Передачи вращательного движения
Передача – устройство, главная функция которого передача энергии на расстояние, в зависимости от способа передачи энергии, они могут быть: механические, электрические, пневматические, гидравлические. В курсе деталей машин мы будем изучать только механические передачи вращательного движения.
Механической передачей называется механизм, который преобразует параметры движения источника энергии (двигателя) при передаче исполнительным органам, в этом случае передача осуществляет согласование параметров движения двигателя и исполнительного рабочего органа.
Передачи вращательного движения по способу соединения тел вращения бывают: 1) передачи с контактом тел вращения – зубчатые, червячные, фрикционные, винтовые, 2) передачи гибкой связью – ремённые и цепные; по способу передачи движения – передачи с зацеплением (зубчатые, червячные, цепные), трением – ременные и фрикционные.
3.10.1. Кинематические и силовые параметры передач
Это параметры, характеризующие вращательное движение элементов передач:
1) Частота вращения, n (об/мин), выражается через угловую скорость (рад/с):
, (3.14)
2) Крутящий момент на валу T, Нм
3) Окружная скорость (Н) – сила вызывающая вращение тел или сопротивление вращению и направленная по касательной к траектории точки ее приложения.
, (3.15)
4) Мощность на валу, Р, Вт:
; (3.16)
. (3.17)
3.10.2. Передаточное отношение и КПД механизма
Отношение угловых скоростей ведущих и ведомых тел называется передаточным отношением.
. (3.18)
Для одноступенчатого редуктора:
, (3.19)
Передаточное отношение привода состоящего из нескольких передач, расположенных последовательно, равно произведению передаточных чисел всех его передач.
, (3.20)
где n – число передач, входящих в привод.
КПД привода равен отношению мощности на ведомом и ведущем валах:
, (3.21)
В общем случае КПД привода состоящего из нескольких передач равен произведению КПД передач входящих в привод:
. (3.22)
3.10.3. Ременные и цепные передачи
Передача вращения посредством ремня, надетого на шкивы, называется ременной передачей (Рис. 3.18).
Рис. 3.18. Ременные передачи
Ременные передачи применяют преимущественно в тех случаях, когда по условиям конструкции валы расположены на значительных расстояниях или высокие скорости не позволяют применять другие виды передач.
Ременные передачи бывают: По форме поперечного сечения ремня: плоскоременные (а), клиноременные (б), круглоременные (г) а также передачи с зубчатыми ремнями (в, д, е) (Рис. 3.19).
а) б)
в г
д е
Рис. 3.19. Формы поперечного сечения ремней
Плоскоременные передачи более простые по конструкции, однако, клиноременные обладают большей нагрузочной способностью.
Ременные передачи по расположению осей валов подразделяются:
1) Открытыми с параллельно расположенными осями валов и вращением шкивов в одном направлении, 2) перекрестные, с параллельными осями валов и вращением шкивов в противоположных направлениях, 3) полуперекрестные со скрещивающими осями валов, 4) угловые со скрещивающимися или пересекающимися осями валов.
По способу натяжения ремня: с периодическим натяжением (перемещением опоры шкива); с автоматическим натяжением (натяжным роликам).
Преимущества ременных передач: 1) возможность больших межосевых расстояний, 2) плавность работы, гашение ударов за счет эластичности ремня и возможности проскальзывания, 3) простота конструкции и эксплуатации, 4) возможность передачи большого диапазона мощностей и скоростей, 5) относительно высокий КПД.
Недостатки: 1) относительно большие размеры передачи, 2) непостоянство передаточного отношения вследствие проскальзывания, 3) повышенная нагрузка на валы от натяжения ремня, 5) не долговечность ремней в среднем 2-3 тысячи часов работы.
Материал ремней: материал ремня должен обеспечивать надежность сцепления со шкивами и достаточную долговечность. Самые распространенные – резинотканевые ремни, кожаные, хлопчатобумажные цельнотканые, полимерные.
Клиновые ремни наиболее распространены и имеют трапециидальное сечение и выпускается 2-х типов: корд-шнуровые (а) и корд-тканевые (б) (Рис. 3.20). Корд шнуровые ремни более гибкие и долговечные поэтому применяются для более сложных условий работы.
а) б)
Рис. 3.20. Типы клиновых ремней
3.10.4. Расчет и проектирование ременных передач
Основными критериями работоспособности ременных передач являются: тяговая способность, определяемая силой трения между ремнем и шкивом; долговечность ремня, которая в условиях нормальной эксплуатации ограничивается разрушением от усталости (Рис. 3.21).
Геометрические параметры ременных передач: аw – межосевое расстояние передачи, d 1 и d2 – диаметры ведущего и ведомого шкивов, α1, α2 – угол обхвата ведущего и ведомого шкивов.
1) Передаточное отношение передачи:
. (3.23)
Рис. 2.21. Схема ременной передачи
С учетом скольжения ремня:
. (3.24)
где ξ(дзетта) – коэффициент скольжения ремня ξ = 0,01…0,02.
Передаточное отношение ременной передачи обычно не превышает шести;
2) Скорость ремня
. (3.25)
3) Угол обхвата меньшего шкива
. (3.26)
4) Длина ремня
. (3.27)
3.10.5. Силовые взаимодействия в ременной передаче
Окружная сила ременной передачи:
, (3.28)
где F1 – натяжение ведущей ветви,
F2 – натяжение ведомой ветви.
Р1 – мощность на ведомом шкиву,
V – скорость ремня,
кg – коэффициент динамической нагрузки.
Окружная скорость равна:
, (3.29)
Сила начального натяжения:
, (3.30)
где А – площадь поперечного сечения ремня,
σ0 - начальное напряжение в ремне.
, (3.31)
Решая совместно выражения (3.30) и (3.31) получим:
; (3.32)
. (3.33)
Уравнения (3.32, 3.33) представляют систему 2-х уравнений с тремя неизвестными, для его решения Эйлером было получено уравнение, представляющее собой зависимость между силой трения ремня о шкив и тяговой способностью передачи:
, (3.34)
где е = 2,71, f – коэффициент трения ремня о шкив, α - угол обхвата шкива ремнем.
Решая совместно уравнения (3.30) и (3.34) получим выражения:
, (3.35)
, (3.36)
. (3.37)
Формулы (3.36 и 3.37) устанавливают связь сил натяжения ветвей работающей передачи с величиной нагрузки Ft и факторами трения (f и α). Они позволяют также определить минимально необходимую величину предварительного натяжения ремня F0 , при которой еще возможна передача заданной нагрузки Ft:
Если: , (3.38)
то в передаче начнется буксование ремня.
Тяговая способность передачи характеризуется величиной максимально допустимой окружной силы Ft или полезного напряжения σF,учитывая формулы (3.34-3.36), можно сделать вывод, что допустимое по условию отсутствия буксования напряжение возрастает с увеличением напряжения от предварительного натяжения σ0:
. (3.39)
Практика показывает, что происходит значительное снижение долговечности ремня с увеличением σ0.
Силы натяжения ветвей ремня передаются на валы и опоры. Равнодействующая нагрузку можно определить по формуле:
. (3.40)
Обычно R в два, три раза больше окружной силы Ft.
Цепные передачи
Передача вращательного движения, основанная на зацеплении цепи и звездочек, называется цепной и является передачей гибкой связью.
3.11.1. Классификация цепных передач
По конструкции – втулочные, роликовые (а), зубчатые (б), фасонно – звенные (в) (Рис.3.22). Втулочные цепи могут быть одно и двух рядные, роликовые – одно, двух, трех рядные. Износостойкость роликовой цепи выше, чем втулочной. Зубчатые цепи – позволяют передавать большие нагрузки, однако имеют высокую стоимость и массу. Фасонно-звенные цепи – имеют небольшую стоимость и простую конструкцию, поэтому широко используется в с/х машиностроении.
а) б) в)
Рис.3.22. Конструкции цепей
По способу смазки цепи – периодическая смазка, капельная, картерная.
Преимущества цепных передач: 1) возможность передачи мощности на значительные расстояния, 2) постоянное передаточное число, 3) сравнительно небольшие нагрузки на валы, 4) большой диапазон передаваемых мощностей (до 100 кВт), 5) высокий КПД.
Недостатки: 1) сложность изготовления цепей и звездочек, 2)вытягивание цепей при эксплуатации, 3)необходимость смазки, подтягивания и др. ухода за цепью, 4) нежелательно применение цепных передач при ударных и резких колебательных нагрузках.
3.11.2. Расчет цепной передачи
Силовая схема цепной передачи аналогична силовой схеме ременной передачи (Рис.3.23). Следует различать: F1 и F2 – силы натяжения ведущей и ведомой ветвей цепи, Ft - окружная сила, F0 – сила предварительного натяжения. Для цепной передачи, работающей по принципу зацепления, величина F0 не имеет такого значения, как для ременной передачи.
Рис.3.23. Силовая схема цепной передачи
1) Передаточное число цепной передачи:
, (3.41)
где z1 и z2 – число зубьев ведомой и ведущей звездочек.
2) Передаточное отношение
, (3.42)
3) Скорость цепи.
, (3.43)
где р – шаг цепи, мм; n – частота вращения звездочки, об/мин; z – число зубьев звездочки.
4) Делительный диаметр звездочки:
, (3.44)
5) Межосевое расстояние передачи:
а = (30…50)р, (3.45)
6) Число звеньев цепи:
, (3.46)
Округляется до ближайшего целого числа.
7) Длина цепи:
l=zзвр, (3.47)
Основной критерий работоспособности приводных цепей это износостойкость их шарниров.
Расчет цепи на износостойкость производят по допускаемым давлениям в шарнирах цепи:
. (3.48)
где d1 и b3— соответственно диаметр валика и ширина внутреннего звена цепи;
[pц] – допускаемое давление в шарнирах цепи;
кэ – коэффициент эксплуатации.
Зубчатые передачи
Принцип действия зубчатой передачи основан на зацеплении зубчатой пары.
Меньшее зубчатое колесо, вращающееся с большей частотой вращения и имеющее меньшее число зубьев, называется шестерней. Ведомое зубчатое колесо, имеющее большее число зубьев и меньшую частоту вращения называется колесом.
Преимущества зубчатых передач: 1) возможность передачи практически любой мощности при широком диапазоне скоростей, 2) компактность, 3) надежность, 4) постоянство передаточного числа, 5) высокий КПД, 6) возможность изготовления из разнообразных материалов.
Недостатки: 1) ограниченность передаточного числа передачи, до 12,5, 2) относительная сложность изготовления, 3) при неточном изготовлении зубчатая передача является источником вибрации и шума.
3.12.1. Классификация зубчатых передач
1) По расположению осей валов – с параллельными, пересекающимися и скрещивающимися осями валов. 2) По форме зубчатого колеса – цилиндрические, конические, эллиптические 3) По форме зуба – прямозубые, косозубые, с круговыми зубьями, шевронные, 4) По взаимному расположению зубчатых колес – с внешним зацеплением и внутренним, 5) По форме профиля зуба – эвольвентные, циклоидальные, передачи Новикова – с круговым профилем зубьев.
Зубчатые передачи могут быть открытыми и закрытыми, силовыми и кинематическими, простыми и планетарными.
Способы изготовления зубчатых колес: литьем, накаткой зубьев на заготовке, нарезание зубьев на заготовке.
3.12.2. Геометрия эвольвентного зубчатого зацепления
Постоянное передаточное отношение зубчатой передачи достигается при определенной форме профиля зубьев. Наибольшее распространение получили эвольвентные профили зубьев. Эвольвентное зацепление обеспечивает высокую прочность зубьев, допускает некоторое изменение межцентрового расстояния при износе или погрешности изготовления.
Эвольвентой называется кривая, описываемая какой – либо точкой, лежащей на прямой, перекатываемой по окружности без скольжения (Рис. 3.24).
Рис. 3.24. Эвольвентное зацепление
3.12.3. Основные геометрические параметры зубчатой передачи
Основные геометрические параметры зубчатой передачи (Рис. 3.25): межосевое расстояние аw, число зубьев шестерни z1 и колеса z2, модуль m, передаточное число U = i.
Рис. 3.25. Геометрические параметры зубчатой передачи
Основные геометрические параметры зубчатого колеса (Рис. 3.26): модуль, диаметр делительной окружности d, впадин df, вершин da, основной dB, ширина b, высота зуба hа, число зубьев z.
Рис. 3.26. Геометрические параметры зубчатого колеса
Расстояние между одноименными профилями соседних зубьев по дуге окружности называется окружным шагом Pt.
Линейная величина в π раз меньше окружного шага зубьев называется окружным модулем зубчатого колеса.
. (3.49)
Все размеры зубьев цилиндрических зубчатых колес вычисляют по делительному нормальному модулю, который называется расчетным модулем зубчатого колеса или просто модулем. Значения модулей принимают по ГОСТу
Для цилиндрической прямозубой передачи существуют следующие зависимости:
- модуль – показывает сколько миллиметров делительной окружности зубчатого колеса приходится на 1 зуб:
. (3.50)
межосевое расстояние:
. (3.51)
высота зуба:
. (3.52)
где ha и c – соответственно коэффициенты высоты зуба и коэффициент
радиального зазора, в общем случае их принимают равными ha=1, с=0,25.
диаметр окружности впадин:
. (3.53)
диаметр окружности впадин:
. (3.54)
3.12.4. Элементы конструкции зубчатого колеса
1. Венец – часть ЗК, где расположены все зубья
2. Обод – часть ЗК, находящаяся между венцом и ступицей, служит для передачи крутящего момента от зубчатого венца к ступице.
3. Ступица – центральная часть зубчатого колеса с отверстием под вал, служит для соединения колеса с валом. (Рис. 3.27).
|
|

|


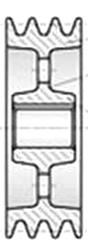
Рис. 3.27. Элементы конструкции зубчатого колеса
3.12.5. Материалы зубчатого колеса
Чугунные ЗК – СЧ 21….30.
Стальные ЗК – Ст.3…40, Сталь 40Х, 40ХН, 20ХГСА. Для повышения нагрузочной способности ЗК из углеродистой стали подвергают термообработке – улучшению, нормализации и поверхностной обработке – азотированию, закалке, цементации.
3.12.6. Силы, действующие зацеплении прямозубой цилиндрической передачи
Силовое взаимодействие колес заключается в передаче по линии NN силы нормального давления Fn. Р – полюс; NN – нормаль зацепления (линия давления); α - угол зацепления; Ft - окружная сила (Рис. 3.28).
Рис. 3.28. Схема сил
Окружная сила:
Ft = Fnּcos α. (3.55)
Радиальная сила:
Fr = Fnּsin α. (3.56)
3.12.7. Виды разрушения зубьев
Контактные напряжения сосредотачиваются в пятне контакта и вызывают усталостное выкрашивание поверхности зубьев (в). Напряжения в зубьях возникающие в результате действия изгибающего момента вызывают поломку зубьев у основания (а, б). Кроме усталостных видов разрушения возникает также износ зубьев связанный с недостаточной смазкой и действием абразивных частиц (г), а также заедание зубьев, возникающее при отсутствии смазки или ее выдавливании с поверхности зубьев при действии больших нагрузок (д) (Рис. 3.29). При заедании происходит условное сваривание поверхностей и отрыв поверхностных слоев зубьев зубчатой передачи.
Рис. 3.29.Виды разрушения зубьев
3.12.8. Расчеты на прочность
1. Проверка зубьев колес по контактным напряжениям σH, Н/мм2:
, (3.57)
где К – вспомогательный коэффициент,
- окружная сила в зацеплении, Н;
КHα – коэффициент, учитывающий распределение нагрузки между зубьями,
для прямозубых колес КHα=1;
КНβ – коэффициент неравномерности нагрузки по длине зуба,
для прирабатывающихся зубьев КНβ =1;
КHv – коэффициент динамической нагрузки, зависящий от окружной скорости колес и степени точности передачи,
uф – фактическое передаточное число.
2. Проверка по напряжениям изгиба зубьев шестерни σF1 и колеса σF2, Н/мм2:
, (3.58)
. (3.59)
где КFα – коэффициент, учитывающий распределение нагрузки между зубьями,
для прямозубых колес КFα=1;
КFβ – коэффициент неравномерности нагрузки по длине зуба,
для прирабатывающих зубьев колес КFβ=1;
КFv – коэффициент динамической нагрузки, зависящий от окружной скорости колес и степени точности передачи;
YF1 и YF2 – коэффициенты формы зуба шестерни и колеса определяются в
зависимости от эквивалентного числа зубьев шестерни и колеса;
Yβ – коэффициент, учитывающий наклон зуба, для прямозубых колес Yβ =1.
Червячные передачи
Рис. 3.30. Схема червячной передачи
Червячные передачи являются разновидностью передач с зацеплением и одним из вариантов винтовой зубчатой передачи (Рис. 3.30).
Здесь роль шестерни выполняет червяк, движение передается по принципу винтовой пары. Классификация червячных передач: 1) По числу заходов червяка – 1, 2-х и многозаходные (до 4-х). 2) По направлению – левая и правая резьба, 3) По расположению червяка относительно червячного колеса: с нижним, верхним, боковым расположением. 4) По форме нарезаемой части червяка – с цилиндрическим или глобоидным червяком (Рис. 3.31), 5) По форме профиля резьбы: цилиндрические,
эвальвентные, конволютные и др. В глобоидной передаче число зубьев червяка и колеса находящихся в зацеплении больше, поэтому ее несущая способность в 1,5-4 раза выше чем у цилиндрических, но она требует высокой точности изготовления.
Преимущества червячных передач: большое передаточное число, плавность и бесшумность работы, компактность и сравнительно малая материалоемкость, способность самоторможения.
Недостатки: низкий КПД = 0,7-0,8, ограниченность передаваемой мощности из за склонности к заеданию (до 200 кВт), необходимость отвода тепла из-за нагрева червяка и колеса, дороговизна материалов венцов червячного колеса.
3.13.1. Геометрические параметры червячной передачи
1) Основные размеры червяка:
делительный диаметр
d1=q m, (3.60)
начальный диаметр
dw1=m (q+2x) (3.61)
диаметр вершин витков
da1=d1+2m, (3.62)
диаметр впадин витков
df1=d1-2.4m, (3.63)
2) Основные размеры венца червячного колеса:
делительный диаметр
d2=dw2=mz2, (3.64)
диаметр вершин зубьев
da2=d2+2m(1+x), (3.65)
диаметр впадин зубьев
dF2=d2-2m (1,2-x). (3.66)
3.13.2. Силы, действующие в червячном зацеплении
В червячном зацеплении действуют (Рис. 3.32):
1) окружная сила червяка Ft1, равна осевой силе колеса Fа2:
, (3.67)
Рис. 32.Силы, действующие в червячном зацеплении
2) Окружная сила колеса Ft2, равная осевой силе червяка Fа1:
, (3.68)
3) Радиальная сила:
. (3.69)
где α – угол зацепления червячной пары.
3.13.3. Расчет на прочность
1) По контактным напряжения зубьев колеса σH, Н/мм2
, (3.70)
где – окружная сила на колесе, Н;
К – коэффициент нагрузки.
Принимается в зависимости от значения окружной скорости колеса.
2) По напряжениям изгиба зубьев колеса σF, Н/мм2:
. (3.71)
где YF2 – коэффициент формы зуба, (определяется в зависимости от
эквивалентного числа зубьев колеса);
b2 – ширина венца колеса.
3.13.4. Материалы червяков и червячных колес
Червяки силовых передач изготавливают из углеродистых и легированных сталей – Ст.35, Ст.40, Ст.40Х, Ст.40ХН и подвергают закалке или Ст.12ХН2 – которая подвергается цементации.
Червячные колеса – при высокой скорости зацепления венцы изготавливают из бронзы: БрОФ10, БрОФН. При скорости зацепления менее 6 м/с из менее дорогой БрАЖ9.
Оси, валы
Оси и валы – служат для поддержания вращения деталей передач. Оси могут быть подвижными и неподвижными. Валы наряду с поддержанием вращения выполняют еще функцию передачи крутящего момента.
3.14.1. Классификация валов
1) По назначению: валы передач и коренные валы; 2) По форме: прямые, коленчатые (в), гибкие (г), 3) По конструкции – гладкие (а) и ступенчатые (б), сплошные и полые (Рис. 33).
а) б)
в) г)
Рис. 33. Виды валов
Участки осей и валов, которыми они опираются на подшипники при восприятии радиальных нагрузок, называют цапфами, а при восприятии осевых нагрузок называют пятами. Пяты могут быть круглыми, кольцевыми, гребенчатыми, а также концевыми (а) и кольцевыми (б) (Рис. 3.34).
Концевые цапфы, работающие в подшипниках скольжения называют шилами, а цапфы расположенные на некотором расстоянии от концов вала называют шейками. Цапфы осей и валов могут быть цилиндрическими и сферическими.
а) б)
Рис. 3.34. Концевая (а) и кольцевая (б) пяты
Плавный переход одной ступени вала к другой называется галтелью (Рис. 3.35). Галтели могут быть постоянного радиуса (а) и переменного радиуса (б).
а) б)
Рис. 3.35. Схемы галтелей
Детали на валах фиксируются следующими способами:
1) Посадкой с натягом (за счет разности размеров отверстия и вала) (а); 2) Упором в бурт (б); 3) Упором в бурт в сочетании с гайкой (в); 4) Пружинными кольцами (г); 5) Штифтовым соединением (д); 6) Стопорным винтом (е) (Рис. 3.36).
Фаски служат для облегчения установки деталей на валу и притупления острых кромок.
а) б) в) г)
д) е)
Рис. 3.36. Осевое фиксирование деталей на валах.
3.14.2. Материалы осей и валов
Марка сталей | Область применения |
Стали обыкновенного качества Ст.5, Ст.6 по ГОСТ 380-94 | Малонагруженные оси и валы без термообработки |
Малоуглеродистые конструкционные стали: - качественные 15, 20 по ГОСТ 1050-88 - легированные 15Х, 20Х, 18ХГТ и др. по ГОСТ 4543-71 | Валы и оси при требовании высокой износостойкости: - опоры скольжения - вал-шестерня |
Среднеуглеродистые конструкционные стали: -качественные 40, 45 и др. по ГОСТ 1050-88 -легированные 35Х, 40Х, 40ХН и др. по ГОСТ 4543-71 | Высоконагруженные валы и оси |
3.14.3. Расчет осей и валов
Основные критерии работоспособности: прочность и жесткость. Неподвижные оси рассчитывают на статическую прочность, вращающиеся оси и валы рассчитывают на статическую прочность и сопротивление усталости.
Расчет на статическую прочность при изгибе
Уравнение прочности будет иметь вид:
, (3.72)
, (3.73)
- осевой момент сопротивления
Расчет валов работающих на кручение
В этом случае уравнение прочности будет иметь вид:
, (3.74)
где [τк], τк – допускаемое и расчетное напряжение кручения,
Т – крутящий момент,
Диаметр вала в опасном сечении:
. (3.75)
Подшипники
Подшипники воспринимают осевые и радиальные нагрузки и сохраняют заданное положение оси вала.
Требования предъявляемые к подшипникам:
1) Минимальные потери на трение, 2) По возможности меньшие габариты и низкая стоимость, 3) Высокая долговечность.
Различают 2 основных типа подшипников по виду трения: подшипники скольжения – в которых опорный участок вала скользит по поверхности подшипника и подшипники качения – в которых трение скольжения заменено на трение качения. Основное конструктивное отличие подшипников качения – наличие тел качения между опорными поверхностями.
3.15.1. Подшипники скольжения
Основным конструктивным элементом подшипников скольжения является вкладыш 2 расположенный в корпусе 1 с тонким слоем антифрикционного материала, поступающего из пресс-масленки 3 через выточку для подачи масла 4, на опорной поверхности (Рис.3.37).
Рис.3.37. Подшипник скольжения
В зависимости от вида воспринимаемой нагрузки подшипники скольжения могут быть радиальными и упорными (подпятки).
3.15.2. Расчет подшипников скольжения по среднему давлению
, (3.76)
где Fr – радиальная нагрузка подшипника (Рис.3.38),
d – диаметр цапфы вала,
l – длина цапфы, (м).
Рис.3.38. Нагрузка на подшипник скольжения
3.15.3. Режимы трения в подшипниках скольжения
В зависимости от толщины масляного слоя подшипник работает в режиме жидкостного, полужидкостного, полусухого и сухого трения.
Характеристика режимов трения подшипников скольжения: сухое трение – имеет место в подшипниках без смазочного материала; полусухое – имеет место при недостаточной смазке; полужидкостное – при постоянной подаче масла и увеличенных угловых скоростях вала; жидкостное трение – при определенной угловой скорости, при этом вал отходит от поверхности подшипника (всплывает), т.е. контакт поверхностей практически отсутствует.
Смазочные материалы: 1) Жидкие масла, 2) консистентные смазки – солидол, литол, 3)Твердые смазочные материалы – графитовая смазка.
Способы смазки: 1) Централизованное – под давлением или самотеком,
2) Индивидуальное.
3.15.4. Материалы подшипников скольжения
Вкладыши подшипников скольжения изготавливают из: 1) бронзы; 2) чугуна; 3) баббита – сплав на основе олова, является одним из лучших материалов для подшипников скольжения. Преимущества: хорошо прирабатывается, не окисляет масло, мало изнашивает вал. Недостатки: хрупкость и высокая стоимость. В связи с этим им заливают только рабочую поверхность вкладыша от 1 до 10 мм; 4) неметаллических материалов – пластмассы и металлокерамика.
Подшипники качения
Подшипники, работающие по принципу трения качения называют подшипниками качения, они имеют тела качения. Конструкция подшипников качения позволяет изготавливать их в массовых количествах как стандартную продукцию, что снижает их стоимость.
3.16.1. Классификация подшипников качения
По направлению воспринимаемой нагрузки – на радиальные, упорные и радиально-упорные; по форме тел качения – шариковые (а), роликовые (б, в), игольчатые (г), витые (д), конические (е, з), бочкообразные (ж) (Рис. 3.39); по количеству рядов тел качения – одно, двух рядные, по нагрузочной способности подшипники разделяют на пять серий диаметров: сверхлегкую, особолегкую, легкую, среднюю и тяжелую.
а) б) в) г)
д) е) ж) з)
Рис. 3.39. Тела качения
Все подшипники качения изготавливают из высокопрочных специальных подшипниковых сталей (высокоуглеродистых, легированных).
Основные типы подшипников качения: радиальный однорядный шариковый (а), радиальный двурядный шариковый (б), радиально-упорный однорядный шариковый (в), двурядный радиальный роликовый (г), радиальный однорядный витой (д), радиально-упорный однорядный конический (е), упорный однорядный шариковый (ж), упорный двурядный шариковый (з), упорный однорядный конический (и) (Рис. 3.40).
а) б) в) г) д) е)
ж) з)
и)
Рис. 3.40. Основные типы подшипников качения
3.16.2. Устройство подшипника качения
В большинстве случаев подшипник качения состоит из наружного (1) и внутреннего (2) колец с дорожками качения, тел качения (3) и сепаратора (4), удерживающего тела качения на определенном расстоянии друг от друга (Рис. 3.41). В некоторых случаях одно или оба кольца могут отсутствовать, тогда тела качения перемещаются непосредственно по дорожкам качения вала или корпуса.
Большое влияние на работоспособность подшипника оказывает качество сепаратора. В подшипниках без сепаратора тела качения набегают друг на друга. При этом кроме трения качения, возникает трение скольжения, увеличиваются потери и износ подшипника. Установка сепаратора значительно уменьшает потери на трение, т.к. сепаратор является свободно плавающим и вращающимся элементом. Их изготавливают из стали, латуни, бронзы или пластмассы.
Рис. 3.41. Схема
подшипника качения
Для смазки подшипников применяются пластичные смазки и жидкие масла. Жидкие смазки более эффективны, т.к. они кроме своей главной функции – уменьшение потерь на трение еще и охлаждают подшипник.
3.16.3. Виды разрушений подшипников качения
1) Усталостное выкрашивание – наблюдается у подшипников после длительного времени их работы в нормальных условиях.
2) Износ колец (дорожек качения)– наблюдается при недостаточной защите от пыли и грязи.
3) Разрушение сепараторов – одна из главных причин выхода из строя быстроходных подшипников качения.
4) Раскалывание колец и тел качения – связано с ударными и вибрационными перегрузками, неправильным монтажом.
5) Остаточные деформации – на беговых дорожках в виде лунок, наблюдается у тяжелонагруженных подшипников.
3.16.4. Подбор подшипников качения
Стандартом ограничено число типов и размеров подшипников. Это позволило рассчитать и экспериментально установить грузоподъемность каждого типоразмера подшипников.
При проектировании машин подшипники качения не конструируют и не рассчитывают, а подбирают из числа стандартных по условным методикам.
Различают подбор подшипников:1) по статической грузоподъемности при частоте вращения n ≤ 1 об/мин., он выполняется по условию:
, (3.77)
где Р0 – расчетная эквивалентная статическая нагрузка, Н,
С0 – статическая грузоподъемность стандартных подшипников, выбирается из таблиц.
2) по динамической грузоподъемности при n > 1 об/мин., он выполняется по условию:
Ср≤ Сном. (3.78)
где Ср и Сном – соответственно расчетная и номинальная грузоподъемность подшипника.
Номинальная динамическая грузоподъемность для радиальных и радиально-упорных подшипников есть такая постоянная радиальная нагрузка, которую подшипник может выдержать в течение номинального срока службы, исчисляемого в один миллион оборотов внутреннего кольца без появления признаков усталости материала любого кольца или тела качения.
Муфты
Муфтами в технике называют устройства, которые служат для кинематической и силовой связи отдельных частей машины.
Муфты используются для: 1) Соединение валов, 2) Включения и выключения исполнительного механизма при непрерывно работающем двигателе (управляемые муфты). 3) Для предохранения машины от перегрузки (предохранительные муфты), 4) Для компенсации вредного влияния несоосности валов, связанной с неточностью монтажа (компенсирующие муфты). 5) Для уменьшения динамических нагрузок (упругие муфты) и др.
Рис. 3.42. Классификация механич
Дата добавления: 2022-05-27; просмотров: 217;