Классификация и способы ведения химико-технологических процессов
Характерной особенностью технологических процессов в производствах являются химические превращения, происходящие в результате химических реакций и приводящие к образованию веществ с отличными от исходных продуктов свойствами. Химическое превращение сопровождается физическими, химическими и тепловыми процессами, которые вместе с химической реакцией составляют физико-химический процесс.
Процессы химической технологии классифицируются в соответствии с законами, лежащими в их основе. Такая классификация позволяет выделить следующие группы процессов.
- гидромеханические
- тепловые
- массообменные
- механические
- химические
Гидромеханические процессы - в разделе «гидравлика» рассматривают вопросы равновесия жидкости в состоянии покоя.
«Гидродинамика» - изучает движение жидкостей и газов, разделение жидких, газовых и неоднородных систем, перемещение их через пористые перегородки.
Тепловые процессы - включают в себя нагревание, охлаждение реакционных масс, выпаривание растворов, конденсация паров и другие процессы, протекающие при подводе или отводе тепла. Тепловые процессы основываются на законах теплопередачи. Массообменные и диффузионные процессы - характеризуются переносом исходных компонентов внутри фазы из одного состояния в другое средством диффузии. К этой группе относятся процессы абсорбции, перегонки, экстракции, кристаллизации, адсорбции, десорбции и сушки.
Механические процессы - измельчение твердых тел, транспортировка, разделение и смешение сыпучих материалов, подчиняются законам механики твердых тел.
Химические процессы - протекают в соответствии с законами химической кинетики и зависят от процессов тепло и массопереноса.
Процессы химической технологии в зависимости от способа организации делятся на периодические и непрерывные. Периодические проводятся в аппаратах, которые работают в циклическом режиме. Непрерывные осуществляются в условиях непрерывной загрузки исходных материалов в аппаратах и выгрузки материалов из аппарата.
Конструкционные материалы
В химической технологии перерабатывается большое количество органических и неорганических продуктов. Эта переработка проводится в широких диапазонах температур (от 200° до 2500°) при давлении от 101,3 до 600 МПа, иногда в сильно - агрессивных средах. Для проведения химических реакций и последующей переработке полученных смесей используются различная аппаратура, которая должна удовлетворить ряд требований, основными из которых являются механическая надежность, долговечность, конструктивное совершенство, простота изготовления, удобство транспортировки и монтажа, удобство эксплуатации.
Механическая надежность - характеризуется прочностью, жесткостью, устойчивостью, герметичностью. Для деталей аппаратов подверженных сжимающим нагрузкам важна их жесткость, т.е. способность сохранения первоначальной формы, устойчивость конструкции. Важным качеством является герметичность. Это необходимое условие для аппаратов и трубопроводов, работающих под избыточным давлением или вакуумом. Долговечность - зависит от ряда факторов и для отдельных производств. Для большинства типов оборудования химических заводов длительность эксплуатации 7-10 лет.
Конструкционное совершенство - характеризуется простотой устройства, малой массой и габаритами, небольшими затратами дорогих материалов, технологичностью исполнения. Коррозийная стойкость металлических материалов характеризуется скоростью коррозии и глубинными показателями коррозии.
Химическая аппаратура должна удовлетворять эксплуатационным показателям: обеспечивать заданную производительность, расходы, коэффициента по сырью, минимальные эксплуатационные расходы, удобство обслуживания, надежность и безопасность в работе.
Выбор конструктивных материалов
При выборе материала для изготовления аппаратов и трубопроводов учитываются прочностные характеристики, теплофизические свойства, стойкость, коррозионная устойчивость, удобство обработки. Основным материалом являются металлы.
Стали - основная группа материалов, в них содержится углерода до 0,3%. А в легированных (стали с низким содержанием водорода, хорошо вытягиваются, но плохо штампуются) - 0,2% углерода.
Условно стали подразделяют на 1)низколегированные - с относительно небольшим количеством благородных добавок и 2)высоколегированные - содержание добавок в них может превышать содержание железа.
Важнейшие легирующие элементы
Хром - улучшает механические свойства, износостойкость, повышает коррозионную стойкость, делает сталь энергостойкой, недостаток - плохо свариваются.
Никель - улучшает прочностные свойства при высоких температурах, повышает коррозионную стойкость, но дорогостоящий.
Марганец - повышает прочностные свойства: при содержании его 10-15 кг к сплаву, приобретает высокую сопротивляемость удара.
Кремний - увеличивает коррозионную стойкость, жаростойкость, но труден в обработке. Ванадий - увеличивает пластичность, улучшает свариваемость, улучшает свойства стали. Титан, ниобий, вольфрам - улучшает свойства стали.
Маркировки сталей
С точки зрения коррозионной стойкости особое значение в химическом машиностроении имеют высоколегированные стали. Легирующие элементы обозначают буквами:
Х - хром Н - никель М - молибден Г - марганец С - кремний Т - титан Б - ниобий В - вольфрам Д - медь Ю - алюминий
Химическая аппаратура должна удовлетворять эксплуатационным показателям, обеспечивать заданную производительность, расходы коэффициентов по сырью, минимальные эксплуатационные расходы, удобства обслуживания, надежность и безопасность в работе.
Чугуны - преувеличение углерода в железных сплавах до 2,8 - 3,7%. Стоимость их намного дешевле, они не обладают пластичностью, детали из них изготавливают только плавкой.
Температура в аппаратах, изготовленных из чугунов, не превышает 250° и давление 0,6 МПа. Низколегированные стали, и чугуны имеют недостаточно облагороженных добавок и называются черными металлами.
Цветные металлы
В химической промышленности помимо сталей и чугунов применяют: алюминий, тантан, никель, свинец, а также сплавы на их основе - латунь, бронза.
Алюминий - стоек к действию кислот (фосфорной, уксусной), сернистых соединений, органических соединений, плохо сваривается, плохие литейные свойства, применяют до 200°.
Медь - хорошо прокатывается, хорошо тянется, штампуется, но плохо обрабатывается из- за большой вязкости. Медь необходима для изготовления аппаратов работающих при низких температурах от 180° до 250°С.
Титан - по прочностным качествам приближается к стали. Он стоек против азотной кислоты, нитратов, хлоридов, органических кислот и мочевины. Используется при изготовлении труб, листа, проката.
Тантан - характеризуется прочностью, тугоплавкостью, очень дорог, употребляется в виде фольги.
Пластмассы - они обладают низким коэффициентом проводимости, поэтому с успехом применяются как теплоизоляционные материалы.
Трубопроводы
Трубопроводами называются участки труб соединенных между собой трубопроводной арматурой и предназначенные для транспортировки жидкостей, газов и сыпучих веществ. По назначению трубопроводы бывают: магистральные, межзаводские, межцеховые, межустановочные, технологические обвязочные.
По изготовлению - бесшовные и сварные.
По материалам - металлические и неметаллические.
По расположению - наземные и подземные.
По эксплуатации - холодные (минус 50°) и горячие (более 50°).
Трубопроводы для застывающих жидкостей оснащаются параспутниками.
Трубопроводы характеризуются условным давлением и диаметром.
РУ - максимальное рабочее технологическое давление, которое может выдержать трубопровод.
ДУ - внутренний диаметр трубы.
Соединения трубопроводов.
![]() |
разъемные неразъемные
фланцевые, раструбные, резьбовые сварка, клейка, спайка
Существует пять видов фланцевых соединений: гладкая с рисками - устанавливается на давление 16 АТ выступ-впадина - устанавливается на давление 25АТ шип-пас - устанавливается на давление 40 АТ
под металлическую прокладку - устанавливается на давление 64 АТ под кольцевую прокладку - устанавливается на давление 100АТ Крепежный материал для фланцев: болты - 16 АТ; шпильки - свыше 16АТ
Фасонные части трубопровода Крестовина - делит поток на три потока Тройник - разделяет поток на два потока
Переходник (фитинг) - предназначен для перехода с одного диаметра трубы на другой. Отвод (колено) - изменяет поток на 90°
Отвод (калач) - изменяет поток, а 180°
Компенсатор - устройства, предназначенные для снижения температурных деформаций.
Трубопроводная арматура
На трубопроводах устанавливается арматура различного назначения и устройства. Она служит для периодического включения и отключения потока, протекающего по трубопроводу (запорная), поддержания заданного давления, температуры или расхода (регулирующая), предупреждения повышения давления выше допустимых пределов (предохранительная), для контроля уровня в аппаратах.
![]() |
а) Стальная клиновая задвижка; б) обратный поворотный клапан; в) вентиль обтекаемой формы; г) проходной сальниковый кран.
Запорная арматура: задвижки, вентили, краны.
Задвижка состоит из корпуса, крышки, через которую проходит шток (шпиндель); на нижней части которой подвешены два диска, а верхняя заканчивается штурвалом (барашком). Для уплотнения штока в крышке имеется сальниковый карман, в который набивается сальниковая набивка и затягивается грунт - буксой. На корпусе ставится РУ и ДУ. Применяется на диаметры трубопровода от 50 до 2500 мм, и для любых газовых и жидких сред. Поток может подаваться в ту и другую сторону. Задвижка ЗКС (клиновая, стальная) ставится только не на агрессивные среды.
Обратный клапан - состоит из корпуса, на нем ставят РУ и ДУ, стрелку. Внутри имеется седло, к которому шарнирно прикреплена заслонка. Сверху и снизу корпус закрывают две крышки на фланцах. Обратный клапан ставят на линиях нагнетания центробежных насосов, чтобы предотвратить ход жидкости в обратном направлении.
Вентиль - состоит из корпуса, крышки, через которую проходит шток, заканчивается запорным органом - клапаном, при работе садящимся на седло. В крышке имеется сальниковый карман, куда набивается сальниковый уплотнитель. Сальник может затягиваться грунт - буксой или гайкой. Крышка может соединяться с корпусом или фланцем, или резьбой. На корпусе ставится РУ, ДУ и стрелка. Вентиль устанавливается на трубе диаметром от 50 до 250 мм, только на чистые среды. Поток может идти только под клапаном.
Кран пробковый - состоит из корпуса в виде гнезда, крышки, через которую проходит шток. Заканчивается запорным органом - в виде пробки с прорезью. На корпусе ставится РУ и ДУ. Ставят только на чистые среды, газовые и паровые фазы, на малые диаметры трубопроводов. На штоке имеется риска , если риска находится в горизонтальном положении, то кран открыт, если в перпендикулярном, то закрыт.
Регулирующая арматура
К регулирующей арматуре относятся: регулирующий клапан, который состоит из мембранно-пружинного организма, верхней и нижней крыжки, прорезиненной мембраны, диска, направляющего стакана, штока, соединительной муфты. Клапан состоит из: золотника, кольца, седла и мембранного привода.
Клапан запорный проходной |
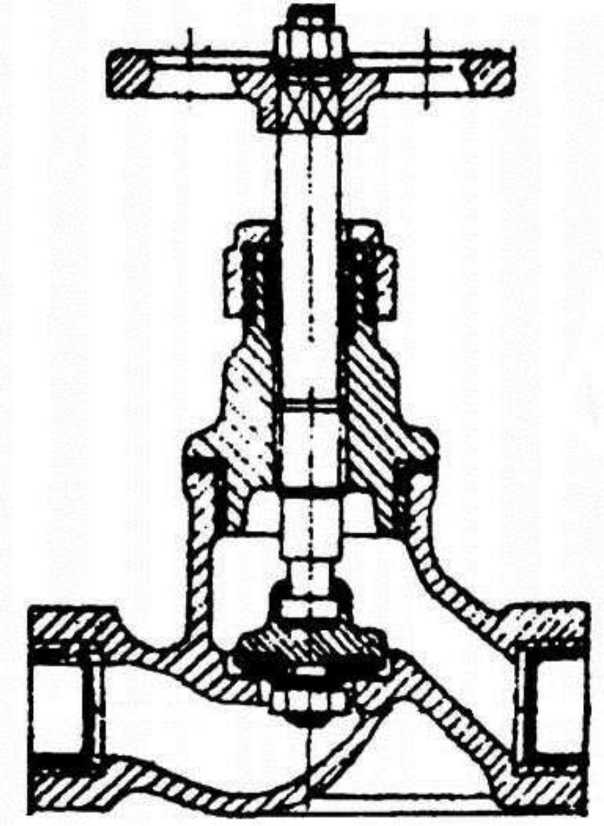
Предохранительная арматура
К ней относится предохранительный клапан, предназначенный для автоматической защиты оборудования и трубопровода от превышения давления. Свыше заранее установленной величины под средством сброса избытка рабочей среды.
Устройство клапана состоит из корпуса, седла, упорного закрепляющего штифта, направляющего кольца, тарелки клапана, направляющей втулки, штока, пружины, гайки для регулирования клапана и устройства для подрыва клапана от руки. Предохранительный пружинный клапан
![]() |
Насосы
Насосы предназначены для перекачивания жидкостей.
По конструкции насосы классифицируются:
Центробежные или лопастные - где кинематическая энергия сообщается жидкости с помощью вращающихся лопастей.
Поршневые (плунжерные) - энергия передается путем периодического изменения объема рабочих камер.
Насосы общего назначения - предназначены для перекачивания воды и неагрессивных жидкостей.
Нефтяные насосы - предназначены для перекачивания нефти, нефтепродуктов, сжиженных углеводородных газов.
Работа насосов характеризуется следующими показателями:
N - Мощность (кВт)
Q - Подача (производительность м3/час) h - Частота вращения вала (оборот/мин)
H - Напор в метрах столба жидкости (высота на которую подается жидкость)
Марки нефтяных насосов
НГ - нефтяной горячий насос (более 200°)
НК - нефтяной консольный (подшипники находятся по одну сторону от рабочего колеса)
НД - нефтяной - двухнапорный (опоры с двух сторон, могут быть до 9 рабочих колес)
НСД - нефтяной - секционный с двухсторонней подачей жидкости
НПС - нефтяной секционный с плоским разъемом корпуса
НКЭ - нефтяной (консолный) на одном валу с электрическим двигателем.
Центробежный насос
![]() |
2) сальник
3) корпус
4) рабочее колесо
5) вал
6) лопасти рабочего колеса
7) нагнетательный патрубок
Центробежный насос состоит из корпуса, имеющего спиралевидный канал 3, в котором вращается рабочее колесо 4 , укрепленное на валу 5 . На рабочем колесе 4 укреплены лопасти 6, между которыми располагаются каналы для прохода жидкости. Подача жидкости в насос осуществляется через всасывающий штуцер 1, соединенный с центральной частью рабочего колеса.
Нагнетательный штуцер 7, расположенный тангенциально по отношению к рабочему колесу служит для отвода жидкости из насоса. Для уплотнения вала рабочего колеса имеются сальники 2.
Принцип работы центробежного насоса
При вращении рабочего колеса во всасывающем патрубке создается разряжение, жидкость заходит в рабочее колесо и под действием центробежной силы отбрасывается к стенкам корпуса насоса. Собирается в направляющем аппарате и сила вращения превращается в силу давления, и жидкость выбрасывается в нагнетательный патрубок. Подготовка к пуску насоса
1) Сделать визуальный осмотр
2) Проверить заземление у насоса и электродвигателя
3) Проверить наличие сальников (торца)
4) Проверить наличие смазки в картере
5) Проверить наличие ограждений у вращающихся частей
6) Вручную прокрутить вал насоса
7) Проверить целостность фундамента и степень затяжки анкерных болтов
8) Проверить исправность манометра: целостность корпуса и стекла, наличие пломбы, наличие штампа о последней поверке (1 раз в год).
Пуск насоса без байпаса
1) Открываем задвижку на всасывающей линии
2) Проверяем отсутствие воздушной пробки
3) Включаем электродвигатель и даем насосу поработать на себя в течение 3 минут. За это время проверяем затяжку сальников (они должны пропускать 50-60 капель в минуту). Смотрим, не греется ли насос, нет ли шума и вибрации, смотрим по амперметру силу тока, в ту или сторону вращается вал. Если все нормально, то открываем задвижку на линии нагнетания.
Остановка насоса
1) Закрываем задвижку на линии нагнетания
2) Отключаем электродвигатель
3) Закрываем задвижку на линии всасывания
! - центробежный насос всегда пускают при закрытой задвижке на линии нагнетания и под заливом жидкости.
Кавитация - мгновенное вскипание жидкости, при давлении ниже давления насыщенных паров при данной температуре.
Чаще всего кавитация возникает на входе в рабочее колесо насоса, или от конденсации паров на выходе с рабочего колеса, при высоком давлении, при низкой температуре. Кавитация также возникает при резком закрытии задвижки на линии всасывания, при уходе уровня из емкости, из-за неправильной установки насоса:
1) насос установлен выше уровня перекачиваемой жидкости
2) насос установлен ниже уровня перекачиваемой жидкости.
Для насоса находящегося выше уровня перекачиваемой жидкости, высоту всасывания уменьшают на 0,5-1 метр (кавитационный запас).
Для насоса находящегося ниже уровня перекачиваемой жидкости, высоту всасывания увеличивают на 0,5-1м, но общая высота не должна превышать 3 метра.
Кавитация сопровождается: гидравлическими ударами, вибрацией, шумом, падением давления и производительности. Насос немедленно отключают и переходят на резервный насос.
Переход с работающего насоса на резервный насос
Расстояние между насосами не должно превышать 80 см.
1) готовимся к пуску резервного насоса
2) открываем задвижку на линии всасывания резервного насоса
3) проверяем отсутствие воздушной пробки
4) включаем электродвигатель резервного насоса и даем поработать не более 3 минут на себя
5) затем одновременно один машинист у резервного насоса открывает задвижку на линии нагнетания, а второй закрывает задвижку на линии нагнетания рабочего насоса, затем отключает электродвигатель у рабочего насоса и закрывает задвижку на линии всасывания у рабочего насоса.
Поршневые насосы
![]() |
Поршневой насос простого действия:
/ — всасывающий трубопровод, 2 — клапанная коробка, 3 — нагнетательный клапан, 4 — нагнетательный, трубопровод. 5 — воздушный колпак, 6 — корпус, 7 — цилиндр, 8 —всасывающий клапан, 9 — поршень нлн плунжер. 10 — кривошнпио-шатуииый механизм ' .
Поршневые насосы подразделяются на приводные, (работающие от электродвигателя) и прямодеиствующие паровые.
Приводные насосы по количеству цилиндров бывают одно, двух, трех, четырех цилиндровые. По расположению цилиндров - вертикальные и горизонтальные. По конструкции насосы бывают собственно-поршневые, плунжерные, диафрагмовые. Принцип работы поршневого насоса.
При движении поршня слева - направо в клапанноИ коробке создается разряжение, всасывающиИ клапан 8 открывается и жидкость идет следом за поршнем. При движении поршня справа налево в клапаннои коробке создается давление, а нагнетательныи клапан открывается. И почти вся жидкость выходит в линию нагнетания, и только часть жидкости забрасывается в газовый колпак. При следующем движении поршня слева
направо, жидкость из газового колпака поступает в линию нагнетания, тем самым сглаживает пульсацию насоса.
Пуск поршневого насоса
1. Готовим насос к пуску
2. Открываем линию всасывания и линию нагнетания
3. Включаем электродвигатель
Отключение поршневого насоса
1. Закрываем задвижку на линии всасывания
2. Отключаем электродвигатель
3. Закрываем задвижку на линии нагнетания
Паровой прямодействующий насос
![]() |
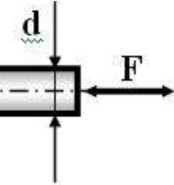
По количеству цилиндров бывают одноцилиндровые (симплекс), двухцилиндровые (дуплекс).
Насос состоит из паровой и гидравлической машины, прямодействующим называется потому, что при движении поршня паровой машины приходит в действие поршень гидравлической машины. Оба поршня находятся на одном штоке. Над цилиндром паровой машины находится золотниковая камера, в которой золотник перемещается, распределяя пар, то в правый, то в левый край канала.
Острый пар - пар, температура которого 250° и давление 10АТ. Острым называется потому, что имеет непосредственный контакт с деталями или веществами.
Мятый пар - отработанный пар, температура которого 180°, давление 4АТ.
Глухой пар - пар, не имеющий непосредственного контакта с деталями или веществами. Перегретый пар - сухой пар, безводный, температура 420°
Пуск парового насоса
1. Готовим паровую машину к пуску
2. Открываем продувочные краны на цилиндрах паровой машины
3. Открываем задвижку на остром паре, так, чтобы поршень не начал двигаться, и прогреваем цилиндр до тех пор, пока пар пойдет без конденсата.
4. Одновременно готовим к пуску гидравлическую машину
5. Открываем задвижку на всасывание и на нагнетание
6. Подаем охлаждение
7. Закрываем продувочные краны
8. Открываем кран до манометра, и открываем задвижку на линии мятого пара, чтобы поршень начал двигаться. И число было 16-20 ходов в минуту. Если поршень не начал двигаться, то нужно закрыть задвижку на мятом паре, открыть продувочные краны, выпустить весь пар, а затем вручную двигать поршень.
Днаграм* ма сжатия газов в идеальном компрессоре |
Компрессоры |
р |
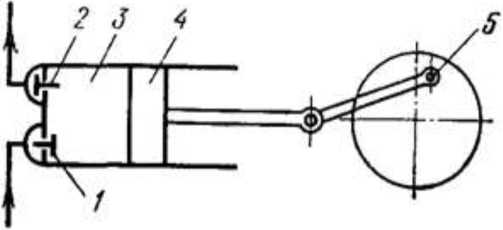
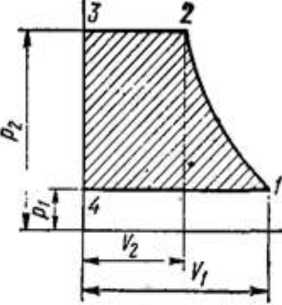
Поршневой компрес* сор простого действия:
/ — всасывающий клапан, 2 — нагне-
тательный клапан, 3 — цилиндр, 4 —
поршень, 5 — кривошипио-шатунный
механизм
Это машины, предназначенные для сжатия и перемещения газов. По принципу действия они бывают центробежные, поршневые; по перекачиваемой среде газовые и воздушные. Центробежные компрессоры подразделяются на вентиляторы - (низконапорные машины р=0,1-0,15 атм.) газодувки и воздуходувки (средние напорные машины р=0,1-2,5 атм.), турбокомпрессоры - (центробежные p=4-30 атм.),вакуум-насосы- это машины предназначенные для откачивания газов из емкостей под р чуть ниже атмосферного и сжатия их до атмосферного.)
Эксгаустеры - (высоконапорные вакуумные машины, для откачивания газов с p ниже атмосферного, сжатия их до атмосферного и чуть выше.)
Поршневые компрессоры по расположению бывают вертикальные и горизонтальные. По числу сжатия бывают 1 -ступенчатые и многоступенчатые. Поршневые компрессоры по создаваемому давлению бывают низконапорные (р до 8 атм.); средненапорные (р от 8 до 80 атм.); высоконапорные (р от 80 до 1000 атм.) и сверхнапорные (р свыше 1000 атм.).
По числу ступеней сжатия бывают от 1 до 17 ступеней. По расположению цилиндров бывают горизонтальные, вертикальные, угловые, V-образные, W- образные, звездообразные, оппозитные (поршни располагаются по обе стороны от коленчатого вала).
Неоднородные системы и методы их разделения.
К неоднородным системам относятся системы, состоящие из двух или нескольких несмешивающихся фаз: туман, дым, суспензия, эмульсия, пена.
Суспензия - система, состоящая из сплошной жидкой фазы, в которой находятся взвешенные, твердые частицы.
Эмульсия - система, состоящая из жидкости и распределенных в ней капель другой жидкости, нерастворимой в первой.
Пена - система, состоящая из жидкости и распределенных в ней пузырьков газа.
Дым - система, состоящая из газа и распределенных в нем частиц твердого материала.
Туман - система, состоящая из газа и распределенных в нем капель жидкости, образующихся в результате конденсации.
Разделение жидких неоднородных систем осуществляется с помощью отстаивания, фильтрования, центрифугирования, сепарирования и электроочистки.
Отстаивание
Отстаивание - наиболее дешевый процесс разделения неоднородных систем.
Сутвнзия
Осбетлсннок
жидкость
Шлам |
Отстойник непрерывного действия:
/ — гребки, 2 — цилиндрический
резервуар, 3 — кольцевой желоб.
4— мешалка
Отстойники периодического действия представляют собой низкие бассейны без перемешивающих устройств. Он заполняется суспензией, которая отстаивается в состоянии покоя в течение времени, необходимого для аппарата. После чего сливают осветленную жидкость через сифонную трубку или шланг. Осадок представляет собой шлам, его выгружают вручную. С увеличением температуры вязкость жидкости уменьшается, и скорость осаждения увеличивается.
Отстойник непрерывного действия
![]() |
Фильтрование
![]() |
схема процесса фильтрования
/ — сосуд для фильт-
оваиня. 2 — осадок.
— фильтровальная перегородка. 4 - лож
ное (перфорирован-
ное) днище
Процесс разделения суспензии с использованием пористых перегородок, которые задерживают твердую фазу суспензии и пропускают её жидкую фазу, называется фильтрованием.
Процесс осуществляется на фильтре, состоящем из сосуда, в котором имеется ложное днище. На днище уложена фильтровальная перегородка. Под действием разности давлений по обе стороны фильтрующей перегородки жидкость - фильтрат проходит через её поры, а твердые частицы суспензии задерживаются в ней, образуя слой осадка. Скорость поддерживается постоянной, если по мере накопления слоя осадка увеличивать перепад давления.
Нутч - фильтр, работающий под вакуумом
К вакуум - насосу /
Нутч-фильтр, работающий
резервуар. |
2 — фильтрующая |
перего |
родка, 3 — ложное дннщс, 4 — емкость |
под вакуумом:
Нутч - фильтр, работающий под вакуумом, изготавливается в виде открытого круглого или прямоугольного резервуара, на некотором расстоянии от дна резервуара находится ложное днище, на дно уложена перегородка. Суспензия заливается на нутч - фильтр сверху, после чего создается вакуум.
Нутч - фильтр, работающий под давлением
![]() |
Нутч-фильтр, работающий под давлением:
/ — корпус аппарата, 2—съемная верхняя часть, 3—штуцер для загрузки, 4 — фильтрующая перегородка, 5 — ложное днище, б—штуцер для отвода фильтрата
Нутч-фильтр, работающий под давлением, состоит из корпуса, съемной крышки и фильтрующей перегородки, лежащей на ложном днище. Для подачи суспензии служит штуцер 3, фильтрат удаляется через штуцер 6. Цикл работы состоит из следующих операций: наполнение нутч-фильтра суспензией, фильтрование суспензии под давлением, удаление осадка с фильтрующей перегородки, съема и промывки фильтрующей перегородки. Недостатками всех нутч-фильтров являются большая занимаемая площадь и сложность обслуживания.
Сепарирование.
Сепарированием называется процесс разделения двух несмешивающихся жидкостей различной плотности.
![]() |
Сепаратор для разделения несмешивающихся жидкостей:
а — схема сепаратора, б — конические перегородки; / — вывод тяжелой жидкости, 2 — вывод легкой жидкости, 3 — труба поступления эмульсин, 4 — верхняя коническая перегородка, 5 —корпус барабана, 6 —
нижняя коническая перегородка
Эмульсия, подлежащая разделению, вводится в корпус барабана 5 по центральной трубке 3, проходит под нижней конической перегородкой 6 и поступает во внутреннюю полость барабана. Здесь под действием центробежной силы происходит расслаивание эмульсии. Тяжелая жидкость отбрасывается к периферии, попадает в канал между корпусом 5 и перегородкой 4 и удаляется через отверстие 1. Легкая жидкость скапливается в центральной части барабана, поднимается вверх и отводится через отверстие 2.
Центрифугирование.
Центрифугированием называется процесс разделения неоднородных систем в поле центробежной сил.
центрифуга: |
/-штуцер для выгрузки осадка, 2-окна |
для*выгрузки осадка, S-окна Для загруз |
кн суспензии, 4 — барабан, 5 —кожух, 5- |
коиический. шнек, 7 - ввод суспензии, 8 - |
окна для выгрузки фильтрата, 9 - штуцер |
для выгрузки фильтрата |
Непрерывно действующая
1 ттктя
♦ житот
В непрерывно действующей центрифуге имеются конический вращающийся барабан 4 и конический разгрузочный шнек 6, размещенный внутри барабана. Суспензия вводится по трубе 7 внутрь шнека и под действием центробежной силы выбрасывается через окна 3 во внутреннюю полость барабана 4. В барабане происходит отстаивание суспензии. Осветленная жидкость под действием центробежной силы перемещается к окнам 8, перетекает в кожух 5 и удаляется через штуцер 9. Осадок непрерывно перемещается в барабане справа налево с помощью шнека, который вращается с частотой, несколько меньшей частоты вращения барабана. Через окна 2 осадок выбрасывается в кожух 4 и выводится из центрифуги через штуцер 1.
В промышленных условиях пыль образуется в результате измельчения твердых тел (при дробление ,размалывание, транспортировке и при горении топлива. Туманы образуются в результате конденсации паров. Промышленная очистка газов, взвешенных в нем твердых, или жидких частиц производится для уменьшения загрязненности воздуха или улавливания из газа ценных продуктов. Очистка отходящих газов является одной из важнейших задач химического производства.
Отстойный газоход
![]() |
Устройством для очистки газа от пыли является отстойный газоход.
На пути запыленного газа устанавливают камеру с перегородками, изменяющими направление, и сборниками пыли. За счет увеличения скорости потока падают частицы пыли, сохраняя прямолинейное движение за счет инерции, ударяются о перегородки и собираются в сборники. Эти устройства применяются для предварительной грубой очистки газов.
Пылеосадительныя камера
![]() |
Схема пылеосадительной камеры:
,7Г^Га3опРовод: —регулировочный шибер; 3 — распреде
лительный канал; * —листы; 5 — сборный канал; 6 — верти-
кальный канал; 8 — дверцы.
Более качественная очистка газов достигается в пылеосадительных камерах.
Устройство пылеосадительной камеры основано на принципе развития максимальной площади осаждения, в целях повышения производительности.
Аппарат с горизонтальными полками делится на ряд каналов малой высоты. Поступление запыленного газа регулируется клапанами. Осажденная пыль периодически выгружается через дверцы.
Циклон
![]() |
Штуцер для выхода газа 2) центральная труба для выхода очищенного газа 3)
крыжка 4) корпус 5) коническое днище 6) штуцер для удаления пыли
Очистка газов под действием центробежной силы производится в специальных аппаратах циклонах. Запыленный газ поступает через входной штуцер 1, в корпусе поток газа начинает вращаться вокруг центральной трубы 2, вдоль внутренней поверхности стенок циклона. При таком вращении частицы пыли под действием центробежной силы отбрасываются к периферии, оседают на внутренней поверхности корпуса 4 и опускаются в коническое днище 5. Очищенный газ выводится из циклона через центральную трубу 2.
Рукавный фильтр
Очищенный
газ
Запыленный
газ
Пыль
Рукавный фильтр:
/ — вход газа, 2 — распределительная
камера, 3 — рукава, 4 — распредели
тельная решетка, 5 — встряхивающее устройство, 6 — выход очищенного га
за, 7 — выход пыли
Запыленный газ нагнетается вентилятором через входной газоход 1, в камеру 2. Далее газ проходит через рукава 3, нижние концы которых закреплены на патрубках распределительной решетки 4. Пыль осаждается в порах ткани, а очищенный газ через трубку 6, удаляется из аппарата. Пыль удаляется через патрубок 7.
Мокрая очистка газов.
Барботажный пылеуловитель
Очищенный газ
Жидкость
Барботажный пылеуловитель:
1 — штуцер поступления запыленного газа, 2 — вход жид кости, 3 — выход очищенного газа, 4 — корпус аппарата, 5 — штуцер отвода жидкости, 6 — перфорированное дни
ще, 7 — штуцер отвода жидкости
М: |
ческом поле:
а — трубчатый фильтр, б — пластинчатый фильтр
Состоит из корпуса 4, внутри которого расположено перфорированное днище 6. Запыленный газ поступает под днище через штуцер 1 и соприкасается с жидкостью, подаваемой на днище, образуя пенный барботажный слой. Жидкость захватывает твердые частицы и удаляется через штуцер 5, а некоторая ее часть, прошедшая через решетку уходит через штуцер 7 в днище аппарата. Очищенный газ удаляется из аппарата через штуцер 3.
Мокрая очистка газов применяется для тонкой очистки газа, но при этом происходит его увлажнение. Мокрая очистка газов проводится в аппаратах различных конструкций - скрубберах, башнях орошения, барботажных пылеуловителях.
Электрическая очистка газов
Электрическая очистка газов основана на ионизации молекул газа и сообщении частицам пыли электрического заряда. Электрически заряженные частицы под действием электрического поля осаждаются на противоположно заряженном электроде, теряют свой заряд и удаляются из газового потока. Ионизация газа возникает в газе, помещенном между электродами, соединенными с источником постоянного тока высокого напряжения. Для электрической очистки газов используется коронный заряд, возникающий в неоднородном электрическом поле, обеспечивающем прохождение тока между электродами, но не вызывающего между ними дугового электрического разряда - пробоя.
Промышленный трубчатый электрофильтр.
![]() |
1) Осадительный трубчатый элемент
2) Коронирующие электроды
3) Рама для подвешивания электродов
4) Встряхивающее устройство
5) Высоковольтные изоляторы
Внутри каждого трубчатого элемента точно по центру подвешивается выполненный из коррозионно-стойкого материала коронирующий электрод 2, укрепленный на конструкции 3 и изоляторах 5. Для удаления пыли и очистки коронирующего электрода 2 имеется встряхивающее устройство 4. Запыленный газ поступает в нижнюю часть фильтра и затем подается в трубчатые элементы, где происходит ионизация. Частицы пыли получают электрический заряд и направляются к осадительному трубчатому элементу. На заземленном трубчатом элементе частицы теряют заряд и оседают, а затем ссыпаются в нижний бункер аппарата и удаляются из него через пылевые затворы.
Электрическая очистка жидких неоднородных систем
Для разделения нефтяных эмульсий, для обезвоживания и обессоливания нефти применяют электродегидратор.
По конструкции они бывают цилиндрические - вертикальные, цилиндрические - горизонтальные, шаровые.
Горизонтальный электродегидратор состоит из корпуса, двух приваренных полусферических днищ. Внутри аппарата проходит перфорированная труба. Над ней имеется пара электродов, каждый электрод подсоединён к своему трансформатору. И проводник проходит через фарфоровый изолятор. В
<== предыдущая лекция | | | следующая лекция ==> |
Болезни, вызываемые воздействием производственного шума (шумовая болезнь) | | | Квалификация преступлений при конкуренции уголовно-правовых норм. |
Дата добавления: 2021-06-28; просмотров: 167;