Структура материалов, наблюдаемая невооруженным глазом или при небольших увеличениях, называется макроструктурой.
Макроанализ проводят путем изучения:
· изломов;
· макрошлифов;
· внешних поверхностей заготовок и деталей.
Наружные, или поверхностные макродефекты расположены непосредственно на поверхности изделий и обнаруживаются невооруженным глазом или при помощи лупы. К ним относятся:
· продольные и поперечные трещины. Представляют собой разрывы металла, возникающие при неравномерном резком нагреве или охлаждении слитков, в процессе закалки стальных изделий;
· неметаллические включения. Представляют собой несплошности металла в виде включений оксидов, сульфидов, силикатов и являются очагами, инициирующими вязкое разрушение алюминиевых и стальных деталей;
· волосовины, рис.4,(образуются при обработке литого металла давлением за счет вытягивания окисленных и потому не заваривающихся газовых пузырей в тонкие трещины, расположенные в направлении деформирования);
· пригар (трудноотделимая корка из смеси металлов, формовочного песка и шлака);
· трещины и непровар в сварных изделиях.
Рис.1 Трещины Рис.2 Раковины
Рис.3 Неметаллические включения Рис.4 Волосовины
Дефектами пластически деформированного металла является надрывы (обусловленные слишком большой степенью деформации), окалина (слой окисленного металла).
Внутренние дефекты выявляются при изучении изломов и макрошлифов. Излом – это поверхность, образовавшаяся вследствие разрушения металла. Изломы изучает наука фрактография. Анализ изломов играет важную роль при оценке причин и динамики разрушения металлических деталей, узлов, которое нередко приводит к авариям. Основными причинами, способствующими возникновению изломов, являются: дефекты строения металлов и сплавов; превышение эксплуатационных нагрузок, действующих на деталь; нарушения технологии изготовления детали; отклонение ее размеров и формы от технических условий, наличие концентраторов напряжений.
Цвет излома может быть разным – у сталей и белых чугунов он светло-серый, у серых чугунов и графитизированных сталей он черный. В зависимости от состава, строения сплава, наличия дефектов, условий обработки и эксплуатации изломы могут быть:
Вязкими - образуются при однократном статическом или динамическом нагружении, которое вначале вызывает пластическую деформацию, а затем – разрушение. Поверхность излома имеет матовый цвет и волокнистое строение. Форма и размер зерен при этом сильно искажаются. Для вязкого разрушения характерно также ямочное («чашечное») строение. На рис.5 показан эскиз поверхности излома детали, где представлена картина значительных пластических деформаций, возникающих в месте излома при разрушении детали. На рис.6 представлена фотография, иллюстрирующая волокнистость и чашечное строение поверхности излома.
Рис.5 Вязкий излом (эскиз) Рис.6 Вязкий излом (фото)
Хрупкими – образуются при однократном статическом или динамическом нагружении без заметной пластической деформации, рис.7. Поверхность излома имеет кристаллическое строение и характерный металлический блеск. Работа развития трещины при хрупком разрушении мала, а скорость распространения трещины весьма велика. Обычно, в хрупком изломе можно видеть форму и размер зерен металла, т. к. излом происходит без значительной пластической деформации и зерна при разрушении металла не искажаются. При этом излом может происходить как по границам зерен (межкристаллический), так и по зернам металла ((транскристаллический). Примером является камневидный излом металла при перегреве, когда трещины зерен обогащаются примесями и тем самым охрупчиваются, рис.8.
Различают и другие виды хрупких изломов – ручьистый, шиферный, форфоровидный и др. Обычно изломы имеют смешанный характер.
Рис.7 Хрупкий излом (эскиз) Рис.8 Хрупкий излом (фото)
Усталостные изломы возникают в результате разрушения металла под воздействием циклических (знакопеременных) нагрузок. Излом имеет ряд характерных зон:
· очаг разрушения – небольшая зона, содержащая фокус излома, - место локальной концентрации напряжений, где возникла зародышевая микротрещина усталости и откуда начинается ее развитие, рис.9, поз.1. Эта зона плоская и гладкая, располагается на поверхности детали или вблизи нее. Очаг усталостного разрушения не всегда удается обнаружить невооруженным глазом.
· зона усталости - зона постепенного развития трещины усталости, формируется при последовательном продвижении трещины усталости. В этой зоне видны характерные бороздки (линии усталости), имеющие конфигурацию колец, что свидетельствует о скачкообразном продвижении фронта трещины усталости, рис.9, поз.2. Направление продвижения указывают ручьи.
· зона долома образуется на последней стадии усталостного разрушения, когда в уменьшающемся рабочем сечении напряжения возрастают настолько, что вызывают практически мгновенное разрушение, рис.9, поз.3.
|
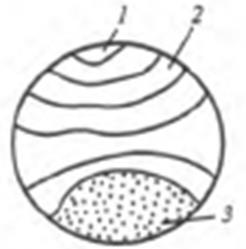
Рис.9 Усталостный излом (схема) Рис.10 усталостный излом (фото)
Другим методом макроанализа является изучение строения металлических материалов на специальных образцах - макрошлифах. Макрошлиф – это образец с плоской шлифованной и протравленной поверхностью, вырезанный из исследуемого участка детали или заготовки. Для его приготовления одну из плоских поверхностей вырезанного образца ровняют напильником или на плоскошлифовальном станке. Затем образец шлифуют вручную или на специальных станках шкурками различной зернистости, совершая возвратно-поступательное движение и переходя последовательно от крупного зерна шлифовальной шкурки к более мелкому. Образец при переходе поворачивается на 900. Обработку проводят до полного исчезновения рисок предыдущей стадии шлифования. Образец промывают водой, просушивают и подвергают глубокому или поверхностному травлению, погружая его в специальный реактив - травитель, выдерживая образец в нем по определенному режиму. Протравленный макрошлиф промывают водой, обрабатывают спиртом, высушивают фильтровальной бумагой.
Поверхностное травление, проводимое менее агрессивными травителями, позволяет:
- выявить в сплавах ликвацию (химическую неоднородность сплава, возникающую при его производстве);
- наблюдать дендритное строение литых сплавов и волокнистость, характерную для строения деформированных сплавов;
- установить способ изготовления деталей обработкой давлением или резанием;
· обнаружить дефекты и присутствие неметаллических включений;
· оценить качество сварных соединений;
· выявить структурную (возникшую в результате термической обработки) или химическую (возникшую в результате химико-термической обработки или наплавки) неоднородность сплавов и готовых изделий.
На рис. 11 представлены макрошлифы болтов, полученных разными способами. Позиция а: при изготовлении болта методом волочения его волокна повторяют конфигурацию сечения болта. Такой болт выдерживает большие нагрузки.
Позиция б: при изготовлении болта точением, волокна располагаются параллельно.
Рис.11 Макрошлифы болтов
Поэтому, в месте перехода от одного диаметра к другому появятся концентраторы напряжений, которые снижают прочность болта.
Дата добавления: 2016-09-06; просмотров: 4961;