Технологичность конструкций корпуса судна
Рост технического уровня предприятий невозможен без повышения технологичности корпусных конструкций. Одно из направлений повышения ТКК – использование модульного принципа: комплектование судов различных архитектурно-конструктивных типов (АКТ) из оптимального количества стандартных деталей, узлов, секций, блоков. При этом следует не упускать из виду удобство ремонта и простоту обслуживания во время эксплуатации. Решить эту задачу позволяет проектирование судов с упрощенными обводами корпуса.
5.1. Технологичность деталей
Деталь – первичный элемент корпусной конструкции, который изготавливается из одного материала без применения сборочных операций. На одно судно их может идти десятки тысяч. С целью классификации деталей, дальнейшего их анализа и разработки типовых маршрутов их изготовления детали разделяют на 5 классов и 8 групп, получая, таким образом, 40 видов деталей, каждому из которых соответствует типовой маршрут изготовления.
С целью повышения технологичности деталей следует:
· широко использовать плазменную резку на стационарных машинах с ЧПУ, что обеспечивает высокую производительность, отсутствие грата, а при резке под водой отпадает необходимость в правке и значительно снижается вредное воздействие на окружающую среду;
· кислородную резку на машинах с ЧПУ следует назначать лишь для вырезки деталей из толстолистового проката;
· полуавтоматическую резку применять только для деталей из толстолистового проката с прямолинейными кромками;
· механическую резку следует применять для деталей типа полос и мелких книц в случае большого количества деталей; при этом необходимо совмещать кромки;
· детали типа поясков, ребер, стенок рационально изготавливать из полосового проката, а не из листового (т.к. полосовой прокат дешевле; но применение полосового проката увеличивает число типоразмеров);
· при конструировании деталей следует учитывать способ резки, например, при механической следует назначать угловые срезы, а при тепловой резке на ЧПУ – вырезы.
· разделку кромок под сварку следует производить одновременно с вырезкой, при этом надо стремиться назначать одностороннюю разделку без притупления (см. рис.5.1 а), если все же притупление необходимо, то резку с разделкой следует производить на машинах с 2-х резаковыми (а двустороннюю разделку – с 3-х резаковыми) блоками (рис. 5.2);
· номенклатура деталей, поступающих в обработку, должна быть из одного техкомплекта, что позволяет сортировать их одновременно;
|
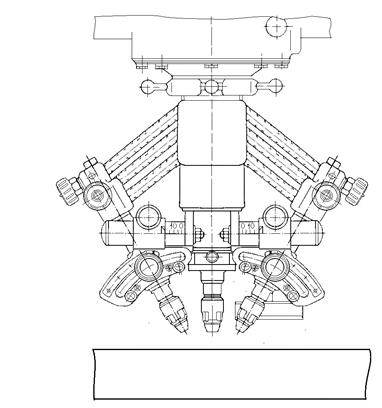
· следует стремиться проектировать детали с прямолинейными кромками. Если до появления автоматической резки точность изготовления деталей с прямолинейными кромками была выше, то с появлением машин с ЧПУ точность вырезки деталей с криволинейными кромками такая же, как и с криволинейными, но программа вырезки деталей с прямолинейными кромками проще, программировать можно непосредственно на дисплее машины (при необходимости). Возможно использовать автоматическую сварку; при изготовлении узлов и секций из деталей с прямолинейными кромками усилия, прилагаемые на совмещение, стыковку и закрепление кромок, значительно ниже, время, затрачиваемое на эти операции, существенно меньше – трудоемкость стягивания и совмещения в 1,5 раза, а в целом – в 2,5 раза меньше; повышается коэффициент раскроя (в начале 70-х годов нормативный коэффициент раскроя составлял 0,75, в 80-х годах – 0,8, в настоящее время – 0,85; а иногда, у судов с упрощенными обводами, удается достичь 0,9 и даже 0,95);
· следует снижать количество деталей, подвергающихся гибке, т.к. при этом 85% вспомогательных операций выполняется вручную (или, по крайней мере, заменять детали со сложной кривизной на детали с простой кривизной, т.к. трудоемкость их изготовления существенно ниже), а трудоемкость сборки конструкций из гнутых деталей в 2 раза выше, чем из плоских;
· чем меньше количество деталей в конструкции, тем больше коэффициент использования металла.
Разработка ТП изготовления деталей:рациональную технологию следует выбирать по показателю трудоемкости изготовления, т. к. форма деталей, разделка кромок и пр. заданы проектантом. Но при этом необходимо учитывать имеемое на предприятии оборудование и его загрузку.
5.2. Технологичность узлов корпусных конструкций
5.2.1. Технологические узлы
Узлы корпусных конструкций классифицируют по конструктивно-технологическим признакам (рис.5.3).
Рассмотрим типовые узлы и возможность механизации их изготовления:
· тавровые и Г- образные балки длинной более 1,5 метров: прямолинейные с малой кривизной и криволинейные – возможна полная механизация изготовления:прямолинейные – на ПМЛ типа МИБ-700, криволинейные – на агрегате СКТ-12-1;
· короткие тавры, бракеты и кницы с поясками – возможна механизация изготовления: их сборка возможна с применением кондукторов, сварка – полуавтоматом в среде CO2, в случае изготовления нескольких одинаковых узлов возможна и автоматическая сварка;
· широкие полосы с ребрами или поясками: прямолинейные и с малой кривизной – возможна механизация изготовления при использовании стендов с передвижными порталами;
· рамки из полос и профиля – возможна механизация;
· полотнища плоские и с небольшой погибью – возможна полная механизация при использовании поточных механизированных линий;
· гофрированные конструкции – механизация затруднена. Гофрированные переборки возможно устанавливать непосредственно на II дно, что может привести к возникновению "жестких точек", и с помощью "домиков", когда нагрузка разносится на большую площадь, что позволяет избежать концентрации напряжений (рис. 5.4);
· Объемные узлы небольшой протяженности (мелкие фундаменты, коробки) – механизация затруднена.
· Судовые фундаменты. Их количество колеблется от 150 до 300 штук, в зависимости от типа и размеров судна; на рыбопромысловых судах и базах может достигать 700. На их проектирование затрачивается 8–16% от рабочего времени проектирования судна. Для обеспечения технологичности фундаментов необходимо учитывать возможность их обработки, простоту сборки и сварки, установки и приварки в секции, установки, сборки и сварки фундаментов на стапеле.
· Объемные узлы небольшой протяженности (мелкие фундаменты, коробки) – механизация затруднена.
· Судовые фундаменты. Их количество колеблется от 150 до 300 штук, в зависимости от типа и размеров судна; на рыбопромысловых судах и базах может достигать 700. На их проектирование затрачивается 8–16% от рабочего времени проектирования судна. Для обеспечения технологичности фундаментов необходимо учитывать возможность их обработки, простоту сборки и сварки, установки и приварки в секции, установки, сборки и сварки фундаментов на стапеле.
Рис. 5.4. Установка гофрированной переборки с помощью "домиков":
1 – палуба; 2,4 – верхний и нижний "домики", соответственно; 3 – гофрированная переборка; 5 – второе дно.
Очень важен правильный выбор баз, допусков на конструктивные размеры и чистоту обрабатываемых поверхностей. Технологичность фундаментов зависит от их серийности.
Узлы внутри групп объединяют по принципу однородности технологических процессов изготовления. Повышение технологической идентичности позволяет снизить трудоемкость за счет единой сборочно-сварочной оснастки.
Ниже приведены рекомендации при проектировании узлов:
· обделку отверстий поясками следует заменять ребрами жесткости;
· по возможности, следует отказываться от криволинейных участков набора;
· следует заменять криволинейные пояски прямолинейными с заменой закругленного рамного соединения кничным, что позволяет исключить гибочные работы, облегчить монтаж и пригонку секций на стапеле (рис. 5.5 );
· корпусные конструкции, в том числе детали и узлы, следует проектировать с учетом их изготовления механизированным и автоматизированным способом;
· конструкции узлов и соединительных деталей, в случае невозможности их изготовления механизированным или автоматизированным способом, должны быть удобными для сборки с применением различных приспособлений, что позволит уменьшить объем ручных работ и, соответственно, снизить трудоемкость изготовления;
· необходимо стремиться к увеличению количества одинаковых деталей и узлов (широкая внутри- и межпроектная унификация);
· шире применять катаный профиль вместо составных сварных балок;
· следует применять детали возможно больших размеров – уменьшается длина сварных швов и протяженность сопрягаемых кромок;
· вместо приварных поясков бракет и книц применять отогнутые фланцы;
· подкреплять вырезы в высоком наборе следует только с одной стороны, ребра жесткости должны быть прямолинейными преимущественно из полосового проката, а горизонтальные ребра не следует приваривать к вертикальным;
· вертикальные ребра жесткости, которые подкрепляют флоры и стрингера, должны быть параллельны друг другу, а при использовании несимметричного полособульба головки должны быть направлены в одну сторону (по крайней мере – в пределах одного узла);
· у горизонтальных ребер жесткости из несимметричного полособульба головки следует ориентировать вниз;
· пояски тавров в пределах одного узла должны быть одной ширины;
|

· флоры и стрингеры должны отличаться только по контуру днища, остальные контуры и вырезы должны совпадать (рис 5.6);
· вырезы в стрингерах (флорах) следует располагать друг против друга (см. рис. 5.6);
· узлы плоских полотнищ:
а) должны иметь хотя бы одну прямолинейную кромку, которую используют в качестве базы;
б) внутрисекционные стыки должны быть в одной плоскости;
в) пазы и стыки должны быть прямолинейны и параллельны друг другу;
г) пазы (стыки) не должны пересекаться;
д) для уменьшения сварочных деформаций от приварки набора необходимо стремиться к соотношению сторон опорного контура, равному 1:2;
е) конструкции узлов и соединительных деталей должны быть удобны для сборки с применением приспособлений, что снижает трудоемкость и требования к квалификации персонала.
5.2.2. Конструктивные узлы соединений балок набора
В настоящее время вместо стыковых соединений широко применяют накройные соединения, что упрощает подгонку и снижает трудоемкость сборки, т. е. такие соединения более технологичны.
Но накройные соединения имеют и недостатки:
· возможна щелевая коррозия (особенно в танках и балластных цистернах);
· возможно снижение надежности в условиях вибрации;
· при использовании симметричного полособульба невозможно выполнить непосредственно-накройное соединение.
Дата добавления: 2021-05-28; просмотров: 407;