ГОРНО-ГЕОЛОГИЧЕСКАЯ ХАРАКТЕРИСТИКА РАЗРАБАТЫВАЕМОГО УЧАСТКА
Здесь в соответствии с заданием дать в виде таблицы 1.1 полную качественную характеристику слоев, слагающих калийный пласт, а также пород кровли и почвы пласта на разрабатываемом участке.
Таблица 1.1– Качественная характеристика слоев пласта и вмещающих
пород
Наименование слоя | Мощность слоя, м | Содержание, % | |
KCL | HO | ||
Кровля пласта | 0,38 | 3,01 | 15,34 |
Верхний сильвинитовый слой (в.с.с.) | 0,61 | 32,53 | 5,35 |
Средний галитовый слой (с.г.с.) | 0,83 | 2,76 | 7,95 |
Нижний сильвинитовый слой (н.с.с.) | 0,92 | 38,40 | 5,86 |
Почва пласта | 0,66 | 1,11 | 23,05 |
Итого по в.с.с., с.г.с., н.с.с. | 2,36 |
В таблице 1.2 привести данные, характеризующие условия залегания пласта на разрабатываемом участке.
Таблица 1.2 – Условия залегания пласта
Наименование параметра | Единица измерения | Значение параметра |
Глубина залегания | м | |
Угол падения | градус | 1-5 (северо-восток) |
Крепость по М.М. Протодьяконову | 2-3 | |
Объемный вес | ![]() | ![]() |
|
2 ТЕХНОЛОГИЧЕСКАЯ СХЕМА ОТРАБОТКИ
КАЛИЙНОГО ПЛАСТА
В этом разделе, используя горно-геологические условия разрабатываемого участка, выбрать наиболее отвечающую этим условиям технологическую схему отработки калийного пласта, которую привести в виде рисунка 2.1. На рисунке показать план и поперечный разрез панели (выемочного столба).
В таблице 2.1 дать основные горнотехнические параметры, характеризующие технологическую схему.
Таблица 2.1 – Горнотехнические параметры технологической схемы
отработки калийного пласта
Наименование параметра | Единица измерения | Значение параметра |
Система разработки | м | столбовая |
Способ подготовки | панельный | |
Способ управления кровлей | полным обрушением | |
Порядок отработки панели | обратный | |
Опережение очистных работ в смежных столбах (ℓоп) | м | свыше 500 |
Длина панели (выемочного столба) – L | м | |
Ширина межпанельного целика (а) – рисунок 2.1 | м | |
Ширина панели (В) | м | |
Длина лавы (ℓл) | м | |
Высота лавы (вынимаемая мощность) с учетом прирезки кровли пласта (0,05 м) − mл | м | 2,41 |
|
1 – панельный конвейерный штрек; 2, 3 – конвейерный и вентиляционный штреки лавы; 4 – разгружающая выработка; 5 – вспомогательная (технологическая) выработка; 6 – конвейерная сбойка; 7, 8 – монтажный и вспомогательный монтажный штреки лавы; 9 – вентиляционная перемычка; 10 – очистной комбайн; 11 – забойная крепь; 12 – забойный конвейер; а – межпанельный целик; 13 – смежная панель, отрабатываемая с опережением по отношению к проектируемой свыше 500 м
Рисунок 2.1 – Технологическая схема валовой выемки Второго
калийного пласта с обратным порядком отработки
|
Номер графиков на рисунке | Характеристика условий поддержания подготовительных выработок | |
Группа сближенных выработок, включающая панельные конвейерный и транспортный штреки, разгружающую выработку, бортовой штрек лавы | ![]() | |
Группа сближенных выработок, включающая панельные конвейерный и транспортный штреки, бортовой штрек лавы | ![]() | |
Группа сближенных выработок, включающая панельные конвейерный и транспортный штреки, бортовой штрек лавы, охраняемый тремя компенсационными щелями | ![]() | |
Группа сближенных выработок, включающая разгружающую выработку и бортовой штрек лавы | ![]() | |
Одиночная выработка без мер охраны | ![]() |
Рисунок 2.2 – Графики для выбора размеров охранных целиков (а)
при поддержании выработок на границе со смежной отрабатываемой
|
Примечания
− | при наличии внутрипанельного целика (прямой порядок отра- ботки панели, слоевая выемка Третьего пласта) в ширину панели входит и этот целик | |
− | в случае расположения в контуре охранного целика закладочных и других вспомогательных выработок, пройденных на всю длину панели параллельно бортовому штреку лавы, размер целика следует увеличивать на суммарную ширину этих выработок | |
− | при комбинированном порядке отработки выемочных столбов в панели ширину внутрипанельного целика с учетом проведенных в целике технологических выработок, а также с учетом длительного срока службы панельных выработок увеличивают на 60 % по сравнению с графиками рисунка 2.2. Это же положение распространяется на случай отработки выемочных столбов от выработок главного направления к границе панели в прямом порядке. |
Для технологической схемы, приведенной на рисунке 2.1, при глубине разработки Н = 598 м (таблица 1.2) и величине опережения очистных работ в смежных панелях(ℓоп) свыше 500 м ширина целика (а) вначале определяется по рисунку 2.2 (график 4), так как кроме целика (а) охрана вентиляционного штрека осуществляется еще и разгружающей выработкой. Ширина целика (а) – смотри рисунок 2.2 составит 48 м, а с учетом величины опережения свыше 500 м а = 48∙1,25=60 м.
Ширина панели (В) составит (смотри рисунок 2.1):
Принимаем В = 280 м.
| |||
|
3 ГОРНО-ПОДГОТОВИТЕЛЬНЫЕ РАБОТЫ
3.1 Подготовка панели и технология проведения подготовительных выработок
Подготовка панели осуществляется с выработок главного направления. В первую очередь (смотри рисунок 2.1) проводятся панельный конвейерный штрек (1) и конвейерный штрек (2) лавы с выполнением через каждые 80 м конвейерных сбоек между ними. По мере проведения данных выработок через каждые 300-500 м по длине выемочного столба нарезаются вспомогательные выработки (5) для проведения вентиляционного штрека (3) лавы с разгружающей выработкой (4). Для проветривания очистного забоя подается свежий воздух по панельному конвейерному штреку лавы, а сброс исходящей струи осуществляется по вентиляционному штреку лавы.
В соответствии с технологической схемой рисунка 2.1 привести рисунок 3.1 и описать технологию проведения панельного конвейерного штрека (1) с конвейерным штреком (2) лавы.
1 – панельный конвейерный штрек; 2 – конвейерный штрек лавы; 3 – вспомогательная выработка; 4 – конвейерная сбойка; 5 – комбайн ПКС-8 (ПК-8М); 6 – бункер-перегружатель; 7 – самоходный вагон 5ВС-15М; 8 – ленточный конвейер КЛ-600; 9 – скребковый конвейер СП-302; 10 – вентилятор местного проветривания СВМ-6; 11 – став вентиляционных труб; 12 – парусная перемычка
Рисунок 3.1 – Технологическая схема проведения подготовительных
|
Проведение данных выработок начинается с проходки панельного конвейерного штрека (1) на длину откатки (300-500 м), а также конвейерных сбоек (4) через каждые 80 м и очередной вспомогательной выработки (3) с отгрузкой руды самоходным вагоном на ленточный конвейер (8). Затем комбайн отгоняется и заходит в забой конвейерного штрека (2) лавы. Руда от комбайна (5) поступает в бункер-перегружатель (6), из которого выгружается в самоходный вагон (7). Самоходный вагон транспортирует руду до скребкового конвейера (9) и разгружается на него. От скребкового конвейера руда попадает на ленточный конвейер (8), смонтированный в панельном конвейерном штреке, а затем на магистральный конвейер. В это время на пройденном участке панельного конвейерного штрека монтируется ленточный конвейер.
Подача свежего воздуха в забой конвейерного штрека лавы осуществляется вентилятором местного проветривания (10) по гибкому ставу вентиляционных труб (11). Загрязненный воздух движется по конвейерному штреку лавы и по вспомогательной выработке попадает на вентиляционный штрек лавы. Для разделения свежей и загрязненной струй воздуха сооружаются временные парусные перемычки (12). После проходки конвейерного штрека лавы на 300-500 м комбайн отгоняется, расширяет пройденный участок штрека до 4,5 м, а затем после очередного отгона по ближайшей конвейерной сбойке заходит в панельный конвейерный штрек для продолжения его проходки. Скребковый конвейер (9) перемонтируется в новую конвейерную сбойку (4), расположенную ближе всех от забоя конвейерного штрека лавы.
Далее написать состав проходческой бригады, количество звеньев, график работы.
В состав звена входит машинист горно-выемочных машин (МГВМ) и горнорабочий очистного забоя (ГРОЗ). В добычные смены машинист управляет комбайном и следит за пересыпом горной массы в бункер-перегружатель, а ГРОЗ транспортирует горную массу на самоходном вагоне от бункер-перегружателя на ленточный конвейер. В ремонтную смену звено обслуживает комплекс, осуществляет профилактический ремонт.
3.2 Техническая характеристика основного оборудования для проведения подготовительных выработок
Дать в виде таблицы 3.1 техническую характеристику комбайна ПКС-8, бункер-перегружателя БП-3А и самоходного вагона 5ВС-15М.
|
Таблица 3.1 – Техническая характеристика оборудования для проведения
подготовительных выработок
Наименование параметра | Единица измерения | Значение параметра |
Комбайн ПКС-8 | ||
Производительность | т/мин | 4,5 |
Размеры сечения выработок: − высота − ширина | м | 3,0 3,0 |
Площадь сечения выработки | м2 | 8,03 |
Угол наклона проходимой выработки | град. | ±15 |
Скорость движения: − маневровая − рабочая | м/час | |
Клиренс | мм | |
Питающее напряжение | В | |
Суммарная мощность электродвигателей | кВт | |
Число электродвигателей | шт. | |
Тип подающего механизма | гусеничный | |
Основные размеры: − длина − ширина (по гусеничному ходу) − высота | мм | |
Масса | т | 58,8 |
Бункер-перегружатель БП-3А | ||
Грузоподъемность | т | |
Вместимость | м3 | 13,8 |
Высота разгрузочной части по нижней кромке рамы | мм | 1200-2050 |
Радиус поворота | мм | |
Дорожный просвет | мм | |
Продолжительность разгрузки | сек. | |
Мощность электродвигателя | кВт | |
Основные размеры: − длина − ширина − высота | мм | |
Масса | кг | |
Самоходный вагон 5ВС-15М | ||
Грузоподъемность | т | |
Вместимость кузова: − без дополнительных бортов − с дополнительными бортами | м3 | 8,6 |
|
Продолжение таблицы 3.1 | ||
Вместимость кабельного барабана | м | |
Ширина колеи | мм | |
Высота разгрузки | мм | 430-1445 |
Дорожный просвет | мм | |
Основные размеры: − длина − ширина − высота | мм | |
Установленная мощность | кВт | |
Скорость движения цепи | м/сек | 0,15; 0,3 |
3.3 Расчет добычи руды из подготовительных выработок и содержания KCLв добываемой руде
Расчет добычи руды и содержания КСL ведется для каждой подготовительной выработки в соответствии с принятой в проекте технологической схемой подготовки и отработки панели.
Исходные данные для расчета и результаты расчета заносятся в таблицу 3.2.
Для технологической схемы, приведенной на рисунке 2.1, таблица 3.2 будет иметь следующий вид.
Таблица 3.2 – Добыча руды и содержаниеKCℓиз горно-подготовительных работ
Наименование выработки | Площадь сечения, Sп, м2 | Длина, ℓ, м | Количество, шт | Суммарная длина, ℓсум., м | Объем выработки, м3 | Добыча руды, т | Содержание в KCℓ добываемой руде, КСℓ, % | ||
всего, Vвыр. | в том числе по породе, Vпор. | Всего, Двыр. | в том числе по породе, Дпор. | ||||||
Панельный конвейерный штрек | 8,03 | ||||||||
Конвейерный штрек лавы | 12,04 | ||||||||
Вентиляционный штрек лавы | 8,03 | ||||||||
Разгружающая выработка | 8,03 |
|
Продолжение таблицы 3.2 | |||||||||
Вспомогательные выработки | 8,03 | ||||||||
Конвейерные сбойки | 8,03 | ||||||||
Монтажный штрек | 12,04 | равна дли-не лавы | |||||||
Вспомогательный монтажный штрек | 8,03 | равна дли-не лавы | |||||||
Итого по ГПР | ![]() | ![]() | ![]() |
В таблице 3.2 данные для граф 1-5, берутся из выбранной технологической схемы ( в данном случае из рисунка 2.1). Для заполнения граф 6-10 для каждой выработки (если они имеют различную привязку к пласту) рисуется полное сечение выработки (Sп), в котором выделяются сечения и так далее в соответствии с расположением выработки.
На рисунке 3.2 в качестве примера показано полное сечение выработки (Sп), пройденной одним ходом комбайна типа ПК-8 с выделением площадей сечений . Так как в принятой в курсовом проекте технологической схеме все выработки пройдены с одной и той же привязкой их к пласту, а именно – с прихватом 0,35 м кровли пласта, то других полных сечений выработок рисовать не требуется и расчетов объемов добычи руды и содержания в них КСL выполнять не надо.
Объем всей выработки и объем пустой породы (смотри рисунок 3.2) в каждой выработке (графы 6 и 7) равны:
![]() |
(3.1)
|
Рисунок 3.2 – К расчету объема добычи и качества руды
из подготовительной выработки
где – суммарная длина выработки, м (графа 5).
Определение площадей сечений выработки производится по таблице 3.3. Например, для рисунка 3.2 имеем:
h1 = 0,35 м, S1 = 0,46 м2;
h2 = 0,61 м, для h1 + h2 = 0,96 м; S = 1,95 м2, а
для h2 = 0,61 м, S2 = 1,95-0,46 = 1,49 м2;
h3 = 0,83 м, для h1 + h2 + h3 = 1,79 м; S = 4,40 м2, а
для h3 = 0,83 м, S3 = 4,40-1,95 = 2,45 м2;
h4 = 0,92 м, для h1 + h2 + h3 +h4 = 2,71 м; S = 7,16 м2, а
для h4 = 0,92 м, S4 = 7,16-4,40 = 2,76 м2;
h5 = 0,29 м, для h1 + h2 + h3 +h4 + h5 = 3,0 м; S = 8,03 м2, а
для h5 = 0,29 м, S5 = 8,03-7,16 = 0,87 м2.
Проверка правильности выполненных действий осуществляется сложением всех площадей , которые должны дать полное сечение выработки – Sп.
Для подготовительных выработок с площадью поперечного сечения,
большей 8,03 м2, подсчет сечений ведется по формуле:
|
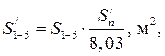
Таблица 3.3 – Определение площадей сечения выработки ( ) для комбайна ПК-8М (ПКС-8)
h S | 0,01 0,02 0,03 0,04 0,05 0,06 0,07 0,08 0,09 0,10 0,11 0,12 0,13 0,14 0,15 0,16 0,17 0,18 0,19 0,20 0,21 0,22 0,23 0,24 0,01 0,01 0,01 0,02 0,03 0,03 0,04 0,05 0,06 0,07 0,08 0,09 0,10 0,12 0,13 0,15 0,16 0,17 0,19 0,21 0,22 0,23 0,25 0,26 |
h S | 0,25 0,26 0,27 0,28 0,29 0,30 0,31 0,32 0,33 0,34 0,35 0,36 0,37 0,38 0,39 0,40 0,41 0,42 0,43 0,44 0,45 0,46 0,47 0,48 0,27 0,29 0,31 0,33 0,35 0,37 0,38 0,40 0,42 0,44 0,46 0,48 0,50 0,52 0,54 0,56 0,58 0,60 0,62 0,64 0,66 0,68 0,70 0,73 |
h S | 0,49 0,50 0,51 0,52 0,53 0,54 0,55 0,56 0,57 0,58 0,59 0,60 0,61 0,62 0,63 0,64 0,65 0,66 0,67 0,68 0,69 0,70 0,71 0,72 0,75 0,78 0,80 0,82 0,84 0,86 0,88 0,90 0,93 0,95 0,97 1,00 1,03 1,06 1,08 1,10 1,12 1,15 1,17 1,20 1,23 1,25 1,27 1,30 |
h S | 0,73 0,74 0,75 0,76 0,77 0,78 0,79 0,80 0,81 0,82 0,83 0,84 0,85 0,86 0,87 0,88 0,89 0,90 0,91 0,92 0,93 0,94 0,95 0,96 1,32 1,35 1,38 1,40 1,42 1,45 1,48 1,51 1,54 1,56 1,59 1,62 1,64 1,67 1,70 1,72 1,75 1,78 1,80 1,83 1,86 1,89 1,92 1,95 |
h S | 0,97 0,98 0,99 1,00 1,01 1,02 1,03 1,04 1,05 1,06 1,07 1,08 1,09 1,10 1,11 1,12 1,13 1,14 1,15 1,16 1,17 1,18 1,19 1,20 1,97 2,00 2,03 2,06 2,09 2,12 2,14 2,17 2,20 2,23 2,26 2,29 2,32 2,35 2,38 2,40 2,43 2,46 2,49 2,52 2,55 2,58 2,61 2,64 |
h
![]() | 1,21 1,22 1,23 1,24 1,25 1,26 1,27 1,28 1,29 1,30 1,31 1,32 1,33 1,34 1,35 1,36 1,37 1,38 1,39 1,40 1,41 1,42 1,43 1,44 2,66 2,69 2,72 2,75 2,78 2,81 2,84 2,87 2,90 2,93 2,96 2,99 3,02 3,05 3,08 3,11 3,14 3,17 3,20 3,23 3,26 3,29 3,32 3,35 |
h S | 1,45 1,46 1,47 1,48 1,49 1,50 1,51 1,52 1,53 1,54 1,55 1,56 1,57 1,58 1,59 1,60 1,61 1,62 1,63 1,64 1,65 1,66 1,67 1,68 3,38 3,41 3,44 3,47 3,50 3,53 3,56 3,59 3,62 3,65 3,68 3,71 3,74 3,77 3,80 3,83 3,86 3,89 3,92 3,95 3,98 4,01 4,04 4,07 |
h S | 1,69 1,70 1,71 1,72 1,73 1,74 1,75 1,76 1,77 1,78 1,79 1,80 1,81 1,82 1,83 1,84 1,85 1,86 1,87 1,88 1,89 1,90 1,91 1,92 4,10 4,13 4,16 4,19 4,22 4,25 4,28 4,31 4,34 4,37 4,40 4,43 4,46 4,49 4,52 4,55 4,58 4,61 4,64 4,67 4,70 4,73 4,76 4,79 |
h S | 1,93 1,94 1,95 1,96 1,97 1,98 1,99 2,00 2,01 2,02 2,03 2,04 2,05 2,06 2,07 2,08 2,09 2,10 2,11 2,12 2,13 2,14 2,15 2,16 4,82 4,85 4,88 4,91 4,94 4,97 5,00 5,03 5,06 5,09 5,12 5,15 5,18 5,21 5,24 5,27 5,30 5,33 5,36 5,39 5,42 5,45 5,48 5,51 |
h S | 2,17 2,18 2,19 2,20 2,21 2,22 2,23 2,24 2,25 2,26 2,27 2,28 2,29 2,30 2,31 2,32 2,33 2,34 2,35 2,36 2,37 2,38 2,39 2,40 5,54 5,57 5,60 5,63 5,66 5,69 5,72 5,75 5,78 5,81 5,84 5,87 5,90 5,93 5,96 5,99 6,02 6,05 6,08 6,11 6,14 6,17 6,20 6,23 |
h S | 2,41 2,42 2,43 2,44 2,45 2,46 2,47 2,48 2,49 2,50 2,51 2,52 2,53 2,54 2,55 2,56 2,57 2,58 2,59 2,60 2,61 2,62 2,63 2,64 6,26 6,29 6,32 6,35 6,38 6,41 6,44 6,47 6,50 6,53 6,56 6,59 6,62 6,65 6,68 6,71 6,74 6,77 6,80 6,83 6,86 6,89 6,92 6,95 |
h S | 2,65 2,66 2,67 2,68 2,69 2,70 2,71 2,72 2,73 2,74 2,75 2,76 2,77 2,78 2,79 2,80 2,81 2,82 2,83 2,84 2,85 2,86 2,87 2,88 6,98 7,01 7,04 7,07 7,10 7,13 7,16 7,19 7,22 7,25 7,28 7,31 7,34 7,37 7,40 7,43 7,46 7,49 7,52 7,55 7,58 7,61 7,64 7,67 |
h S | 2,89 2,90 2,91 2,92 2,93 2,94 2,95 2,96 2,97 2,98 2,99 3,00 7,70 7,73 7,76 7,79 7,82 7,85 7,88 7,91 7,94 7,97 8,00 8,03 |
Примечание – отсчет высоты выработки (h) ведется сверху вниз |
|
где | ![]() | − | площади сечений выработки с бóльшим, чем 8,03 м2 полным сечением, м2; |
![]() | − | площади сечений выработки с полным сечением, Sп = 8,03 м2; | |
![]() | − | вся площадь поперечного сечения выработки с бóльшим, чем 8,03 м2 сечением, м2. |
Например, у конвейерного штрека лавы шириной 4,5 м, . По выполненным на странице 15 расчетам
(при высоте сечения
). Тогда
.
Таким же образом рассчитываются сечения . При этом сумма всех сечений
должна составить
.
После подсчета по формуле 3.1 Vвыр. и Vпор. в каждой из подготовительных выработок, рассчитывается добыча руды (Двыр) и добыча пустой породы (Дпор) из выработок по формулам:
, (3.3)
, (3.4)
где | ![]() ![]() | − | объем всей выработки и объем пустой породы в выработке соответственно, м3; |
![]() | − | объемный вес руды и породы, т/м3 ![]() |
Полученные данные заносятся в графы 8 и 9 таблицы 3.2.
Содержание КСL в руде, добываемой из каждой подготовительной выработки, рассчитывается по формуле:
(3.5)
где | ![]() | − | содержание КСℓ (таблица 1.1) в площадях сечений выработки ![]() | ||
![]() | − |
![]() |
Результаты расчетов заносятся в графу 10 таблицы 3.2.
Таблица 3.2 заканчивается итоговыми цифрами по графам 8, 9, 10.
Средневзвешенное содержание КСL в руде, добываемой из ГПР − графа 10, рассчитывается по формуле:
, (3.6)
где | ![]() | − | добыча руды из каждой подготовительной выработки, т; | |
![]() | − | содержание KCL в руде, добываемой из каждой подготовительной выработки, %. |
|
4 ОЧИСТНЫЕ РАБОТЫ
4.1 Технология очистной выемки
На рисунке 4.1 листа формата А3 или А.4 привести:
- план лавы;
- продольное сечение лавы, включая сопряжения со штреками;
- три поперечных сечения лавы (до прохода комбайна, при проходе комбайна и после прохода комбайна или перед его отгоном;
- суточный график организации очистных работ в лаве.
На плане и сечениях показать оборудование механизированного комплекса (комбайн, забойную крепь, забойный конвейер, крепь сопряжений лавы со штреками).
Очистная выемка в лаве ведется одним или двумя комбайнами. При наличии в лаве одного комбайна он может работать по односторонней или челноковой схемам. Очистной цикл по односторонней схеме работы комбайна с передвижкой крепи впереди комбайна (смотри рисунок 4.1) состоит из следующих операций:
- зарубка комбайна «косым заездом» на участке лавы длиной 25-30 м от вентиляционного штрека (ВШЛ);
- выемка полосы в направлении от вентиляционного к конвейерному штреку (КШЛ) с одновременной передвижкой забойной крепи впереди комбайна;
- передвижка эстакады с приводом забойного конвейера и крепи сопряжения на вентиляционном штреке;
- отгон комбайна с зачисткой просыпи руды на почве вынутой полосы;
- передвижка эстакады с приводом забойного конвейера и крепи сопряжения на конвейерном штреке;
- передвижка забойного конвейера на участке лавы длиной ℓл − (25-30) м, считая от конвейерного штрека.
|
![]() | |||
![]() | |||
режущим органом комбайна. После выемки уступа заканчивается задвижка забойного конвейера по всей длине лавы и из образовавшейся от зарубки «косым заездом» ниши начинается выемка новой полосы. Последовательность выполнения операций по выемке уступа, образующегося в результате вырубки на конвейерный штрек опережающего шнека комбайна такая же, как и на вентиляционном штреке.
При челноковой схеме работы комбайна в очистном цикле отсутствует операция по отгону комбайна, так как выемка руды ведется как от ВШЛ к КШЛ, так и в противоположном направлении – от КШЛ к ВШЛ с одновременной передвижкой забойной крепи и забойного конвейера позади комбайна.
4.2 График организации очистных работ в лаве
Механизированный комплекс обслуживает бригада в составе 10 человек. Режим работы бригады четырехсменный, три смены добычные и одна – ремонтная. Продолжительность смены – 6 часов. В каждую смену работает звено из двух человек; машиниста горно-выемочных машин 7-го разряда и горнорабочего очистного забоя 6-го разряда. В ремонтную смену дополнительно выходит один электрослесарь и один крепильщик. Время работы
комплекса по добыче – 18 часов в сутки, профилактическое обслуживание – в ремонтную смену (6 часов).
По нормам продолжительность выполнения комбайном СЛ-500 одного цикла очистных работ в лаве длиной 200 м составляет 270 мин и складывается из времени выполнения следующих операций:
- зарубка комбайна «косым заездом» – 20 мин.;
- выемка руды с одновременной передвижкой забойной крепи – 130 мин.;
- концевые операции у вентиляционного штрека – 35 мин., у конвейерного штрека – 45 мин.;
- отгон комбайна и передвижка забойного конвейера – 40 мин.
Количество циклов (N) в сутки с учетом трех добычных смен составит:
(4.1)
где | Тс | − | время трех добычных смен, мин.; | ||
Тп | − |
|
Количество циклов в сутки можно определять другими способами, например, путем расчета суточной производительности комбайна (Qсут):
(4.2)
где | Nуст | − | установленная мощность электродвигателей приводов, кВт (N=800 кВт); |
t | − | время добычных смен в сутки, час (t=18 час.); | |
Kисп | − | коэффициент использования машинного времени (Кисп = 0,35); | |
Эр | − | энергоемкость разрушения калийной руды, ![]() |
Выход руды с одной полосы (Доч):
т, (4.3)
где | ℓл | − | длина лавы, м ![]() |
mл | − | вынимаемая мощность, м ![]() | |
bз | − | ширина захвата комбайна, м ![]() | |
γ | − | объемный вес руды, т/м3 ![]() |
Количество циклов в сутки:
(4.4)
|
По полученным данным продолжительности операций в цикле и количеству циклов строится график организации очистных работ в лаве, который приводится на рисунке 4.1.
4.3 Характеристика основного оборудования механизированного комплекса
В состав комплекса, используемого для механизации процессов очистной выемки и управления кровлей полным обрушением, входят:
- двухшнековый комбайн СЛ-500 – 1 шт.
- забойный скребковый конвейер ЕКF-3 – 1 шт.
- штрековый конвейер СПШ-1-228 – 2 шт.
- забойная крепь Фазос – 12/28 – 100 шт.
- крепь сопряжения Фазос – 15/31 – 3 шт.
- насосная станция СНН-150/30 – 2 шт.
- холодильная установка РК-130 – 1 компл.
- специальный кабелеукладчик – 1 компл.
- электрооборудование – 1 компл.
- гидропередвижчик УПШ-1700 – 2 («кривой» и «прямой»).
Приводится техническая характеристика комбайна, забойной крепи, крепи сопряжения, забойного скребкового конвейера.
Таблица 4.1 – Техническая характеристика основного оборудования
механизированного комплекса
Наименование параметра | Единица измерения | Значение параметра |
Комбайн СЛ-500 | ||
Вынимаемая мощность | м | 2,3-3,0 |
Установленная мощность приводов | кВт | 2х400 |
Рабочее напряжение двигателя | В | |
Высота комбайна от почвы пласта | мм | |
Ширина захвата режущего органа | мм | |
Диаметр шнеков | мм | |
Подрубка почвы | мм | |
Вес комбайна | кг | |
Забойная крепь Фазос – 12/28 | ||
Количество секций крепи | шт. | |
Количество гидростоек в секции | шт. | |
Конструктивная высота крепи: − минимальная − максимальная | м | 1,2 2,9 |
|
Продолжение таблицы 4.1 | ||||||
Шаг установки секций крепи, S | м | 2,0 (между секциями № 99 и № 100 S=1,75 м) | ||||
Шаг передвижки секций крепи | м | 0,8 | ||||
Длина перекрытия секции крепи | м | 2,65 | ||||
Ширина перекрытия секции крепи | м | 1,70 | ||||
Ширина призабойного пространства, Вз | м | 3,85 | ||||
Сопротивление гидростойки крепи: − при начальном распоре − при рабочем давлении, Qс | кН | |||||
Масса секции | кг | |||||
Тип крепи | − | Фазос – 15/31 О3 | ||||
Количество секций крепи на конвейерном штреке | шт. | |||||
Количество секций крепи на вентиляционном штреке | шт. | |||||
Количество стоек в секции крепи | шт. | |||||
Конструктивная высота крепи: − минимальная − максимальная | м | 1,5 3,085 | ||||
Шаг передвижки секций крепи | м | 0,8 | ||||
Длина перекрытия | м | 3,05 | ||||
Ширина перекрытия | м | 1,4 | ||||
Сопротивление секции крепи: − при начальном распоре крепи − при рабочем давлении | кН | |||||
Забойный конвейер ЕКФ – 3 | ||||||
Производительность | т/час | |||||
Длина конвейера | м | 150-210 | ||||
Тяговый орган: − колибр цепи − количество цепей − скорость движения цепи − шаг установки скребков − разрывное усилие | мм шт м/сек мм кН | 30х108 1,0 | ||||
Мощность электродвигателя | кВт | |||||
Количество двигателей | шт. | |||||
Напряжение | В | |||||
Рештак:
− длина
− ширина
Дата добавления: 2017-03-12; просмотров: 1451; |