Железоуглеродистые сплавы
ОСНОВНЫЕ МЕТАЛЛИЧЕСКИЕ СПЛАВЫ, ИСПОЛЬЗУЕМЫЕ В ПРОИЗВОДСТВЕ
Железоуглеродистые сплавы
Компоненты и фазы в сплавах железа с углеродом.
Железо (Fe) имеет Тпл= 1539 °С и две полиморфные модификации: α-железо (Feα) с ОЦК-решеткой существует при температурах до 911 °С и выше 1392 °С, γ-железо (Feγ) с ГЦК-решеткой существует в интервале температур 911 – 1392 °С. При температуре 911 °С железо претерпевает полиморфное превращение: Feα→ Feγ. При 768 °С изменяются магнитные свойства железа (точка Кюри): до 768 °С железо ферромагнитно, выше – парамагнитно.
Углерод (С) имеет Тпл= 3500 °C – неметалл, существует в виде двух кристаллических модификаций: графита со слоистой гексагональной решеткой и алмаза с метастабильной кубической решeткой.
Железо с углеродом образует следующие фазы: твердые растворы внедрения на основе Feα и Feγ, а также химическое соединение – Fe3C.
Феррит (Ф) – твердый раствор углерода в α-железе с предельной растворимостью углерода 0,02 %. Выше 1392 °С существует высокотемпературная модификация феррита. Свойства феррита близки к свойствам железа. Он мягкий – твердость 80 НВ, и пластичный – δ = 30 %.
Аустенит (А) – твердый раствор углерода в γ-железе с предельной растворимостью углерода 2,14 %. Аустенит имеет твердость 200 НВ, пластичность δ = 40-50 %.
Цементит (Ц) – химическое соединение железа с углеродом (карбид железа Fe3C) содержит 6,69 % углерода. Имеет ромбическую решетку. Температура плавления 1252 °С. Цементит – метастабильная фаза: при нагреве до 1200 °С разлагается на железо и углерод. Цементит твердый (800 НВ), но не пластичный.
Диаграмма состояния железо – углерод.На диаграмме состояния железо – углерод рассматриваются процессы кристаллизации железоуглеродистых сплавов (стали и чугуна) и превращения в их структурах при медленном охлаждении до комнатной температуры. Диаграмма (рис. 3.1) показывает фазовый состав и структуру сплавов с концентрацией от чистого железа до цементита (6,67 %С).
Рис. 3.1. Диаграмма состояния железо-углерод:
Ж - жидкий раствор;
А – аустенит;
Ц – цементит (Fe3С);
Ф – феррит;
П – перлит (эвтектоидная смесь феррита и цементита);
Л – ледебурит (эвтектическая смесь аустенита и цементита, ниже линии PSK – смесь перлита и цементита)
Затвердевание жидкого сплава начинается при температурах, соответствующих линии ликвидуса ACD. Линия солидуса AECF соответствует температурам конца затвердевания. При температурах, соответствующих линии АС, из жидкого сплава кристаллизуется аустенит, а линии CD – цементит, называемый первичным цементитом. В точке С при 1147 °С и содержании углерода 4,3 % из жидкого сплава одновременно кристаллизуется аустенит и первичный цементит, образуя эвтектику – ледебурит. При температурах, соответствующих линии солидуса АЕ, сплавы с содержанием углерода до 2,14 % окончательно затвердевают с образованием аустенита. На линии ECF (линия эвтектического превращения) сплавы с содержанием углерода от 2,14 до 6,67 % окончательно затвердевают с образованием эвтектики (ледебурита) и структур, образовавшихся ранее из жидкого состояния, а именно: в интервале 2,14-4,3 % С – аустенита, а в интервале 4,3-6,67 % С – первичного цементита.
При дальнейшем охлаждении сплавов при температурах, соответствующих линиям GSE, PSK и GPQ происходят превращения в твердом состоянии. Превращения в твердом состоянии происходят вследствие полиморфного превращения γ-Fe в α-Fe и в связи с понижением растворимости углерода в аустените и феррите. С понижением температуры избыток углерода выделяется из твердого раствора в виде цементита.
В области диаграммы AGSE находится аустенит. При охлаждении сплавов до температур, соответствующих линии GS, аустенитраспадается с выделением феррита. А при температуре ниже линии SE из аустенита выделяется вторичный цементит. В области диаграммы GSP находится смесь феррита и аустенита. Ниже линии GP существует только феррит. При дальнейшем охлаждении до температур, соответствующих линии PQ, из феррита выделяется цементит (третичный).
В точке S при температуре 727°С и содержании 0,8 % С весь аустенит распадается и превращается в механическую смесь феррита и цементита – перлит. В любом сплаве системы при температурах, соответствующих линии PSK (линия эвтектоидного превращения), происходит распад оставшегося аустенита с образованием перлита.
Таким образом, при комнатной температуре все сплавы железа с углеродом состоят только из двух фаз: феррита и цементита.Кроме того, при концентрации углерода более 0,02 %, во всех сплавах присутствует структурная составляющая перлит.
На диаграмме состояния железо–углерод сплавы, находящиеся левее точки Е (менее 2,14 % С), называются сталями. Сплавы, находящиеся правее точки Е (от 2,14 % до 6,67 % С), называются чугунами.
Стали, описываемые диаграммой состояния железо-углерод, называются углеродистыми сталями. Они содержат до 2 % углерода, а также примеси (Si, Mn, S, P). По структуре в равновесном состоянии они классифицируются на: доэвтектоидную сталь, содержащую от 0,02 до 0,8 % С; эвтектоидную сталь, содержащую 0,8 % С; заэвтектоидную сталь, содержащую более 0,8 % С. Сплав, содержащий до 0,02 % С, называется техническим железом (рис. 3.2).
Рис. 3.2. Микроструктура технического железа (а), эвтектоидной стали с пластинчатым перлитом (б) (×400)
Рис. 3.3. Микроструктура доэвтектоидной стали содержанием углерода: а – 0,1 %; б –0,3 % (×250)
В стали может быть четыре типа структур. Первый тип структуры − феррит и третичный цементит − наблюдается в техническом железе. При рассмотрении в микроскоп феррит наблюдается в виде светлых зерен неодинаковой яркости (рис. 3.2, а). Третичный цементит выделен внутри зерен феррита в виде мельчайших частиц. Второй тип структуры − перлит − наблюдается в эвтектоидной стали. Перлит в большинстве случаев имеет пластинчатое строение (рис. 3.2, б).
Третий тип структуры – феррит и перлит − наблюдается в доэвтектоидных сталях. По мере увеличения концентрации углерода в доэвтектоидной стали, количество зерен феррита убывает, а количество зерен перлита увеличивается (рис. 3.3).
Четвертый тип структуры − вторичный цементит и перлит − наблюдается в заэвтектоидной стали. На шлифе цементит выглядит, как светлая неразрывная сетка, разделяющая пластинчатые участки перлита (рис. 3.4).
Рис. 3.4. Микроструктура заэвтектоидной стали (×300)
Чугуны, описываемые диаграммой состояния железо-углерод, называются белыми чугунами. Они содержат от 2,14 до 6,67 % углерода, а так же большее, чем в стали, количество примесей (Si, Mn, S, P). Согласно диаграмме, существует три разновидности белых чугунов: доэвтектический– 2,14-4,3 % С; эвтектический – 4,3 % С; заэвтектический– более 4,3 % С.
Доэвтектический чугун имеет структуру перлит, ледебурит и вторичный цементит, эвтектический – ледебурит и заэвтектический – ледебурит и первичный цементит (рис. 3.5).
Рис. 3.5. Микроструктура белых чугунов: а – доэвтектического;
б – эвтектического; в – заэвтектического (×500)
Классификация и применение сталей. Стали являются самым востребованным техническим материалом. Это обусловлено очень широким спектром их механических и эксплуатационных свойств, что достигается за счет легирования и операций внешних воздействий (термообработка и т.п.).
Стали классифицируются по различным признакам. По химическому составу они подразделяются на углеродистые и легированные. По структуре в равновесном состоянии углеродистые и легированные стали подразделяются на доэвтектоидные, эвтектоидные и заэвтектоидные. По структуре после охлаждения на воздухе легированные стали подразделяются на перлитные (ферритоперлитные), мартенситные и аустенитные. По качеству стали разделяют на стали: обыкновенного качества (массовое содержание вредных примесей – серы и фосфора – не более 0,04 % и 0,05 % соответственно); качественные (не более 0,035 % P и 0,004 % S); высококачественные стали (не более 0,025 % каждой примеси); особо высококачественные стали (не более 0,025 % P и 0,015 % S). Также существуют другие классификации: по способу выплавки, способу разливки и т.д.
Остановимся более подробно на классификации стали по назначению – стали общего назначения, конструкционные, инструментальные, специальные.
Стали общего назначения всегда углеродистые обыкновенного качества. Применяются для производства машин, станков, строительных металлоконструкций, предметов широкого потребления. Стали обыкновенного качества обозначают буквами “Ст” и цифрами от 0 до 6, например Ст.2кп., Ст.3кп, Ст.3пс. Буквы “Ст” обозначают “сталь”, цифры от 0 до 6 – условный номер марки стали в зависимостиот химического состава. Индексами указывается степень раскисления: кп – кипящая, пс – полуспокойная, сп – спокойная.
Конструкционные стали применяются для изготовления деталей машин и механизмов (зубчатые колеса, штоки, валы, маховики и т.д.). В основном, это качественные углеродистые и низколегированные стали. Конструкционные качественные углеродистые стали маркируются двухзначным числом, указывающим содержание углерода в сотых долях процента. Например: сталь 20 (0,2 % С), сталь 45 (0,45 % С), сталь 60 (0,6 % С). В легированных конструкционных сталях, легирующие элементы в марке стали указывается буквой и последующей цифрой, обозначающей примерное содержание данного легирующего элемента в процентах. Легирующие элементы имеют условные обозначения буквами русского алфавита (Х – хром, Н – никель, М – молибден, В – вольфрам, К – кобальт, Т – титан, А – азот, Г – марганец, Д – медь, Ф – ванадий, С – кремний, П – фосфор, Р – бор, Б – ниобий, Ц – цирконий, Ю – алюминий). Например: сталь 40Х (0,4 % С; ~ 1 % Cr), сталь 20Г (0,2 % С; ~ 1 % Mn), сталь 30ХНМА (0,3 % С; ~ 1 % Cr; ~ 1 % Ni; ~ 1 % Mо; А в конце марки обозначает сталь высокого качества).
Инструментальные стали используют для производства режущего, измерительного и штампового инструмента. Инструментальные стали всегда качественные и высококачественные. Они могут быль как углеродистыми, так и легированными. Инструментальные качественные углеродистые стали маркируются буквой У (углеродистая инструментальная сталь) и числом, указывающим содержание углерода в десятых долях процента. Например: сталь У8 (0,8 % С), сталь У13 (1,3 % С). Низколегированные инструментальные стали маркируются так же, как конструкционные, но содержание углерода дается в десятых долях процента. Если первая цифра в марке отсутствует, то содержание углерода превышает 1 %. Это стали 9ХС, ХВГ, ХВ5. Быстрорежущие стали маркируются буквой Р. Последующее число показывает содержание вольфрама в процентах. Так как содержание в быстрорежущих сталях углерода ~ 1 %, а хрома ~ 4 %, они не указываются в марке. Остальные элементы обозначаются как во всех легированных сталях. Например: стали Р18, Р6М5, Р6М5Ф2К8.
К специальным сталям относятся стали, разработанные для особых условий эксплуатации: при повышенной и пониженной температуре, в агрессивной среде. Это всегда высококачественные и особо высококачественные высоколегированные стали. К ним относятся жаростойкие и жаропрочные стали, нержавеющие и кислостойкие стали, криогенные стали и многие другие.
Классификация и применение чугунов. Как описывалось выше, чугун – это железоуглеродистый сплав с содержанием углерода >2,14 %. Кроме того, в чугуне содержатся примеси: кремний, марганец, сера, фосфор и др. С целью улучшения свойств в чугуны могут вводиться легирующие элементы, такие как хром, никель, медь и др.
Чугун, по сравнению со сталью, имеет как преимущества, так и недостатки. Положительными свойствами этого материала являются: хорошие литейные свойства, хорошая обрабатываемость резанием, достаточно высокая работоспособность в условиях трения, способность гасить вибрации, небольшая стоимость. Недостатком чугуна являются его низкие пластические свойства и ударная вязкость, что препятствует использованию чугуна для изготовления деталей, работающих при значительных динамических, ударных нагрузках, и делает невозможным в большинстве случаев использование обработки давлением для изготовления чугунных изделий.
По структуре различают чугуны, в которых углерод находится в виде химического соединения с железом Fe3С – цементита, и чугуны, в которых углерод, в основном, находится в свободном состоянии, в виде графита. Первая разновидность чугуна называется белым чугуном (его строение описано выше).
Получают белый чугун при ускоренном охлаждении в процессе отливки деталей, заготовок. Способствует также получению этой разновидности чугуна повышенное содержание в нем хрома, марганца. Структура белого чугуна определяет его механические свойства: это твердый хрупкий материал. Вследствие низкой пластичности, белый чугун применяется очень редко, в основном, для изделий, работающих в условиях абразивного и гидроабразивного износа, когда его повышенная хрупкость не играет решающей роли.
В ряде случаев изготавливают детали с так называемой отбеленной поверхностью. Их поверхностный слой представляет собой белый чугун и имеет повышенную твердость и износостойкость, а сердцевина имеет структуру другой разновидности чугуна (с наличием графита), что обеспечивает необходимый комплекс механических свойств. Примерами таких изделий с отбеленной поверхностью являются валки холодной прокатки, шары шаровых мельниц.
Чугуны, в которых углерод находится в свободном виде, классифицируют по форме графитовых включений: серый чугун – в нем содержится графит в виде пластинчатых включений; ковкий чугун с хлопьевидными включениями графита; высокопрочный чугун в котором графит имеет шаровидную форму. Металлическая основа этих чугунов может быть перлитной, ферритной или ферритоперлитной (рис.3.6).
|
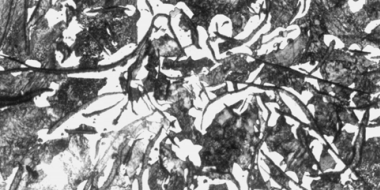
|
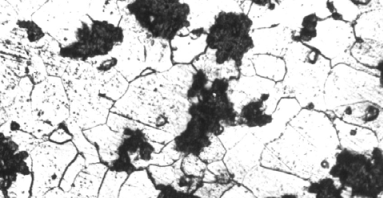
|
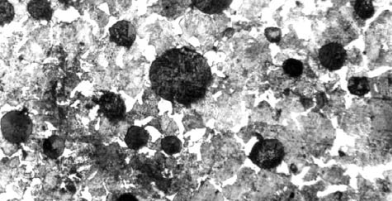
Рис. 3.6. Структура чугунов: а – серый чугун с ферритоперлитной основой; б – ковкий чугун с ферритной основой; в – высокопрочный чугун с феррито-перлитной основой (×300)
Графитовые включения в чугуне снижают его механические свойства, особенно пластичность. Чем менее разветвленную форму они имеют, тем меньше их отрицательное влияние. Это связано с тем, что графитовые включения, играя роль трещин и пустот в чугуне, являются концентраторами напряжений. Чем компактнее форма включений, тем ниже концентрация напряжений и тем меньше снижение механических свойств металла за счет графита.
Серый чугун получают при медленном охлаждении металла при литье изделий, а также при повышенном содержании кремния, углерода. Обозначается он буквами СЧ, после которых ставится цифра, показывающая предел прочности при растяжении σвв кг/мм2. Например, СЧ12 (σв = 12 кг/мм2). Применяется серый чугун для изготовления слабонагруженных деталей, работающих в легких условиях.Например, корпуса редукторов, насосов, электродвигателей, различные крышки, отопительные батареи и т.п.
Ковкий чугун получают из белого чугуна путем специального отжига. Это длительная термическая обработка, при которой белый чугун медленно нагревается до температур 950-1000 °С и после определенной выдержки медленно охлаждается. При таком отжиге происходит графитизация цементита белого чугуна с образованием хлопьевидных включений графита. Обозначается ковкий чугун буквами КЧ, после которых следуют цифры, показывающие предел прочности при растяжении σвв кг/мм2 – первая цифра, и относительное удлинение δ в % – вторая цифра. Например, КЧ 30-6 (σв = 30 кг/мм2, δ = 6 %). Применяется этот чугун для изготовления деталей, работающих в более тяжелых условиях по сравнению с деталями из серого чугуна, - при повышенных нагрузках, при знакопеременных и небольших ударных нагрузках. Например, картеры редукторов, коробок передач автомобилей, кронштейны рессор, различные крюки, фланцы и т.п.
Высокопрочный чугун получают путем модифицирования его при выплавке магнием или церием в количестве 0,05 %. Модификаторы способствуют формированию шаровидных включений графита. Обозначаются высокопрочные чугуны буквами ВЧ и цифрой, показывающей предел прочности при растяжении σв. Например, ВЧ 40 (σв = 40 кг/мм2). Применяется высокопрочный чугун для изготовления ответственных деталей, работающих в довольно сложных условиях при повышенномнагружении. Например, коленчатые и распределительные валы легковых автомобилей, прокатные валки, корпуса турбин, детали кузнечно-прессового оборудования и др.
Представляет интерес использование чугунов для деталей, работающих в специфических условиях (агрессивные среды, высокие температуры и др.). Для этого в чугуны вводят легирующие элементы, способствующие повышению необходимых свойств. Такие чугуны называют легированными или чугунами специального назначения. Они дешевле легированных сталей и, вследствие лучших литейных свойств, оказываются предпочтительнее для получения отливок.
Цветные сплавы
Наиболее широко применяемыми цветными металлами являются медь, алюминий, магний, титан, олово, свинец, никель. Мировое производство цветных металлов, в том числе и редких (тантала, германия, ниобия и др.), непрерывно возрастает. Эти металлы обладают особо ценными свойствами и поэтому, несмотря на относительно высокую стоимость, их широко используют в промышленности. Особенно перспективны материалы, которые дают возможность снизить массу конструкций при повышении их прочности и жесткости. Высокая коррозионная стойкость цветных металлов обусловлена образованием на поверхности металла пленки оксида. Эта пленка обладает хорошим сцеплением с металлом благодаря близости их удельных объемов и предохраняет металл от дальнейшей коррозии.
Цветные металлы применяются в электротехнической промышленности, авиации, радиоэлектронной промышленности. В качестве конструкционных материалов цветные металлы применяются, главным образом, в виде сплавов. В тех случаях, когда это возможно, цветные металлы заменяют черными или неметаллическими материалами – пластмассой, керамикой и т. д.
Алюминий и его сплавы.Одним из наиболее легких конструкционных материалов является алюминий. Его плотность 2,7 г/см3, температура плавления 658 °С. Алюминий имеет кубическую гранецентрированную решетку без полиморфных превращений. В отожженном состоянии алюминий обладает малой прочностью (σв= 80-120 МПа) и твердостью (25 НВ), но большой пластичностью (δ = 35-45 %). Отличается высокой коррозионной стойкостью в пресной воде и атмосфере.
Алюминий получают из руд, содержащих оксиды алюминия. Маркируется алюминий буквой А и числом, зависящем от количества примесей. Например, А999, А995, А97, А95, А85, А5.
Благодаря высокой пластичности и электропроводности алюминий широко применяют в электротехнической промышленности для изготовления проводов, кабелей; в авиационной промышленности – труб, маслопроводов и бензопроводов; в легкой и пищевой промышленности – фольги, посуды. Алюминий используют как раскислитель при производстве стали. Ввиду низкой прочности и незначительной упрочняемости при пластической деформации в холодном состоянии технически чистый алюминий как конструкционный материал применяют сравнительно редко.
В результате сплавления алюминия с магнием, медью, цинком и другими металлами получены сплавы с достаточно высокой прочностью, малой плотностью и хорошими технологическими свойствами. Различают литейные и деформируемые алюминиевые сплавы.
Литейные сплавы алюминия маркируются буквами АК и числом, показывающим условный номер сплава. Чтобы сплав обладал хорошими литейными свойствами, он должен иметь узкий температурный интервал кристаллизации. Кроме того, желательно, чтобы он имел низкую температуру плавления. Этим требованиям удовлетворяют эвтектические сплавы. Наибольшее распространение получили сплавы алюминия с кремнием, образующие эвтектику при содержании 11,6 % кремния. Эти сплавы называются силуминами.
Широко применяется силумин эвтектического состава АК12, содержащий 10-12 % кремния и модифицированный добавками малого количества натрия 0,5-0,8 % (рис. 3.7а).
Модифицированный силумин имеет очень хорошие литейные свойства, но малую прочность (σв = 180 МПа). Термической обработкой этот силумин не упрочняется. Уменьшение содержания кремния и добавка небольшого количества магния и марганца (АК9) ухудшает литейные свойства силуминов, но улучшает механические. Эти сплавы являются дисперсионно твердеющими и упрочняются закалкой и старением (рис. 3.7б).
Рис. 3.7. Диаграмма состояния системы Al–Si (а) и микроструктура силумина (×400) (б).
Кроме силуминов, используются литейные сплавы алюминия с медью (АМ5) и магнием (АМг10). Они обладают значительно большей прочностью, чем силумины, но их литейные свойства хуже.
Деформируемые сплавы алюминия применяются для изготовления проволоки, фасонных профилей и различных деталей, получаемых ковкой, штамповкой или прессованием. Эти сплавы делят на упрочняемые и не упрочняемые термообработкой.
К неупрочняемым относят сплавы алюминия с марганцем и магнием. Они обладают высокой коррозионной стойкостью, умеренной прочностью, высокой пластичностью, хорошо свариваются. Их применяют для изделий, эксплуатируемых в агрессивной среде, а такжеизготавливаемых путем глубокой штамповки: рам и кузовов, перегородок зданий, переборок судов, бензиновых баков и т. п.
Деформируемые сплавы, упрочняемые термообработкой, имеют наибольшую плотность (3 г/см3) и высокую прочность (σвдо 700 МПа). Их применяют для изготовления ответственных деталей. Наиболее распространенным сплавом этой группы является дуралюмин. Дуралюмин маркируют буквой Д и порядковым номером: Д1, Д16, Д18. Основным компонентом, упрочняющим дуралюмин, является медь (до 5 %), в качестве дополнительных легирующих элементов используют магний (до 1 %), марганец (до 2 %), титан и др. Медь и магний способствуют дисперсионному твердению сплава при термообработке за счет выделения дисперсных частиц CuAl2 и Al3Mg2. Марганец усиливает упрочнение и повышает коррозионную стойкость.
Термообработка дуралюмина заключается в закалке и старении. В результате термической обработки прочность дуралюмина повышается в два раза (для дуралюмина Д1 с 200-240 МПа до 450-500 МПа), а пластичность практически не меняется.
Достоинством дуралюмина является высокая удельная прочность (отношение предела прочности к плотности), что особенно важно в самолетостроении. Например, из сплава марки Д16 делают обшивку и лонжероны самолетов, кузова автомашин и т. д.
Титан и его сплавы.Титан – металл серебристо-белого цвета, плотностью 4,5 г/см3 и температурой плавления 1670 °С. Ниже температуры 882 °С существует α-титан, имеющий гексагональную плотноупакованную решетку. При 882 °С происходит полиморфное превращение, и выше этой температуры существует β-титан, имеющий объемно-центрированную кубическую кристаллическую решетку.
Главное преимущество титана и его сплавов состоит в сочетании высоких механических свойств с коррозионной стойкостью в агрессивных средах (в азотной, соляной и фтористой кислотах) и относительно низкой плотностью. Прочность титана σв– 300-500 МПа, относительное удлинение δ = 20-30 %. Чем больше в титане примесей, тем он прочнее и менее пластичен. Технически чистый титан марок ВТ1-00 содержит не более 0,4 % примесей, ВТ1-0 не более 0,55 % примесей. Высокая коррозионная стойкость титана достигается за счет образования на его поверхности плотной оксидной пленки. Главные недостатки титана – высокая стоимость, низкая износостойкость, склонность к взаимодействию с газами при температурах выше 500-600 °С. Технический титан хорошо обрабатывается давлением, сваривается (в среде аргона), но обработка его резанием затруднена.
Главная цель легирования титана – повышение механических свойств. Такие легирующие элементы, как Al, Fe, Mn, Cr, Sn, V, повышают прочность титана (рис. 3.8), несколько снижая при этом пластичность и вязкость. Al, Zr, Mo, Sn увеличивают жаропрочность. Mo, Zr, Nb, Та повышают коррозийную стойкость.
По влиянию на температуру полиморфного превращения все легирующие элементы в титановых сплавах делятся на α-стабилизаторы, β-стабилизаторы и нейтральные. К α-стабилизаторам, повышающим температуру полиморфного превращения, относятся алюминий, кислород и водород. В качестве легирующего элемента используется только алюминий. β-стабилизаторы (Мо, V, Mn, Fe, Cr и др.) снижают температуру полиморфного превращения и расширяют область существования β-титана. Нейтральные легирующие элементы (Sn, Zr) почти не влияют на температуру полиморфного превращения.
Рис. 3.8. Зависимость предела прочности титанового сплава от содержащихся основных лигирующих элементов
По структуре после отжига титановые сплавы делятся на α-сплавы, псевдо-α-сплавы, (α+β)-сплавы, псевдо-β-сплавы и β-сплавы. Псевдо-α-сплавы содержат очень небольшое количество (до 5 %) β-фазы, а псевдо-β-сплавы очень небольшое количество α-фазы. Двухфазные (α+β)-сплавы и псевдо-β-сплавы способны к упрочению путем закалки и искусственного старения. После закалки, в зависимости от содержания β-стабилизаторов, может образоваться мартенсит (пересыщенная α-фаза) и неустойчивая β-фаза. Мартенсит в титановых сплавах не обладает повышенной прочностью по сравнению с равновесной α-фазой.
Упрочение происходит при искусственном старении за счет выделения мелкодисперсных частиц α-фазы при распаде мартенсита β-фазы. В зависимости от химического состава закалка производится от 700-900 °С, а старение – при 420-600 °С.
По технологическому признаку титановые сплавы классифицируются на деформируемые, литейные и порошковые. По свойствам титановые сплавы делятся на высокопластичные, сплавынормальной прочности, высокопрочные, жаропрочные, коррозионностойкие.
Деформируемые сплавы. К α-сплавам относятся технический титан ВТ1-00 и ВТ1-0, сплавы марок ВТ5 (5 % А1) и ВТ5-1 (5% А1 и 2,5 % Sn) и др. Эти сплавы не упрочняются термической обработкой и применяются в отожженном состоянии (рис. 3.9). Они характеризуются хорошей свариваемостью, высокими механическими свойствами при криогенных температурах.
Рис. 3.9. Диаграмма состояния системы Ti–Al
Псевдо-α-сплавы сохраняют достоинства α-сплавов, но за счет наличия небольшого количества β-фазы имеют более высокую пластичность. Поэтому они хорошо обрабатываются давлением как в горячем, так и в холодном состоянии. Кроме алюминия, псевдо-α-сплавы легируются небольшим количеством β-стабилизаторов. К этим сплавам относятся ОТ4 (3,5 % А1, 1,5 % Мn), ОТ4-1 (1,5 % А1, 1 % Мn), ВТ4 (5 % А1, 1,5 % Мn).
Двухфазные (α+β)-сплавы легируются одновременно алюминием и β-стабилизаторами. К ним относятся высокопрочные сплавы марок ВТ6 (6 % А1, 4,5 % V), ВТ14 (4,5 % А1, 3 % Мо, 1 % V), ВТ16 (2,5 % А1, 5 % Мо, 5 % V), жаропрочные сплавы ВТЗ-1 (6 % А1, 2,5 % Мо, 2 % Сr, 0,3 % Si, 0,5 % Fe), BT8, ВТ9 и др. Эти сплавы упрочняются закалкой и старением (рис. 3.10). При этом чем больше содержание β-фазы, тем сильнее выражен упрочняющий эффект.
Рис. 3.10. Микроструктура титанового сплава ВТ6 после закалки (×400
)
Псевдо-β-сплавы содержат небольшое количество α-стабилизатора и большое количество β-стабилизаторов (до 20 % ). Они подвергаются закалке и старению, после чего их прочность доходит до σв= 1300-1700 МПa, что является наибольшим значением для титановых сплавов. Наибольшее распространением из этой группы получил сплав ВТ15 (3 % А1, 7 % Мо, 11 % Сr).
Однофазные β-сплавы большого применения не получили, так как для получения β-структуры требуется вводить очень большое количество дорогих β-стабилизаторов. Например, сплав марки 4201, содержит 33 % молибдена. Он характеризуется исключительной коррозионной стойкостью и может заменить тантал, сплавы на никелевой основе, благородные металлы.
Литейные сплавы титана по составу аналогичны деформируемым. В конце марки они имеют букву Л. Пo структуре они относятся к α-сплавам (ВТ1Л, ВТ5Л) или (α+β)-сплавам с небольшим количеством β-фазы (ВТЗ-1Л, ВТ14Л). Литейные титановые сплавы имеют меньшую прочность и пластичность, чем деформируемые. Упрочняющая термическая обработка для них не применяется, так как при этом резко снижается пластичность.
Область применения титановых сплавов очень велика: в авиации (обшивка самолетов, диски, лопатки компрессоров и т. д.); в ракетной технике (корпуса двигателей, баллоны для сжатых и сжиженных газов); в химическом машиностроении (оборудование, находящееся в среде хлора и его растворов, детали, работающие в азотной кислоте, теплообменники); в судостроении (обшивка морских судов, поэтому эти суда не требуют окраски); в энергомашиностроении (диски, лопатки стационарных турбин); в криогенной технике. В автомобильной отрасли применяемые титановые сплавы позволяют уменьшить массу автомобильных и дизельных двигателей, увеличить их частоту вращения и мощность.
Медь и ее сплавы.Чистая медь имеет розовато-красный цвет, плотность ее 8,93 г/см3, температура плавления 1083 °С. В отожженном состоянии σв= 250 МПа, δ = 45-60 %, твердость 60 НВ. Кристаллизуется в кубической гранецентрированной решетке и полиморфных превращений не имеет. Благодаря высокой электропроводности около половины всей произведенной меди используют в электро- и радиотехнической промышленности для изготовления проводников, монтажных и обмоточных проводов, токопроводящих деталей приборов, аппаратов, в электровакуумной технике. Как конструкционный материал медь неиспользуется из-за высокой стоимости и низких механических свойств. Маркируется буквой М и цифрами, зависящими от содержания примесей. Медь марок М00 (0,01 % примесей), М0 (0,05 %) и М1 (0,1 %) используется для изготовления проводников электрического тока, медь М2 (0,3 % ) – для производства высококачественных сплавов меди, МЗ (0,5 % ) – для сплавов обыкновенного качества. Широкое использование в промышленности имеют сплавы меди с другими элементами – латуни и бронзы.
Латуни. Сплав меди с цинком называется латунью. Механические свойства латуни – прочность и пластичность – выше, чем меди, она хорошо обрабатывается резанием, давлением, характеризуется высокими коррозионной стойкостью, теплопроводностью, электропроводностью (рис. 3.11).
Рис. 3.11. Диаграмма состояния системы Cu–Zn (а) и зависимость механических свойств латуни от содержания цинка (б)
Большим преимуществом латуней является сравнительно низкая их стоимость, так как входящий в состав сплава цинк значительно дешевле меди. Максимальную прочность имеет латунь, содержащая 45 % цинка (σв= 350 МПа), а максимальную пластичность – латунь, содержащая 32 % цинка (δ = 55 %). При увеличении содержания цинка выше 39 % резко падает пластичность, а выше 45 % – и прочность. Поэтому латуни, содержащие более 45 % цинка, не применяются. Подобное изменение свойств связано со структурой латуней. Медь и цинк образуют целый ряд твердых растворов.
При содержании цинка до 39 % латунь является однофазной и структура её представляет собой α-твёрдый раствор цинка в меди с гранецентрированной кубической решеткой (α-латунь). При большем содержании цинка латунь является двухфазной: в её структуре появляется хрупкая β-фаза, представляющая собой твёрдый раствор на базе соединения Сu и Zn с объемно-центрированной кубической решеткой (α+β латунь) (рис. 3.12).
Рис. 3.12. Микроструктура двухфазной латуни ЛМцСКА
При содержании цинка более 45 % структура латуни состоит только из β-фазы.
По химическому составу различают простую (двойную) латунь, в которой содержатся только медь и цинк, и сложную (специальную), в которой кроме цинка содержатся легирующие элементы: никель, свинец, олово, кремний и др. Специальная латунь отличается повышенной прочностью, лучшими антикоррозионными и технологическими свойствами. По технологическому признаку латуни делятся на литейные и деформируемые (обрабатываемые давлением).
Латуни маркируются буквой Л. В деформируемых латунях указывается содержание меди и легирующих элементов, которые обозначаются соответствующими буквами (О – олово, А – алюминий, К – кремний, Н – никель, Мц – марганец, Ж – железо, С – свинец). Содержание элементов дается в процентах после всех буквенных обозначений. Например, латунь Л63 содержит 63 % меди и 37 % цинка. Латунь ЛАЖ 60-1-1 содержит 60 % меди, 1 % алюминия, 1 % железа и 38 % цинка. В марках литейных латуней указывается содержание цинка, а количество легирующих элементов (в %) ставится после букв, их обозначающих. Например, литейная латунь ЛЦ40Мц3А содержит 40 % цинка, 3 % марганца, менее 1 % алюминия и 56 % меди. Простые латуни выпускают следующих марок: Л96, Л90, Л85, Л70, Л68, Л63, Л60. Все они являются деформируемыми, а по структуре однофазными (кроме Л60). Наибольшее применение имеют латуни, содержащие 90, 80, 70 и 68 % меди.
Бронзы. Сплав меди с оловом, алюминием, свинцом и другими элементами, среди которых цинк и никель не являются основными, называют бронзой. По основному легирующему элементу бронзы делятся на оловянные, алюминиевые, кремнистые, бериллиевые, свинцовые и др. Бронзы обладают хорошими литейными свойствами, хорошо обрабатываются давлением и резанием. Большинство бронз отличаются высокой коррозионной стойкостью и, кроме того, широко используются как антифрикционные сплавы.
По технологическому признаку бронзы делят на деформируемые и литейные. Маркируются бронзы буквами Бр, за которыми показывается содержание легирующих элементов в %. Обозначения легирующих элементов и отличия в марках деформируемых и литейных сплавов у бронз такие же, как у латуней. Например, деформируемая бронза БрОФ 6,5-0,4 содержит 6,5 % олова и 0,4 % фосфора, а литейная бронза БрОЗЦ7С5Н – 3 % олова, 7 % цинка, 5 % свинца, менее 1 % никеля.
Особенно широкое применение в машиностроении имеют оловянные бронзы (рис. 3.13).
Рис. 3.13. Диаграмма состояния системы Cu–Sn (а) и зависимость механических свойств бронзы от содержания олова (б)
Они обладают высокими механическими (σв= 150-350 МПа; δ = 3-15%; 60-90 НВ) и антифрикционными свойствами, коррозионной стойкостью, хорошо отливаются и обрабатываются резанием. По структуре оловянные бронзы, подобно латуням, бывают однофазными и двухфазными. Обычно вторая фаза выделяется при содержании олова больше 7-9 % (рис. 3.14).
Однофазные оловянные бронзы, имеющие высокую пластичность, используются в качестве деформируемых, двухфазные – в качестве литейных. Для улучшения качества в оловянную бронзу вводят свинец, повышающий антифрикционные свойства и обрабатываемость; цинк, улучшающий литейные свойства; фосфор, повышающий литейные, механические и антифрикционные свойства.
Рис. 3.14. Микроструктура двухфазной оловянной бронзы (300)
Литейные оловянные бронзы БрО5Ц5С5, БрО6Ц6С2, БрО10Ф1 и др. применяют для получения деталей машин, работающих в условиях морской и пресной воды, для изготовления антифрикционных деталей (вкладышей подшипников скольжения). Литейные оловянные бронзы имеют самую низкую усадку и наилучшую жидкотекучесть среди
<== предыдущая лекция | | | следующая лекция ==> |
Диаграммы состояния сплавов | | | ИЗМЕНЕНИЕ СТРОЕНИЯ И СВОЙСТВ МЕТАЛЛИЧЕСКИХ СПЛАВОВ ВНЕШНИМ ВОЗДЕЙСТВИЕМ |
Дата добавления: 2019-02-08; просмотров: 989;