Реечное станочное зацепление.
Способы изготовления зубчатых колес. В настоящее время зубчатые колеса изготавливают способами копирования и огибания.
По первому способу изготовляют зубчатые колеса в основном только с равноделенным шагом. При этом большинство их выполняется с заведомой погрешностью. Второй способ - способ огибания такими существенными недостатками не обладает: этим способом можно изготовить самые разнообразные зубчатые колеса и притом теоретически точно. Поэтому способ огибания нашел распространение и представляет особый интерес.
При способе огибания заготовке, из которой изготовляют зубчатое колесо, и режущему инструменту, имеющему зубчатую форму (червячная фреза, гребенка, долбяк), сообщают на станке такие движения относительно друг друга, которые воспроизводят процесс зацепления. Это зацепление называют станочным.
Помимо движений, воспроизводящих процесс зацепления инструменту сообщается еще технологическое движение резания. При этом режущие кромки инструмента описывают поверхность, называемую производящей. Укажем, что производящая поверхность и изготавливаемая боковая поверхность зуба являются взаимоогибаемыми, откуда сам способ и получил свое наименование.
При расчете геометрических параметров элементов высшей кинематической пары учитывают технологические возможности изготовления деталей на формообразующих станках (металлорежущих, прокатных станах, прессах и т. д.). Геометрия соответствующего формообразующего инструмента тесным образом связана с производящими поверхностями. Для инструментов, осуществляющих процесс формообразования путем срезания стружки, такой производящей поверхностью является воображаемая поверхность, содержащая режущие кромки инструмента или образуемая при их главном движении, необходимом для резания. Если режущие кромки - прямые, а главное движение - прямолинейное, то производящей поверхностью является плоскость. Если режущие кромки криволинейные, а главное движение - прямолинейное, то производящей поверхностью является цилиндрическая поверхность (например, эвольвентная поверхность для долбяков).
Зацепление проектируемой поверхности зубьев с производящей поверхностью по аналогии с зацеплением нарезаемого колеса с производящей поверхностью режущего инструмента называют станочным зацеплением. Этот термин был предложен В. А. Гавриленко, крупным ученым, обобщившим и развившим основные положения теории зацепления эвольвентных передач. Сущность станочного зацепления заключается в том, что производящая поверхность (поверхность режущих кромок инструмента) и проектируемая поверхность зуба («нарезаемого» колеса) имеют такое же относительное движение, какое имели бы зубчатые колеса при зацеплении друг с другом при взаимодействии аксоидных поверхностей.
При нарезании цилиндрических зубчатых колес оси производящего колеса (т. е. воображаемого зубчатого колеса, у которого боковые поверхности являются производящими поверхностями) и проектируемого («нарезаемого») колеса параллельны между собой и аксоидами являются цилиндры. Если производящее колесо имеет конечное число зубьев, то режущими инструментами являются долбяк (рис. 14.5 е), абразивный хон (рис, 14.5 ж), которыми можно обрабатывать боковые поверхности зубьев колес с различными числами зубьев (рис, 14.5, з). При бесконечно большом радиусе аксоида производящего колеса инструмент должен иметь бесконечно большое число зубьев, т. е. превратиться в рейку. В этом случае инструментом обычно являются червячная фреза (рис. 14.5, б) или абразивный червячный круг (рис. 14.5, г), у которых реечный производящий контур (рис. 14.5, д) расположен на винтовой поверхности. Частным случаем является инструмент, называемый зуборезной гребенкой (рис. 14.5, а) или пара тарельчатых шлифовальных кругов (рис. 14.5, в). Главным движением резания у долбяка, гребенки и абразивного хона является поступательное движение, а у червячной фрезы и
|
![]() |
шлифовальных кругов - вращательное движение.
В процессе движения огибания (обкатки) основной шаг инструмента по профильной нормали соответствует основному шагу проектируемого («нарезаемого») колеса. Процесс перехода от формообразования одного зуба к другому в процессе обкатки осуществляется автоматически при непрерывном относительном движении (рис. 14.5, д. з).
Если производящую поверхность рассечь плоскостью, перпендикулярной оси нарезаемого колеса, то в сечении получим исходный производящий контур (ИПК). Станочное зацепление есть зацепление ИПК с профилем зуба нарезаемого колеса.
Рассмотрим реечное станочное зацепление, т. е. такое, когда ИПК имеет очертания зубчатой рейки. Эвольвентные кромки этого ИПК прямолинейны. Режущий инструмент (червячная фреза или гребенка), образующий своим главным движением эвольвентный реечный ИПК, обладает очень ценным свойством: его можно изготовить, сравнительно дешево и точно. Геометрия зубьев нарезаемого колеса определяется параметрами ИПК реечного инструмента и его расположением по отношению к колесу.
Исходный производящий контур эвольвентного реечного инструмента. Форма я размеры ИПК стандартизованы. Эвольвентные части профиля зубьев ИПК (рис. 14.6, а) прямолинейны и наклонены к оси зуба под углом . Переходы от прямолинейной части зуба к основанию впадины и к вершине осуществлены по дуге радиусом
t. Точки сопряжения отмечены на ИПК буквами А, С, D, Е. Прямолинейная часть CD является эвольвентной, а скругления АС и DE - неэвольвентной частью контура. Прямая, разделяющая зуб по высоте на две равные части, называется делительной. На ИПК отмечаются еще четыре линии, параллельные делительной прямой и проходящие по основаниям впадин зубьев, по их вершинам и через точки сопряжения С и О. Расстояния между этими прямыми выражают размеры зуба исходного производящего контура по высоте и измеряются соответственно величинами ha = ha*m и C = c*m, где ha* - коэффициент высоты зуба, с* - коэффициент радиального зазора. Согласно стандарту: ha* = 1,0 ; с* = 0,25. Прямые, проходящие через точки С и D, называются прямыми граничных точек.
|
![]() |
Размерами вдоль делительной прямой являются шаг, толщина зуба н ширина впадины. Шаг р исходного производящего контура, измеренный по любой прямой, параллельной делительной, есть величина постоянная, равная



(14.7)
Таким образом. ИПК реечного инструмента характеризуется четырьмя стандартными параметрами: m, , ha*, c*.
Реечное станочное зацепление и коэффициент смещения. Реечное станочное зацепление, как и всякое зацепление, имеет начальные линии. Ими являются станочно-начальная прямая рейки и станочно-начальная окружность колеса, которые катятся друг по другу без скольжения. Можно показать, что в реечном станочном зацеплении радиус rw0 станочно-начальной окружности равен радиусу делительной окружности r.
Угол реечного станочного зацепления w0 равен профильному углу а исходного производящего контура (как углы с взаимно перпендикулярными сторонами). Отметим также, что угол профиля зуба колеса в точке, находящейся на делительной окружности, равен профильному углу
исходного производящего контура.
На станке инструмент можно расположить по-разному относительно нарезаемого колеса. Поэтому в станочном зацеплении делительная прямая ИПК может располагаться различным образом по отношению к делительной окружности колеса: I) она может касаться делительной окружности - нулевая установка инструмента; 2) быть отодвинутой от нее — положительная установка; 3) пересекать ее—отрицательная установка.
Расстояние между делительной прямой и делительной окружностью называется смещением инструмента. Его выражают в виде произведения модуля m на коэффициент смещения х и ему присваивают знак. При нулевой установке смещение mх > 0, х > 0. При положительной установке mх > 0, х> 0. При отрицательной установке смещением является стрелка сегмента, которую делительная прямая отсекает от делительной окружности; в этом случае mx < 0, x < 0.
На рис. 14.6, а изображено реечное станочное зацепление при нарезании зубчатого колеса с положительным смещением и указаны все элементы производящего исходного контура, нарезаемого колеса и станочного зацепления.
Линия реечного станочного зацепления начинается в точке N и через полюс P0 уходит в бесконечность. Длина ее активной части ограничена точками В1’ и B’’, находящимися на пересечении линии станочного зацепления с прямой QQ граничных точек и окружностью вершин (рис. 14.6, а)
Профиль зуба колеса имеет эвольвентную и неэвольвентную части. Переход эвольвснтного профиля в неэпольвентиый находится на окружности граничных точек колеса, радиус которой rl = OB1'.
Расстояние между окружностью вершин зубьев колеса и прямой впадин ИПК представляет собой станочный зазор С0. Величина его складывается из двух частей: с*m, ym, где
у — коэффициент уравнительного смещения.
Размеры изготовляемого зубчатого колеса с внешними зубьями. Диаметр вершин прямозубого колеса (рис. 14.6, а):
(14.8)
Высота зуба из того же рисунка:
(14.9)
Если x = 0 (смещения инструмента нет) и у = 0, то da = m(z + 2ha*), h = m(2ha* + с*), и при стандартных значениях ha* = 1,0 и с* = 0,25 получим da = m(z+2) и h = 2,25m.
Стачочно-начальная прямая перекатывается по станочно-начальной окружности (она же делительная) без скольжения. Поэтому толщина зуба s по делительной окружности нарезаемого колеса равна ширине ММ впадины по станочно-начальной прямой ИПК (рис. 14.6, б).
Отрезок ММскладывается из ширины впадины ИПК по делительной прямой e0 = m/2 и двух катетов, каждый из которых равен xm tg
, поэтому:
s = m/2 + 2 xm tg
(14.10)
Если инструмент установлен относительно колеса без смещения (xm = 0), то s = m/2; значит, толщина зуба s по делительной окружности колеса равна ширине впадины е, так как s + е =
m. В этом случае получается колесо с равноделенным шагом s = e, Если xm > 0, то s >
m/2 и, следовательно, s > e. Если xm < 0, то s <
m/2, и поэтому s < e.
При нарезании косозубых колес применяется тот же инструмент 1, что для прямозубых, но устанавливается он наклонно под углом по отношению к торцовой плоскости t - t колеса (заготовки) (рис. 14.6, в). На этом рисунке показана развертка 2 делительного цилиндра косозубого колеса, в результате чего винтовые линии косого зуба преобразовались в прямые линии. В торцовой плоскости t - t косозубого колеса вследствие наклона инструмента шаг увеличивается и становится равным p/cos
, а следовательно, и модуль в торцовой плоскости будет нестандартным, равным m/cos
. Поэтому при расчете линейных размеров косозубого колеса по формулам, в которые входит стандартный модуль, вместо m следует подставлять m/cos
, например делительный диаметр косозубого колеса d = zm/ cos
.
|
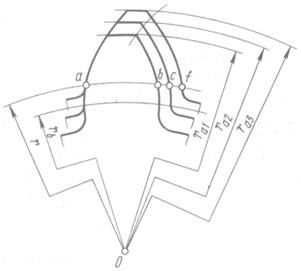




Угол профиля исходного производящего контура при нарезании косозубого колеса увеличивается по сравнению со стандартной величиной = 20°, поскольку размеры по высоте не изменяются, а шаг в торцовом сечении увеличивается. Расчетный угол профиля
t исходного производящего контура при нарезании косозубых колес определяют по формуле:
На рис. 14.7 сравниваются профили зубьев трех колес, имеющих одинаковые числа зубьев, нарезанные одним и тем же инструментом, но с различными смещениями: x1 < x2 < x3. Колеса имеют одинаковые радиусы делительных и основных окружностей; следовательно, профили зубьев всех трех колес очерчены по одной и той же эвольвенте. Но толщины зубьев s1, (дуга ab), s2 (дуга ас), s3 (дуга af) и радиусы окружностей вершин ra1, ra2, ra3, у колес будут разные. По мере увеличения х толщина зуба у основания увеличивается, а у вершины уменьшается, т. е. коэффициент смещения существенно влияет на форму зуба. Следовательно, назначая при проектировании тот или иной коэффициент смещения, можно влиять на форму зубьев колёс и на качество зубчатой передачи, наделяя её желательными свойствами.
Контрольные вопросы к лекции N14
1. Что называют зубчатым колесом?
2. Расскажите об основных элементах зубчатого колеса.
3. Запишите формулы окружного и углового шагов эвольвентного зубчатого колеса.
4. Какие методы изготовления зубчатых колёс Вы знаете?
5. В чём заключается сущность изготовления эвольвентных колёс методом огибания?
6. Дайте определение станочного зацепления.
7. Выведите формулы для определения основных размеров зубчатого колеса ( ) используя схему станочного зацепления.
Дата добавления: 2017-02-13; просмотров: 5562;