации, в технологии органических веществ. Эти реакторы конструктивно более сложны, чем колонны с насадкой, их эксплуатация связана с большими затратами, но они обеспечивают более высокие расходы жидкости и газа, работают более интенсивно, обеспечивают возможность тонкого разделения жидких смесей.
Полая башня с разбрызгиванием жидкости представлена на рис. 6. В реакторах такого типа (а также в полых камерах с разбрызгиванием жидкости) развитие поверхности жидкой фазы происходит ее диспергированием, т. е. разбрызгиванием, распылением пневматическим или механическим путем в объеме или потоке газа. Полый колонный реактор с разбрызгиванием жидкости применяется, например, в производстве серной кислоты.
|
|
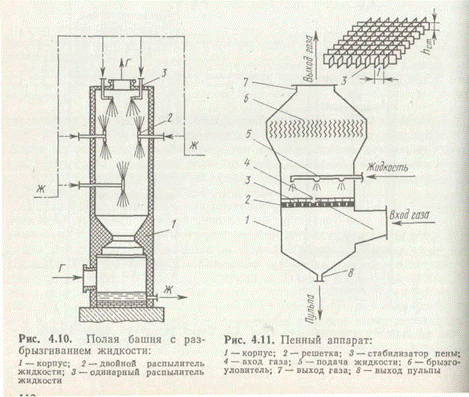
Пенные аппараты (рис. 7) по интенсивности работы значительно превосходят барботажные при меньшем расходе энергии. В пенных аппаратах поток газа проходит снизу вверх через решетку с такой скоростью, при которой силы трения газа о жидкость уравновешивают ее массу. В результате образуется взвешенный слой подвижной пены в виде быстро движущихся пленок, капель, струй жидкости, тесно перемешанных с пузырьками и струйками газа. Скорость газа в сечении аппарата может составлять от 1 до 4,5 м/с (в 2—4 раза больше, чем в барботажных аппаратах). При более высоких скоростях газа взвешенный слой пены разрушается и уносится с газом в виде потока взвеси капель. При скорости газа менее чем 1 м/с жидкость протекает через решетку и работа аппарата нарушается.
ПРОЦЕССЫ И РЕАКТОРЫ в системе газ —твердое (г —т)
Некаталитические процессы в системе Г—Т широко применяются в химической промышленности. К ним относятся адсорбция и десорбция газов на твердых сорбентах, возгонка и конденсация паров твердых веществ, пиролиз твердого топлива, различные виды обжига твердых материалов. Наиболее характерны для системы Г—Т обжиг твердых материалов и адсорбционные процессы. Обжиг — это высокотемпературная обработка зернистых твердых материалов с целью получения твердых и газообразных про дуктов, а также для придания твердым материалам механической прочности (технология силикатов). При обжиге могут идти разнообразные физико-химические процессы — пиролиз, возгонка, диссоциация, кальцинация и др. — в сочетании с химическими реакциями в твердой фазе, между газообразными и твердыми реагентами, а также в газовой фазе. В процессе обжига происходит частичное расплавление твердых веществ с образованием жидкой фазы, которая взаимодействует с другими фазами. Одно из основных превращений при обжиге — это термическая диссоциация твердых веществ.
Адсорбция — это процесс поглощения газов поверхностью твердых сорбентов. Адсорбция газов применяется для улавливания ценных летучих растворителей. Последующей десорбцией (отдувкой) адсорбированных растворителей производят их регенерацию (рекуперацию). Адсорбция применяется для очистки воздуха от токсичных газов и паров, для разделения сложных газовых смесей на компоненты и т. д. Адсорбция и десорбция играют видную роль в гетерогенном катализе, так как являются стадиями каталитического превращения вещества. Адсорбционные процессы происходят только на поверхности твердого сорбента.
Основные типы реакторов для процессов в системе Г—Т.Эти реакторы показаны на рис. 8.
Некоторые производственные высокотемпературные процессы проводятся в автоклавах, контактных аппаратах, котлах, выпарных аппаратах и т. п. Большинство некаталитических процессов между твердыми и газообразными веществами основано на химических реакциях и осуществляется при высоких температурах. Химические реакторы, применяемые для таких процессов, имеют общие характерные особенности и называются печами.
|
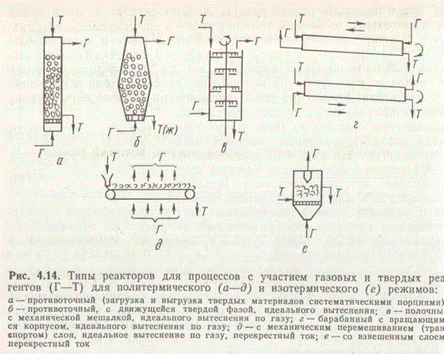
Промышленной печью называется аппарат, в котором за счет горения топлива и других химических превращений или применения электрической энергии вырабатывается теплота, используемая для тепловой обработки различных веществ, которые при этом претерпевают ряд физических и химических превращений. Промышленные печи классифицируют по отраслям производства, по технологическому назначению, источнику тепловой энергии, способу нагрева, способу загрузки сырья и т. п.
Классификация промышленных печей по принципу их устройства и работы
Типы печей | Название печей | Для каких процессов применяются |
1. Шахтные | 1. Доменная 2. Печи цветной металлургии 3. Известковая 4. Газогенератор | Выплавка чугуна Выплавка меди, свинца, никеля Разложение карбонатов Газификация твердого топлива |
II. Полочные | Механическая | Обжиг колчедана, руд цветных металлов и солей |
III.С распылением твердого материала | 1. Печь пылевидного обжига 2. Сушило | Обжиг колчедана и руд цвет-ых металлов Сушка материалов |
IV.Взвешенного (кипящего) слоя | 1. Обжиговая 2. Регенератор 3. Газогенератор 4. Печь крекинга 5. Сушило | Обжиг колчедана, руд цветных металлов, известняка Выжигание углерода споверхности катализатора Газификация и пиролиз твердого топлива Разложение тяжелых нефтяных фракций Сушка зернистых материалов и паст |
V. Барабанные вращающиеся | 1. Цементная 2. Спекания 3. Кальцинации 4. Обжиговая 5. Сушило | Пр-во цементного клинкера Пр-во глинозема Обезвоживание глинозема Разложение гидрокарбоната натрия Обжиг колчедана, глины, доломита, восстановление сульфатов Сушка различных материалов |
VI. Туннельные | 1. Обжиговая 2. Пиролиза 3. Плавильная 4. Сушило | Обжиг огнеупоров и корамики Пиролиз древесины, сланца Плавка серной руды Сушка огнеупорных и керамических изделий |
VII.Камерные | 1. Обжиговая 2. Отжиговая 3. Кольцевая 4. Коксования 5. Сушило | Обжиг керамики Отжиг стекла Обжиг огнеупоров, строительного кирпича и т.д. Коксование твердого топлива Сушка огнеупоров и керамики |
Некоторые типовые печи.Наиболее распространены шахтные, барабанные вращающиеся, ванные и электрические печи.
Шахтные печи представляют собой топливные печи прямого нагрева с выделением теплоты в самом нагреваемом материале за счет окисления твердого топлива, входящего в состав сырьевой смеси (шихты). Шихта образует в печи фильтрующий слой и движется противотоком дутью — газам, реагирующим с шихтой на поверхности и в порах кусков. Обе фазы находятся при режиме, близком к идеальному вытеснению.
Типичным представителем шахтных печей служит доменная печь.
|
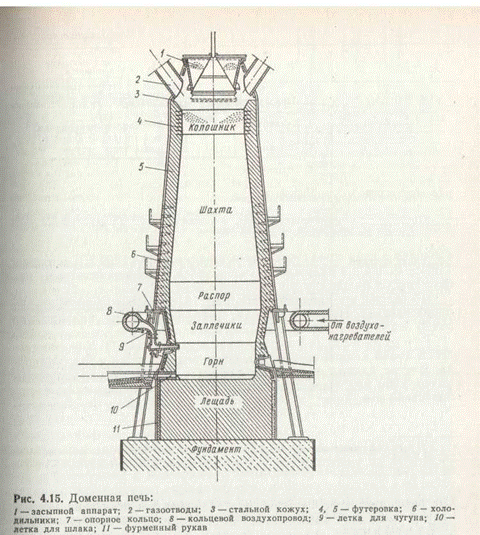
Доменные печи (рис. 9) состоят из следующих основных частей: засыпного аппарата, колошника, шахты, распара, заплечиков, горна, фурм и лещади. При помощи засыпного аппарата шихту загружают в колошник каждые 10—15 мин. Из колошника через газоотводы отводят газ. Сырьевая шихта движется вниз по шахте, имеющей вид усеченного конуса, подогревается, после чего происходят процессы восстановления железа. В горн через фурмы вдувают горячий воздух для горения топлива. В области фурм температура достигает 1600—1800°С. Восстановленное в области распара (900°С) и заплечиков (1000°С) металлическое железо проходит зону высоких температур, плавится, насыщается углеродом и стекает в горн в виде чугуна. Шлак и чугун периодически выводятся из печи через летки. Стальной кожух доменной печи футеруется огнеупорным шамотным кирпичом. Огнеупорная футеровка охлаждается специальными холодильниками. Производительность доменных печей повышается увеличением их рабочего объема. Современные доменные печи имеют объем до 5000 м3 и обеспечивают выплавку стали до 4 млн. т в год.
Барабанная вращающаяся печь представляет собой стальной барабан, футерованный огнеупорным кирпичом и установленный на опорных роликах под небольшим уклоном к горизонтали.
|
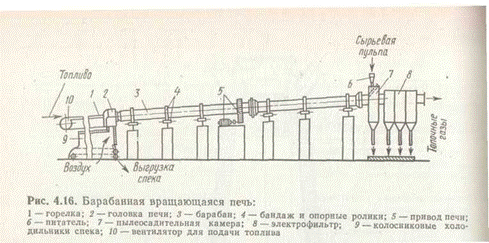
Барабан вращается вокруг своей оси со скоростью 0,5— 2,0 об/мин при помощи венцовой шестерни и привода от электромотора. При вращении происходит развитие реакционной поверхности и перемешивание твердых и газообразных реагентов; твердые материалы пересыпаются в потоке газа.
Барабанные печи чаще всего представляют собой агрегаты прямого нагрева, т. е. обогреваемые главным образом непосредственным соприкосновением обжигаемого материала с факелом и раскаленными топочными газами. Барабанные вращающиеся печи отличаются большими размерами (длина до 200 м, диаметр до 5 м), высокой производительностью, простотой устройства и обслуживания, устойчивостью в работе. По этим причинам барабанные печи широко распространены и служат типовыми печами и сушилками, применяемыми в производстве цемента и других силикатных материалов, глинозема, соды, щелочей, солей и многих других. На рис. 10 изображена барабанная вращающаяся печь для производства цементного клинкера. Исходная шихта (сырьевая смесь) загружается в верхнюю часть печи и движется противотоком топочным газам, образующимся при сжигании газообразного, жидкого или пылевидного топлива, подаваемого в нижнюю часть печи. Сырьевая смесь проходит в печи зоны сушки, кальцинации (900—1200°С), спекания (1300—1450°С) и охлаждения. Спекшийся материал (клинкер) выгружается в нижнем конце — головке печи.
По такому же принципу работают барабанные печи в других производствах. Некоторые из них (например, печь кальцинации соды) могут работать по принципу прямотока.
Туннельная (канальная) печь (рис. 11) представляет собой канал длиной до 200 м, выложенный из огнеупорного кирпича.
|
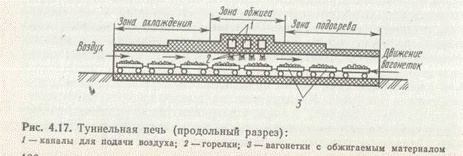
Внутри канала по рельсам движутся вагонетки с обжигаемым материалом или изделиями навстречу потоку топочных газов (зоны подогрева и обжига), а затем потоку воздуха (зона охлаждения). Это топливные печи прямого нагрева — в зоне обжига сгорает природный газ или мазут. Туннельные печи широко применяют для обжига огнеупоров и других керамических изделий.
Ванными называются печи, в которых твердый материал плавится и подвергается дальнейшей термической и химической переработке в жидком состоянии. Это топливные печи прямого нагрева; теплота передается нагреваемому материалу конвекцией от горения газов и лучеиспусканием от факела горения топлива, раскаленных стен и свода печи.
Ванные печи широко применяют в производстве сталей, цветных металлов, в стекловарении. В наиболее распространенных ваннах отражательных печах теплопередача осуществляется «отражением» теплоты от факела горящего топлива и нагретого свода к нагреваемому материалу. Примером таких печей может служить стекловаренная печь (рис. 12).
|
|
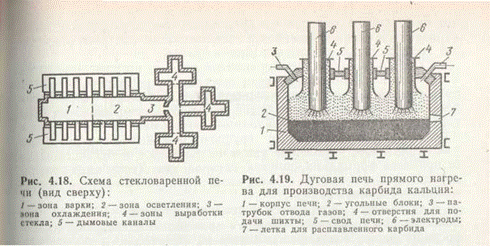
Электрические печи подразделяют на печи сопротивления, цуговые, комбинированные и индукционные.
В печах сопротивления проводником тока, обладающим большим сопротивлением, может служить или обжигаемый материал (прямой нагрев), или специальные проводники (косвенный нагрев), в дуговых печах нагрев материала осуществляется за счет теплоты дуги, которая образуется или между электродом и нагреваемым материалом (прямой нагрев), или между двумя электродами (косвенный нагрев). Комбинированные печи работают на сочетании обоих принципов, т. е. с использованием дуги и сопротивления материала. Так, например, электродуговая печь прямого нагрева для производства карбида кальция (рис. 13) представляет собой металлический корпус, выложенный огнеупорным кирпичом. В свод печи вставлены электроды. Нижний под печи, имеющий уклон к месту выгрузки карбида, выложен угольными блоками. Около электродов расположены отверстия для подачи шихты. Реакционные газы отводятся через патрубки, а расплав карбида — через летку. Мощность современных карбидных печей достигает 40 тыс. кВт.
ПРОЦЕССЫ И РЕАКТОРЫ ДЛЯ СИСТЕМЫ ТВЕРДОЕ —ЖИДКОСТЬ (Т —Ж)
Многие химические производства основаны на процессах с участием твердых и жидких реагентов — адсорбция и десорбция твердыми поглотителями растворенных веществ, растворение и кристаллизация из растворов, плавление и кристаллизация из расплавов, полимеризация жидких мономеров в твердые полимеры, диспергирование твердых тел в жидкости и многие другие.
Адсорбцией на активированном угле, силикагеле, цеолитах, и других адсорбентах извлекают металлы из растворов, очищают смазочные масла и другие нефтепродукты, осветляют технические растворы, выделяют йод из буровых вод. Большое значение как сорбенты имеют высокомолекулярные ионообменные смолы, при помощи которых ведут такие крупномасштабные операции, как умягчение воды, извлечение урана из растворов и пульп, очистку от примесей формалина, спиртов, сахаров, вин. Десорбцией получают уловленные вещества в более концентрированном виде, одновременно регенерируя сорбент.
Растворение твердых веществ в жидкостях — один из наиболее распространенных приемов в химической технологии. Условно растворение можно разграничить на физическое и химическое. В первом случае происходит лишь разрушение кристаллической решетки и растворенный компонент может быть снова выделен в твердом виде путем кристаллизации. Такой тип растворения применяют в производстве минеральных солей. При химическом растворении при взаимодействии растворителя и растворенного вещества природа его изменяется и кристаллизация вещества в первоначальном виде, как правило, невозможна. Характерным примером может служить растворение металлов в кислотах при травлении поверхности металлов, при получении медного купороса из медных отходов и серной кислоты.
Особое значение в технологии имеет избирательное растворение твердых веществ — экстрагирование и выщелачивание, основанные на разной растворимости компонентов смеси в различных растворителях. Процессы растворения, экстрагирования и выщелачивания на практике обычно сопровождаются кристаллизацией из растворов. Кристаллизация особенно широко применяется в производстве солей и минеральных удобрений, в металлургии.
Равновесие в системе Т—Ж описывается правилом фаз и выражается диаграммами фазового состояния. На расчетах с помощью фазовых диаграмм основана технология силикатных материалов, технология минеральных солей, кальцинированной соды. Для обратимых химических процессов с участием твердых и жидких реагентов равновесие характеризуется константами равновесия химических реакций в жидкой фазе.
Реакторы для процессов Т—Ж (рис. 14), так же как реакторы Ж—Г, являются типовой химической аппаратурой.
|
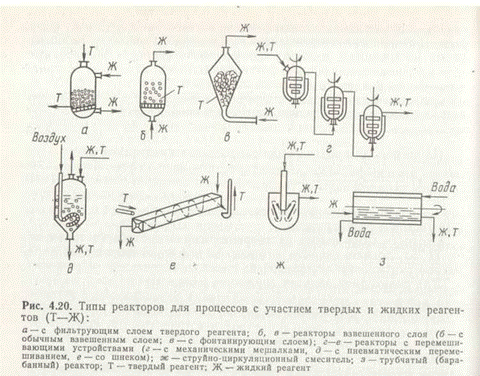
В них производят как физические операции (растворение, экстрагирование, кристаллизацию), так и химические процессы. Приемы развития поверхности контакта фаз и их относительного перемещения зависят от изменений, претерпеваемых твердой фазой. При изменении размеров и формы твердых частиц (растворение) широко применяют реакторы с перемешивающими устройствами. Другой прием ускорения относительного перемещения фаз — это пропускание жидкости через фильтрующий или взвешенный слой твердого материала. Этот прием применяется и тогда, когда твердые частицы не изменяют форму и размер (ионообмен).
ПРОЦЕССЫ В СИСТЕМАХ ТВЕРДОЕ— ТВЕРДОЕ (Т — Т), ЖИДКОСТЬ —ЖИДКОСТЬ (Ж —Ж) И МНОГОФАЗНЫЕ
Процессы с участием двух твердых фаз и более (Т—Т) обычно представляют собой спекание твердых веществ при их обжиге. Спекание — это получение твердых пористых кусков из пылевидных или порошкообразных материалов при их нагреве до температуры ниже температуры плавления. Спекание применяется при агломерации руд в порошковой металлургии, в производстве глинозема (оксида алюминия); особенно широко процессы спекания используют в технологии силикатных материалов и изделий — вяжущих веществ, керамики, огнеупоров и др.
Процессы, происходящие между реагентами в двух несмешивающихся жидких фазах (Ж—Ж), включают экстрагирование, эмульгирование и деэмульгирование. Экстрагирование основано на избирательной растворимости жидкостей в различных растворителях. Оно применяется в том случае, если ректификация жидкой смеси невозможна (низкая термическая стойкость, близость температур кипения компонентов и др.). Экстрагирование используется при очистке нефтепродуктов, при извлечении фенола из надсмольных и сточных вод коксования и полукоксования, в производстве анилина, брома, иода. Эмульгирование — процесс диспергирования одной жидкости в другой, а д е э м ул ьг и р о в а н и е — расслоение эмульсий на исходные жидкости. Эмульсии и, следовательно, эмульгирование применяют в производстве лекарств, пищевых продуктов, пигментов и красок, а также для получения многих высокомолекулярных соединений методом эмульсионной полимеризации. Примером деэмульгирования может служить обезвоживание нефти путем разрушения ее эмульсии с водой с применением ультразвука или других методов.
Реакторы для гетерогенных жидкофазных процессов аналогичны гомогенным реакторам. Они обычно имеют перемешивающие устройства и внутренние теплообменники. В промышленности для взаимодействия несмешивающихся жидкостей используют реакторы периодического и непрерывного действия, единичные и каскады. Экстрагирование осуществляют также в колоннах с насадкой или ситчатыми полками, при противоточном режиме движения жидких фаз: тяжелая жидкость сверху вниз, а легкая — снизу вверх.
<== предыдущая лекция | | | следующая лекция ==> |
КЛАССИФИКАЦИЯ ХИМИЧЕСКИХ РЕАКТОРОВ | | | Каталитические процессы и реакторы |
Дата добавления: 2016-09-26; просмотров: 3709;