ОБОГАЩЕНИЕ ПОЛЕЗНЫХ ИСКОПАЕМЫХ. ОСНОВНЫЕ ХАРАКТЕРИСТИКИ
Обогащение полезных ископаемых — совокупность процессов механической переработки минерального сырья с целью извлечения ценных компонентов и удаления пустой породы и вредных примесей, которые не представляют практической ценности в данных технико-экономических условиях. В результате обогащения из руды получают концентрат, качество которого выше, чем качество руды. Качество концентрата характеризуется содержанием ценного компонента (оно выше, чем в руде), содержанием полезных и вредных примесей, влажностью и гранулометрической характеристикой.
Полезными примесями называют отдельные химические элементы или их природные соединения, которые входят в состав полезного ископаемого в небольших количествах и могут быть выделены и использованы совместно с основным ценным компонентом, улучшая его качество. Например, полезными примесями в железных рудах являются хром, вольфрам, ванадий, марганец и др. Вредными примесями называют отдельные элементы и природные химические соединения, содержащиеся в полезных ископаемых и оказывающие отрицательное влияние на качество извлекаемых ценных компонентов. Например, в железных рудах вредными примесями являются сера, мышьяк, фосфор, в коксующихся углях - сера, фосфор, в энергетических углях - сера и т.д.
Предварительное обогащение полезных ископаемых позволяет:
• увеличить промышленные запасы сырья за счет использования месторождений бедных полезных ископаемых с низким содержанием ценных компонентов;
• повысить производительность труда на горных предприятиях и снизить стоимость добываемой руды за счет механизации горных работ и сплошной выемки полезного ископаемого вместо выборочной;
• повысить технико-экономические показатели металлургических и химических предприятий при переработке обогащенного сырья за счет снижения расхода топлива, электроэнергии, флюсов, химических реактивов, улучшения качества готовых продуктов и снижения потерь полезных компонентов с отходами;
• комплексно использовать полезные ископаемые, так как предварительное обогащение позволяет извлечь не только основные полезные компоненты, но и сопутствующие, содержащиеся в малых количествах;
• снизить расходы на транспортирование к потребителям более богатых продуктов, а не всего объема добываемого полезного ископаемого;
• выделить из минерального сырья те вредные примеси, которые при дальнейшей его переработке могут загрязнять окружающую среду и тем самым угрожать здоровью людей и ухудшать качество конечной продукции.
Обогащение, как и любой другой технологический процесс, характеризуется показателями. Основные технологические показатели обогащения следующие:
• масса продукта (производительность) - Q, C, Т, выражается обычно в тоннах в час, тоннах в сутки и т.д.;
• содержание ценного компонента в продукте - а, в, S - это отношение массы ценного компонента в продукте к массе продукта; содержание различных компонентов в полезном ископаемом и в полученных продуктах принято вычислять в процентах;
• выход продукта - уи, ук, ухв - это отношение массы продукта к массе исходной руды; выход любого продукта обогащения выражают в процентах, реже в долях единицы;
• извлечение ценного компонента - ви, ек, ехв - это отношение массы ценного компонента в продукте к массе этого же компонента в исходной руде; извлечение выражается в процентах, реже в долях единицы.
Рассмотрим вариант, когда в результате обогащения получают только два продукта. В этом случае выход концентрата
ук = (C/Q) 100.
Этой формулой можно пользоваться, если известна масса продуктов. Однако часто она неизвестна. А вот содержание полезного компонента в продуктах известно практически всегда.
Ук |
а — -Э1 в -Э 100; уХв = ——— 100; Ук + Ухв = 100. |
в-Э .............. а-Э Извлечение полезного компонента в концентрат |
Вк = |
ср Qa |
100, или вк |
УкР В = YхвЭ • В + В = 100 ---- 5 &хв 5 &к 1 &хв---- -LW. а а |
Выход концентрата и хвостов через содержания определяется следующими формулами:
Полезные ископаемые на обогатительных фабриках проходят целый ряд последовательных операций, в результате полезные компоненты отделяются от примесей. Процессы обогащения полезных ископаемых по своему назначению делятся на подготовительные, вспомогательные и основные.
К подготовительным относят процессы дробления, измельчения, грохочения и классификации. Их задача - разъединить полезный минерал и пустую породу и создать нужную гранулометрическую характеристику перерабатываемого сырья.
К основным относят следующие процессы:
• гравитационные, основанные на различиях в плотности разделяемых минералов;
• флотационные (различия в поверхностных свойствах разделяемых минералов);
• магнитные (различия в магнитной восприимчивости разделяемых минералов);
• электрические (различия в электрических свойствах разделяемых минералов);
• специальные (различия в цвете, блеске, форме, естественной или наведенной радиации разделяемых минералов);
• комбинированные, в схему которых помимо традиционных процессов обогащения (не затрагивающих химического состава сырья) включены пиро- или гидрометаллургические операции, изменяющие химический состав сырья.
Задача основных процессов обогащения - разделить полезный минерал и пустую породу.
К вспомогательным относят обезвоживание, пылеулавливание, очистку сточных вод, опробование, контроль и автоматизацию. Задача этих процессов - обеспечить оптимальное протекание основных процессов.
Совокупность последовательных технологических операций обработки, которым подвергают полезные ископаемые на обогатительных фабриках, называется схемой обогащения. В зависимости от характера сведений, которые содержатся в схеме обогащения, ее называют технологической, качественной, количественной, качественно-количественной, водно-шламовой и схемой цепи аппаратов.
I.2. ГРАНУЛОМЕТРИЧЕСКИЙ СОСТАВ
При обогащении твердых полезных ископаемых приходится иметь дело с зернистым материалом, состоящим из массы зерен различной крупности. На практике за размер зерна принимают размер квадратного отверстия, через которое это зерно проваливается. Материал, прошедший через отверстие l\ и оставшийся на отверстии l2, причем l2 < l\, называется классом крупности. Крупность класса обозначают следующим способом: -l\+l2 (минус l\ плюс l2). Например, класс -25+10 мм. Характеристика массы зерен различного размера по крупности называется гранулометрической характеристикой. Гранулометрический состав материала в зависимости от крупности определяют одним из следующих способов: ситовой анализ - d > 50 мкм, седиментацион- ный анализ - d « 50^5мкм; анализ под микроскопом - d < 5 мкм. Наиболее часто для контроля процессов грохочения, дробления и измельчения на обогатительных фабриках используют ситовый анализ, т.е. рассев сыпучего материала на стандартных ситах с отверстиями различных размеров. Для ситового анализа применяют два набора стандартных сит:
1) набор, в котором за основу принято сито 200 меш (меш - количество отверстий на одном линейном дюйме), отверстие в этом сите 0,074 мм; каждое последующее сито больше предыдущего в V2 раз, т.е. модуль шкалы этого набора V2 (шкала Тейлора);
2) набор, в котором за основу принято сито с отверстием 0,012 мм; каждое последующее сито больше предыдущего в 4°Ш (метрическая шкала).
Пробы рассеивают сухим или мокрым способом в зависимости от крупности материала и необходимой точности ситового анализа. Если не требуется особой точности и материал не слипается, то применяют сухой способ рассева. Массу пробы для ситового анализа принимают в зависимости от крупности наибольшего куска в пробе:
Размер куска, мм 0,1 0,3 0,5 1 3 5 10
Масса пробы, г 25 50 100 200 300 2250 18000
Сита устанавливают сверху вниз от отверстий крупных размеров к мелким. Пробу помещают на верхнее сито и весь набор сит встряхивают на механическом встряхивателе в течение 10-30 мин. Время рассева определяется крупностью материала: при d < 5 и d > 5 мм время рассева соответственно 30 и 10 мин. Остаток на каждом сите взвешивают. Выход классов получают делением массы каждого класса на массу исходной пробы.
Результаты ситового анализа записывают в таблицу. Вычисляют суммарные выходы, представляющие собой сумму выходов всех классов крупнее (суммарный выход по плюсу) и мельче (суммарный выход по минусу) отверстий данного сита.
Характеристикой крупности называют графическое изображение гранулометрического состава сыпучего материала. Характеристики крупности строят в прямоугольной системе координат. Суммарную характеристику крупности Y = fx) строят по точкам, положение которых находят по абсциссам х - диаметрам кусков и ординатам Y - суммарным выходам классов мельче или крупнее х.
Если по оси ординат отложены выходы материала, крупнее заданного диаметра, то характеристика построена «по плюс х», если мельче данного диаметра, то «по минус х». Обе характеристики зеркально отражают друг друга и, будучи построены на одном графике, пересекаются в точке, соответствующей выходу материала, равному 50 %.
Найденная гранулометрическая характеристика позволяет:
1. По виду кривой судить о преобладании крупных или мелких зерен. Суммарные характеристики «по плюс х» бывают выпуклыми, вогнутыми и прямолинейными. Выпуклая кривая получается при преобладании в материале крупных зерен, вогнутая - при преобладании мелких зерен. Прямолинейная кривая свидетельствует о равномерном распределении в материале зерен по крупности, т.е. на любом участке характеристики на единицу изменения диаметра приходится одинаковое изменение суммарного выхода материала.
2. По кривой суммарной характеристики можно определить выход любого класса крупности.
3. На основании гранулометрической характеристики можно вывести аналитические зависимости для определения удельной поверхности материала.
I.3. ПОДГОТОВИТЕЛЬНЫЕ ПРОЦЕССЫ ОБОГАЩЕНИЯ
Задача этих процессов - разъединить полезный минерал и пустую породу и создать нужную гранулометрическую характеристику обогащаемой руды.
1.3.1. ГРОХОЧЕНИЕ
Грохочение - процесс разделения зернистых материалов по крупности на просеивающих поверхностях с калиброванными отверстиями.
Зерна (куски) материала, размер которых больше размера отверстий сита, остаются при просеивании на сите, а зерна меньших размеров проваливаются через отверстия.
Материал, поступающий на грохочение, называется исходным, остающийся на сите - надрешетным (верхним) продуктом, проваливающийся через отверстия сита - подрешетным (нижним) продуктом.
Процесс грохочения характеризуется эффективностью — выраженным в процентах или в долях единицы отношением массы подрешетного продукта к массе нижнего класса в исходном материале. Эффективность грохочения можно также определить как извлечение нижнего класса в подрешетный продукт. Пусть отгрохачивается Q тонн руды, содержащей а процентов мелочи (зерен мельче, чем отверстие грохота), при этом получается С тонн подрешетного продукта, содержащего Р процентов мелочи, и Т тонн надрешетного продукта, содержащего S процентов мелочи. Тогда по определению
„ C -100 а —и 4
E = -------- 100, или E = ------------ 10 .
Qa (100 — и)а
Эффективность грохочения определяется следующими факторами: гранулометрическим составом исходного материала, его влажностью, углом наклона грохота, амплитудой и частотой колебания грохота. По крупности выделяют три вида зерен: 1) легкие, размер которых меньше, чем отверстие грохота (d < 0,75/), такие зерна легко отгрохачиваются и не снижают эффективность; 2) трудные, размер которых близок отверстию грохота (d = /), такие зерна могут застревать в отверстиях, резко снижая эффективность; 3) затрудняющие, размер которых чуть больше отверстия грохота (d = 1^1,5/), такие зерна скапливаются на поверхности решета грохота, снижая эффективность грохочения. Таким образом, чем больше в материале трудных и затрудняющих зерен, тем ниже эффективность грохочения.
Рабочими поверхностями грохотов могут быть колосниковые решетки, набранные из параллельных брусьев (круглые, квадратные, ромбические, в виде рельсов и т.д.), стальные решета со штампованными или сверлеными отверстиями, плетеные сетки из стальной или латунной проволоки, резиновые маты со штам-
![]() |
пованными отверстиями, сита из синтетических материалов (полиуретан, капролакс и др.).
Основными типами промышленных грохотов являются: колосниковые, валковые, дуговые, барабанные, вибрационные.
Колосниковые грохоты, устанавливаемые под углом к горизонту, представляют собой решетки, собранные из колосников. Материал, загружаемый на верхний конец решетки, движется по ней под действием силы тяжести. При этом мелочь проваливается через щели решетки, а крупный класс сходит в нижнем конце (рис.1.1). Эти грохоты применяют, в основном, для крупного грохочения руд. Размер щели между колосниками - не меньше 50 мм, в редких случаях 25-30 мм. Угол наклона решетки зависит от физических свойств грохотимого материала. По практическим данным, угол наклона составляет для руд 40-45°, для углей 30-35°. При переработке влажных материалов угол наклона грохота увеличивают на 5-10°. Эффективость грохочения колосниковых грохотов невысокая, она составляет около 70 %.
Валковый грохот (рис.1.2) представляет собой наклонную площадку, набранную из горизонтальных параллельных осей, которые свободно вращаются в подшипниках. На каждую ось надет ряд металлических дисков (валков), которые располагаются в
![]() |
![]() |
шахматном порядке. На верхний край грохота подается исходный материал и под действием силы тяжести скатывается по каткам вниз, при этом мелкий материал проваливается сквозь промежутки между валками. Такие грохоты применяют для грохочения сравнительно легких и хрупких материалов, например для крупного грохочения углей. Эффективность их грохочения несколько выше, чем у колосниковых, и составляет около 75 %.
Дуговые грохоты широко используют для мокрого грохочения тонких продуктов. Рабочая поверхность - изогнутая в виде дуги плоскость, которая набрана из поперечной колосниковой решетки. На верхний край дуги подается исходный материал в виде пульпы. Мелкие зерна вместе с водой разгружаются через сито в разгрузочную коробку, а крупные - в конце дугового сита. Поскольку пульпа движется по дуге, возникающая центробежная сила повышает эффективность грохочения, она может достигать 90 %. Дуговые грохоты применяют при ширине щелей от 0,25 до 3 мм.
Барабанные грохоты в зависимости от формы барабана могут быть цилиндрическими или коническими. Боковая поверхность барабана, образованная перфорированными стальными листами или сеткой, служит просеивающей поверхностью грохота. Ось цилиндрического барабана наклонена к горизонту под углом 4-7°, а ось конического барабана горизонтальна. Исходный материал загружают внутрь барабана на верхнем конце, и вследствие вращения и наклона он продвигается вдоль оси барабана. Мелкий материал проваливается через отверстия, крупный - удаляется из барабана на нижнем конце (рис.1.3). Диаметр барабана колеблется от 500 до 3000 мм; длина - от 2000 до 9000 мм.
Вибрационные грохоты являются самыми распространенными в горно-добывающей промышленности. Главной их особенностью является наличие вибрационного устройства, которое сообщает грохоту гармонические колебания (вибрации), необхо-
![]() |
![]() |
1 - вибровозбудитель; 2 - короб; 3 - сито; 4 - опорные пружины
димые для процесса грохочения. По конструкции вибрационные устройства разнообразны, но по характеру колебаний все вибрационные грохоты можно разбить на две большие группы: 1) с прямолинейными качаниями короба; 2) с круговыми качаниями. В первой группе наибольшее распространение получили самоба- лансные грохоты.
Самобалансные грохоты (рис.1.4) имеют приводной механизм в виде двухвального вибровозбудителя. Прямолинейные гармонические колебания короба грохота генерируются силой инерции двух противоположно вращающихся дебалансовых грузов. Короб с ситом, закрепленный на вертикальных упругих опорах, под действием вибровозбудителя совершает прямолинейные колебания по стрелке А под углом в к плоскости сита.
Ко второй группе относятся, например, инерционные грохоты, которые изготавливаются в подвесном или в опорном исполнении. Предпочтение отдается опорным грохотам как более надежным в работе. Вибрационные грохоты характеризуются высокой производительностью и значительной эффективностью (7585 %) грохочения, поэтому являются самыми распространенными.
I.3.2. КЛАССИФИКАЦИЯ
Классификация - это процесс разделения материала по крупности в жидкости (или газе), основанный на различии скоростей падения в полях гравитационной силы (гравитационная классификация) или центробежной силы (центробежная классификация) зерен различной крупности. В соответствии с используемой средой (вода или воздух) классификация может быть гидравлической или пневматической, наибольшее распространение получила гидравлическая классификация.
Скорость осаждения зерна в жидкости определяется плотностью, размером и формой зерна, а также плотностью и вязкостью жидкости. Например, скорость осаждения зерна в воде можно определить по следующим формулам: мелкого зерна (d < 0,01 см)
v = 5425d 2(5 — 1);
зерна среднего размера (d = 0,01^0,27 см)
v = 120d(5 — 1)2/3;
крупного зерна (d > 0,27 см )
v = 55 Vd (5-1) .
В этих формулах: v - скорость осаждения зерна, см/с; d - размер зерна, см; 5 - плотность зерна, ^м3.
Обычно при обогащении полезных ископаемых классификации подвергается продукт, содержащий частицы меньше 6 мм для руд и 13 мм для углей. Гидравлическую классификацию применяют для разделения по граничной крупности 40 мкм и более.
Исходное питание ОСНОВНЫМИ классифици
![]() |
Простейшими гидравлическими классификаторами являются автоматические конусы (рис.1.5). На обогатительных фабриках их используют в отдельных случаях во вспомогательных операциях - для отделения песков от шламов при низкой эффективности классификации или обезвоживании обесшламленного мелкозернистого материала, а также как буферные емкости. Разгрузка слива происходит самотеком через сливной порог, а песков - непрерывно через песковые насадки или с применением разного рода затворов периодического действия.
![]() |
У спирального классификатора (рис.1.6) исходный материал подается в нижнюю треть ванны. Мелкие частицы, у которых скорость падения низкая, удаляются со сливом через порог. Крупные частицы, чья скорость падения выше, оседают на дно и спиралью транспортируются в верхнюю часть ванны, где разгру-
жаются через специальное отверстие. На дне аппарата образуется постель из осевших частиц, которая предохраняет ванну от износа.
![]() |
Гидроциклоны (рис.1.7) - аппараты для классификации тон- коизмельченных материалов по гидравлической крупности в центробежном поле, создаваемом в результате вращения пульпы. Их применяют также для обогащения мелко- и среднезернистых руд в тяжелых суспензиях. Исходная пульпа подается в гидроциклон под давлением через питающую насадку, установленную тангенциально непосредственно под крышкой аппарата. Пески разгружаются через песковую насадку, а слив - через сливной патрубок, расположенный в центре крышки и соединенный со сливной трубой непосредственно или через сливную коробку. Движущихся деталей в гидроциклоне нет. Главной действующей в гидроциклоне силой является центробежная сила инерции, возникающая при вращении пульпы благодаря тангенциальной подаче питания. Под действием центробежной силы более крупные и более тяжелые частицы твердого отбрасываются к стенке корпуса гидроциклона, опускаются под действием силы тяжести вниз и разгружаются через песковую насадку. Более тонкие и легкие частицы вытесняются к центру гидроциклона и выносятся в слив.
Гидроциклоны применяют в настоящее время в качестве классифицирующих аппаратов на подавляющем большинстве обогатительных фабрик.
1.3.3. ДРОБЛЕНИЕ
Дробление и измельчение - процессы уменьшения размеров кусков (зерен) полезных ископаемых путем разрушения их действием внешних сил. Принципиально процессы дробления и измельчения не различаются между собой. Условно считают, что при дроблении получают продукты преимущественно крупнее 5 мм, а при измельчении - мельче 5 мм. Для дробления применяют дробилки, а для измельчения - мельницы.
Крупность зерен, до которой надо дробить или измельчать исходный материал перед обогащением, определяется размером вкрапленности полезных минералов и процессом, принятым для обогащения данного ископаемого. Необходимая крупность устанавливается опытным путем при исследованиях обогатимости каждого полезного ископаемого.
Способы дробления различаются видом воздействия разрушающей силы на куски дробимого материала. Известны четыре основных способа дробления: раздавливание, раскалывание, истирание и удар.
Процесс дробления характеризуют степенью дробления i, которая показывает, во сколько раз уменьшается размер куска при дроблении:
i = D / d,
где D и d - максимальный размер куска соответственно до и после дробления.
На обогатительных фабриках дробление и измельчение полезных ископаемых перед обогащением производят с высокой степенью сокращения крупности. Например, перед флотационным обогащением полезное ископаемое иногда измельчают до крупности менее 0,1 мм. Если при этом руда поступает из карьеров, то размер максимальных кусков в исходном материале может доходить до 1500 мм. Тогда степень измельчения i = 1500/0,1 = 15000.
Получение таких высоких степеней дробления в одной дробильной машине практически невозможно. Вследствие конструктивных особенностей машины для дробления и измельчения эффективно работают только при ограниченных степенях измель
чения, поэтому рациональнее дробить и измельчать материал от исходной крупности до требуемого размера в нескольких последовательно работающих дробильных и измельчающих машинах. В каждой из таких машин будет осуществлена лишь часть общего процесса дробления или измельчения, называемая стадией дробления или измельчения.
В зависимости от крупности дробимого материала и дробленого продукта стадии дробления имеют особые названия: первая стадия - крупное дробление (до 300 мм); вторая стадия - среднее дробление (до 100 мм); третья стадия - мелкое дробление (до 10 мм).
Степень дробления, достигаемая в каждой отдельной стадии, называется частной, а во всех стадиях - общей,
/0 _ i 1 ?2 ■■■ in
Основными типами применяемых дробящих аппаратов являются щековые, конусные, валковые и молотковые (роторные) дробилки.
Щековые дробилки выпускают двух типов - с простым и сложным качанием щеки. В щековой дробилке с простым качанием щеки материал раздавливается между двумя щеками, из которых одна неподвижная, а другая подвижная - качающаяся. Подвижная щека шарнирно подвешена на неподвижной оси и попеременно то приближается к неподвижной щеке, то удаляется от нее. При сближении щек находящиеся между ними куски дробимого материала раздавливаются. Качательные движения щеки создаются вращающимся эксцентриковым валом через передаточный механизм.
Исходный материал поступает в пространство между щеками сверху. Дробленый продукт разгружается снизу при отходе подвижной щеки (рис.1.8). В дро- Рис. I.8. Щековая дробилка билках со сложным качанием с простым движением щеки
щеки подвижная щека висит эксцентрично на вращающемся валу, вращение которого сообщает щеке колебательные движения, достаточные для дробления материала. Щековые дробилки находят применение на обогатительных фабриках, в основном, для крупного и среднего дробления.
![]() |
Валковые дробилки используют принцип раздавливания и раскалывания материала, находящегося в рабочем пространстве между движущимися гладкими, рифлеными или зубчатыми цилиндрическими поверхностями.
В зависимости от конструктивных особенностей и назначения применяют валковые дробилки следующих типов: одновалковые - для дробления агломерата и угля; двухвалковые (рис.1.10, а) - для дробления горных пород и руд; двухвалковые с зубчатыми валками - для дробления угля и мягких пород; четы-
б |
![]() |
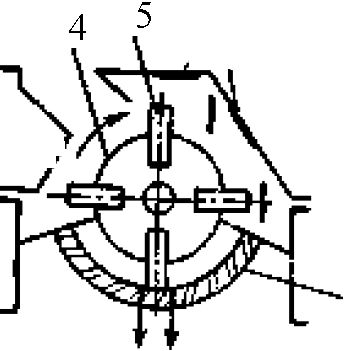
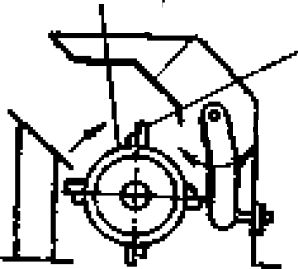
Рис.1.10. Дробилки: а - двухвалковая; б - молотковая; в - роторная
1 - валок; 2 - ось; 3 - пружина; 4 - ротор; 5 - молоток; 6 - колосниковая
решетка; 7 - било
рехвалковые с гладкими валками для дробления кокса и известняка (на аглофабриках). Наибольшее распространение получили двухвалковые дробилки. В зубчатых дробилках каждый валок состоит из вала и жестко засаженного на него многогранника, к которому болтами крепятся сменные зубчатые сегменты (бандажи) в виде отливок из марганцовистой стали.
Молотковые и роторные дробилки с вращающимся ударным ротором бывают в основном двух типов (рис.1.10, б, в): молотковые с шарнирно подвешенными молотками и роторные с жестко закрепленными лопатками (билами).
Молотковые и роторные дробилки применяют для крупного, среднего и мелкого дробления хрупких, мягких и средней твердости полезных ископаемых. Достоинства этих дробилок заключаются в простоте их конструкции, компактности, надежности и относительно высокой степени дробления (10-20 и более).
На обогатительных фабриках дробилки, как правило, работают в паре с грохотами. Если грохот ставится перед дробилкой, то такое грохочение называют предварительным. В этом случае из руды перед дробилкой отсевают мелкий класс и снижают нагрузку на дробилку. Если грохот стоит после дробилки, то такое грохочение называется поверочным. При этом из дробленного продукта отсевают готовый класс крупности, а крупную фракцию (надрешетный продукт) возвращают в дробилку. Иногда поверочное и предварительное грохочения совмещают на одном грохоте - смешанное грохочение.
I.3.4. ИЗМЕЛЬЧЕНИЕ
Измельчение полезных ископаемых производят в мельницах. Их подразделяют на механические (с мелющими телами) и аэродинамические (без мелющих тел). В качестве мелющих тел применяют металлические стержни и шары, рудную «галю» и крупные куски самой руды (самоизмельчение).
На обогатительных фабриках применяют, в основном, цилиндрические барабанные шаровые или стержневые мельницы и мельницы самоизмельчения.
Барабанная мельница (рис.1.11) представляет собой пустотелый барабан, закрытый торцовыми крышками и на 40-45 %
![]() |
объема заполненный измельчающими телами. Загрузочная и разгрузочная полые цапфы барабана помещены в подшипники, которые опираются на железобетонные опоры. При вращении подаваемая в барабан руда вместе с измельчающими телами поднимается на некоторую высоту, а затем скатывается или падает вниз, подвергаясь измельчению за счет сил ударов и трения в слоях измельчающей среды. Различают каскадный, смешанный и водопадный режимы движения измельчающей среды. Какой будет режим - зависит от скорости вращения барабана. При малом числе оборотов барабана наблюдается каскадный режим, при увеличении скорости вращения наступает водопадный и, наконец, при еще большей скорости (критическая) измельчение прекращается. Объясняется это тем, что при скорости вращения барабана, равной или большей критической, мелющие тела (шары или стержни) центробежной силой прижимаются к внутренней поверхности барабана (центрифугируют). Критическая скорость вращения мельницы в оборотах в минуту
МКр = 42,3 /4D, где D - диаметр барабана, м.
Обычно на практике скорость вращения мельницы составляет около 80 % от критической.
Чаще всего стержневые мельницы применяют или при грубом измельчении мелковкрапленных руд для их последующего обогащения, или в первой стадии (в открытом или замкнутом цикле) при двух- и многостадиальном измельчении для подготовки материала к последующему измельчению. Расход стали (шаров или стержней) при измельчении руд составляет около 1 кг/т руды.
Снизить расход стали позволяет самоизмельчение, которое бывает двух видов: рудное и рудно-галечное. В первом случае измельчающей средой являются куски самой неклассифицированной руды, во втором - руда узкого класса крупности или какой-либо другой твердый материал («галя»). Поскольку измельчающая способность кусков руды значительно ниже, чем стальных шаров (стержней), мельницы самоизмельчения имеют диаметр намного больше (до 11 м), чем шаровые (стержневые). При этом, падая с большей высоты, руда лучше сама себя измельчает. Самоизмельчение осуществляется или в воде в мельницах «Каскад», или на воздухе в мельницах «Аэрофол». Самоизмельчение имеет определенные преимущества: при рудном самоизмельчении можно измельчить руду крупностью 350-0 мм; уменьшается пе- реизмельчение руды, снижается расход стали и в некоторых случаях улучшаются технологические показатели последующего обогащения.
I.4. ОСНОВНЫЕ ПРОЦЕССЫ ОБОГАЩЕНИЯ
Задача основных процессов обогащения - разделить полезный минерал и пустую породу. В их основе лежат различия в физических и физико-химических свойствах разделяемых минералов.
1.4.1. ГРАВИТАЦИОННЫЕ МЕТОДЫ ОБОГАЩЕНИЯ
Гравитационными методами обогащения называют такие, в которых разделение минеральных частиц, отличающихся плотностью, размером и формой, обусловлено различием в характере и скорости их движения в текучих средах под действием силы тяжести и сил сопротивления. Гравитационные методы занимают ведущее место среди других методов обогащения. Они могут быть собственно гравитационными (разделение в поле силы тяжести - обычно для относительно крупных частиц) и центробежными (разделение в центробежном поле - для мелких частиц). Если разделение происходит в воздушной среде, то процессы называют пневматическими; в остальных случаях - гидравлическими. Наибольшее распространение в обогащении получили собственно гравитационные процессы, осуществляемые в воде.
По типу используемых аппаратов гравитационные процессы можно разделить на отсадку, обогащение в тяжелых средах и обогащение на наклонной плоскости в потоке воды: концентрацию на столах, обогащение на шлюзах, в желобах, винтовых сепараторах. Применяют также относительно новые гравитацион-
ные процессы - обогащение в вибрационных концентраторах, противоточных сепараторах, обогатительных циклонах с водной средой и др.
![]() |
1 и 2 - соответственно тяжелая и легкая фракции; 3 - исходное питание; 4 - подрешетная вода |
Этим методом можно обогащать материалы крупностью от 0,1 до 400 мм. Отсадка применяется при обогащении углей, сланцев, окисленных железных, марганцевых, хромитовых, кас- ситеритовых, вольфрамитовых и других руд, а также золотосодержащих пород. В процессе отсадки (рис.1.12) материал, помещенный на решете отсадочной машины, периодически разрыхляется и уплотняется. При этом зерна обогащаемого материала под влиянием сил, действующих в пульсирующем потоке, перераспределяются таким образом, что в нижней части постели сосредотачиваются частицы максимальной плотности, а в верхней - минимальной (размеры и форма частиц также оказывают влияние на процесс расслоения). Часто на решето укладывают искусственную постель из материала, плотность которого больше плотности легкого минерала, но меньше плотности тяжелого. Крупность постели в 5-6 раз больше крупности максимального куска исходной руды. В настоящее время известно около 100 конструкций отсадочных машин. Наиболее распространена гидравлическая отсадка. А среди машин чаще всего применяют беспоршневые.
Обогащение полезных ископаемых в тяжелых средах основано на разделении минеральной смеси по плотности. Процесс происходит в соответствии с законом Архимеда в средах с плот-
Рис. 1.13. Тяжелосредный колесный сепаратор |
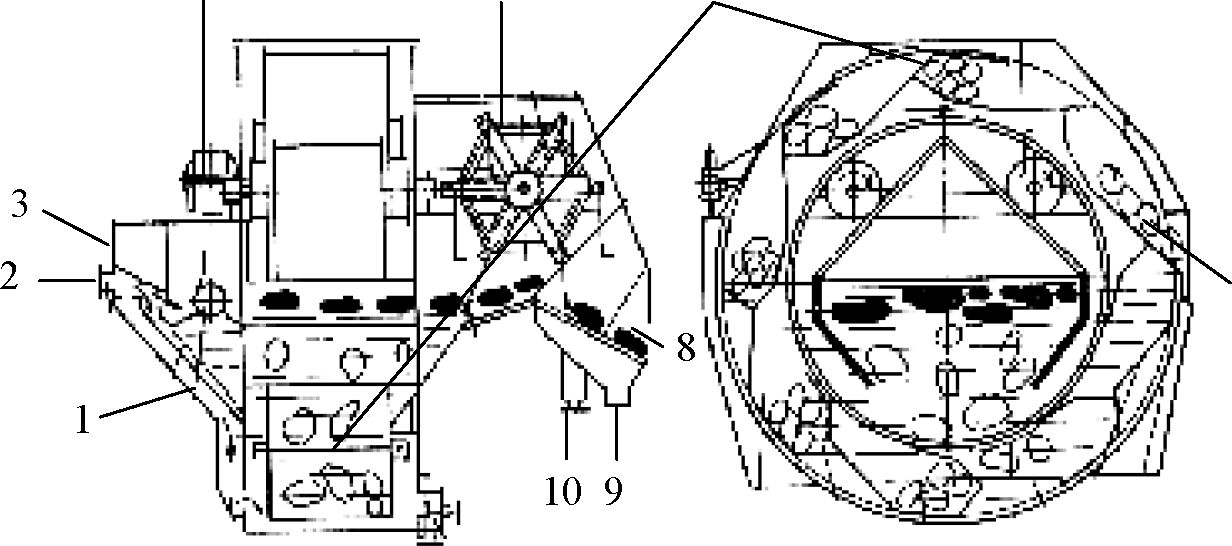
1 - корпус с ванной; 2 - подача суспензии; 3 - исходный материал; 4 - привод элеваторного
колеса; 5 - гребковое устройство; 6 - элеваторное колесо; 7 - легкий продукт; 8 тяжелый про-
дукт; 9,10 - сброс суспензии
ностью, промежуточной между плотностью удельно-легкого и удельн
<== предыдущая лекция | | | следующая лекция ==> |
Миелиновые нервные волокна | | | Возникновение и развитие налоговых отношений в Древнерусском государстве Киевская Русь. Период феодальной раздробленности Руси. |
Дата добавления: 2021-12-14; просмотров: 666;