ТЕХНОЛОГИЯ АЗОТНОЙ КИСЛОТЫ
Чистая азотная кислота HNO3 при нормальной температуре — бесцветная жидкость, замерзающая при —41°С, кипящая при 86°С. Максимальную температуру кипения 121,9°С имеет раствор, содержащий 68,4% HNO3, представляющий собой азеотропную смесь. Азотная кислота очень сильный окислитель. Многие органические вещества (в том числе животные и растительные ткани) при действии азотной кислоты разрушаются, а некоторые способны воспламеняться. Концентрированная кислота пассивирует такие металлы, как железо, на этом и основано использование стали как конструкционного материала в производстве азотной кислоты. Отечественная промышленность выпускает азотную кислоту двух видов: разбавленную с содержанием 50—60% HNO3 и концентрированную, содержащую 96—98% HNO3. Разбавленная кислота используется в основном для производства азотосодержащих минеральных удобрений. Крепкая азотная кислота потребляется для производства взрывчатых веществ, красителей, пластических масс, нитролаков, кинопленки и других важнейших продуктов. Азотную кислоту производят из аммиака.
ФИЗИКО-ХИМИЧЕСКИЕ ОСНОВЫ ПРОЦЕССА
Производство разбавленной азотной кислоты из аммиака складывается из следующих стадий:
1) контактное окисление аммиака до оксида азота (II):
4NH3 + 5О2 ® 4NO + 6Н2О, ΔН = – 907 кДж (а)
2) окисление NО до NO2:
2NO+O2 D 2NO2, ΔН = –112 кДж (б)
3) абсорбция диоксида азота водой с образованием разбавленной азотной кислоты:
3NO2+ H2O D 2HNO3 + NO, ΔН = –135 кДж (в)
Выделяющийся при этом оксид азота (II) окисляется до диоксида
И снова абсорбируется.
Контактное окисление аммиака.При окислении аммиака кроме
основной реакции (а) могут протекать и другие процессы, которые приводят к непроизводительному расходованию аммиака:
4NH3 + 4O2 ® 2N2O + 6H2O ΔН = –1105 кДж (г)
4NH3 + 3O2 ® 2N2 + 6H2O ΔН = –1270 кДж (д)
4NH3 + 6NO ® 5N2 + 6H2O, ΔН = –1810 кДж (е)
Равновесие реакций окисления аммиака (а), (г), (д) в условиях производства полностью смещено вправо. Следовательно, превращение аммиака в конечные продукты при 750 °С может достигать почти 100%. Общая скорость процесса определяется соотношением скоростей реакций (а) — (е). В отсутствие катализатора наиболее быстрой является реакция окисления до элементного азота. Поэтому, в азотнокислотном производстве процесс окисления производят на катализаторах, обладающих избирательностью действия, т. е. на таких катализаторах, которые резко ускоряют реакцию получения NО по сравнению с прочими реакциями окисления аммиака.
В азотнокислотной промышленности в основном применяют платиновые катализаторы. Процесс окисления аммиака на платиновом катализаторе относится к числу наиболее быстрых каталитических реакций, известных в настоящее время. В производственных условиях практически полное окисление аммиака достигается за 10–4 с.
Скорость каталитического окисления аммиака.Скорость процесса окисления зависит от технологического режима процесса и конструкции контактного аппарата. На высокоактивных платиноидных катализаторах процесс протекает в диффузионной области. На менее активных (оксидных) катализаторах при пониженных температурах окисление аммиака определяется скоростью каталитических актов, т. е. протекает в кинетической области.
Повышение температуры способствует увеличению не только скорости химической реакции, но и коэффициента диффузии аммиака в смеси. Поэтому повышение температуры — эффективное средство увеличения скорости процесса окисления, протекающего как в кинетической, так и в диффузионной области. Однако повышение температуры катализа выше ~850°С снижает выход NО и повышает выход элементного азота (рис. 1) за счет реакции (д), а также термической диссоциации NH3 и других вредных побочных реакций.
|
|
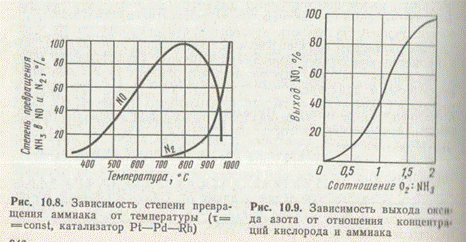
Повышение давления ускоряет процесс окисления NH3, так как увеличиваются концентрации реагирующих компонентов в реакционном объеме, уменьшается объем газовой смеси.
Однако при повышенном давлении существенно возрастает унос мельчайших частичек платины с газами, что удорожает товарную кислоту, поскольку платина имеет высокую стоимость, а процесс улавливания микроскопических частичек платины из нитрозных газов после контактного аппарата весьма сложен и не обеспечивает полного устранения потерь платины. При повышении давления необходимо увеличивать толщину стенок аппаратуры, в результате чего возрастает ее стоимость. Поэтому применяют избыточное давление 0,2—1 МПа.
Состав газовой смеси влияет на температурный режим и общую скорость процесса, особенно если лимитирует не диффузия, а химическая реакция между NH3 и О2. По уравнению реакции (а) на 1 моль NH3 расходуется 1,25 моль О2, однако при таком соотношении компонентов выход оксида азота (II) не превышает 65%, т. е. очень мал (рис. 2). Для увеличения степени окисления аммиака на практике применяют соотношение O2:NH3=1,8—2,0, что соответствует содержанию аммиака в аммиачновоздушной смеси 9,5—10,5 (об. доли в %). Следует учитывать, что при обычной температуре смесь аммиака с воздухом взрывоопасна в интервале 16—27% NH3. При повышении температуры границы взрывоопасности расширяются.
Промышленные катализаторы процесса окисления аммиака.
Эти катализаторы представляют собой сплав платины с 4% Pd и 3% Rh. Платиноидные катализаторы выполняют в виде сеток из тонкой проволоки диаметром 0,06—0,09 мм, имеющих 1024 отверстия в 1 см2. Сетки эти для создания определенного времени контактирования скрепляются в виде пакета, устанавливаемого в контактном аппарате.
На 1 м2 активной поверхности контактной сетки под атмосферным давлением можно окислить до 600 кг, а при давлении 0,8 МПа — до 3000 кг аммиака в сутки. Однако при работе под давлением 0,8 МПа и более платиновый катализатор разрушается быстрее.
Разрушению катализатора способствуют и многие контактные яды (соединения серы, фосфин и др.), которые помимо отравления катализатора снижают его механическую прочность. Примеси (пыль, ржавчина, смазочное масло и т. п.), содержащиеся в газе, также снижают активность и прочность катализатора. Для восстановления активности катализатора его промывают разбавленным раствором соляной кислоты. Все это приводит к тому, что в процессе окисления аммиака катализатор становится рыхлым и мельчайшие частицы его уносятся с потоком газа. Если под атмосферным давлением унос платины на 1 т азотной кислоты составляет 0,04—0,06 г, то при повышенном он достигает уже 0,15—0,20. Часть Pt улавливается и регенерируется, но и при этом расходы платины составляют значительную часть себестоимости азотной кислоты.
С целью экономии платины применяют двухстадийное контактирование, при котором аммиак частично окисляется на платиноидных сетках, а затем доокисляется в слое неплатинового зернистого катализатора. В качестве неплатиновых катализаторов применяют различные композиции оксидов или солей, в том числе оксиды железа или хрома, соли кобальта. Удельная производительность платинового катализатора велика благодаря высокой скорости реакции окисления.
Активность катализаторов может сильно понижаться вследствие отравления некоторыми примесями, имеющимися в газовой смеси, или же в результате экранирующего действия механических взвесей. К наиболее сильным контактным ядам процесса окисления аммиака принадлежат соединения серы и фосфора.
В промышленности применяется несколько типов контактных аппаратов для окисления аммиака. Однако все они имеют приблизительно одинаковый принцип действия.
При повышенном давлении устанавливают до 18 сеток. При двухстадийном контактировании (рис. 3) число платиноидных сеток может быть снижено до 1—3 (при повышенном давлении).
Окисление оксида азота (II) до диоксида. Нитрозные газы, полученные при окислении аммиака, содержат NО и другие оксиды азота, кислород, азот и пары воды. Для получения азотной кислоты оксид азота (II) необходимо окислить до диоксида.
Процесс окисления NО кислородом воздуха описывают следующим суммарным (балансовым) уравнением:
2NO+ О2 D 2NO2, ΔН = –112 кДж (ж)
В соответствии с принципом Ле Шателье равновесие этого процесса сдвигается вправо при повышении давления и снижении температуры. Практически образование диоксида азота начинается при температуре ниже 700°С, а при температуре ниже 100°С равновесие почти полностью сдвинуто вправо.
Константа скорости процесса увеличивается с понижением температуры, что иногда рассматривают как нарушение закона Аррениуса. В действительности это явление можно объяснить тем, что процесс по формуле (ж) протекает в две стадии. Сначала происходит быстрая обратимая экзотермическая реакция димеризации оксида азота
2NO D N2O2 (з)
а затем окисление димера по экзотермической практически необратимой (при t<100oC) реакции
N2O2 + О2 ® 2NO2 (и)
При повышении температуры равновесие реакции (з) смещается влево, концентрация димера N2O2 сильно снижается. Соответственно снижается и скорость реакции (и).
В результате уменьшается и общая скорость процесса. Поэтому для увеличения скорости превращения NO в NO2 реакционную смесь энергично охлаждают. Повышение давления способствует сдвигу равновесия по реакции (з) в сторону димера и увеличению скорости реакции (и). Повышается и степень абсорбции диоксида азота. Поэтому в последние годы в производстве азотной кислоты перешли от установок под атмосферным давлением к повышенному давлению до 1 МПа.
При окислении оксида азота может протекать реакция ассоциации NO2 с образованием димера:
2NO2 D N2O4, ΔH = –57 кДж
Скорость этой реакции очень велика, а равновесие с повышением давления и уменьшением температуры сдвигается в правую сторону.
Таким образом, в нитрозных газах, поступающих на абсорбцию, содержатся NO2, N2O4, O2, N2O, NO, N2O2, N2, пары воды и др.
Абсорбция диоксида азота и его димера протекает по схемам:
2NO2 + H2O D HNO3 + HNO2, ΔH = –116 кДж
N2O4 + H2O D HNO3 + HNO2, ΔH = –59 кДж
Получающаяся при этом азотистая кислота неустойчива и разлагается:
3HNO2D HNO3 + 2NO + Н2О, ΔH = 76 кДж,
поэтому суммарно взаимодействие NO2 с водой можно представить уравнением:
3NO2 + H2O D 2HNO3 + NO, ΔH = –136 кДж.
В производстве необходимо получать кислоту возможно большей концентрации. При этом увеличивается давление пара оксида азота над раствором кислоты, что снижает движущую силу процесса и, следовательно, общую скорость процесса. Для сдвига равновесия в сторону образования HNO3 необходимо снижать температуру, а также повышать давление. При абсорбции оксидов азота используют принцип противотока, т. е. наиболее концентрированный газ встречается с концентрированной кислотой, а в конце абсорбции остатки NO2 поглощаются наиболее слабой кислотой.
Вследствие экзотермичности процесса абсорбции температура вытекающей продукционной кислоты обычно составляет не менее 50°С, поэтому в установках, работающих под атмосферным давлением, получается кислота, содержащая лишь около 50% HNO3. В установках, работающих под давлением 0,6—0,8 МПа, можно получить 58—60%-ную кислоту. Поднимая давление до 5 МПа, в установках прямого синтеза HNO3 из оксидов азота и кислорода получают кислоту концентрацией 98% HNO3.
ПРОИЗВОДСТВО АЗОТНОЙ КИСЛОТЫ
Для получения разбавленной азотной кислоты из аммиака в промышленности до недавнего времени использовали три системы: 1) под атмосферным давлением; 2) под повышенным давлением и 3) комбинированные, в которых окисление аммиака происходит под атмосферным давлением, а окисление оксида азота и абсорбция NO2 водой — под повышенным.
Несмотря на меньшие расходы платины, системы производства кислоты под атмосферным давлением в настоящее время не применяются из-за малой производительности, громоздкости аппаратуры и соответственно больших капитальных вложений, существенных потерь аммиака и необходимости применения дорогостоящей и не слишком эффективной щелочной очистки отходящих газов от оксидов азота.
Современные установки, работающие под повышенным давлением (от 0,2 до 1 МПа), и комбинированные разработаны по принципу энерготехнологических систем, в которых энергия отходящих газов (связанная с их высокой температурой и давлением) и теплота реакции окисления аммиака используются для сжатия воздуха и нитрозных газов, а также получения технологического пара. Этими же схемами предусмотрено возможно более полное использование низкопотенциальной теплоты.
Принципиальная технологическая схема получения разбавленной азотной кислоты под повышенным давлением приведена на рис. 4.
|
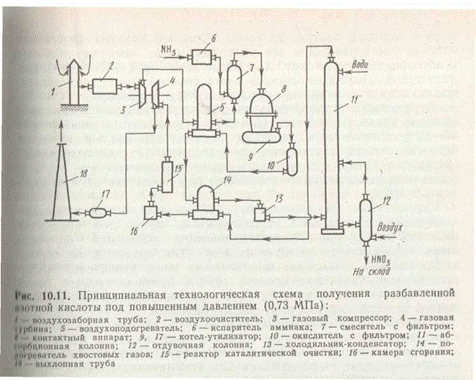
Атмосферный воздух после соответствующей очистки поступает в компрессор 3, приводимый в движение газовой турбиной 4. В компрессоре воздух сжимается до давления 0,73 МПа, нагреваясь при этом до 135°С, и поступает далее в подогреватели воздуха 5, где его температура поднимается до 250°С за счет теплоты выходящих из окислителя 10 нитрозных газов. В смесителе 7 воздух смешивается с газообразным аммиаком, который поступает сюда из испарителя аммиака 6. Образовавшаяся аммиачновоздушная смесь далее поступает в контактный аппарат 8, где при температуре около 900°С на Pt—Rh—Pd-катализаторе происходит окисление аммиака. Нитрозные газы, содержащие 9,0—9,5% NO, поступают в котел-утилизатор 9, в котором происходит охлаждение до необходимой температуры и образование пара. Далее газы поступают в окислитель 10, в котором окисляются до диоксида азота. Охлажденные в подогревателе воздуха 5, подогревателе хвостовых газов 13 и холодильнике-конденсаторе 12 до температуры около 45°С нитрозные газы поступают в абсорбционную колонну 11, орошаемую противоточно водой. Поскольку абсорбция NO2 водой экзотермична, абсорбционные тарелки снабжены змеевиковыми холодильниками, в которых циркулирует охлаждающая вода (на схеме не показано). Полученная азотная кислота самотеком поступает в отдувочную колонну 12, где с помощью горячего воздуха из готовой азотной кислоты происходит отдувка растворенных в ней нитрозных газов, которые подаются в абсорбционную колонну. Хвостовые газы, пройдя систему каталитической очистки от оксидов азота восстановлением их аммиаком до элементного азота, выбрасываются в атмосферу.
В установках такого типа степень превращения аммиака в азотную кислоту достигает 98—99%, а концентрация кислоты — 60—62%. Однако при окислении аммиака под давлением увеличиваются потери платинового катализатора. Поэтому применяют системы, в которых окисление аммиака производят при гораздо более низком давлении (~0,4 МПа), чем окисление оксида азота (до 1,2 МПа).
Современные азотнокислотные ХТС характеризуются большой мощностью отдельной технологической нитки, составляющей 380—400 тыс. т/год. Указанные системы позволяют получить лишь разбавленную азотную кислоту. Для производства взрывчатых веществ, некоторых пластических масс, красителей требуется концентрированная кислота (98%). Азотную кислоту такой концентрации можно получить либо концентрированием разбавленной азотной кислоты или прямым синтезом.
Отгонкой воды из разбавленной азотной кислоты можно получить лишь 68%-ный раствор, поскольку именно такая концентрация отвечает азеотропной смеси HNO3—Н2О. Поэтому концентрирование проводят с применением водоотнимающих средств, таких, например, как 92—94%-ная H2SO4. Концентрированная серная кислота, образующая при этом гидраты, кипит при более высокой температуре, чем 100%-ная HNO3. В качестве водоотнимающего средства может использоваться также нитрат магния.
В настоящее время значительное применение находит прямой синтез концентрированной азотной кислоты, который протекает по уравнению реакции:
2N2O4 (ж) + 2Н2О (ж) + О2 (г) D 4HNOa (ж), ΔН = — 59,5 кДж.
В действительности поглощение димера диоксида осуществляется разбавленной азотной кислотой, содержащей около 45% воды, Эта операция осуществляется в автоклаве при 90°С и 5 МПа. В автоклаве получается так называемый нитроолеум HNO3×nNO2, содержащий до 25% NO2. После отдувки диоксида азота и получается 97—98%-ная азотная кислота.
<== предыдущая лекция | | | следующая лекция ==> |
МЕТОДЫ ФИКСАЦИИ АТМОСФЕРНОГО АЗОТА | | | Производство серной кислоты |
Дата добавления: 2016-09-26; просмотров: 2998;