Определение понятия «система»
Задачи анализа и синтеза процессов и объектов ОМД, как сложных систем
Определение понятия «система»
Термин «система» используют в тех случаях, когда хотят охарактеризовать исследуемый или проектируемый объект как нечто целое (единое), сложное, о котором невозможно сразу дать представление, показав его, изобразив графически или описав математическим выражением.
Понятие «система» в переводе с греческого «συστημα» означает «составленное из частей», «соединение», от «соединяю, составляю». Как показывает анализ [1], в термин система на разных стадиях ее рассмотрения можно вкладывать разные понятия, говорить как бы о существовании системы в разных формах.
В результате обобщения многочисленных определений понятия система предлагается следующее определение [2]: система – это множество взаимосвязанных и взаимодействующих элементов любой природы, объединенных единством цели или общими целенаправленными правилами взаимоотношений.
Под элементом принято понимать предел членения системы с точки зрения аспекта рассмотрения, решения конкретной задачи, поставленной цели.
Раскроем определение «система» применительно к понятию «технологическая система» – совокупность функционально взаимосвязанных средств технологического оснащения, предметов производства и исполнителей для выполнения в регламентированных условиях производства заданных технологических процессов и операций[1]. Различают четыре иерархических уровня технологических систем: технологические системы операций, технологические системы процессов, технологические системы производственных подразделений и технологические системы предприятий.
Подсистема технологической системы – технологическая система, выделяемая по функциональному или структурному признаку из технологической системы более высоко уровня.
Элемент технологической системы – часть технологической системы, условно принимаемая неделимой на данной стадии анализа.
Работоспособное состояние технологической системы – состояние, при котором значения параметров и (или) показателей качества изготовляемой продукции, производительности, материальных и стоимостных затрат на изготовление продукции соответствуют требованиям, установленным в нормативно-технической и (или) конструкторской и технологической документации.
Технология (технологический процесс) – совокупность методов обработки, изготовления, изменения состояния, свойств, формы сырья, материала или полуфабриката, осуществляемых в процессе производства продукции.
Совершенствование производства продукции, получаемой методами обработки давлением, можно осуществлять двумя путями: 1) улучшение действующих технологических процессов и оборудования; 2) создание (разработка, исследование и проектирование) новых. Проблемы, связанные с методическими различиями понятий – улучшение систем и создание (проектирование) систем подробно рассмотрены в работе [3].
Улучшением систем называют процесс, обеспечивающий работу системы или систем согласно ожиданиям, при этом система уже создана и порядок её работы установлен. Улучшение системы означает выявление причин отклонений от заданных норм работы системы или возможностей по улучшению работы системы, т. е. получение результатов, соответствующих целям проекта.
Процесс улучшения систем характеризуется следующими шагами:
1. Определяется задача и устанавливается система и подсистемы.
2. Путем наблюдения определяются реальные состояния, условия работы или поведение системы.
3. Реальные и ожидаемые условия работы системы сравниваются, чтобы определить степень отклонения.
4. В рамках подсистем строятся гипотезы относительно причин этого отклонения.
5. Из известных фактов методом дедукции делаются выводы, большая проблема разбивается на подпроблемы путем редукции.
Метод улучшения систем основан на аналитическом подходе, т. е. причины отклонений ищут в границах самой системы, исходной посылкой служит тот факт, что, все отклонения вызваны дефектами в элементах системы и их можно объяснить специфическими причинами. Функция, назначение, структура и взаимодействие с другими системами при этом под сомнение не ставится.
Создание и проектирование систем отличается от улучшения систем исходными посылками и используемыми методами [2].
В противоположность методологии изменений по улучшению систем, системный подход является методологией проектирования, основывающейся на следующих положениях:
1. Проблема определяется с учетом взаимосвязи с большими (мега) системами, в которую входит рассматриваемая система и с которыми она связана общностью целей.
2. Цели системы обычно определяются не в рамках подсистем, а их следует рассматривать в связи с более крупными (мега) системами или системой в целом.
3. Существующие проекты следует оценивать величиной вмененных издержек или степенью отклонения системы от оптимального проекта.
4. Оптимальный проект обычно нельзя получить путем внесения небольших изменений в существующие принятые формы, он основывается на планировании, оценке и принятии таких решений, которые предполагают новые и положительные изменения для системы в целом.
Выбор методического подхода – улучшать действующие технологические процессы или/и создавать новые, должен основываться на тех целях, которые стоят в настоящее время или встанут в будущем перед производителями продукции.
Глобальная цель анализа и синтеза состоит в выборе и обеспечении таких условий функционирования технологических процессов (ТП), при которых в заданном интервале времени [0, T] они находятся в работоспособном состоянии. Показателем достижения цели будет мера степени соответствия реального результата функционирования ТП требуемому.
Условия работоспособности ТП нами приняты [4] в виде отношений
Yi ( t )ÎYiT,"tÎ [0, T], i = 1, ... , n, (1.1)
где YiT – область допустимых значений i-х характеристик качества продукции и выходных параметров, определяющих требования к ТП, заданная следующим образом:
YiT = [ai , bi] , i = 1, ... , k, (1.1а)
YiT ³ аi , i = k+1, ... , m, (1.1б)
YiT £ bi , i = m+1, ... , n, (1.1в)
где ai и bi – нижняя и верхняя границы.
С позиций точности функционирования встаёт задача обеспечения минимального отклонения фактических значений характеристик от требуемых, для чего введем следующий критерий
"t, ïY(t) – YTï= dY(t) ®min,
а с позиций стабильности (устойчивости)
"t,"Y(t), dY Î D,
где D – поле допуска на отклонения dY, tÎ [0, T].
Сформулируем основные задачи анализа и синтеза процессов и объектов ОМД, как сложных систем [4]:
1. Задачи анализа (прямые задачи), решаемые при условии известной структуры технологической системы (или выбираемой на стадии создания) и наличия математических моделей:
– оценка состояния, когда по заданным значениям входных параметров (управляемых и неуправляемых) Хi определяются значения внутренних Zj и выходных параметров Yi в заданный момент времени;
– оценка работоспособности, которая включает анализ влияния возможных производственных и эксплуатационных отклонений входных параметров dХi от расчетных на разброс внутренних Zj и выходных параметров dYi;
– прогнозирование состояния (разброс параметров и постепенные отказы), когда по заданным в начальный момент времени значениям входных параметров Хi предсказывается момент отказа функционирования t или интервал времени, в течение которого возможен этот отказ;
– выбор оптимальных номинальных значений входных параметров Хiопт, обеспечивающих экстремальные значения отдельных выходных параметров Yiextr при наложении ограничений на остальные.
2. Задачи параметрического синтеза, процесс выбора параметров технологических систем, обеспечивающих заданные требования к качеству их функционирования:
– поиск заданного состояния технологической системы Zj по заданным условиям работоспособности;
– выбор совокупности управляемых (настроечных) параметров, позволяющих эффективно осуществлять подстройку и управление качеством функционирования технологической системы, и оценка допустимых интервалов их вариаций;
– оценка работоспособности при статистическом характере выбранных исходных параметров и возможных трендовых изменениях;
– оптимизация поля допусков на разброс исходных параметров по критерию минимума полей рассеивания выходных параметров;
– оптимизация номинальных значений параметров, которые изменяются во времени, например, износ инструмента.
На рис. 1.1 приведена графическая иллюстрация тех преобразований информации, которые совершаются в процессе анализа и синтеза [2].
Отличие задач анализа от синтеза состоит в том, что в случае анализа при выбранном значении вектора входных параметров вектор выходных параметров может и не находиться в заданной области работоспособности, поэтому основная задача синтеза состоит в поиске вектора входных параметров по заданной области работоспособности (области пространства состояний технологического процесса).
Рис. 1.1. Графическая иллюстрация анализа и синтеза [2]: 1 – точка, отвечающая некоторому допустимому вектору X; 2 – точка, отвечающая некоторому вектору Y(X); 3 – точка, удовлетворяющая требованиям по показателям качества; А – анализ; С – синтез
В развитие рассмотренных выше подходов нами в работе [14] сформулированы следующие принципы структурно-параметрического подхода к совершенствованию технологических процессов ОМД: цель совершенствования должна быть подчинена принципам внешнего дополнения и целесообразности, как основным системообразующим факторам; процедуры (процесс) совершенствования, как определенно направленные воздействия, должны осуществляться на стадиях проектирования и функционирования технологического процесса, как системы, подчиняться принципам развития и рационального поведения и обеспечивать, на основании действия принципа отношения зависимости, такие изменения структуры, ритма функционирования и пространства состояния внутренних параметров, которые приведут технологический процесс к такому состоянию или эволюции состояний, при котором будет достигнута глобальная цель и подчиненные ей промежуточные цели, установленные на основании принципа отношения необходимости (или предшествования). Структурная схема применения принципов совершенствования приведена на рис. 1.2.
|
|
|
|
|
|
|
|
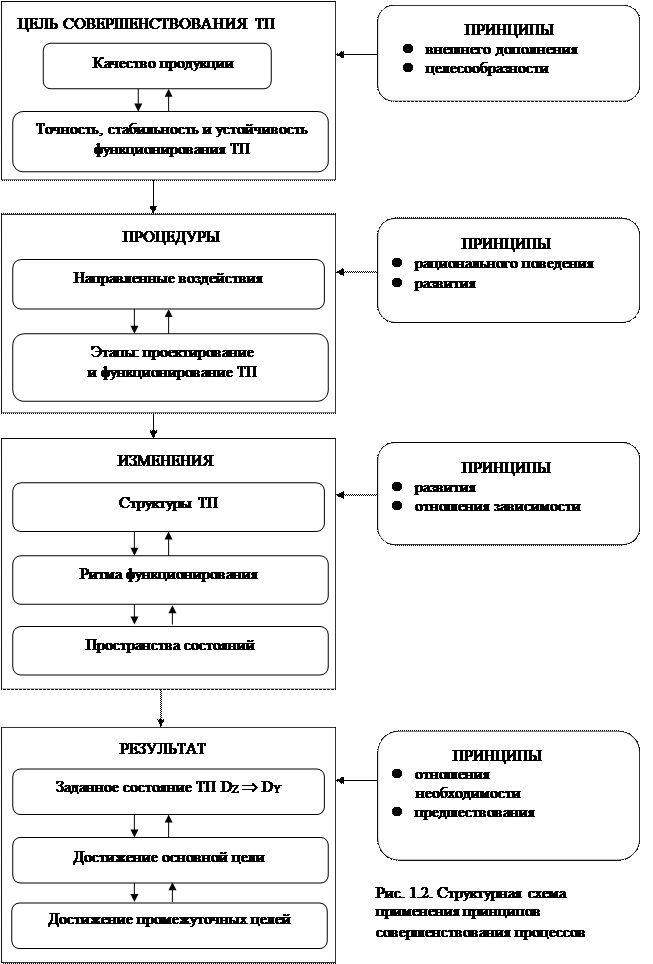
Дата добавления: 2017-01-26; просмотров: 2606;