КЛАССИФИКАЦИЯ ХИМИЧЕСКИХ РЕАКТОРОВ
Для реакторов характерны не только разнообразные конструктивные решения, но и различные способы их действия. Однако, несмотря на большие различия в конструкции, имеются общие практически для всех реакторов характеристики их функционирования. К ним относятся способ подвода реагентов и продуктов реакции; режим движения и перемешивания реагентов в реакционном пространстве реактора; условия теплообмена и температурный режим в аппарате; фазовый состав реагентов и продуктов реакции. Поэтому рассмотренная ранее классификация химических процессов по ряду признаков в известной степени относится и к реакторам, поскольку эти признаки существенно влияют на тип и конструкцию аппарата. Так, тепловой эффект реакции требует различных теплообменных устройств для отвода или подвода теплоты в реакционный объем. Поэтому деление процессов на экзо- и эндотермические требует выбора и соответствующего химического реактора. По тем же причинам реакторы, так же как и химические процессы, делят по наивысшей температуре процесса на низко- и высокотемпературные; по применяемому давлению — на аппараты, работающие на высоком, повышенном, нормальном и низком (под вакуумом) давлениях. Реакторы также классифицируют по фазовому состоянию реагентов на аппараты для осуществления гомогенных и различных гетерогенных процессов.
Но наиболее важными характеристиками работы любого химического реактора являются: 1) способ подвода и отвода реагентов; 2) режим движения и перемешивания реагентов; 3) температурный режим в реакционном объеме аппарата. Рассмотрим классификацию реакторов по этим признакам.
СПОСОБ ПОДВОДА И ОТВОДА РЕАГЕНТОВ
Он может осуществляться периодически, непрерывно и полупериодически (полунепрерывно). По аналогии с технологическими процессами различают и реакторы периодического, непрерывного и полунепрерывного действия.
Реакторы периодического действия. В такие реакторы реагенты загружают в начале операции. После определенного времени, необходимого для достижения заданной степени превращения, аппарат разгружают. Основные параметры процесса (концентрация реагентов и продуктов реакции, температура, давление и т. п.) изменяются во времени. Среднюю скорость процесса можно измерить производительностью реактора. Истинная же скорость сильно и нелинейно меняется в течение периода работы реактора, во-первых, вследствие понижения концентрации исходных реагентов (по логарифмическому закону); во-вторых, вследствие неизотермичности процесса (обычно повышение температуры в начале периода и понижение в конце его). На скорость превращения часто сказывается также появление новых фаз в процессе работы такого реактора. Реакторы периодического действия работают, как правило, при сильном перемешивании реагентов, близком к полному смешению, и соответственно при одинаковой температуре во всем реакционном объеме в любой момент времени работы.
Реакторы непрерывного действия (проточные). Эти реакторы от пуска до остановки непрерывно (или систематическими порциями) питают исходными веществами и выводят из них продукты реакции. Величина, обратная времени пребывания (времени контакта), называется объемной скоростью u, которую можно определить как отношение расхода материала (т. е. объем поступающего вещества Vp за время t) к полезному реакционному объему V.
u= Vp/V.
Таким образом, объемная скорость может характеризовать производительность непрерывно действующего аппарата.
Сростом объемной скорости для процессов с одномаршрутными реакциями производительность (интенсивность) реактора увеличивается, однако при этом падает степень превращения (выход продукта) и растет сопротивление движению реагентов через аппарат.
рис. 4.
Поэтому объемную скорость целесообразно увеличивать лишь до некоторого предела, определяемого также экономическими соображениями.
Реакторы полунепрерывного действия. Реакторы этого типа хактеризуются тем, что сырье поступает в аппарат непрерывно или определенными порциями через равные промежутки времени, а продукты реакции выгружаются периодически. Возможна и непрерывная выгрузка продукта при периодической подаче сырья. Такие реакторы работают в переходном режиме, основные параметры процесса изменяются во времени.
РЕЖИМ ДВИЖЕНИЯ И ПЕРЕМЕШИВАНИЯ РЕАГЕНТОВ
Различают два вида перемешивания реагентов в потоке, проходящем через реактор — продольное (осевое) и радиальное. Продольное перемешивание обусловливает смешение компонентов потока только что вошедших в реактор с ранее находящимися в нем, т. е. перемешивание вдоль длины (высоты) реактора. Радиальное перемешивание обусловливает смешение компонентов внутри слоя движущегося потока по его радиусу. Продольное перемешивание выравнивает концентрационные и температурные поля по длине реактора, а радиальное — по его радиусу. Именно продольное перемешивание определяет тип реактора, поскольку оно характеризует структуру потока, неоднородности поля скоростей, концентраций и температур, время пребывания компонентов в реакционной зоне, интенсивность смешения продуктов реакции и исходных веществ, т. е. все, что так или иначе наиболее существенно влияет на протекание ХТП. Поэтому по режиму движения и перемешивания реагентов различают два предельных типа реакторов непрерывного действия: идеального вытеснения и полного (идеального) смешения (перемешивания).
Реактор идеального вытеснения. Эти реакторы характеризуются тем, что реагенты последовательно «слой» за «слоем» без перемешивания ламинарным потоком проходят весь реакционный путь, определяемый, как правило, длиной (высотой) аппарата.
|
|
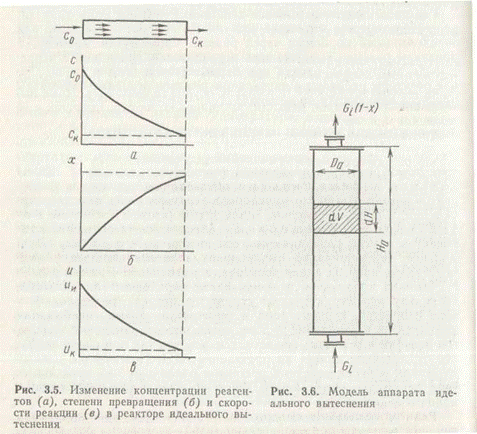
Реакторы полного смешения. Они характеризуются тем, что частицы реагента (ион, молекула или зерно твердого материала), попавшие в данный момент времени в аппарат, благодаря интенсивному перемешиванию имеют равную со всеми частицами вероятность первыми покинуть его. В реакторах полного смешения любой элемент объема мгновенно смешивается со всем содержимым реактора, так как скорость циркуляционных движений по высоте и сечению аппарата во много раз больше, чем скорость линейного перемещения по оси реактора. нецелесообразным.
В системе Г—Т к типу смешения приближается режим работы аппаратов со взвешенным (кипящим) слоем (КС) зернистого материала, причем наиболее близки к режиму полного смешения аппараты КС с мешалками (рис. 7). Близки к режиму полного перемешивания аппараты циклонного типа, применяемые для сжигания серы и обжига сульфидных руд.
|
|
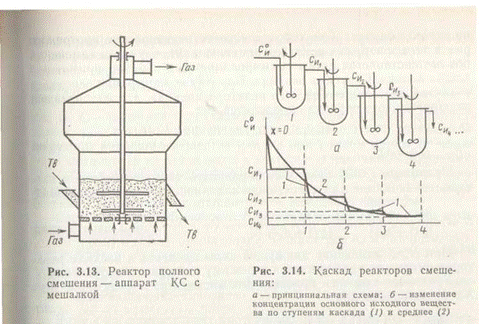
Каскад реакторов полного перемешивания. Их применяют для обеспечения достаточного общего выхода продукта, поскольку в единичном реакторе смешения при больших степенях превращения движущая сила процесса стремится к нулю и его скорость оказывается очень низкой. В каскаде реакторов полного перемешивания со сравнительно небольшой степенью превращения в каждой ступени (рис. 8) состав реакционной смеси изменяется при переходе из одного аппарата в другой, а в каждом реакторе концентрационные и температурные поля безградиентны.
Расчет каскада реакторов осуществляется путем суммирования всех изменений, происходящих в каждой ступени каскада. С ростом числа реакторов в каскаде реакционный объем для достижения одной и той же степени превращения должен уменьшиться (рис. 9).
|
По температурному режиму реакторы подразделяют на адиабатические, изотермические и политермические.
Адиабатические реакторы. Такие аппараты при спокойном (без перемешивания) течении потока реагентов не имеют теплообмена с окружающей средой, так как снабжены хорошей тепловой изоляцией. Вся теплота реакции аккумулируется потоком реагирующих веществ. Изотермические реакторы. Они имеют постоянную температуру во всех точках реакционного объема.
Способы достижения изотермичности различны. Можно приблизиться к изотермическим условиям процесса при помощи теплообменных устройств, помещенных в реакционный объем (для отвода теплоты в экзотермических и подвода в эндотермических реакциях). При этом в каждом элементарном объеме аппарата отвод или подвод теплоты должен быть равен теплоте реакции. Изотермический режим достигается при интенсивном перемешивании реагентов в аппарате с мешалкой и в реакторах со взвешенным (кипящим, пенным) слоем, т. е. в аппаратах, в которых гидродинамический режим обеспечивает приближение к полному перемешиванию реагентов с продуктами реакции и инертными компонентами. В отдельных случаях изотермичность в реакторе достигается за счет теплового равновесия экзо- и эндотермического превращений, например компенсацией теплоты экзотермической реакции испарением растворителя (воды).
Политермические реакторы. Политермическими называются реакторы, в которых теплота реакции лишь частично компенсируется за счет отвода (подвода) теплоты или процессов с тепловым эффектом, противоположным по знаку основному.
К политермическим аппаратам относят реакторы с малой степенью смешения реагирующих веществ и теплообменниками, помещенными внутри реакционного объема, например трубчатые контактные аппараты.
Для выбора типа реактора и определения его производительности часто приходится прибегать к экспериментальным исследованиям и переносу результатов эксперимента на промышленные условия. Такой переход от лабораторных или опытно-промышленных условий реализации процесса к заводским осуществляется при помощи моделирования.
Моделирование.Моделирование — процесс сопоставления информации, полученной каким-либо образом, с информацией, которую получают на модели того или иного явления или процесса.
Моделями обычно называют системы, которые отражают отдельные, ограниченные в нужном направлении стороны явлений рассматриваемого процесса.
Моделирование процесса и соответствующего ему реактора, как правило, начинается с изучения физической сущности явления, установления переменных величин, влияющих на изучаемое явление, для чего составляют так называемую общую функциональную зависимость. Эта зависимость может быть представлена в виде системы уравнений, связывающих входящие в нее основные параметры. Для описания того или иного технологического процесса, а следовательно, и аппарата, в котором этот процесс будет осуществляться, обычно используют следующие основные уравнения: 1) стехиометрические уравнения химической реакции; 2) уравнение скорости химической реакции; 3) уравнение сохранения массы вещества (материальный баланс); 4) уравнение сохранения энергии (тепловой баланс); 5) уравнение гидродинамики.
Как правило, система этих уравнений в аналитическом виде может быть решена лишь в очень редких случаях. Обычно же приходится вводить целый ряд упрощающих допущений, начальных и граничных условий, после чего решение уравнений носит частный характер.
Различают три вида моделирования: по равенству основных частных соотношений, физическое и математическое.
Равенство основных частных соотношений.Данным видом моделирования иногда пользуются проектировщики, перенося не слишком ответственные операции, уже осуществленные в промышленности, с одних масштабов на другие.
Физическое моделирование.При физическом моделировании изучение данного явления происходит при его физическом воспроизведении в разных масштабах. При этом исследуется влияние на явление различных факторов (чаще всего физических: скорости потоков, интенсивности перемешивания, температуры, давления, геометрических размеров и т. п.). Если изучается скорость какого-либо химико-технологического процесса, то предполагается, что кинетика собственно химического превращения известна, т. е. описана соответствующим кинетическим уравнением.
Эксперименты проводятся непосредственно на самой изучаемой модели, а результаты исследования обобщаются в виде безразмерных критериальных уравнений. Безразмерная форма позволяет распространить полученные зависимости на группу подобных между собой явлений. Как правило, критериальное уравнение включает в себя целый ряд критериев и симплексов подобия. Обычно различают кинетические, диффузионные, тепловые и гидродинамические критерии подобия.
Кинетические критериивключают в основном три критерия:
критерий Дамкелера, характеризующий отношение скорости химической реакции к изменению концентрации основного исходного вещества по высоте (длине) реактора.
критерий Маргулиса, характеризует отношение скорости процесса к скорости реакционного потока:
критерий Аррениуса- характеризует влияние температуры на процесс.
Диффузионные критерииописывают явления массопереноса в системе.
Диффузионный критерий Пекле, характеризующий
отношение скорости потока к приведенной скорости молекулярной
диффузии.
Диффузионный критерий Прандтля
характеризует отношение вязкостных свойств и диффузионной способности системы;
Критерий Нуссельта, характеризующий меру отношения скорости процесса к приведенной скорости молекулярной диффузии.
Гидродинамические критерииподобия: Рейнольдса, Архимеда, Фруда.
Тепловые критерииподобия:
Нуссельта, Прандтля.
Метод физического моделирования используют в инженерной практике для перехода от исследовательских разработок к промышленному внедрению, особенно применительно к относительно несложным системам (например, гидравлическим или тепловым с однофазным потоком), поскольку приходится оперировать ограниченным числом критериев.
При анализе сложных, многофазных систем, с которыми чаще всего и приходится иметь дело в химико-технологических процессах, теория подобия наталкивается на принципиальные трудности, обусловленные сложностью масштабных переходов, большим набором определяющих критериев и симплексов подобия, многосторонностью связей в системе, неизбежностью введения упрощающих допущений и т. п.
Математическое моделирование. Математическое моделирование является методом, при котором изучение явления осуществляется на так называемой математической модели. Математической моделью принято называть систему уравнений (конечных или дифференциальных), которая описывает всю совокупность явлений, составляющих данный процесс. При этом предполагается, что физическая сущность явления известна и для его описания найдена модель, адекватная (соответствующая) изучаемому физическому образцу. В модели должны быть учтены все основные факторы, влияющие на процесс. Для этого пользуются теоретическими предпосылками, характеризующими данное или сходное по природе явление, а также результатами практической деятельности аналогичных или родственных производств и сведениями экспериментального характера.
Основная отличительная особенность математического моделирования заключается в том, что все изменения условий (так называемая деформация модели) производятся на самой модели (система уравнений) путем параметрического изменения уравнений, добавления новых и перестройки уже внедренных связей. Поскольку все эти манипуляции выполняются кибернетически при помощи ЭВМ, надобность в эксперименте или отпадает совсем, или резко сокращается число переменных, подлежащих исследованию на физической модели.
При математическом моделировании можно решить и задачу оптимизации, т. е. установить такие параметры процесса, которые обеспечат максимальную производительность аппарата при заданном качестве готовой продукции. Именно благодаря широким возможностям метода математического моделирования, а также бурному развитию вычислительной техники этот метод находит все большее распространение не только при создании новых производств, но и при совершенствовании действующих в виде создания автоматизированных систем управления технологическим процессом (АСУТП) и целой химико-технологической системой (ХТС).
Дата добавления: 2016-09-26; просмотров: 5205;